July 2011, Vol. 238 No. 7
Features
Shale Gas Measurement And Associated Issues
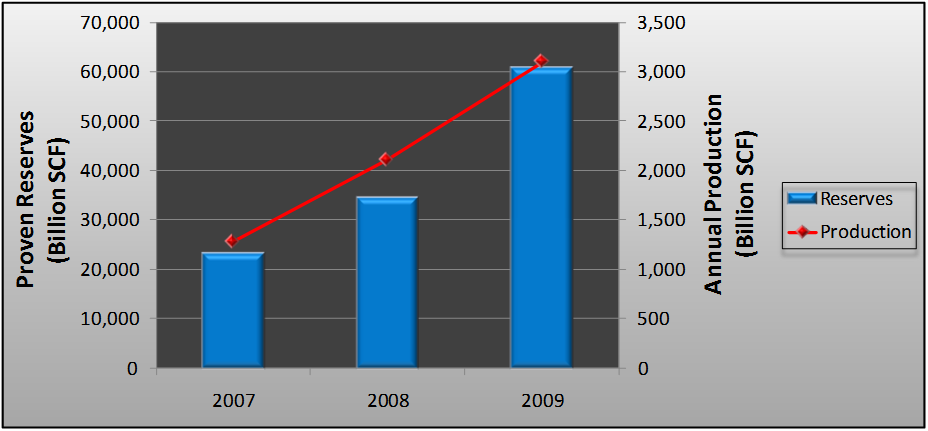
Widespread exploitation of horizontal drilling and hydraulic fracturing techniques has made it possible to extract vast amounts of natural gas previously locked in shale formations throughout the United States. This relatively recent development has likely changed the domestic energy landscape for decades to come.
Figure 1 illustrates just how quickly shale gas production and proven reserves have ramped up in recent years; Figure 2 shows the latest projections for domestic gas production through the year 2035 from the Energy Information Administration (EIA, the federal entity responsible for tracking energy production and consumption in the U.S. and worldwide).
Figure 2. Predicted U.S. Natural Gas Production Trend. (Data provided by the EIA. Date of latest prediction: April 2011.)
Shale Gas Compositions
The production and transport of shale gas is posing some unique challenges for the natural gas industry. The existing infrastructure for producing and transporting “conventional” natural gas, which has been the norm for nearly the past 100 years, has been optimized to efficiently process and deliver gas that meets end-user requirements for heating value, hydrocarbon dew point, and contaminant content. Produced shale gases observed to date have shown a broad variation in compositional makeup, with some having wider component ranges, a wider span of minimum and maximum heating values, and higher levels of water vapor and other substances than pipeline tariffs or purchase contracts typically allow.
Table 1. Examples of Variations in Shale Gas Compositions across the U.S (1, 2)
Table 1 presents some example shale gas compositions from a 2009 study (1). These compositions were taken from shale plays that supply gas to the transmission network and end-users, including the Antrim, Barnett, Fayetteville, Haynesville, Marcellus, and New Albany plays. Table 1 also lists the historical mean values of these same components in pipeline-quality gases around the U.S. (2) (Note that none of the shale gas compositions listed in Table 1 were shown to contain butane or pentane (highlighted in yellow in Table 1).
It is not known if these components were truly absent from the sample gases or, instead, the analyses were incomplete.) Some produced shale gases contain significantly higher amounts of ethane than the historical average of transmission-grade gas, while others have shown levels of diluents or hexanes and heavier hydrocarbons above historical averages. Not only are shale gases different from historical transmission-quality gases, they vary from one formation to another, and even within the same formation. Significant differences in levels of ethane, propane, hexane and heavier components, and diluents (primarily CO-2 and nitrogen) have been seen among the various shale formations. These, in turn, result in significant differences in the heating value, Wobbe number, and other parameters that guide end-use applications of natural gas.
Because of these variations in gas composition, each shale gas formation can have unique processing requirements for the produced shale gas to be marketable. Ethane can be removed by cryogenic extraction while carbon dioxide can be removed through a scrubbing process. However, it is not always necessary (or practical) to process shale gas to make its composition identical to “conventional” transmission-quality gases. Instead, the gas should be interchangeable with other sources of natural gas now provided to end-users. The interchangeability of shale gas with conventional gases is crucial to its acceptability and eventual widespread use in the U.S.
Concerns About Interchangeability
For most of the last decade, prior to the shale gas boom, natural gas demand in the U.S. exceeded conventional gas production and it appeared inevitable that the U.S. would be importing a significant quantity of LNG to meet future demand. With that prospect, there was growing concern that differences between the compositional makeup of imported LNG and conventionally produced natural gas would result in serious combustion efficiency and emissions problems at the burner tip. There was so much concern that the Federal Energy Regulatory Commission (FERC) asked the Natural Gas Council and other interested parties to make recommendations on how to deal with the anticipated problem.
