May 2011, Vol. 238 No. 5
Features
A/C Mitigation Strategies Light Up Corrosion Seminar
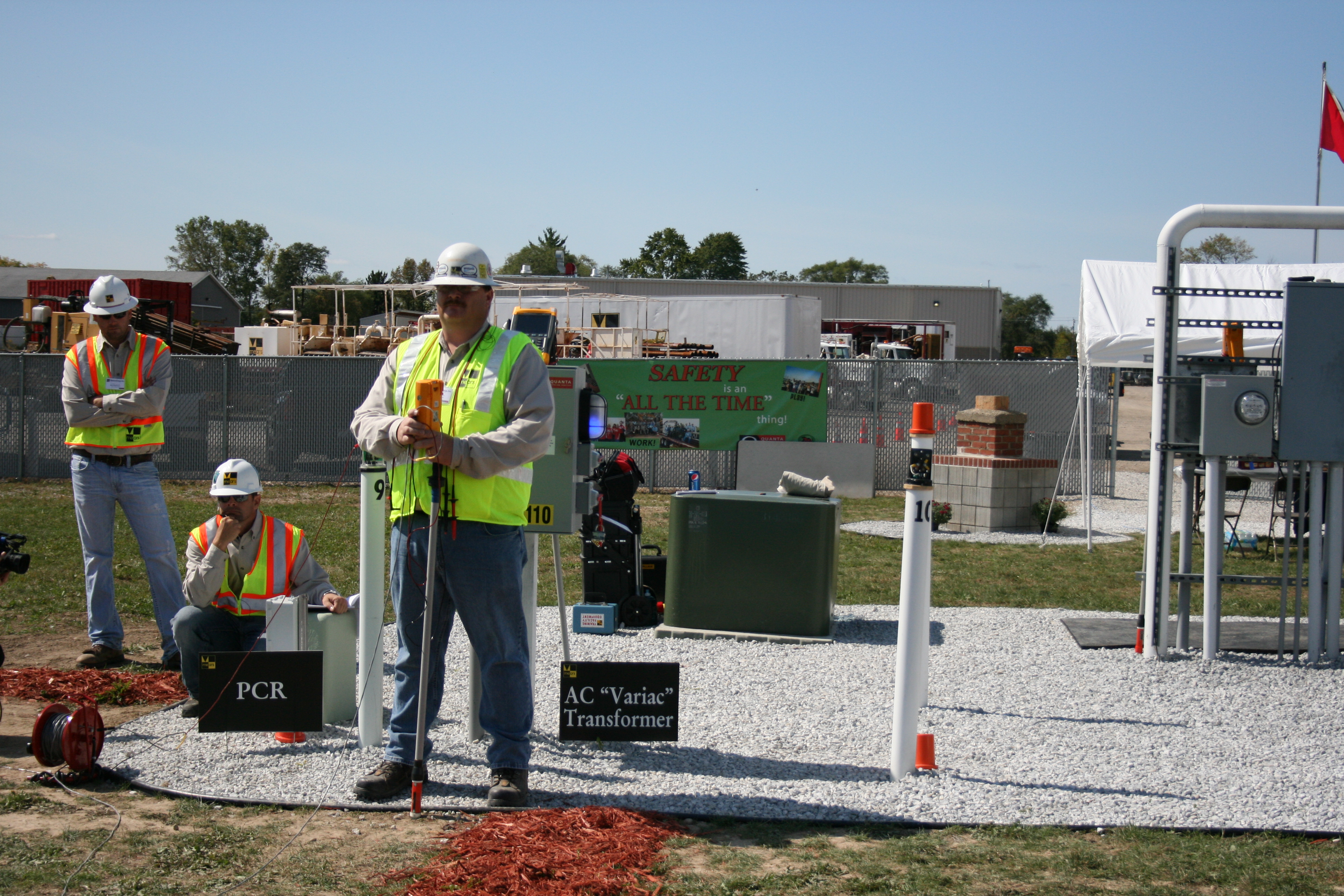
In the U.S. and many other countries, shared land use by pipelines and other utilities is common. This trend means the number of overhead high-voltage transmission lines parallel to and sharing a common corridor with underground pipelines has increased, and they all need grounding to prevent interference by alternating current (A/C).
At its fourth annual integrity seminar, Mears Group, Inc., part of Quanta Services, focused on the topic of A/C mitigation. A combination of classroom presentations and a field demo at Mears’ state-of-the-art field test facility in Rosebush, MI attracted more than 75 pipeline integrity personnel.
Kevin GarrityVice President of Integrity Solutions for Mears Group, Inc., began by discussing pipeline integrity problems in shared power line rights-of-way.
“Transmission systems with voltage of 69 kV or greater are the types of operating systems that contribute to the electromagnetic interference on buried structures,” he said. “In corrosion, we work a lot with DC so we’re looking at a rectified wave form. With alternating currents it’s a constantly changing magnitude and polarity. When this occurs, it causes expanding and collapsing electro-magnetic fields.”
