September 2015, Vol. 242, No. 9
Features
Strategy Report Points to Improved Safety, Smart Pigs
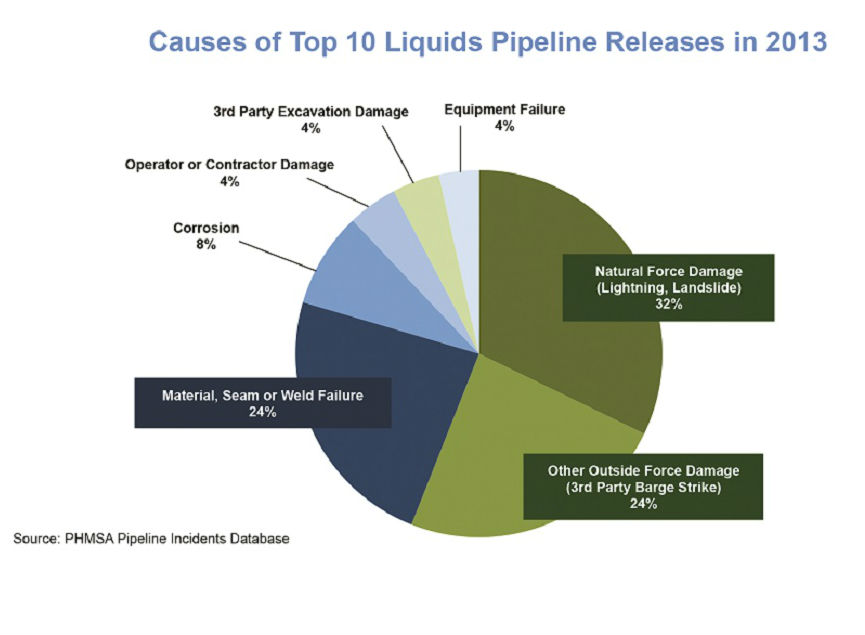
With liquids pipeline incidents down by half since 1999, even as their use to transport crude oil pipeline has increased, there is little doubt among experts about what has led to this success on the safety front – preventive maintenance and integrity management programs.
“The ILI inspections using smart pigs are finding early signs of corrosion and other issues, which allows for repair before the situation becomes a problem,” said Andrew Black, president and CEO of the Association of Oil Pipe Lines (AOPL). “Preventive maintenance and the advances in technology are the big reasons for these results.”
The American Pipeline Institute (API) recently surveyed its members and found that $2.1 billion was spent on integrity management since 2013. Still, even with crude oil and petroleum products reaching their destinations safely a stunning 99.999% of the time, according to the API-AOPL Annual Liquids Pipeline Safety Performance Report & Strategic Plan, Black said the industry is committed to doing better.
This is all the more impressive when considering U.S. transmission pipelines delivered over 14.94 barrels of crude oil and petrochemical products in 2013, an increase of 6.2% over the previous year. The impressive array of statistics found in the performance report doesn’t end there:
• In all, crude oil and petroleum products delivered by U.S. transmission liquids pipeline rose 6.2% from 2012 to 2013. Of that, operators delivered 8.3 barrels of crude oil by U.S. transmission pipeline in 2013, an increase of 11.3% over the previous year.
• Over the last five years, crude oil barrels delivered by U.S. transmission pipeline rose 1.351 barrels or 19.4% as crude pipeline mileage grew to 192,396 miles, a 15.4% increase over the last 10 years.
• According to the U.S. Energy Information Administration (EIA), U.S. crude oil production has grown by 3 MMbbl/d since January 2011 and is projected to grow 3.1 MMbbl/d to reach 9.6 MMbbl/d in 2019, near the nation’s historical high in 1970. Total production of crude oil and other petroleum liquids is expected to grow from 11.1 MMbbl/d in 2012 to 14.6 MMbbl/d in 2019.
Goal: Zero Incidents
“Zero pipeline incidents is the statistical goal,” Black said. “Even with the reduction of incidents, we are undertaking efforts to improve performance. We are working to improve technology to find and diagnose potential problems.”
With the advancement of inspection technology and the ability to find early signs of corrosion there have been 76% fewer corrosion-related incidents in the last 15 years, according to the performance report. In 2013, liquids pipeline operators inspected 47,089 miles of pipelines with “smart pig” inline inspection tools.
