July 2016, Vol. 243, No. 7
Features
SEMS: A Solution to Eliminate or Reduce Accidents, Improve Safety
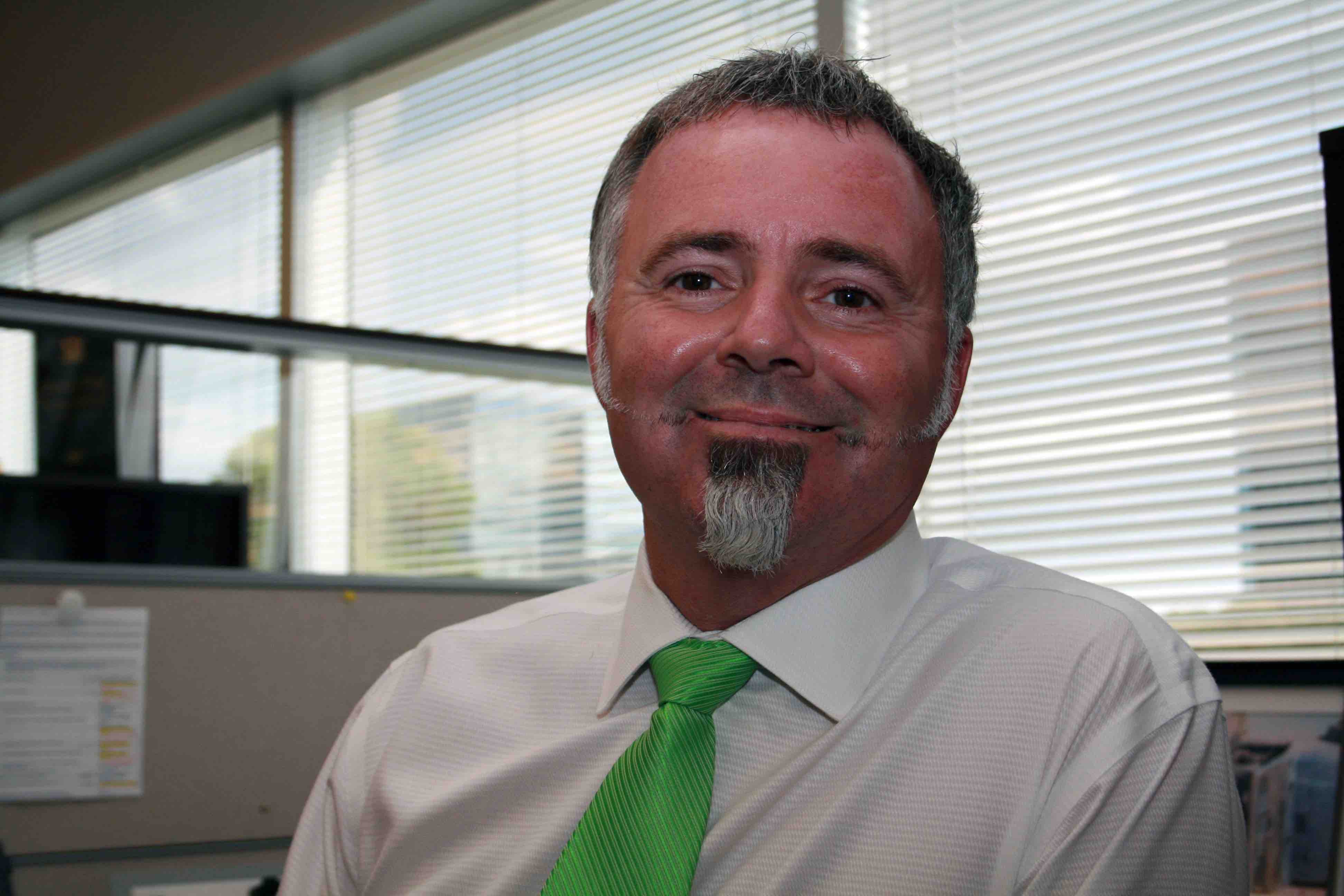
A worker makes a mistake on an offshore platform that causes equipment damage or maybe even an oil spill. More often than not, the employee will be retrained or fired, but will that solve the circumstances that led to the incident in the first place? In my view, the mistake was the result of a management system failure and until the root cause is addressed, the same mistake could happen again.
