February 2009 Vol. 236 No. 2
Features
Operating Conference Roundtable Focuses On Integrity Management
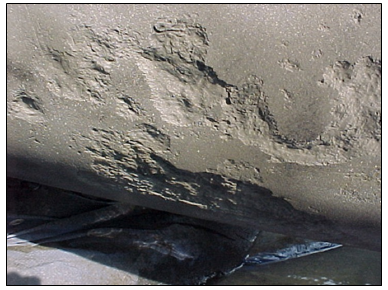
The Southern Gas Association (SGA) holds an annual conference at which many subjects are discussed involving gas transmission and distribution operations.
Topics are chosen by the participants and, while some short presentations are provided, most of the time is spent in peer-to-peer discussions of specific, present-day issues of concern to pipeline operators. This article summarizes some of the relevant issues discussed at the July 2008 Transmission Integrity Management Program (TIMP) roundtable held in Atlanta. The TIMP sessions were co-chaired by Garry Matocha, Principal Engineer of Spectra Energy and Virgil Wallace, Senior Pipeline Integrity Engineer of Williams.
The roundtable began with four presentations providing background on successes and effects on operators of the IMP regulations. The presentations also set the stage for subsequent discussions among operators and service providers.
Dave Johnson of Panhandle Energy and chair of the Interstate Natural Gas Association of America (INGAA) Pipeline Safety Committee led off discussing what the industry has learned to date from performing integrity assessments and the PHMSA IMP audits. In high-consequence area (HCAs) – the focus of the regulations – there have been 0.05 immediate repairs per mile and 0.14 scheduled repairs per mile, since inception of the regulations. Immediate response conditions are being conservatively classified. The industry has an effective suite of tools inline inspection (ILI), engineered pressure tests and direct assessment and it has capable service providers to apply them.
There remains a need for new technology. Representatives of the industry, service providers and PHMSA are working to establish additional inspection tools such as Guided Wave Ultrasonic Technology (GWUT). The process for using GWUT is advancing successfully and is now embodied in a document referred to as the “18 Points.” This is a consensus document developed jointly by PHMSA and INGAA. (http://primis.phmsa.dot.gov/gasimp/docs/GuidedWaveCheckList110107.pdf)
Integration of best practices, as well as knowledge advancement and sharing, are effectively taking place. The industry is good at “pigging and digging” but needs to improve in documentation. While there is no uniform understanding of requirements and enforcement among the PHMSA auditors, the inspection teams’ expectations appear to be converging.
Mark Hereth, a principal at P-PIC, told how IMP has changed what operators do. Operators are formalizing processes and procedures as well as improving documentation of their work. While the regulations and even the supporting consensus standards are largely prescriptive, operators have found multiple paths to solve specific issues. More companies are now making long-term plans to assess their entire systems over 10-15 years It is also becoming clear that operators who successfully apply IMP are finding that they attain a competitive advantage which enables them to obtain special permits for class location changes and operation up to 80% of SMYS.
Chris Bullock, senior pipeline integrity engineer with CenterPoint Energy, provided examples of operator experience as what constituted or created a new HCA and why. He also showed how different kinds of corrosion, dents, SCC and weld anomalies have been found as a result of the pipeline assessments.
Keith Leewis, a senior fellow with P-PIC, and Dave Johnson, vice president pipeline safety with Panhandle Energy, discussed the status of the following pipeline safety regulations and related consensus standards:
- NACE SP0169, Control of External Corrosion on Underground or Submerged Metallic Pipeline Systems, and NACE RP0502, Pipeline External Corrosion Direct Assessment Methodology, were both reaffirmed in 2007.
- ASME B31.8, Gas Transmission and Distribution Systems, was modified and reissued in 2007, to include new considerations for dents.
- ASME B31.8S, Managing System Integrity of Gas Pipelines, is undergoing some modifications including a more comprehensive repair methods table, a modification of the treatment of stress corrosion cracking (SCC) to include near neutral and high ph SCC and a clear definition of failure pressure, Pf. The modified B31.8S should be approved shortly.
Roundtable Discussions
There were about 15 operating companies on hand to discuss the following topics:
How is non-mainline piping being treated when is it part of the IMP? (Blow-offs, crossovers).
- There was no consensus on approach on whether to consider these lines part of mainline piping or not, and whether they must be included in IMP plans.
- There has been some internal corrosion found within approximately 100 feet of compressor suction and discharge lines.