Garrity continued, “When we put a pipeline underground with a coating on it, we have built a transformer. The primary side is the overhead power line with these electro-magnetic fields that are generated in a perpendicular or normal direction of the flow of current. We have an air gap between the primary and secondary side.
“We have a soil environment that has a resistance component to it and then we have, for the most part, protective coatings that have extremely high dialectic strength, particularly the newer coatings. The higher the dialectic strength, the greater the insulation between the primary and the secondary. As a result, these waves propagate down the length of the overhead conductor and introduce an A/C voltage onto the buried pipeline. This can result in high voltages on long sections of a pipeline,” he said.
Two conditions, phase-to-ground faults and lightning strikes, can place large magnitudes of current in the earth and create large voltage differences. That current will flow to underground pipelines and can burn through the coating. In some instances, it may even burn through the pipe, causing a failure, Garrity explained.
“From the A/C corrosion standpoint and the A/C safety standpoint, we’re really looking at the steady state condition that occurs during the electro-magnetic induction. The magnitude is a function of the line current, and not necessarily the voltage, but with higher voltage power lines we get more current flowing,” he said.
Garrity said the power that is transferred is proportional to the length of parallelism and line current, and inversely proportional to the separation difference. So, as pipelines move out of the corridor, the magnitude of the voltage decreases, but at the point of diversion is where we see peak conditions in terms of voltage failure levels.
“We’ve always known A/C is a potential safety problem,” Garrity said.
“Typically, aboveground pipe is grounded for safety. If the voltage on the pipe when measured with respect to ground is less than 15 volts, that pipeline is generally considered safe. That number is based solely on the assumption that the electrical resistance on the human body between your hands and your feet is about 1,500 ohms. The safe let-go current is about 10 milliamps of A/C. More could adversely impact our central nervous system.”
Garrity said the NACE standard is very conservative.
“It is either less than 15 volts or less than 6 milliamps of current. Safety has always been the concern, but we now know that A/C corrosion can and does occur at much lower voltages,” he said.
“The cause of A/C corrosion on pipelines is basically induced A/C current leading to A/C current discharge at coating flaws. Contributing factors are better coatings, which mean smaller coating flaws. The amount of bare metal surface in contact with the earth is smaller, so the current density increases. Also, low soil resistivity leads to high discharge currents at induced A/C voltage.
“What we know today based on research is that if current density is less than 20 amps per meter squared, we should not expect to have any A/C-induced corrosion. In the range of 20-100 amps per meter squared, corrosion may occur, although corrosion is unpredictable in this range. When levels reach over 100 amps, it is a certainty that corrosion will occur.”
In a subsequent presentation, Professor Joe Payer from the University of Akron focused on A/C-induced corrosion. Payer spent several years at the research organization Battelle before moving in 2009 to the University of Akron, which launched a program offering students a degree in corrosion engineering in fall 2010.
Regarding A/C-induced corrosion, Payer said not enough is known about the mechanisms that cause it and what controls it. Study of A/C-induced corrosion will be a cornerstone of the new program. He compared today’s understanding of A/C-induced corrosion to stress corrosion cracking, which was well-recognized but poorly understood until recently.
“Our knowledge of corrosion cracking–‘How does that occur, why does it occur, can we test for it, can we control it, can we mitigate it’–really took a number of years to develop. With A/C-induced corrosion, we are at that same early stage of recognition. We know it’s a problem, but we don’t have a strong technical basis for controlling it.
“Corrosion is damage that occurs to a material in contact with the surrounding environment. It is always a combination of materials, properties and environment,” Payer said. He noted that if you place steel in an unfavorable environment, one of three things can happen: nothing will occur; it corrodes actively; or it exhibits passive behavior. With passive behavior the material is unstable and reacts, but the reaction is the formation of a metal oxide that protects the material.
“Regarding A/C-induced corrosion,” Payer said, “the magnitude of the current is the key from a corrosion standpoint. The fewer and smaller holidays exacerbate the problem, and higher levels of CP actually exacerbate the problem as well. A hypothesis is that with high levels of induced A/C, we drive the surroundings of these exposed areas to a very high alkaline environment and then we get non-protective corrosion products as we move from passivity to active corrosion. Another component is cathodic disbondment.
“We’re only at the early stages of being able to reproduce this in the laboratory and understand it. The mitigation methods don’t have the strong technical basis to support them. That is needed to feel comfortable.”
Instead, Payer advocated a strong, viable industry and academic research program into this issue.
Robert Checketts, vice president of operations, IT and engineering for Kern River Gas Transmission Co., outlined the significance of A/C interference on the Kern River Pipeline system.
Kern River was issued a special permit by the U.S. Department of Transportation Pipeline and Hazardous Materials Safety Administration (PHMSA) in 2008 to increase the maximum allowable operating pressure
(MAOP) from 1,200 psig to 1,333 psig and station MAOP from 1,250 to 1,350 psig.
