September 2014, Vol. 241, No. 9
Features
New Smart Coatings Detect and Mitigate Corrosion in One Step
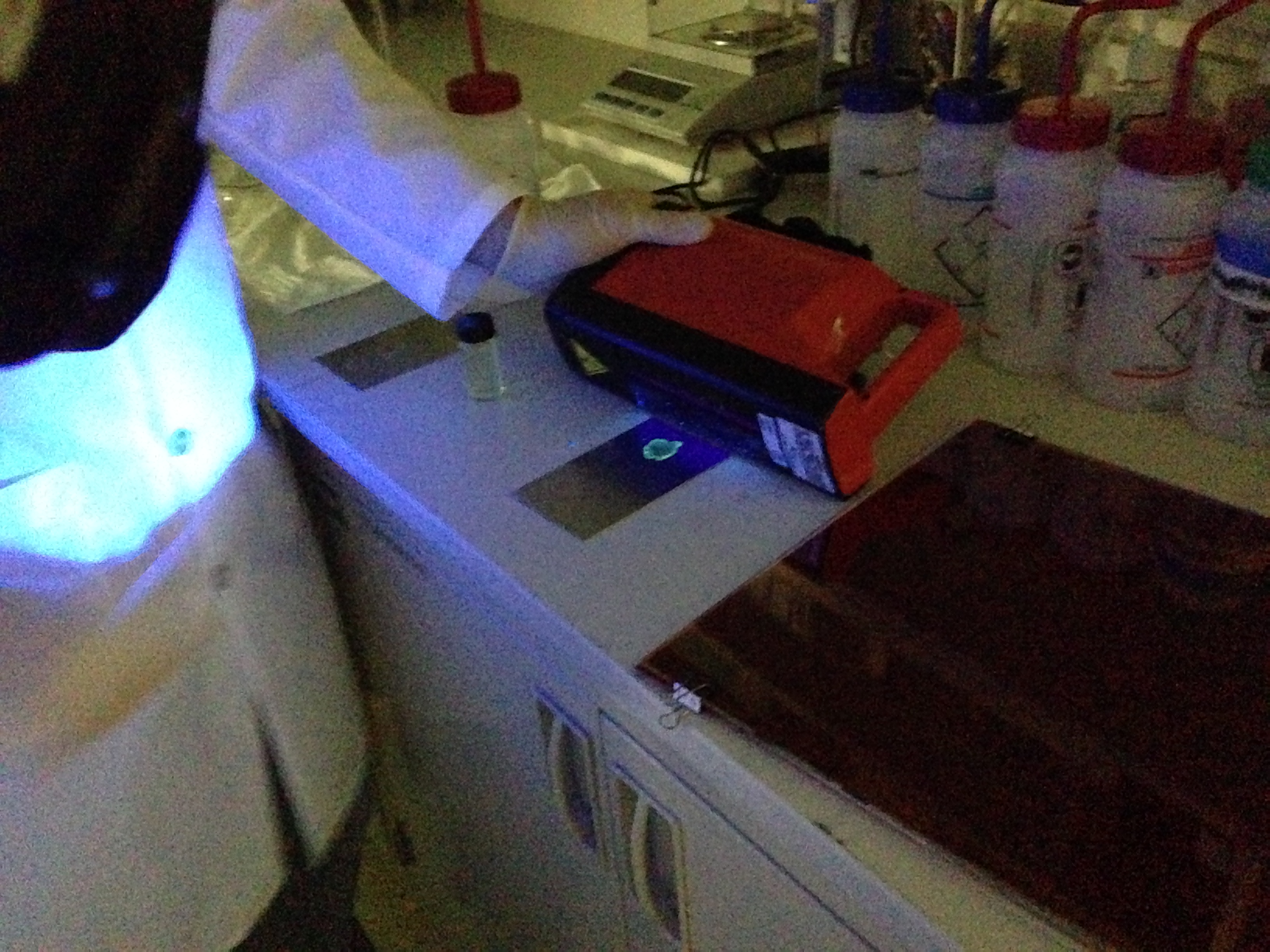
An insidious and often invisible enemy is eating away at the bottom line of the oil and gas industry.
Corrosion erodes profit margins, and increases the risk of costly equipment failures or environmental disasters. The oil and gas industry spends $7 billion annually on direct corrosion control and repair on liquid oil and gas transmission pipelines alone. Another $1.4 billion a year goes toward protecting or restoring production and exploration infrastructure and equipment.
