April 2013, Vol. 240 No. 4
TechNotes
Struggling With Mobility To Improve Operational Integrity, Safety And Your Bottom Line?
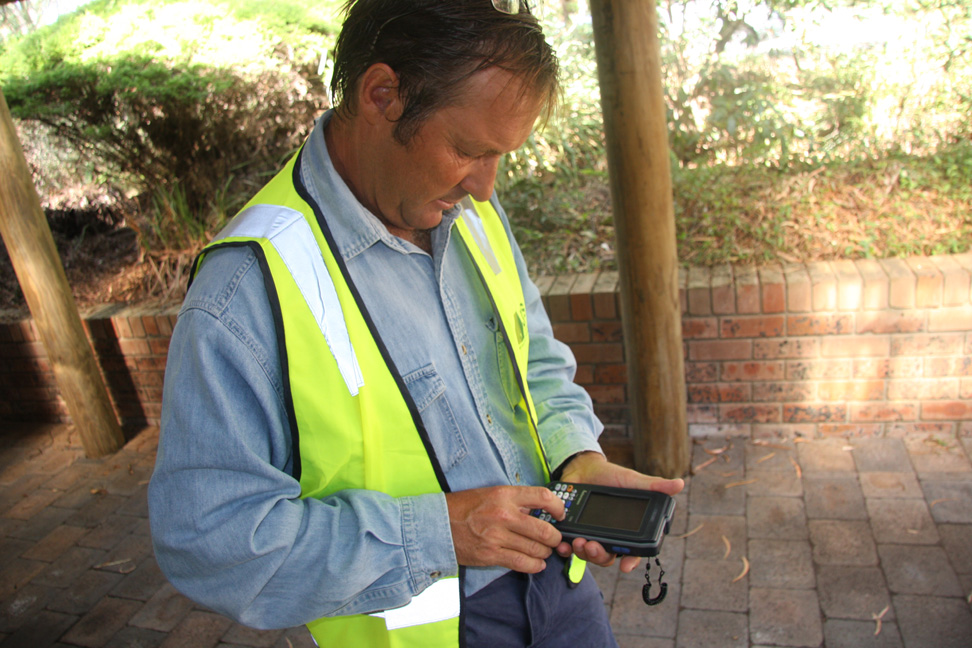
Operators and service contractors in oil and gas, chemicals, and pipelines are constantly searching for new solutions to help them improve their operations, safety and environmental compliance, and of course the financial “Bottom Line.” So, why do many companies struggle with leveraging mobile technology for improving their operations?
Often the struggle begins with selecting a mobile device. While this issue may be putting the proverbial cart before the horse, it is a valid concern, since a large percentage of your mobile technology investment is dedicated to equipping your field force with a tablet, handheld, smart- phone, or a laptop. Issues such as operating systems: Android, iOS, or Windows, rugged vs. non-rugged, intrinsic safety, WiFi capabilities, screen size, and battery life all need consideration before selecting a device for your fleet.
By selecting the “right mobile tool” for the job, operators and contractors can leverage features such as scanners, cameras, GPS, touchscreens, and telemetry. Consider the workforce that receives job orders electronically. They will know the exact location of the asset with directions if needed. Onsite they can easily confirm the asset id via barcodes or rfid, document the condition of the asset on their mobile device, and possibly capture photos if conditions allow.
Then, the worker can perform the job with an application that guides the procedure and integrates any supporting safety protocols. All the while, he has access to parts inventory, reference manuals, and drawings to assist him. Telemetry can be used for tracking mobile equipment and collecting usage data that aids in maintenance reporting and justifying future equipment purchases. By leveraging your mobile device’s ability to capture job data, assist work flow, and validate procedural and safety requirements, your operation starts realizing performance improvements across the board.
Designing and programming a mobile application is another roadblock that most companies encounter. Often, companies default their mobile strategy to their ERP or Accounting system. This approach is the most common and typically results in expensive and unsuccessful mobile implementations. Choosing a Mobile Enterprise Application Platform “MEAP” is the most important step for achieving operational improvements in the field.
The primary requirement for any MEAP is the ability to design and prototype applications that match your field staff’s work flow so you can gain user acceptance early and often. Another requirement is the ability to build an application once with the capacity to deploy native code to a variety of mobile devices. Now your selection of a mobile device is not so risky because you will have the ability to run your application on any device type, allowing for “BYOD” bring your own device, mixed fleet deployments. This can translate to a huge savings on hardware and development costs because you will have a pathway for device upgrades, without redeveloping the application. Your ROI on mobility becomes sustainable.
As your mobility strategy gains momentum, operations can expand the scope of performance indicators to include productivity gains in the back office. A well-designed mobile application will integrate with your ERP, asset management and accounting systems to facilitate data transactions such as invoicing, inventory management and compliance tracking. The administrative staff will benefit from timely electronic updates from the field, legible standardized job reports and automatic data importing into back-office systems, eliminating the drudgery of clerical data entry.
Management benefits from faster status reports from the field because the time from the field-data capture to administrative processing is reduced dramatically from weeks to days, sometimes even hours, positively affecting financial performance such as cash flow, days-sales-outstanding, and inventory planning.
In addition, management’s compliance burdens become lighter due to superior electronic record keeping, since all field data, EHS documents, and digital signature approvals are archived and available for on demand reporting. Imagine no more scrambling through stacks and folders of paper documentation when a regulator, customer or contractor challenges with an audit.
There is no doubt about it; quit struggling with mobility and start implementing. Operators and service contractors can gain improvements in operational integrity, safety, and positively affect their respective bottom lines with a flexible mobile platform that provides a device upgradeable pathway, the ability to work in the field without WIFI signal, the ability to archive and recover data in case of a device failure and streamlines business processes. This results in higher productivity, lower operational risk and improved financial bottom lines.
Comments