April 2011 Vol. 238 No. 4
Features
Utility Saves By Using Keyhole Technology
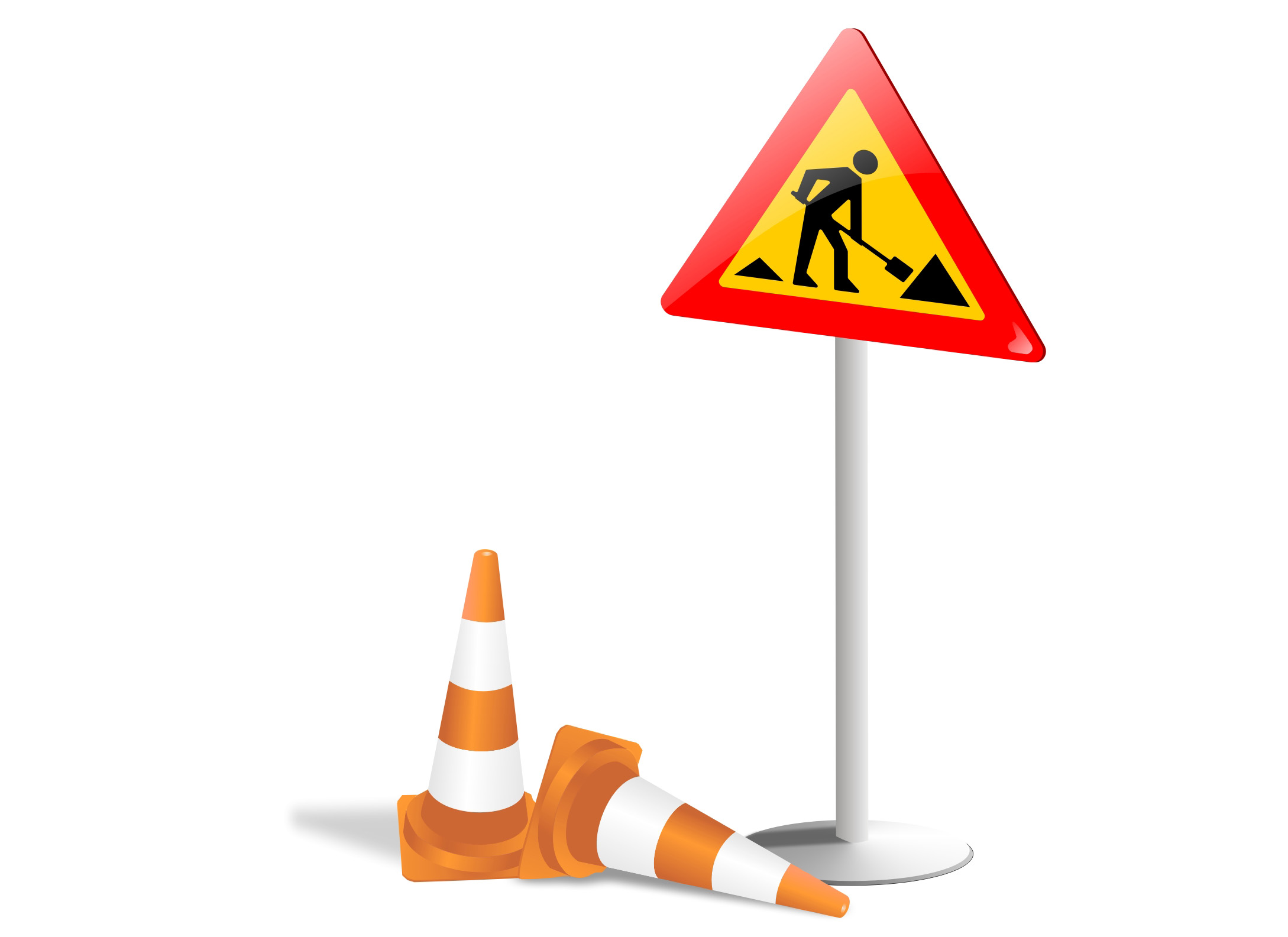
Washington Gas is in the midst of a major project to rehabilitate about 143,000 gas service lines and 1,900 miles of gas mains. Specifically, the utility is renewing the steel service lines by inserting plastic pipe into them, and it is encapsulating – or renewing the life of – the mechanical fittings that join the mostly 40-foot lengths of wrapped steel distribution main to prevent leaks on the couplings.
