October 2010 Vol. 237 No. 10
TechNotes
Pipe Rehabilitation Coating With Brains
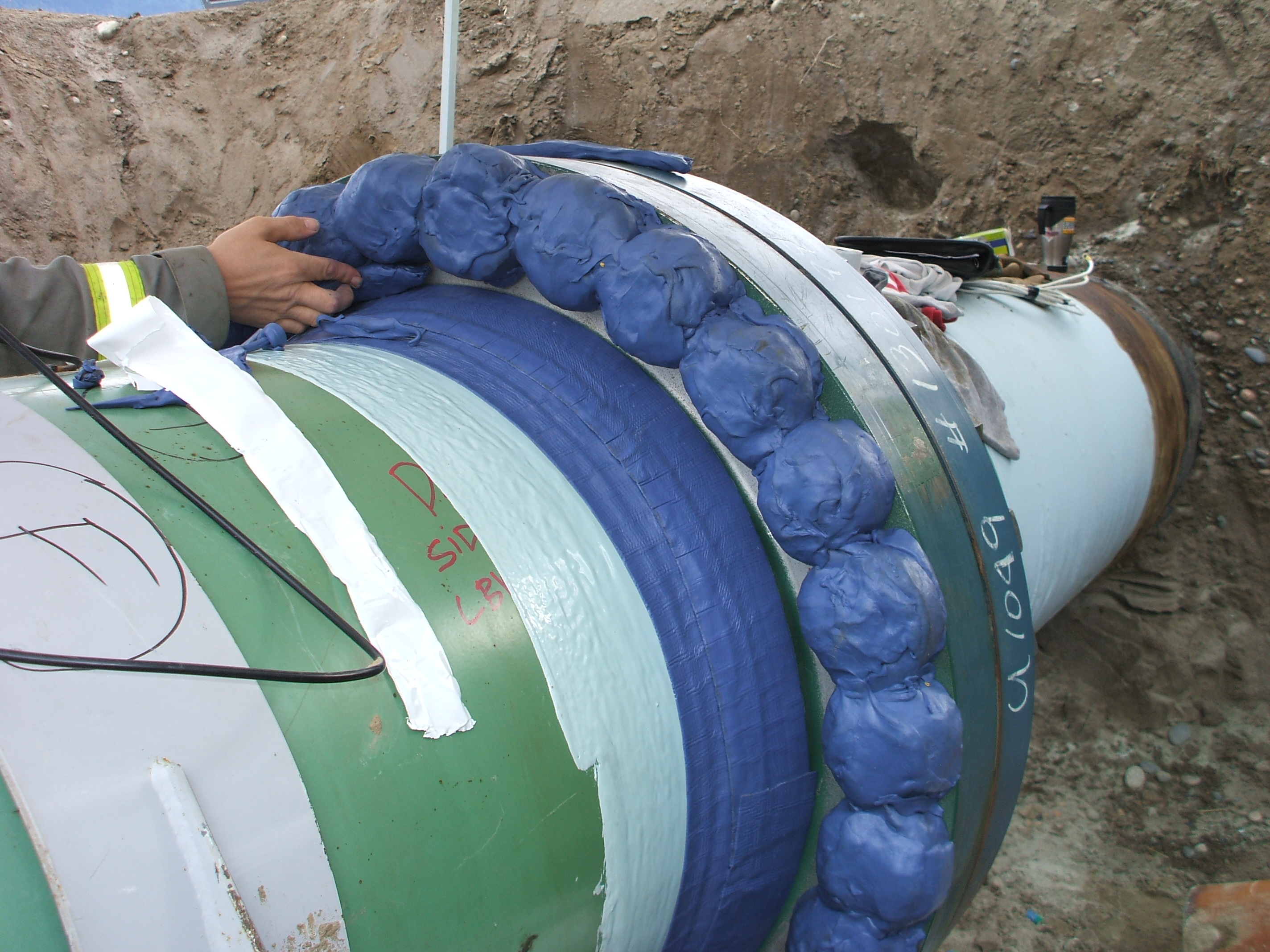
Corrosion causes billions of dollars of damage every year. Pipeline coatings tend to especially fail in their capability to protect against corrosion during rehabilitation. Practice teaches that many rehabilitated coating failures are caused by lapses during application and improper surface preparation (NACE study 1996).
There are a few phenomena that play an important part in the corrosion process and should be taken into consideration at rehabilitation: 1) salts and osmosis, 2) adhesion, 3) microbiological induced corrosion (MIC), 4) surface preparation and 5) water permeability.
Salts and osmosis. The presence of salt plays an important role in a corrosion mechanism. Salt particles are present in most of the situations and are difficult to remove. Because salts attract water and because many pipeline coatings are not 100% impermeable to water vapor or water the presence of salt is always a risk in practice.
Adhesion. Any pipeline coating must have a good adhesion to the substrate. To obtain a good adhesion in practice is not easy. The reason for this is that the application circumstances must be taken into consideration and many coatings require a perfect surface preparation. Generally one can say that a proper adhesion in practice is not as simple as it seems because usually efforts are being made to bond two different types of material with different surface tensions together and they tend to delaminate or disbond.
