July 2013, Vol. 240 No. 7
Features
Risky Business: Safety compliance rules are changing. How will you respond?
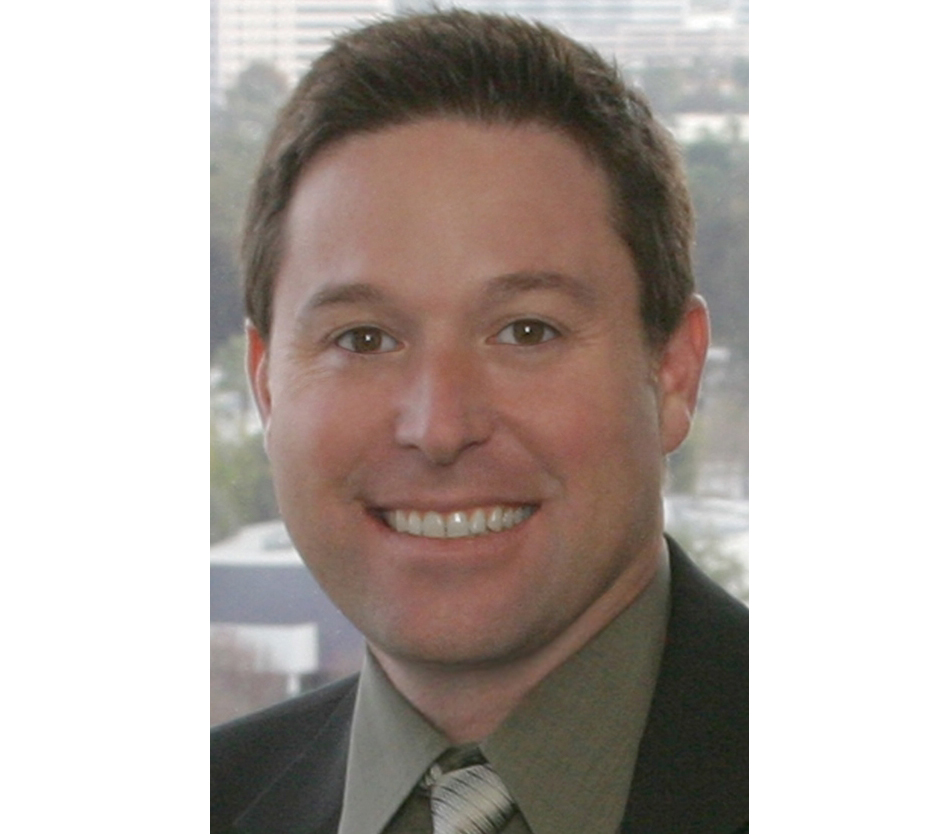
Every energy company CEO has safety and compliance (or the lack of it) in the back of his mind as he goes through the day.
Events like a BP-magnitude disaster conjure up worst-case scenario images of loss of life, federal investigations, CNN and FOX news reports, billions of dollars in fines — and damaged careers.
It’s difficult to be confident that your company is prepared for a major incident. After all, who can forget what BP CEO Tony Hayward said to shareholders just a few days before the horrific $30 billion Gulf tragedy: “Safety remains our No. 1 priority, and I’m pleased to report we can see clear progress.”
So what can you do to help your company’s executives sleep well every night — and not have images of safety disaster drifting into their thoughts?
The traditional response is to buy or build a check-the-box safety compliance system that prescribes the “correct” action for every process step and possible outcome. These invariably include forms and checklists, and usually assign checkers to check the employees responsible for filling out forms in the field. Layered on top of the forms are consulting firm programs to generate “safety consciousness” by using posters, events and employee-safety committees to build awareness and enthusiasm for following safety rules and filling in the boxes correctly.
This approach has served the industry for decades, but it’s no longer good enough.
Just ask an industry veteran such as Casey Davis, vice president of Health Safety and Environment at Wild Well Control Inc., a leading oil industry emergency response company.
“Energy companies develop massive volumes of documentation for safe operations that say, for instance, ‘This is how we safely manage our drilling operations,’” he said. “The problem is not everyone reads these seven-volume manuals — or they don’t read them carefully enough. Or they don’t follow the procedures captured there closely enough.
“There are many potential risks in energy development, such as allowing an inexperienced hand to run a critical safety system without adequate supervision, or placing a supervisor with a reputation for taking shortcuts in charge of vital tasks. Missing equipment inspections or audits. Failing to properly test safety systems. Response plans that are out of date. Those are just some of the things that can lead to a crisis.”
How does company management meet this challenge?
The answer is a well-designed, integrated management system, which many oil and gas industry executives and regulators now consider a necessity.
Instead of treating safety as something outside normal employee routine, an effective integrated management system instills safe practice into every company management process and makes it an intrinsic aspect of each job description. Like brushing teeth and other personal hygiene habits, worksite safety becomes a pervasive, ever-present aspect of every decision, task and outcome. There’s no need for posters or lunch-time committee meetings because every employee embraces safety as a given, just like using a toothbrush every morning.
Today’s standards are higher and regulators are under the gun to ensure better results. To get to the next level of safety performance, energy sector regulators throughout the world are beginning to embrace this philosophy.
U.S. regulators have long supported the use of management systems to improve compliance performance. They are now putting teeth into compliance evaluation and enforcement, and the costs can be staggering. Most recently, in response to a number of significant safety incidents, the National Transportation Safety Board called for comprehensive safety management systems for all aspects of business operations.
The Pipeline and Hazardous Materials Safety Administration (PHMSA) said in a report that safety management systems are critical to “continuously identify, address and monitor threats to the safety of the company.” A PHMSA advisory committee, consisting of industry participants, regulators and subject-matter experts, is developing high-level guidance to help operators build effective safety management systems.