Indirect costs, which can include business interruption, environmental cleanup and legal expenses, can easily double the financial impact of corrosion.
Scientists at Battelle fighting back against corrosion with a new dual-action microbead that can both detect and mitigate corrosion as soon as it starts. The Smart Corrosion Detector™ bead exposes corrosion before it is visible to the naked eye, automatically releases self-healing chemicals to fill the corrosion cracks at the microscopic level.
With 185,000 miles of liquid petroleum pipelines, nearly 320,000 miles of gas transmission pipelines, and more than 2 million miles of gas distribution pipelines in the United States alone, the possibility of more effective corrosion control and detection is huge for the industry.
Microbeads allow for faster and more accurate inspection of pipelines, and extend the service life of equipment by slowing or stopping corrosion when it starts.
The smartbeads look like a fine white powder and can be mixed into paints and coatings. Using a special light, the beads glow in the presence of corrosion, so inspectors can easily see early stage corrosion, even if it isn’t showing through the paint. This early visual indicator allows companies to investigate and correct the source of the corrosion.
These beads go farther, however: they mitigate corrosion as it happens. When corrosion is detected, the smart beads crack open, releasing a proprietary chemical that heals microscopic cracks caused by rust and corrosion.
Corrosion, including rust, occurs naturally, beginning small – with invisible changes to the physical structure of a material (usually a metal). These changes can be caused by a chemical reaction when metals are exposed to water, acids, gases or even chemicals produced by microbes (called microbially induced corrosion (MIC).
These small changes add up to big effects over time. Corrosion weakens the physical structure of the material, and eventually leads to failure of the affected component. By the time corrosion is visible to the eye, the damage can be quite costly to repair. The consequences of failure, which can include business interruption, environmental damages and human health implication, can be even costlier.
While smart coatings have been in development for some time now, this is first product to deliver both detection and repair properties in a single bead. Existing products generally have two separate microcapsules: one microcapsule with a reactive oligomer core, and a second microcapsule containing a catalyst.
The oligomer microcapsule breaks open when corrosion is detected. However, the self-healing properties are dependent upon the second type of capsule also being present at the same location to release the catalyst. The complex curing mechanism, along with stability issues with the materials in the core of the microcapsules, has made this two-part process less than ideal for real-world applications like pipelines.
By combining both properties in a single microbead, the self-healing chemicals can be automatically released as soon as corrosion is detected at the microscopic level. And by eliminating the need for a separate external catalyst, it also eliminates the challenges associated with a primer-based cure.
The microbeads are made of a thermoplastic core surrounded by a thermoset shell. Battelle scientists needed to find a shell material that would be compatible with (and insoluble in) the epoxy resin-based paints and coatings typically used for pipelines and other infrastructure. The shell also needed to be resilient under applied pressure, but break open easily when encountering the microfractures caused by corrosion. The thermoplastic core needed to be compatible with the epoxy primer resin, flow via capillary action, form a film resistant to corrosive materials, dry in a reasonable time period and be stable after encapsulation.
Tests have shown the coatings impregnated with the microcapsules perform favorably compared no non-treated coatings. And tests of the self-healing properties of the microbeads show significant improvement in corrosion controlling properties compared to both untreated coatings and coatings with separate beads for the self-healing payload and the catalyst.
The technology has not yet been commercialized, and Battelle is actively seeking collaborators to conduct field testing for specific applications and bring the beads to market. The impact on the industry could be huge. It will also dramatically slow the spread of corrosion and help to prevent corrosion-related pipeline and equipment failures.
With millions of miles of infrastructure out in the elements, the industry will be fighting the forces of corrosion as long as it depends on pipelines for transmission and delivery. For widely distributed and difficult to reach pipelines, slowing down the spread of corrosion and buying time to find and mitigate the causes could go a long way toward extending the life of the infrastructure and preventing accidental releases.
The potential cost savings, in both direct equipment replacement and repair, and indirect costs associated with equipment failure, could be in the billions of dollars.
Author: Ram Lalgudi is a senior research scientist at Battelle with expertise in coatings, adhesives, composites, membranes, encapsulation and medical products. He holds a doctorate in polymer chemistry from the National Chemical Laboratory, India.
Comments