As a result of that application, Checketts remarked that company personnel became much more knowledgeable about A/C interference and their system in general.
He said the Kern River line was constructed in 1998 and coated with 3M’s 206N fusion bonded epoxy (FBE) coating. In 2003, a 36-inch loop line was laid, coated with 3M’s 6223 FBE product with a 6253 abrasion-resistant overlay. The company has performed several A/C-related studies and assessments including: A/C fault current studies; A/C step and touch potential mitigation; A/C interference modeling and mitigation; annual A/C voltage potential monitoring; pipeline inline inspection and direct assessment.
Checketts said Kern River studied its entire pipeline system and identified 314 miles of collocated right-of-way where A/C interference could potentially affect the system. As part of the company’s permit conditions they did a comprehensive A/C assessment in the collocated areas. This included a review of historical A/C voltages and soil resistivity data; review and integration of the inline inspection external metal loss anomaly data; review of pipeline direct examination data; close-spaced and test station A/C voltage and soil resistivity surveys; and calculation of pipeline A/C current density of an assumed coating holiday size of 1 cm squared.
Mears was hired to engineer and install Kern River’s mitigation program, which included installing grounding to reduce induced A/C voltage and current discharge below the initiation threshold for external corrosion. Grounding consisted of installing horizontal zinc ribbon 10 feet off the pipe’s centerline. Zinc ribbon is connected to the pipeline at 1,000-foot intervals and connections include installation of polarization cell replacements (PCR) and A/C current density monitoring coupon test stations. The company installed 60 miles of horizontal zinc ribbon grounding and 469 current density monitoring coupon test stations.
As part of its monitoring program, Kern River conducts quarterly readings of current density at monitoring coupon test stations. This includes: 24-hour monitoring at selected areas each quarter and integration of power line load data; engineering assessments at locations greater than 20 amps per meter squared; installation of mitigation at locations greater than 50 amps per meter squared; A/C assessment of any power line addition, expansion or capacity increase; and engineering assessment of installed mitigation integrating inline inspection and cathodic protection close interval survey data every four years.
Checketts said A/C interference has been mitigated in all areas.
“Quarterly monitoring has confirmed successful design and performance of the installed system. Dual criterion evaluation of ongoing monitoring and integration of inline inspection data will ensure A/C interferences continue to be mitigated.”
Mark Hereth of Houston-based P-PIC, LLC, focused on the special permitting process that enables an operator planning to build a new pipeline, and in some circumstances operating an existing pipeline, to be operated at 80% of specified minimum yield strength (SMYS). He said that new supply is driving increased capacity and new infrastructure.
“A/C interference is only going to be a continuing issue as the Federal Energy Regulatory Commission pushes for more co-location into utility corridors, particularly in rights-of-way with high voltage power lines.”
Hereth said design for 80% SMYS is in the ASME code but has never been adopted by the Office of Pipeline Safety (OPS).
“Several pipelines submitted applications in 2005-06 and PHMSA held a public meeting in March 2006. Spectra Energy, Alliance Pipeline and Kinder Morgan received approvals in 2006. Several other pipelines submitted applications after that,” he said.
“The technical aspect of this application process involved building on what we’ve done with integrity management. The technical aspect was for us to take the same rigor in looking at A/C threats and how we assess and mitigate risk, and then expand them to design and construction,” he explained.
This ultimately led to the development of 47 special permit requirements. These include: pipe design, FBE coating, manufacturing quality control, construction quality control, pressure test to 100% SMYS and 1.25 MAOP, post-construction dent tool repair greater than 2%, a rigorous commissioning plan, integrated external corrosion control, more stringent gas quality control and following Common Ground Alliance (CGA) best practices for damage prevention, Hereth said.
The integrated external corrosion control included CP in service within one year; baseline ILI within three years; interference current surveys within six months of operation; corrosion surveys within six months of CP in operation; CIS within two years of operation and more stringent anomaly evaluation criteria and ILI within seven years of commencing operation at 80%.
“All companies completing this process became much more familiar with their systems and sleep better at night as a result,” he said.
PHMSA issued a proposed MAOP rule in October 2008 that became effective later that year, but according to Hereth, it did not fully address existing pipelines and had the effect of requiring them to seek special permits.
At the close of integrity seminar classroom sessions, the afternoon was spent outside at Mears’ testing facility, where a field demonstration of induced A/C was provided. Differences were demonstrated in pipeline protective coating quality, application of cathodic protection to buried piping, induced A/C effect on buried piping and the effectiveness of A/C mitigation.
For more information: Bill Marshall, Mears Group, bill.marshall@mears.net.
Mears is a turnkey EPC Integrity Solutions company completing Direct Assessment, Internal Line Inspection, AC Mitigation and Hydrotest projects for Liquids and Natural Gas Transmission and Distribution Companies and the Power Industry nationwide. Mears employs a large staff of Engineers and NACE-certified personnel to assist with turnkey projects worldwide. Call 800-632-7727 to talk to an Integrity Solutions expert.
Comments