Canada’s National Energy Board (NEB) is also clearly behind this approach to safety, stating at a recent conference, “The NEB believes that the implementation of robust management systems is an essential component to the development of a strong corporate safety culture.”
And, it intends to use it to guide enforcement. In 2011, the NEB released a regulatory change notice with clear and detailed expectations for regulated company management systems that parallel PHMSA guidelines.
A company’s management system must provide a strong foundation for a culture of safety, strongly affirmed by organization leadership, rigorously documented, known to all employees and consistently implemented from corporate office throughout all levels of the company.
This goes well beyond a check-the-box safety compliance system or a “safety awareness” program with posters and committee assignments.
Since 1985, Interliance Consulting Inc. has helped clients throughout the world improve operating, financial and compliance performance by upgrading their management architecture.
The primary objective of any management system is to help the client consistently make and execute better safety decisions at all levels of the organization. To do this, a management system project assesses and re-architects client business management systems to simplify and align decisions, so every employee from CEO to field technician can execute the company plan.
The critical first step in the process is defining the scope of management system (what functions are to be managed) and system objectives (what are the system’s key outputs). These provide the criteria for detailing performance targets and deliverables, and determining how management system performance will be objectively measured. This also supplies the framework for evaluating current operations and serves as the base for management architecture design.
Every robust management system must incorporate six essential elements: clear policy and management processes; performance measurement and feedback; accountabilities; risk management and planning; effective employee training and evaluation; and routine reviews. The project assesses in detail the company’s current management system and its operation to determine what is actually occurring in the field.
This assessment is invariably enlightening; there is almost always a gap between headquarters belief and the actual situation.
Even minor procedural discrepancies can have surprising consequences.
For example, a U.S. energy company experienced a fire at one of its Canadian operations. It executed its emergency plan and dispatched a highly trained response team to the scene with equipment from the U.S. Unfortunately the team was stopped at the border for lack of proper documentation. During the critical initial hours of the emergency, firefighting equipment sat in a truck while the company’s top-responders directed operations by phone.
Another example: A safety management system assessment for a major oil equipment corporation identified three separate departments with duplicative and conflicting approaches to safety practice, which could actually reduce safety performance in areas of overlap.
A thorough management system assessment goes well beyond measuring field performance and safety incident rates. It looks for symptoms of management architectural flaws or immaturity. For example, the presence of management “silos” suggests that functional planning and execution may be inconsistent or unreliable in parts of the organization. An excess of management operating committees is symptomatic of authority misalignment — committee meetings are needed to negotiate issues created by overlapping or poorly defined responsibilities.
Once system performance criteria is established and assessment results are in hand, it is possible to discern management system gaps, identify relevant stakeholders and their interests, and design alternatives that will best achieve results.
Integrated management system design is a detailed, multi-step process more akin to an engineering construction project than a typical consulting engagement. This involves identifying and defining system functions and sub-functions, determining their supporting processes, and mapping overlaps and interactions throughout the company. The project must also align functional and process aspects of management system performance with other relevant functions in the organization, such as maintenance, operations and engineering. This requires an understanding of stakeholder needs, regulatory and management requirements, and the basic practicalities of day-to-day field operations.
Perhaps the most important, and sometimes most difficult, stage of a project is implementation of the system within the company. This requires use of a formal management-of-change process that maps out all of the implementation requirements from high-level executive management sponsorship to documentation of specific responsibilities and duties. And, this also requires continuing support of the implementation process until everyone in the company is thoroughly familiar with their role in delivering superior results.
An effective management system provides a comprehensive set of policies, procedures and responsibilities that defines how the company ensures performance, measures results, manages change and continuously improves performance over time. It is a living tool that guides the activities of everyone in the organization.
The benefits are immediately obvious once the modernized management system is in place. Wild Well’s Casey Davis describes the results for his company by saying, “Our safety management system defines every procedural element so that if a regulator asks, ‘How do you know — and how do you make sure — that every safety system is functioning and fit for duty?’ We can show them the steps, show them how our people are trained and that their individual competency is validated so the likelihood of a disaster is much less than if the company had purchased a basic health, safety and environmental (HSE) management system.
“When a regulator does a thorough audit of our company, they can tell that we’ve done our work ahead of time and in anticipation of being compliant with major regulations — and a lot of the credit goes to our management system.”
However, a well-designed management system can do much more than simply satisfy regulators.
“The project easily paid for itself, saving us more than $2 million per year. With our HSE management system in place, we have lowered our underwriting costs and have driven our equipment or personnel losses to zero,” Davis said. “We avoid injuries and illnesses that have to be managed and that have to be paid for. Our commitment to safety enables us to work for world-class clients who expect safe operations when we’re on their site or in their facility.”
An integrated management system significantly elevates performance in “can’t fail” functions, such as Health and Safety, Environment, Regulatory Compliance, Risk Management and Emergency Response. However, the largest financial return comes from re-architecting core business functions, such as operations and maintenance, capacity growth, marketing and sales, business planning, and financial management.
Get ready for the new world of safety performance. Expectations are higher. Regulators are more sophisticated and tougher. The cost of failure continues to grow. A well-crafted, formal safety management system is now essential to every energy sector company.
So, how can one sleep well at night? Modernize and upgrade the company’s management systems and drive performance to new levels. If it’s done right, the company will be safer, more effective and more profitable as a result.
As one regulator deftly points out, “Safety compliance is paramount. Why? Because safety is what allows you to go home at the end of the day… and effective compliance is what allows you to come back the next morning.”
Comments