- The non-mainline piping lines are assessed by some operators if they are in an HCA, usually with ultrasonic testing or guided wave technology. It is unclear whether PHMSA approval to use guided wave for other than crossings is required.
- Direct examination of a length of pipe is always an alternative to the use of ILI, pressure testing or DA.
- It was suggested that each operator define “what is” and “what is not” non-mainline piping, state that clearly in their IMP plans and manage the lines accordingly.
Record Keeping
- Record keeping is labor- and time-intensive.
- Some software programs make record-keeping/documentation easier.
- One company uses a Word program for documentation and tracking.
- One company has an enterprise documentation and tracking system.
- No one has dedicated personnel for record keeping.
- It is difficult to determine what must be documented and what does not require documentation.
Direct Assessment
- Pre-assessment is essential and must be fully applied.
- Operators are not finding problems with cased crossings; however, access can sometimes be limited by pavement that extends past the casing.
- Finding a PHMSA “no objection” path for cased pipe still represents a concern since both DA and ILI sometimes present interpretation difficulties and GWUT even with the 18 points does not always receive a “no objection” from PHMSA.
- GWUT is only as good as the operator. Qualification of the operators of the technology is critical and this is reflected in the 18 points.
- All the participants believe that filling the annulus between the casing and the pipe with a dielectric solution (like wax) was a permanent repair (>25yrs).
- Operators are finding value in the use of remote monitoring on portions of their system, such as with cathodic protection.
Data Integration
- There is a need to determine how to do it effectively with the exponentially increasing amount of data being generated. You should ask yourself what data will be needed in 10 years and then ensure that it is being collected now.
- Some companies reported having trouble populating databases and getting accurate data from the field.
- Some use integrated data to grade threats and threat type to determine assessments and prevention and mitigation (P&M) measures. No one has identified P&M measures they don’t need.
- Operators find that CIS (Close Interval Survey) data and other engineering data captured in geographical information systems (GIS) are not necessarily compatible and not easily integrated.
- It is important to get the GIS and IMP groups together so that data can more readily be integrated and evaluated.
- One suggested best practice is to “GPS” all welds and pipe joint numbers as the pipe is installed, record operating temperatures down the pipeline and soil properties observed during construction.
Risk Management
- Is there a value to redoing risk assessments after baselines? They can help establish and re-evaluate P&M measures. Risk assessments also are essential in re-evaluating re-inspection intervals. Participants were unsure if risk ranking had value after the baseline assessments were complete, even though threat assessment remains valuable.
- Most companies are just using the HCA characteristics and population-driven consequence factor in risk analysis. One company is using cost of life, injuries and other costs for consequence modeling.
Continuous Improvement
- Everyone could use guidance on approaches and processes to effectively add continuous improvement into their IMP.
- One suggestion was to get the subject matter experts together, evaluate IMP audit results, modify processes and document the process you went through and what changes that prompted. One company is doing this three times per year.
- INGAA sponsors an IMP metrics program which gathers IMP-specific data on an annual basis (The Impact of the Integrity Management Program on Gas Transmission Pipelines, Summary of Results 2004-2007, INGAA, July 2008). INGAA IMP Metrics team members can use their data to benchmark their performance relative to the group, represented by 120,000 miles of transmission piping, and make improvements to the IMP plan accordingly. The IMP metrics members of 10 pipeline companies have performed more than 400 IMP audits to date. The results of audits can be used to modify the IMP and this is the essence of continuous improvement.
- Another avenue for continuous improvement is attendance at the SGA roundtables, hearing something new that may apply to your pipeline and adopting that process or technique.
There were a number of other issues that were discussed but time and space do not permit presenting them here. Clearly, the participants of these roundtables find them extremely useful and an effective use of their time.
The SGA TIMP roundtable Web page describes the session and provides a link to a short “De-Brief Web Conference” (audio and slides) by the session chair and vice chair. Visit http://www.southerngas.org/EVENTS/OpCon_TIMP_RoundTable.htm
Author
Bernd J. Selig is an associate with Process Performance Improvement Consultants (P-PIC). He has more than 40 years of experience in the power, equipment insurance and pipeline industries. He has been a member of ASME, ANS and NACE, was an accreditor of mechanical engineering departments for six years and served as a member of ASME’s Board on Research & Technology Development. He has written numerous articles and technical papers during his career. Recently, he was the editor of ASME’s B31.8S supplement to B31.8, Integrity Management Programs for Gas Pipelines and B31Q Pipeline Personnel Qualification.
Comments