The parties approached by FERC (collectively known as NGC+) subsequently developed a White Paper3 with interim recommendations for addressing limits on natural gas quality parameters to help ensure continued clean and efficient combustion of natural gas at the burner tip. Although the LNG import era is apparently waning, the gas composition challenges posed by an increasing amount of LNG in the gas supply stream have some similarities to those posed by shale gas.
The concept of natural gas “interchangeability,” discussed extensively in the NGC+ White Paper, is what helps ensure clean and efficient combustion at the burner tip, regardless of the compositional makeup of the sources of gas that constitute the supply stream. The NGC+ White Paper defines interchangeability as “the ability to substitute one gaseous fuel for another in a combustion application without materially changing operational safety, efficiency, and performance or materially increasing air pollutant emissions.”
Interchangeability is described in technically based quantitative measures, such as indices, that predict combustion efficiency, emissions, flame stability, and gas-fired equipment performance. These indices have demonstrated broad application to end uses, and can be applied without discrimination of either end-users or individual suppliers. The White Paper recommended interim guidelines on four indices of interest:
1. The Wobbe number for a given area (an index related to energy flow rate to a combustion device) should remain within ±4% of the local historical average or established target gas value, subject to a maximum limit of 1,400 Btu/scf.
2. The maximum recommended limit on heating value (energy content per unit volume of gas) is 1,100 Btu/scf.
3. The recommended upper limit on butanes and heavier hydrocarbons (C4+) is 1.5 mole %.
4. The maximum recommended amount of total inert components (CO-2, nitrogen, etc.) is 4 mole %.
However, rather than establish “hard and fast” gas quality specifications based on these interim guidelines, FERC established a gas quality policy (4) based on five principles:
1. Only quality and interchangeability specifications in FERC-approved gas tariffs can be enforced.
2. Gas quality provisions in tariffs must be flexible to accommodate evolving science, and to allow pipelines to balance safety and reliability with the importance of maximizing supply.
3. Pipelines and customers should develop gas quality provisions based on sound technical requirements.
4. Pipelines and customers should negotiate technical requirements based on the NGC+ interim guidelines.
5. FERC will consider gas quality disputes on a case-by-case basis.
The second and third principles, in particular, recognize that new gas supplies, such as shale gas, should be used where possible, but that the potential impact of unprocessed gas should also be considered in setting acceptable interchangeability limits. Comparing the example shale gas compositions in Table 1 to the interim limits of the NGC+ White Paper, two-thirds of the unprocessed gas compositions have indices outside the interim limits (the out-of-tolerance values are highlighted in red in the table).
If there is sound technical justification that these gases will not cause corrosion or other problems with the end-user, a transmission pipeline operator could accept them for transport. Without this justification, a pipeline operator with gas tariffs based on the interim guidelines could declare the gas to be “out-of-tolerance” and refuse to transport it.
When shale gas is out-of-tolerance per the FERC provisions, the options available to the gas producer and pipeline operator are the same as the options for dealing with other gas supplies with high levels of unacceptable components. Restricting unacceptable gas from entering the transmission pipeline grid is always an option, but is often the choice of last resort, since replacement gas supplies may be hard to obtain. Processing of the gas – extraction of hydrocarbon condensates, dehydration to remove water, and “scrubbing” to remove CO-2 and hydrogen sulfide – is a common approach, but may not be pursued if it is not cost-effective.
Blending of the out-of-tolerance shale gas with other acceptable gas streams or with nitrogen is another approach, but blending must be performed properly to be effective. For example, blending two streams directly at a pipe junction is more effective than injecting one stream after another into a main line and hoping that diffusion between the two “slugs” will adequately mix the two compositions.
Other Shale Gas Concerns
Other concerns with shale gas are not common to those associated with LNG supplies, but will be familiar to anyone dealing with rich, sour, or water-wet production gases. Managing the hydrocarbon dew point (HDP) to meet tariff specifications or avoid condensation of the heavier hydrocarbon components in the gas stream is of particular concern for some shale gas producers. Table 2 lists the amounts of major components of shale gases gathered by one pipeline company from various shale plays in the U.S. (5)
Other pipeline companies have reported similar findings. In Table 2, the amount of hexanes and heavier hydrocarbons in the unprocessed shale gases varies from 0.478% in supplies from the Eagle Ford shale down to zero in Appalachian gas. HDPs can vary just as widely, as can the processing requirements to make the shale gas supplies meet the requirements of the transporting pipelines.
Table 2. Example Shale Gas Compositions Collected from Various Shale Plays by One Transmission Pipeline Operator. (5) (Note 1: Appalachian gas processed for propane, Eagle Ford unprocessed, and Haynesville treated for CO-2. Note 2: The listed hydrocarbon dew point temperatures are at pipeline-operating pressure.)