“The ILI inspections using smart pigs are finding early signs of corrosion and other issues, which allows for repair before the situation becomes a problem,” Black said.
Development of smart pigs using ultrasonic sound waves to find potential cracks in pipes has been a game changer. These tools that can find subtle, microscopic, hairline features in a pipe often hidden in welding seams are the current research effort.
“We are hoping in the next 15 years that one of the great technological innovations is further improvement in finding hairline crack features,” Black said.
According to the performance report improvement in smart pig technology that led to the “steep drop in the number of corrosion-caused incidents is apparent.” Other incident causes, such as operator error and flawed seams and welds are “relatively flat over time,” the data showed.
Two big factors beyond inspections have contributed to the success in the war on corrosion, Black said. One is the ongoing improvement to enhanced coatings, which continues to get better. The other is cathodic protection, which has helped the industry in minimizing external corrosion.
“Successful cathodic protection programs have gone on longer than that [15 years], but they are very important,” he said. “When the liquids pipeline industry looks at where to address strategic planning efforts, we’re finding satisfaction comparatively on corrosion-related incidents.”
While the performance report revealed other good news in that third-party damages resulting in incidents have declined by 78% since 1999, operator error-related incidents have increased slightly over the past several years.
“We do see an uptick in pipeline operator errors,” Black said. “This is the smallest category of barrels released per incident [38 barrels], and it’s only 2% of the total release volume. An industry team has been reviewing operator incidents and hasn’t found a single specific trend, but we continue to dig deeper.”
Incidents caused by third-party excavation are down over time as well, the performance report said, “reflective of efforts to increase public awareness and 811 call-before-you-dig programs.”
In 2013, about two-thirds of liquids pipeline incidents occurred within operator facilities, often at pump stations, located every 35 to 50 miles along a pipeline, or at storage locations, primarily located at the beginning, junction point and end of pipelines, according to the Pipeline and Hazardous Materials Safety Administration (PHMSA).
Incidents at facilities are generally smaller, involving pump leaks or seepages from valves and other equipment. Incidents reported to PHMSA can be as small as five gallons. Because of their size and remote location, operator-facility incidents are unlikely to affect public safety.
In fact, analysis of 397 pipeline incidents reported to PHMSA in 2013 showed 35% were smaller than one barrel while 20% exceeded 500 barrels. By focusing on rights-of-way, this allows operators to develop strategies to decrease these types of incidents, Black said.
Better Diagnostics
In order to improve technology, Black said, the industry is working at getting better in diagnosing potential problems before they happen. He pointed to research and development underway on inline crack detection tools as well as efforts to better identify and respond to threats through regulating practice on crack detection and management.
“There is so much information now that we think operators could benefit from some guidance on integrating data and proper guidance on the use of video tests,” he said. “We know hydrotests have an important role in commissioning new pipelines, but we also need to do more critical thinking about the use of hydrotesting on existing pipelines.”
Pipeline operators have been boosting local emergency response capabilities, too, with the addition of free online training programs.
“This is one of the most active efforts we’ve had over the last couple of years,” Black said. “We’ve heard there are resource constraints on first-responders and time constraints. We’re bringing the free online training portal to them.”
The operators have worked with the National Association of State Fire Marshals in presenting the training program and with the Emergency Response Advisory Board, which meets twice a year. The completion rates for the program have increased in each state since the program’s inception.
The upshot of all this, according to Black, is that “Pipelines are the safest way to transport large volumes of crude oil and petroleum products. The Department of Transportation confirms that and the State Department confirmed that in the study on Keystone XL.”
For further information or to read the report in its entirety, visit aopl.org.
Safety Principles Cut Across the Board
These safety principles reflect the shared commitment of pipeline operators to safety. They represent not only aspirational goals all operators strive toward, such as zero incidents, but also everyday ways of doing business that promote continuous improvement and excellent safety performance:
Zero Incidents – Only with a goal of zero safety incidents can we minimize accidents. Pipeline operators believe that every incident is preventable and work to that high standard.
Organization Commitment – Not only do senior leaders of pipeline companies value safety, but safety is emphasized at every level of the organization from employees who accept personal responsibility for safety to front-line managers who are vital to reinforcing a safety culture and implementing continuous improvement.
Culture of Safety – Pipeline operators embrace the need to provide a workplace culture where safety is an enduring value that all employees share, act upon, learn from, are rewarded for and judged upon.
