September 2015, Vol. 242, No. 9
Web Exclusive
Compression Report: Trade Keeps Sharp Eye on Changing Market
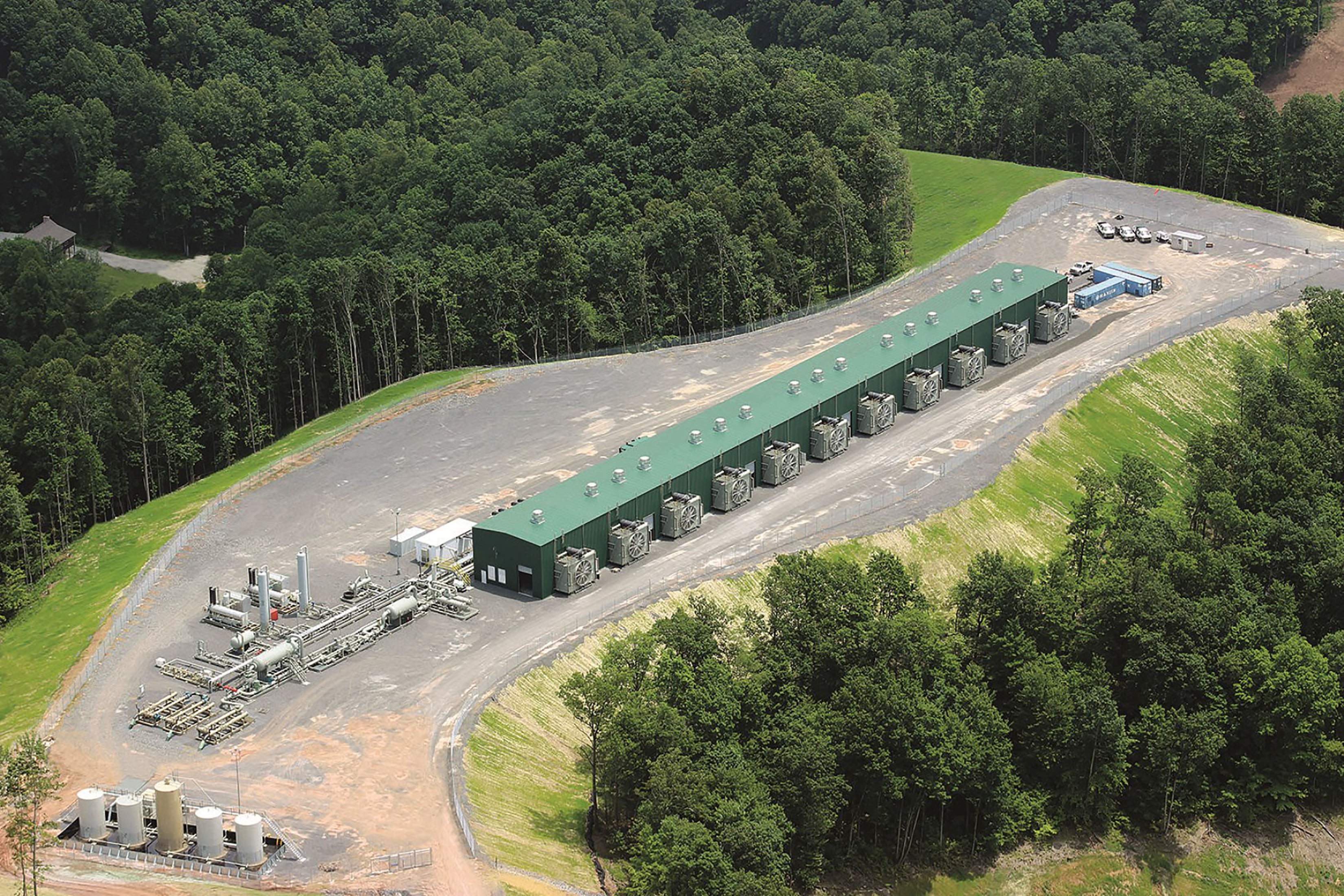
It’s a topic the general public doesn’t know much about, but there would be no natural gas pipelines – hence no natural gas – without compressors. Today compression is a main topic of conversation in the industry for many reasons, environment – which includes siting, noise and emissions control – economics, and engineering/construction challenges. As the natural gas industry continues to expand and change direction, more pipelines will be built in the next few years, all dependent on compression.
