September 2012, Vol. 239 No. 9
Features
Training Seminar Held For TCPL Technical Corrosion Staff
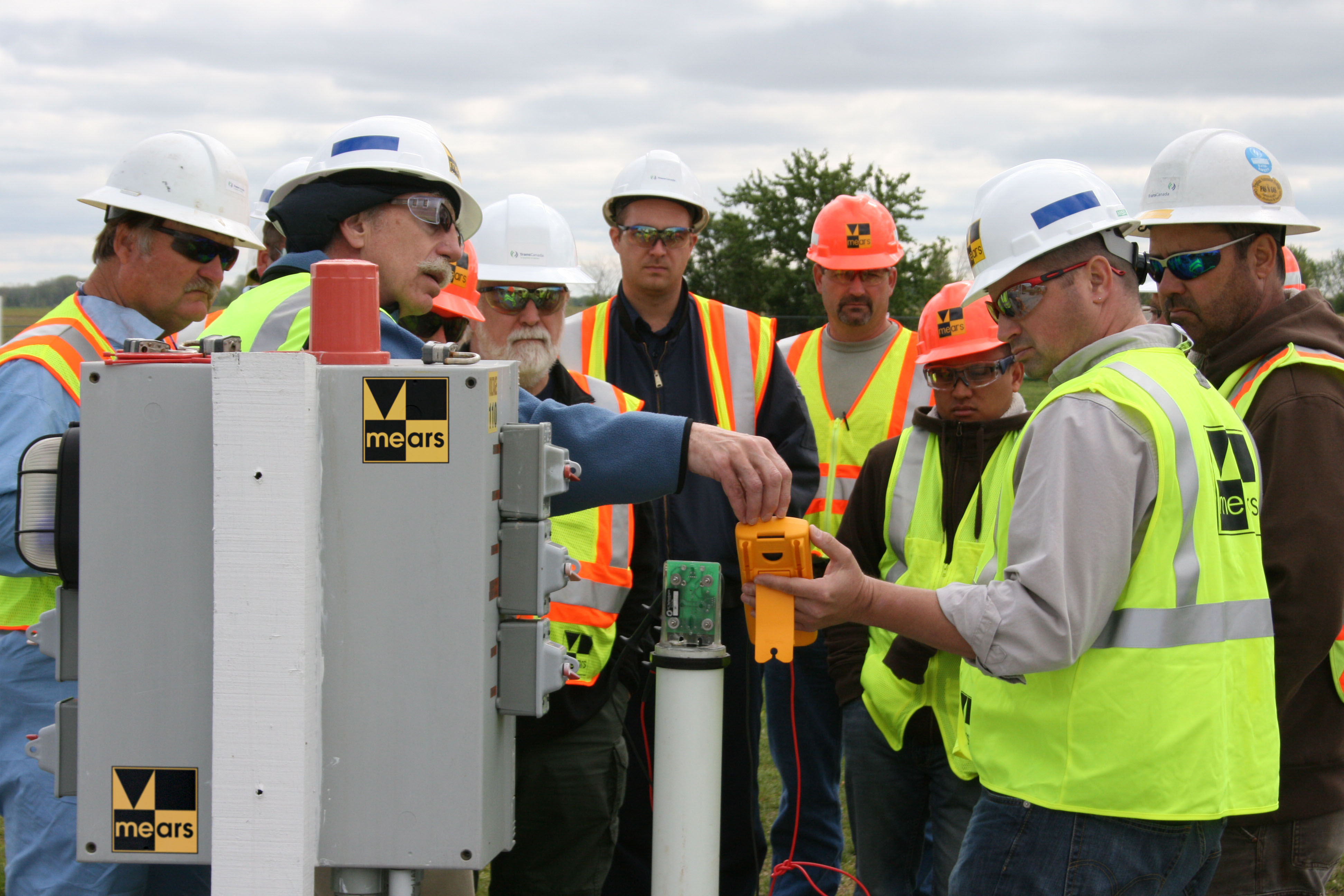
In December of 2011, Mears Group Inc. was approached by TransCanada Pipeline (TCPL) to create a viable training seminar for approximately 60 TransCanada technical corrosion staff from the U.S. and Canada.
They wanted to incorporate their in-house techniques with some of the industry standard techniques that are used at Mears. They also wanted to take advantage of the Mears Michigan Corrosion Training Facility. Mears accepted.
TransCanada specified that the following mandatory topics were to be included in the seminar:
1. Stray Current and Interference Testing
2. CP Theory and Testing Methods
3. Casing testing procedures along with PHMSA requirements
4. Coatings applications for test station CAD welds using approved TransCanada procedures and components.
Each seminar segment was designated to have its own instructor with intimate familiarity of the subject. Through a collaborative design effort it was decided that the coatings and CP Theory segments would have a TransCanada instructor along with several support personnel. The Stray Current and Casing segment instructors would be provided solely by Mears – Phil Simon, Kris Hoisington, Lyle Buckingham and Kevin Northon — who provided classroom and field training.
Each seminar segment was broken down into a classroom/teaching portion and a field/hands-on portion. Because the in-classroom teaching portion generally preceded the hands-on portion, the seminar segments had to be able to occur in the training facility simultaneously. The field portions of the classes were designed to accommodate all of the demonstration topics simultaneously so they did not interfere with one another.
Each segment covered the aspects shown below.
1. Stray Current and Interference Testing
a. DC Stray Current
b. AC Stray Current
c. DC and AC Stray Current Mitigation Methodologies
d. DC and AC Stray Current Detection Methods
2. CP Theory and Testing Methods
a. TransCanada CIS and DCVG Hybrid Testing Procedure and Demonstration
b. Analog DCVG Testing and Demonstration
c. Current Attenuation Survey
d. ACVG
3. Casings
a. Testing Procedures Classroom Explanation and Field Demonstration
b. Testing Procedures Field Demonstration
4. Coatings
a. TransCanada approved coatings applications using:
i. Mastic Coating
ii. SPC 2888
iii. Kema Coat
b. Pipe Surface Preparation
c. Accelerated Coating Application Method
With the large amount of material that needed to be covered, each class became approximately 4 hours long with a total seminar length of 2 days. The training seminar was very well received by the participants with requests for possible additional training at the Mears & NACE training facility in future years.
TransCanada’s Manager of Pipe Integrity Corrosion Prevention, James Card, stated “TransCanada has hosted an Annual Corrosion Control Training Conference for many years and this was the most educationally rewarding and value added session in my 5 years experience of attendance. All of our Corrosion Engineers, corrosion Specialists and Corrosion Technicians have gained a greater understanding for the cathodic protection related tools, procedures and applications used in this training.
The Mears facility is top notch and I strongly believe we will use this facility again very soon for additional training of our personnel. I would like to thank the whole Mears team along with TransCanada’s corrosion control professionals Yvan Fournier, Chris Phillis and Richard Christman who worked many hours with the Mears team to provide the best TransCanada Annual Corrosion Control Training Conference to date.”
This training event is an example of the technical expertise available at Mears combined with TransCanada’s need for theory and hands-on training for its field personnel. This training will create a better trained TransCanada technical group to service the needs of the pipelines and TransCanada’s clients.
Comments