February 2016, Vol. 243, No. 2
Features
Wireless Field Measurement Takes Next Step
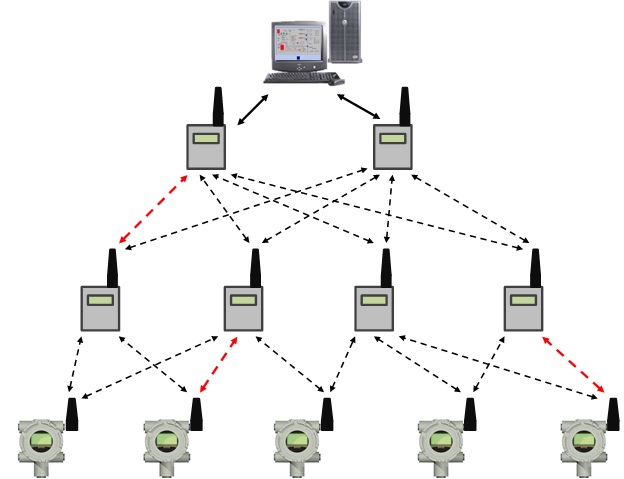
For process monitoring applications, the wireless revolution has come of age. Particularly in the upstream sector, oil and gas operations have fully realized the value proposition advertised by manufacturers.
Wireless transmitters are now commonly applied to measurements of level, pressure and temperature at compressors, gathering lines, separators, rod pumps and wellhead “trees.” Wireless instruments have proved to be cost-effective, reliable, safe, secure, simple and environmentally friendly.
In light of recent oil price trends driving the need for improved efficiency, cost savings are more important than ever. By eliminating conduit, conduit seals, intrinsic safety barriers and wiring, as well as associated installation labor, wireless instrumentation significantly reduces installation costs. Case studies have confirmed manufacturer-stated savings that range upward of 60%.
Wireless networks are easy to start up. Most products will self-configure on a network or begin operating after minimal configuration. As attested by users needing to add a casing pressure measurement or plunger arrival switch, wireless instruments are also easy to drop into existing installations.
Contemporary radio transceiver technology provides reliability that rivals that of hard-wired networks. By minimizing data transmission delays due to latency, radio module manufacturers have come through with feasible “wire replacements.” In fact, some engineers have argued that wireless networking is actually more reliable than hard-wired networking.
Those installers who do encounter startup problems are relieved to know that diagnostic tools make wireless network troubleshooting as simple as it is for hard-wired networks. The most common problems result from attempts to push the radio-signal range. Wireless instrumentation communicates on high-frequency bands, which require near line-of-sight communications. Radio signals are loath to bend around buildings, process units, terrain and trees.
Transmitters are available in two, license-free, radio frequency bands, 900 MHz and 2.4 GHz. Given equivalent transmitting power, the 900-MHz band provides the longer range. Depending on the antenna, a 2.4-GHz signal will range between 500-3,000-plus feet vs. over a mile for a 900-MHz signal. These are usually ample for a wireless well site. By contrast, higher-powered radios for SCADA applications offer ranges of 5 miles at 2.4 GHz and 20 miles for 900 MHz.
Wireless instrumentation is environmentally friendly. By eliminating trenching for conduit runs, wireless instruments greatly simplify land-use issues and safety requirements, including regulatory compliance. It also minimizes exposure of personnel to hazardous conditions. And 24/7 monitoring removes most requirements for travel to the site.
Wireless instruments have also proved to be reliable. Robust devices operate in outdoor environments at temperatures ranging from -40oF to as high as 185oF (85oC). Hazardous area approvals, typically Class I, Division 1, allow installation in practically any oil and gas process.
Prospective users can choose from a variety of wireless networks. Industry-standard, mesh networks, such as ISA100 (IEC 62734) and Wireless HART (IEC 62591), have been designed for use in process plants and field locations.
The mesh network architecture allows signal routing around large process units and building structures. Wireless signals easily traverse spaces in which wiring would be difficult, expensive and risky. In case of a failure in any node or path, self-organizing networks allow devices to implement a self-healing, alternate communications path.
In order to minimize the number of devices needed at field sites, operators often select single-level, point-to-multipoint networks, instead of mesh networks. At open-space locations such as well sites, barriers to line-of-site radio signals are not encountered as regularly as they are in process plants.
Since the mesh structure is not as important, field users continue to purchase a great deal of products that use proprietary communications with protocols, such as ASCII and Modbus.
For designers of wireless instrumentation, power consumption is the biggest technical hurdle. Severed from hard-wired connections to equipment such as remote terminal units (RTUs), wireless devices are, by necessity, self-powered.
Innovative designs have minimized current draw in order to allow wireless devices to operate for years with a small battery. A useful tool offered by suppliers is the battery life calculator, which provides an accurate estimate of battery life based on operating conditions. On a website or spreadsheet, the user can enter just a handful of operating parameters and obtain an estimate in seconds.
Since the radio transmitter is the primary power user, the “update rate” is the key factor. Note that the term, “rate,” is a misnomer. The figure is really the interval between updates. The lower the update interval, the more often the transmitter is operating and consuming power.
The following table depicts representative battery lifetime estimates, based on update interval, with other, selected factors being equal:
Update interval Pressure Transmitter Multi-variable Transmitter
60 minutes 12 years 10 years
60 seconds 10 years 7 years
10 seconds 4 years 3 years
1 second 7 months 5 months
As the table shows, wireless instruments are excellent solutions for processes requiring update intervals as low as 10 seconds. Those are considered slow processes in which the measured variable is not apt to change rapidly. Examples include tank gauging, temperature measurements and many pressure measurements. That makes wireless instruments ideal for oil and gas well sites. Long battery life is essential for field operations in which travel is expensive and sites often inaccessible.