Continuous Improvement – Pipeline operators believe that no matter how safe they already are, they can always improve safety. Vision, commitment, culture, and systems are necessary to improve safety continuously.
Learn From Experience – Pipeline operators learn how they can improve safety from their own experiences and by sharing lessons learned with and from other pipeline operators.
Systems for Success – Safety management systems demonstrate that safety efforts are succeeding by measuring performance, tracking changes and confirming improvements.
Employ Technology – From in-line inspections with diagnostic robots traveling inside pipelines called “smart pigs” to innovative ways to interpret integrity data, operators constantly research and develop new ways to maximize safety.
Communicate with Stakeholders – Operators know communicating with the public and stakeholders who value safety is vital to improving safety.
Teamwork Counts When it Comes to Safety
Industrywide safety groups pursued pipeline performance improvement goals:
Pipeline Safety Excellence (PSE) Steering Committee: This group of pipeline executives focuses on ensuring progress on industrywide safety performance improvement initiatives.
Each executive serves as a “champion” on one of the industry’s strategic initiatives supporting work on that initiative, facilitating additional resources if appropriate, keeping the PSE Steering Committee informed on initiative progress, and raising issues needing resolution with the broader group.
In 2014, the PSE Steering Committee oversaw API-AOPL strategic initiatives to improve inspection technologies, enhance pipeline threat identification and response, expand safety culture and management practices, and boost response capabilities. The PSE Steering Committee is continuing this executive leadership and oversight role in 2015.
Performance Excellence Team (PET): The PET brings together senior managers from across industry to exchange the latest information on pipeline safety.
PET members also engage in three standing sub-teams focusing on pipeline performance data management, pipeline damage prevention and safety culture. In 2014, PET led the pipeline industry’s annual industry-wide pipeline safety performance strategic planning process.
This year, in addition to its strategic planning process role, PET is leading strategic initiatives to implement new API recommended practice on pipeline safety management systems and foster pipeline safety culture with an industrywide sharing, learning and improvement program.
Pipeline Integrity Work Group (PIWG): PIWG is an API-led group of industry managers with responsibility for ensuring the integrity of the pipelines at their companies.
The managers oversee programs to evaluate, inspect and perform maintenance on their systems. As part of PIWG, they share learnings and best practices to improve pipeline integrity. PIWG recently completed an update to the industrywide standard for managing integrity of pipelines.
PIWG led two 2014 strategic initiatives to develop an API-recommended practice on crack detection, analysis and response with an emphasis on seam-related cracks, as well as one to develop industrywide guidance on implementing threat data integration programs and activities.
In 2015, PIWG will complete its development activities from 2014, and then lead three strategic initiatives: implementation of new API-recommended practice on crack detection, analysis and response; implementation of industrywide guidance on integrating pipeline threat data; and development of industrywide guidance on the appropriate use of hydrotesting.
Operations and Technical Group (OTG): The OTG is an API-led group of industry managers with responsibility for pipeline operations and engineering. They meet regularly to share operating experiences and best practices.
Each year, OTG hosts an industrywide pipeline information exchange to share information on incidents or near misses that yielded learnings and improvements in pipeline safety. OTG also facilitates the consideration and adoption of industrywide operations and safety standards.
Cybernetics Work Group: Cybernetics is an API-led group of operations managers responsible for leak-detection technology and control room systems.
In 2014, the group began developing an API-recommended practice for leak-detection program management. The group is completing development of an API 1149 technical report and will undertake the 2015 strategic initiative to implement API recommended practice for pipeline leak-detection program management.
Public Awareness Group (PAG): PAG is an API-led group of community outreach managers working to improve programs to raise public awareness of local pipelines and “call-before-you-dig” programs.
Operator Qualification Work Group (OQ): OQ is an API-led group that ensures operator qualification practices meet regulatory requirements that contribute to safe operations and a safe operating culture.
Environment, Health and Safety Group (EH&SG): EH&SG is an API-led group that promotes environment, health and personal safety issues within pipeline operators.
Pipeline safety leadership teams: In 2011, the executive leadership of the liquids pipeline industry launched several industrywide teams to address specific safety performance issues.
In 2012, the leadership created an additional team to address emergency response. The groups take on special projects that are time-sensitive or meet a specific program needs.
Black
Comments