December 2016, Vol. 243, No. 12
TechNotes
United Pipeline Systems Relines Steel Line for Canadian National Resources, Ltd.
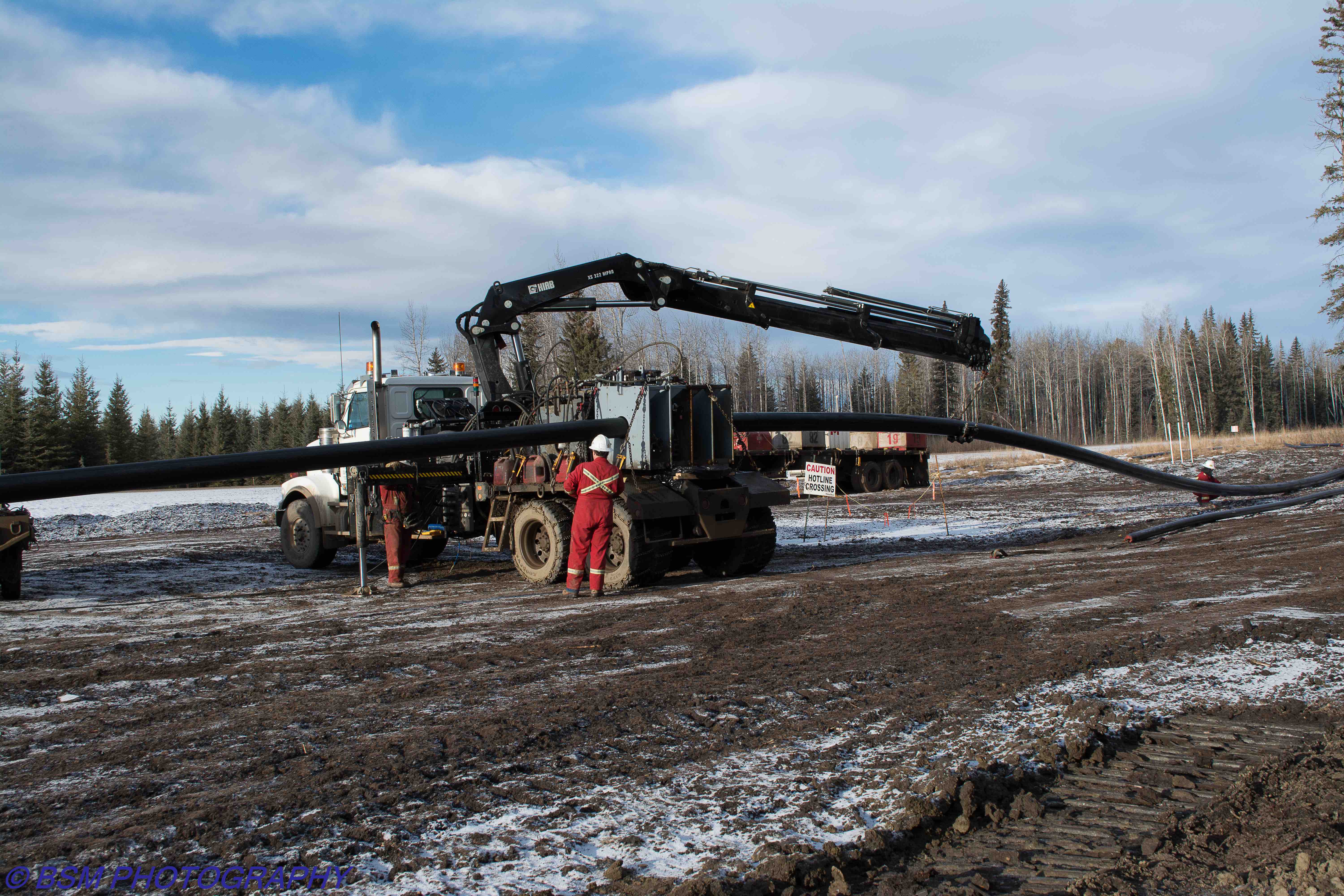
Elevated water temperatures running through pipelines can present umber of problems to owners in the oil and gas industry. Identifying ways to mitigate the issues associated with high temperatures, such as interior corrosion, have led United Pipeline Systems to develop a new polyethylene (PE) liner explicitly designed for high temperatures.
Under normal circumstances, high temperatures can soften PE material, leading to failure for both the liner and steel host pipe. For a water injection line near Swan Hills in Alberta, Canada, a special solution was necessary since the pipe carried production water at more than 150°F.