On the other hand, wireless instrumentation has largely been out of the loop when it comes to dynamic flow measurement and process control applications that demand per-second updates. Battery life is too short for well field operators, who insist on multiple years between battery replacements. Without the travel costs and restrictions, plant operations are typically satisfied with the sub-one year battery life estimates for instruments operating on one-second intervals.
What’s Next in Wireless?
A new generation of wireless instruments is emerging with greater power efficiencies that allow longer battery life for instruments using one-second update intervals, and a wider selection of power sources. Multi-variable measurement has also emerged with differential pressure, static pressure and temperature sensors in a single wireless instrument.
The new generation effectively expands applications to the pipeline and gas distribution industries where many processes demand one-second updates and long battery life. For example, wireless instrumentation has previously not been feasible for custody-transfer flow metering applications, which must meet American Petroleum Institute (API) Manual of Petroleum Measurement Standards, Chapter 21.1 requirements.
For upstream operators, the technology enables a completely wireless well site that includes live flow measurement in addition to monitoring of levels, pressures, temperatures and process unit status. An RTU or dual-radio gateway device interfaces the local, wireless network at the well site to a longer-range SCADA system network.
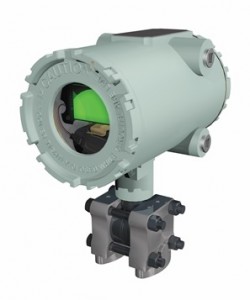
A wireless, API 21.1-compliant, “DP/P/T” transmitter will operate over a multiple-year timeframe using an internal battery. Custody-transfer metering installations – and upstream applications using similar criteria – can now benefit from the reliability, safety, security, simplicity and environmental friendliness offered by a cost-effective wireless instrument.
Since wireless designers have reached the point of diminishing marginal returns in their power-reduction efforts, the focus has turned to the sensing technology. Like radio transceivers, pressure sensors and temperature sensors in wireless instruments operate on duty cycles that are intended to minimize current draw.
For the most popular technologies, such as capacitive sensors, designers have reached the floor in terms of current draw and have turned to other solutions. In order to realize further power reductions, piezo-resistive technology is the most promising.
By using a higher resistance, 10K Ohms vs. 5 K Ohms, designers have cut current draw in half, while maintaining the high accuracy that is demanded by custody-transfer flow measurement applications. Furthermore, a high impedance sensor has virtually no self-heating and is extremely stable. This allows a pressure measurement to be taken as soon as power is applied, thus minimizing the “power-on” time per measurement.
Additional improvements in power management have been realized at the application and firmware levels in the instruments. Among the best examples is historical data logging. Normally, transmitters output only the latest values of live measured variables. In case of a communications failure, those values are lost. However, by storing a history of measured values, the transmitter provides database backup.
Designers have extended this feature as a power-conservation measure. Instead of operating the radio transmitter every time the measured variable updates, the instrument can transmit a history less frequently. This tactic is feasible for remote monitoring applications that do not demand live updates.
Some devices have further extended the historical data logging concept to provide databases that meet API 21.1 requirements for natural gas measurement. Averages of the measured variables are maintained on user-configurable intervals such as 15-minute, hourly and daily.
The improvements in power management address contemporary issues with lithium thionyl chloride batteries. Due to their hazardous material classification, lithium batteries are subject to special handling requirements and restrictions in transportation and disposal. These issues work against the operating cost advantages provided by wireless instruments.
Lithium battery technology is otherwise ideal. A lithium battery provides far more power per unit volume than other technologies. While a lithium battery with a 19 amp-hour capacity fits in a small, wireless instrument enclosure, a lead acid cell battery with similar capacity would be 14 times larger.
A lead acid cell battery that is small enough to fit inside a wireless instrument enclosure won’t last long without a charging source such as a solar panel. But solar panels present added installation costs plus risks of damage, theft and vandalism. Since they are typically not suitable for Class I, Division 1 locations, they could also require trenching and conduit seals to complete remote installations.
However, the new-generation wireless instruments are efficient enough to allow installation of the solar panel, along with the rechargeable battery pack, within the instrument enclosure.
Even though the panel is not aimed directly at the sun, sufficient energy can be gathered from secondary light reflections to maintain the charge usage rate. Such an installation could have a power-system life that depends only on the cycle life of the battery, which could be 10 years or more. This substantially reduces operating risks at a cost that is significantly lower than that for a lithium battery.
Conclusion
For upstream, oil and gas measurement process monitoring applications, wireless instruments have proved to be cost-effective, reliable, safe, secure, simple and environmentally friendly.
Now, an emerging generation of wireless instruments is expanding into more demanding applications such as dynamic flow measurement. By combining ultra-low power-sensing technology with the API 21.1-compliant measurement performance that is required by custody-transfer users, wireless, multi-variable (DP/P/T) transmitters are broadening upstream applications and moving into pipeline and distribution applications.
The technology enables a completely wireless well site that includes live flow measurement in addition to monitoring of levels, pressures, temperatures and process unit status.
Author: Kevin L. Finnan is a consultant with Newgate Instruments, a manufacturer of precision measurement products for natural gas applications. He was previously vice president of Marketing for CSE-Semaphore, a manufacturer of Internet-enabled automation, SCADA and telemetry products, and director of Marketing at Bristol Babcock. He can be contacted at Kfinnan@aol.com or 860-248-1929.
Comments