Where HDPs cannot be easily measured, predicting them by other means can also pose problems. Figure 3 shows HDP data for a sample of Eagle Ford shale gas.6 The HDP of the stream was measured using a Bureau of Mines chilled-mirror analyzer, as shown by the balloon notation on the graph. The HDP curve was also predicted using an analysis of the stream from an onsite gas chromatograph (GC), the Souve-Redlick-Kwong (SRK) equation of state, and various methods of characterizing the hexanes-plus hydrocarbon fraction. The onsite GC was only capable of analyzing separate hydrocarbons through the pentanes, and reported all heavier hydrocarbons as a “C6+ fraction.” The HDP curve was predicted using several different assumptions about the distribution of heavy hydrocarbons in the C6+ fraction.
As expected, the assumption that the fraction was entirely made up of normal hexane under-predicted the dew point temperature by 10°F (i.e., the dark blue curve on Figure 3). Using this assumption could easily lead to the use of sampling equipment that is not adequately heated, produced gas that is not adequately processed, and similar problems. Other characterizations, such as the GPA 60/30/10 C6/C7/C8 split and the 47/36/17 C6/C7/C8 split, produced HDP curves that predicted an HDP temperature higher than observed. As long as such over-predictions are not severe, these characterizations could be used to predict HDPs in those instances where direct measurement of the HDP temperature is neither practical nor economical.
Figure 3. Example of Problems Associated with Hydrocarbon Dew Point Prediction for a Rich Shale Gas Stream. (6)
Monitoring Shale Gas Quality
Diluents and contaminants, such as water vapor, oxygen, and hydrogen sulfide, may be found in shale gas and thus must be monitored using special measurement equipment. The measurement accuracy of these devices can vary greatly, depending on the equipment. For example, length-of-stain tubes (sometimes called Draeger tubes) and laser-based analyzers are both available to measure the moisture content of a natural gas stream. Length-of-stain tube kits can be purchased for a few hundred dollars, but current standards for their use cite an accuracy of ±25% of reading. A single laser-based analyzer costs roughly two orders of magnitude more than a Draeger tube kit, but manufacturer-stated accuracy is typically ±1% of reading.
Selection of the best equipment for monitoring a particular shale gas stream should take into account not only the initial capital cost, but also operational and maintenance costs, plus, the potential costs associated with inaccurate diluent and contaminant measurements – including additional gas-processing costs, costs associated with pipe corrosion or other equipment damage, and expenses associated with unanticipated shut-ins. Contaminants, such as CO-2, hydrogen sulfide, and water vapor, must stay within tariff limits for a transmission pipeline or local gas distribution company to accept a gas stream and errors in gas volume or heating value of even a fraction of a percent can be very costly over time.
When selecting a system of equipment to measure shale gas quality, some items the pipeline operator may want to consider include:
* Parameters to be measured (e.g. hydrocarbons, diluents, contaminants, pressure and temperature, etc.);
* Measurement accuracy and repeatability limits and tolerances;
* Equipment costs (roughly proportional to accuracy);
* Desired sampling frequency and timeliness of measured data; and
* Data interfaces, communications systems, and SCADA requirements.
Closing Thoughts
Shale gas poses some unique challenges when it comes to the measurement and control of the compositional makeup of the gas transported to consumers. This article outlines those challenges and provides information and strategies for properly addressing them. Production of natural gas from shale formations is in its infancy and the natural gas industry is still learning about the nuances associated with measuring and transporting it effectively. New research initiatives are planned to learn more about shale gas sampling and analysis methods, so look for new information on these subjects in the months and years ahead.
Authors
Darin L. George, Ph.D., holds the post of Senior Research Engineer in the Fluid Dynamics and Multiphase Flow Section, Mechanical Engineering Division of Southwest Research Institute, San Antonio, TX.
Edgar B. Bowles, Jr., M.S., holds the post of Director, Fluids and Machinery Engineering Department, Mechanical Engineering Division of Southwest Research Institute, San Antonio, TX. Ph: 210-522-2086, e-mail: Ed.bowles@swri.org.
References
1 Bullin & Krouskop, “Compositional Variety Complicates Processing Plans for U.S. Shale Gas,” Oil and Gas Journal, March 9, 2009.
2 “Variability of Natural Gas Composition in Select Major Metropolitan Areas of the United States,” Gas Research Institute, Report No. GRI?92/0123, 1992.
3 Natural Gas Council, White Paper on Natural Gas Interchangeability and Non-Combustion End Use, Feb. 28, 2005.
4 FERC Docket No. PL04-3-000, June 15, 2006.
5 “El Paso Energy Shale Gas Composition Variation,” AGA Shale Gas Workshop, Sept. 15-16, 2010.
6 Private communication between Dr. George and a Texas gas pipeline operator.
Comments