Originally installed in 2000, the pipe was first lined in 2008 with PE 3608 and subsequently relined using PE 4710 in 2010 due to a steel failure. According to the Plastic Pipe Institute, PE 4710 presents a variety of benefits in comparison to PE 3608, including higher tensile yield strength and upgraded pressure capabilities.
The 6-inch carbon steel pipeline carries hot water combined with high gas and CO2 content. In 2015, CNRL identified the line as high risk and approached United Pipeline Systems to help mitigate any future issues that may result in a breach of the pipeline.
With a nearly 20-year relationship relining pipe for CNRL, United proposed using a new type of PE 4710 specifically designed for high temperatures. Manufactured with a new resin, the upgraded 4710 PE-RT is a raised temperature polyethylene material specifically designed for the severe conditions present in oil & gas and industrial environments.
About the Tite Liner® RT System
Known commercially as the Tite Liner® RT system, this technology is manufactured using DOW’s INTREPID™ 2499 NT resin, a bimodal high density polyethylene resin technology that enhances its high temperature performance. The system offers a temperature rating of up to 180°F and a non-continuous use temperature greater than 200°F, making it more than adequate for the 150°F line.
Tite Liner® RT liners are intended for use in pipeline and piping systems where extreme conditions, including pH imbalanced water (saline solutions), aggressive chemicals, hydrocarbons and highly oxidative conditions, as well as high temperatures, exist. Suitable applications include oil and gas field pipelines, gas distribution pipelines and other industrial and mining applications.
The only real challenge to this project was timely delivery of enough resin to Uponor, the pipeline manufacturer/extruder, to produce the Tite Liner® RT system and meet the client’s schedule. It was the first time that Uponor had produced the PE-RT and all went well, from extruding the liner and the billet to creating stub ends for the project.
In addition to high temperature resistance, other benefits of the Tite Liner® RT system include:
- Elimination of internal corrosion in severe applications
- Chemical compatibility in broad oil and gas applications with H2S and C02
- Resistance to highly oxidative conditions
- Superior notch and scratch resistance
- Superior resistance to rapid crack propagation
- Increased flow capacity with reduced friction loss
- Extended service life resulting in lower cost of ownership versus alternatives such as CRA
- Reliable and safe performance record
- Good creep resistance
- Excellent slow crack growth resistance performance
- Improved cyclic fatigue resistance
- Increased tensile and ductile strength
Raised Temperature Bimodal Polyethylene Resin Testing
INTREPID™ 2498 and 2499 bimodal polyethylene resins have been tested in an unrestrained (or free standing) application at a nominal stress of 2.4 MPa (350 psi) for more than 10,000 hours in the ASTM F1473 Pennsylvania Notch Test (PENT), compared to the ASTM D3350 requirement of 100 hours for PE3608. Even compared to the ASTM D3350 requirement of 500 hours for PE4710 pipe, the specialized resin offers resistance more than 20 times longer. Additionally, in a compressed fit lined pipe application, the Tite Liner® RT system offered higher temperature creep resistance at 180°F for improved integrity.
System Installation
The pipeline is located in the Old Devon/Anderson oil field, an environmentally sensitive area near the Swan River. The large field contains multiple different lines along the right-of-way, so proper project planning was essential.
Installation of the new liner system is similar to the traditional Tite Liner® system. Developed in 1985, the Tite Liner® technology enables a thermoplastic liner to fit tightly inside a host pipe. The system is manufactured with a larger outside diameter (OD) than inside diameter (ID) of the host pipe. The installation requires temporary reduction in the diameter of the thermoplastic liner for insertion. The liner then expands tight following installation and acts as a continuous barrier between the host pipe and corrosive or abrasive material.
Prior to relining, the original liner material had to be removed. This can be done using a variety of methods, including being cut out or pulled out. For this project, a strip was cut out of the existing liner, causing the liner to collapse within the host pipe, making for easy removal.
After removal, the client logged the bare pipeline to see if any repairs were needed in the steel before installing Tite Liner® RT system. Installation proceeded in October 2015, using the same method as the traditional Tite Liner®system – fused the same, rolled the same and fitted with screened stub ends. A total of almost 2,200 linear feet of pipeline was rehabilitated in three separate installations, or shots. See the table below for installation lengths.
Installation | Linear Feet |
Shot #1 | 108 LF |
Shot #2 | 1,243 LF |
Shot #3 | 843 LF |
Since the completion of this project, the first successful PE-RT installation for CNRL, United has completed an additional installation in same field. This latest line consisted of a single pull of 1,673 linear feet – the longest shot to date.
United personnel including Operations Manager Ed McClintock, Project Manager Todd Kehoe and Superintendent Bill Jorstad led the project’s successful implementation and completion.
Comments