Mike Paris is vice president of the compression product line at Houston-based Valerus, an industry leader. He began his career in 1985 in Corpus Christi, TX as a project engineer in the packaging division of Energy Industries. He spent two years in Broken Arrow, OK working for Dresser-Rand Compressor Services, then moved on to The Hanover Company where he spent the next 12 years, his most recent position being vice president of engineering. He holds a bachelor’s of science degree in mechanical engineering from Louisiana Tech University and is a registered professional engineer in the state of Texas.
In this interview, Paris provides a perspective of today’s compression business, starting with Mexico where the ongoing Energy Reform is expected to be a boon for the U.S. natural gas industry and the compressor manufacturers.
P&GJ: What is your perspective internationally, especially as Mexico opens up to natural gas development?
Paris: Mexico’s opening to the private sector will generate numerous opportunities for exploration and production operators, international oil and gas companies, suppliers and investors. The Energy Reform will spur engineering and construction activity across Mexico, offering a whole host of opportunities to the business.
Currently, there are a series of changes that will increase the amount of business related to natural gas, especially in the power generation and exploration of natural gas. We are expecting to see a huge boom in shale gas production all along the northern part of Mexico. Many new companies are focusing on self-generated power (using natural gas as fuel) as well as new pipeline projects to satisfy the growing demand in natural gas. Pipeline projects are a critical part of our business model as they require new compressor stations to be built to redistribute the gas.
Valerus has offered a strong market position in Mexico since 2006 and we intend to capitalize on our strengths, partnering with local and international clients to help deliver these projects. For example, Valerus was an integral partner on the team to work with Pemex to provide in excess of 200,000 hp of compression capacity to develop the Magallanes and Santuario blocks in Tabasco State. Foreign expertise in the form of technology, when combined with the local talents of Mexican personnel, will help open new frontiers.
P&GJ: What new compression technologies and methodologies is the industry exploring?
Paris: We are constantly eyeing new technology and practices to better service our customers. Compression technology is rooted in very basic and, as I like to say, “tried and true” methodology. However, we are now seeing more efficiency in compression technology and a shift to a more modular, plug-and-play concept being adopted here in the U.S.
Modularized structures at a well site allow production companies to adjust to shifting production levels as the need arises without overspending on unnecessary components. Modularization eliminates waste while providing scalability that the static structure of a permanent or semi-permanent compression station simply cannot deliver.
While the concept of modularization is not new, a tidal change in the natural gas industry has taken place in recent years. No longer perceived as temporary or inadequate for full-scale production, modularization combined with the plug-and-play model is becoming an industry standard. The plug-and-play model offers companies limitless customization to provide what they need when they need it. Modules may be quickly and easily added as necessary, or removed to reduce costs on unneeded or unused equipment. Thus, the structure keeps pace with production needs, while efficiently managing structure costs. It makes good economic sense.
Shale plays are more popular and populated than ever. However, each shale region has a specific lifecycle and viability. When a site is tapped, remediating and cleaning the area is expensive. But by using modular equipment, companies may reduce the cost and time needed for cleanup. The plug-and-play modular structures allow companies to pull out of these shale plays more quickly and remediate the location without significant cost.
The industry has been using modular design internationally for years, and it is exciting to see the concept become more accepted domestically. We have found modular design works very well in remote areas with harsh climates, such as the Northeast in the dead of winter. Prebuilt modular designs can be installed in days instead of weeks, increasing efficiency, saving costs and providing a sound design solution.