Microbiologically influenced corrosion (MIC). This is, much to the surprise of many people in the pipeline industry, responsible for almost 50% of their corrosion problems. MIC is a phenomenon in which corrosion is initiated, accelerated – or both – by the activities of micro-organisms. Sulfate-reducing bacteria (SRB) are obligatory anaerobic bacteria utilizing sulphate as a terminal electron acceptor and organic substances as carbon sources. During the metabolic process, sulphate is reduced to sulphide, which reacts with hydrogen produced by metabolic activities or by cathodic reaction of corrosion processes to form hydrogen sulphide. There are bacteria that can live without oxygen but none can live without water.
Surface preparation. Bad surface preparation appears to be a main cause of corrosion problems, NACE studies have proven. Very often, field-applied-coatings need a nearly excellent prepared surface of the substrate in order to get effective adhesion and sandblasting often is required.
Water permeability. Even if there is the slightest permeability for water, corrosion will occur. No matter how good a coating has been applied, no matter how the application circumstances have been controlled, corrosion will occur if water or water vapor is able to travel through a coating; especially if salt particles or pollutants are present in the voids of the blasted substrate.
In respect to the above-mentioned phenomena and in order to prevent corrosion during and after rehabilitation, one has to prevent blank steel parts coming into contact with water by employing a protective coating. But this coating then has to be 100% impermeable for water and to be perfectly matched and remain matched to the surface pores of the pipeline. The coating should have a perfect adhesion and reduce the risk for MIC. Moreover, in practice, the application procedure should be easy and reduce risk of failures. Many of the existing coating materials do not meet this requirement and – especially with field-applied rehabilitation coatings – pipeline owners are facing challenges from the mentioned phenomena.
A substance like oil – i.e. without the presence of water particles – will possibly fulfill this requirement. However, oil has a character that is too fluid to seriously act as a pipe coating. A mastic with fluid-type properties with no or a very low degree of crystalline behavior and wetting characteristics may meet this requirement and could make the coating self-healing.
Such a coating is a smart viscous elastic coating.
VISCOTAQ is a smart coating and has been developed for the protection of underground and aboveground substrates against corrosion. Because a good application of a corrosion preventative coating determines the long-term effectiveness of the coating, a choice has been made of materials with specific rheological behavior that allows for an easy and failure-free application in the field. VISCOTAQ consist of amorphous a-polar polyolefins. The material has been designed in such a way that – as a solid – it shows both elastic and fluid properties. Due to these properties it has self-healing characteristics.
How can such a smart coating overcome the typical pipeline coating rehabilitation challenges?
Elimination of salt problems. The new smart coating is impermeable to water and therefore the hazardous salt particles have been neutralized because water will not travel through the coating. Rinsing with clean water in remote areas is not necessary anymore.
Elimination of adhesion problems. The new coating has excellent wetting characteristics. It has an adhesion to the substrate’s surface and is actually pushed to the substrate by air pressure and has a cohesive fracture, meaning when it is peeled off, the material will break apart and the remaining film is left on the pipe. The material shows cold flow as it is a pressure-sensitive adhesive.
It flows into the pores of the pipe and there exists a very intimate match between the substrate and the coating. This results in an extremely good and immediate adhesion. Due to the wetting characteristics, adhesion will take place rather quickly and will remain for decades.
Elimination of osmosis problems. Due to its impermeable character for moisture the phenomenon of osmosis does not occur. In addition, the coating has self-healing characteristics. Minor pinholes will be dealt with by the wetting and viscous properties of the coat wrap and damages will heal automatically.
Elimination of MIC problems. With the new coating, MIC does not occur. The material is impermeable for water and consists of an organic polymeric composition with inorganic filler material. It is proposed here that if no nitrogen nutrients are available in the coating substance, it is impossible for micro-organisms to grow on this material under anaerobic conditions.
Elimination of surface preparation problems. A surface preparation of ST-2 removal of sand, loose parts and grease is sufficient. Sandblasting is better. However, it is not absolutely necessary. Due to the coating’s cold flow characteristics and the low surface tension, the material shows a perfect adhesion to all materials, even to PE and PP.
Elimination of water permeability problems. The material is made of amorphous a-polar polyolefins with no reactive groups and free radicals. It has an extremely low permeability for water and is impermeable for moisture under ambient conditions. Due to the amorphous structure, the coating will wet the surface of the substrate up to a physical molecular level.
Self healing. Tests and practice have proven that the material overcomes typical coating rehabilitation problems due to its 1) impermeable character to moisture and gases, 2) easy application, 3) failure-free application to any surface and 4) immediate adhesion to any material.
One of the main characteristics of the material, however, is its self-healing effect. Due to its amorphous behavior and the continuous pressure of the outer wrap or the soil, minor damages will automatically be repaired. It is indeed a smart coating.
Author
Leo van Beugen is managing director of Kleiss & Co. and Pipesurvey International and vice president of Amcorr Products & Services. He has more than 13 years of experience in the development and market introduction of self-healing coatings (smart coatings) and has been involved as an advisor in several onshore and offshore coating rehabilitation projects. He can be reached at Lvanbeugen@kleiss.nl, or 31-78-629.13.13.
Comments