“Unlike the couplings, the wrapped steel pipe is in really good condition and does not need to be replaced,” says Katie Harkless, Washington Gas project manager – replacement.
Keyhole technology has lowered the cost and improved the efficiency of this twofold replacement project, according to Clayton Munsey, Washington Gas manager – field technologies.
“Making an 18-inch diameter keyhole cut rather than a conventional 3- by 5-foot or 4- by 6-foot utility cut has reduced our costs by approximately 50%. A majority of that savings comes from eliminating the need for the extensive pavement restoration work associated with digging a conventional size hole.”
Repairing the distribution main couplings through a keyhole excavation requires that the location of each coupling be pinpointed before digging begins.
“We do this by sending a tethered camera into the pipeline. At first we were digging conventional holes and physically disconnecting the pipe to insert the camera,” explained Munsey. “Then we moved to a second-generation technology that involves a 45-degree launch fitting for the camera and eliminates the need to shut off the gas flow. We are now evolving to the next generation – inserting a camera into the pipe through a keyhole opening.”
“One of the challenges with keyhole technology comes at the permit stage,” said Tracy Townsend, Washington Gas operating and engineering division head. In the case of the coupling project, keyhole technology entails removing a core of pavement to open up an 18-inch hole. When the job is done, the pavement core is restored to its original position.
“We interact with approximately 100 permitting jurisdictions, and it has taken a team effort to convince the jurisdictions to accept reinstalled and grouted pavement cores as a permanent restoration that won’t lead to the degradation or decreased life of their streets.” Townsend said.
The utility also is using keyhole technology to renew the 143,000 steel service lines. “When we insert the 1/2-inch plastic pipe into the existing 3/4-inch steel service line, we start the project at the meter rather than at the tee connecting the service line to the main,” said Harkless.
In a move unrelated to the current restoration project but related to keyhole technology, Washington Gas worked with a vendor on a project to incorporate a service line tee and an excess flow valve into a single device.
“The idea was to have a combination tee and valve device that can be maneuvered into place through an 18-inch keyhole and will work effectively to close off the gas flow if there is damage to the service line,” said Munsey.
Consolidate Service And Meter Work
Washington Gas turned over meter installation to the underground contractors who install the gas service lines when a residential customer converts to natural gas from another fuel source.
“By eliminating the need for a separate contractor to install the meter,” said Townsend, “we have lowered the installation cost per service by reducing the number of trips it used to take to provide natural gas service to an existing residence to one.”
She added that consolidating service line and meter installation has improved customer satisfaction. “We hope this year to apply the single-contractor procedure in the new housing construction sector.”
Putting service line and meter installation into the hands of the underground contractors required some coordination, according to Townsend. “We refined some processes, educated the plumber associations and HVAC contractors about the change in procedures and provided training and technology for underground contractors.”
Further Cost Reductions
The utility bundled material purchases and combined projects for bids to cut costs. In one case, this strategy saved $500,000, reported Harkless.
“We had three projects involving installation of 12-inch piping at pressure-reducing stations. By treating the three projects as a single project, we were able to purchase all of the piping at the same time and extend a request for bids that bundled the separate projects. Basically, we were saying to potential contactors that if they bid on the package of projects, they are guaranteed a greater amount of work than they might have had if we’d solicited separate bids for each project. This approach created a more competitive bidding atmosphere.”
The utility also went through a strategic sourcing process for all stock materials and bundled large steel orders into single orders to save about $1 million annually, according to Townsend.
“We reassessed our distribution maintenance, repair and operations vendors and reduced the number from about 90 that might supply us with one or two stock items to eight primary vendors that together are able to provide the majority of the components we need.” Townsend said.
Washington Gas found that the rubber compression fittings on the tees connecting plastic service lines to the steel gas mains experienced deterioration and leakage, according to Munsey. Normally, a repair would require welding to remove and replace the tee. The utility, which is replacing about 20 of these couplings annually, was seeking a technique that removed the welding component from the equation.
“Internally, we came up with an idea and worked with a vendor to develop a retrofit that eliminates the need for a welder during removal and replacement of the existing tee,” he said.
The new retrofit device, which has an O-ring seal, fits into the existing tee after the rubber compression fitting on the service line side has been removed – no welding necessary.
“We have been using this retrofit for more than a year and have realized a cost saving of approximately 15-20%,” Munsey reported.
Acknowledgement
This article is based on an interview prepared by Washington Gas for American Gas magazine from the American Gas Association.
Comments