Pre-fabricated structures are already the norm for offshore construction; the historic build-on-site model is becoming antiquated and is highly dependent on a number of variables. As industry experts know, coming in on-time and on-budget is contingent on controlling variables. Thanks to 3-D modeling and fabrication of modular equipment in a manufacturing facility, the variables of atmosphere, personnel and resources may be overseen and better controlled. Model and testing ensure that a high-quality and functional product is delivered to the site. This process results in the delivery of build stations and piping that are functional, efficient and highly mobile.
In order to achieve maximum efficiency, and therefore lower costs, plug-and-play structure developers must adequately manage inventories in order to stay competitive and meet market demand. The plug-and-play design is standardized, and that design philosophy is mirrored in all of the equipment in order to ensure compatibility. By ensuring that the standardized materials are always on hand, costs associated with labor and shipping decrease, resulting in increased speed to market.
P&GJ: What are your thoughts on emission issues, specifically, how more strict regulations challenge compression operators and manufacturers?
Paris: There can be no denying that reduced emissions should be required from sources where the technology is readily available and economically feasible. However, too often the rules initially proposed are simply too onerous for the industry and impose an unfair burden. They may not even be practical for how equipment is actually operated. Sometimes where controls are available, the economic trade-off for implementation is too great, or creates other consequences not anticipated by regulators.
This is where industry involvement in the regulatory process is critical: When rules are proposed for a given industry, those affected should comment on the draft rules, whether through the company or industry trade groups. Bringing new facts, economics and operating scenarios to the table with the regulators will often result in some changes before rules become final.
For example, the Environmental Protection Agency (EPA) rules through Subpart ZZZZ of its National Emission Standards for Hazardous Air Pollutants (NESHAP) for stationary reciprocating internal combustion engines regulation requires more manpower for recordkeeping, reporting and equipment maintenance. This results in a pretty significant increase in operating costs just by virtue of the sheer number of engines out there. Most would say this hurts the industry.
To facilitate compliance, each company’s environmental and operations group must communicate closely to ensure they have an accurate inventory of engines and their locations. Where catalysts are required, it’s also important to talk to vendors to ensure their products are in compliance. Similarly, if an engine is a rental, companies must make sure they do their due-diligence to ensure it complies.
The most obvious benefits to these regulations are the reduced emissions from engines that may not otherwise require controls, which in turn preserve or improve local air quality. As I mentioned, challenges include keeping track of all of the testing, recordkeeping and reporting that is required to comply with the new rules. While companies already do this for other equipment, these rules can add another layer of “compliance burden.”
Our industry works very hard – both individually and in various work groups – to provide significant input on any new rule that’s pending, and the EPA really listens to many of these comments, and amends the rules accordingly. I think this shows how the regulators and industry can work together successfully for a common cause, and should encourage participation in regulatory negotiations.
P&GJ: Are manufacturers able to keep up with increased demand as natural gas usage continues to increase? What are the challenges involved?
Paris: Manufacturers are able to keep up with demand providing that our customers are able to help us plan and “level load” our facilities. Where the manufacturing supply chain gets squeezed is when customers have to wait until late in a project cycle to place firm orders, thus requiring quick delivery. Often this strains available trained manpower and shop space, as well as sourcing of major components such as engines, exchangers and compressor frames.
P&GJ: What new products and services will have an impact on the industry and why?
Paris: Speed to market has always been the pivotal driving factor for natural gas compression manufacturers; however, it is of even greater importance in today’s competitive landscape and current market conditions. The industry continues to see more and more manufacturing companies begin to offer pre-designed and pre-engineered products to meet customers’ demand for speed and efficiency.
Valerus, for example, has developed configurable gas compression packages that are available for delivery in only four weeks, assembled in the industry’s only ISO 9001-certified packaging facility. Customers are seeking solutions to bring their gas stream to market faster, and are demanding products that meet their production needs with configuration flexibility, superior performance and rapid delivery.
3-D rendering of Valerus compressor package.
Paris
Comments