The oil and gas industry and regulators recognize the importance of the management system in creating a culture where employees are properly trained and the work environment prevents lapses, slips, mistakes or violations. A good management system is focused on preventing failures. It was for this reason that the Bureau of Safety and Environmental Enforcement (BSEE) and the oil and gas industry established the Safety and Environmental Management System, or SEMS for short, for all offshore operations in U.S. waters.
What is SEMS?
SEMS was an outgrowth of the 2010 Deepwater Horizon disaster and it adopted the previously voluntary practices in the American Petroleum Institute (API) Recommended Practice 75 (RP 75) Safety Environmental Management Program (SEMP) and made it mandatory for all offshore operators and lessees in U.S. waters. RP 75 was originally created as a management system that outlined the best practices companies should follow for their offshore oil and gas operations. SEMS is evolving, as the industry and regulator share best practices through the non-profit Center for Offshore Safety (COS), Ocean Energy Safety Institute (OESI) and other key industry associations such as API.
Operators must develop an effective SEMS to identify, address and manage safety and environmental hazards and impacts during the design, construction, start-up, operation, inspection, maintenance and decommissioning of all new and existing offshore oil and gas operations. SEMS prescribes a minimum of 17 components or elements to be considered a compliant system.
Those 17 elements are: General, Safety and Environmental Information, Hazard Analysis, Management of Change, Operating Procedures, Safe Work Practices, Training, Mechanical Integrity (Assurance of Quality and Mechanical Integrity of Critical Equipment), Pre-Startup Review, Emergency Response and Control, Investigation of Incidents, Auditing (Audit of SEMS Elements), Record-Keeping, Stop Work Authority, Ultimate Work Authority, Employee Participation Plan and Reporting Unsafe Working Conditions.
SEMS is a management system the operator puts in place, not the regulator. Every management system is different and each company addresses it differently based on their organization, structure, hazards, operations, etc. API RP 75, as well as SEMS, doesn’t dictate how to do things – it just states certain elements must be addressed such as a thorough hazard analysis.
Although SEMS is focused on offshore operations, the elements and the focus on fixing the management system can apply to all pipeline projects, regardless of complexity. These ideas can be easily migrated to any industry involved in high-risk operations. By probing the management system, companies identify opportunities for improvement and can create a positive, safe work environment for everyone.
SEMS has changed how training is conducted. There are three aspects to competency commonly referred to as knowledge, skills and ability as opposed to some previous methods that may have only considered a certificate of course completion in isolation. The training certificate is now the first step. The second step is to observe the person doing the work and verify they have the skills and ability to perform that work through oversight, such as mentoring programs. In SEMS, the competency of trainers must be verified.
SEMS Audits
One feature that makes SEMS unique is the requirement for audits. The BSEE audit requires all operators in the U.S. waters to use an independent third-party Audit Service Provider (ASP) to evaluate their SEMS. BSEE assigned these responsibilities to the Center for Offshore Safety (COS) which also serves as the Accreditation Body for all ASPs. Every operator or lessee SEMS program must be audited at least once every three years by an ASP.
Audits have resulted in significant changes in how companies approach and perform their operations. Companies have now implemented better barriers and are focused on risk mitigation and on preventing failures in the management system. The goal is to proactively prevent incidents from occurring and SEMS has created a culture shift in the value of these audits. The COS takes the audit results and develops metrics that are used by industry in a positive manner to help everyone.
Another advantage of SEMS audits is the requirement for contractor evaluations and “bridging documents” for operators and their contractors. Depending on the contract and what they are looking to achieve, the advantage of SEMS is it can be applied to contractors and you can assess a contractor to the operator’s management system. Today, the oil and gas operator cannot simply contract out their responsibilities anymore.
It can be difficult for a company to do a contractor evaluation because it is hard to remain independent and objective. In an environment like today, companies are being pushed hard to reduce costs. If a contractor is independently verified, it carries a lot more weight. Although contractors aren’t required to be certified under SEMS, operators can recommend they meet these requirements and that makes it easier on the regulator since they don’t have the responsibility to police 5,000 to 6,000 contractors. BSEE regulates about 80-90 operators.
In most accident investigations, often the report will point fingers at specific individuals. It often becomes a blame game that brings the organization’s culture down. Although human error comes down to four things: slip, lapse, mistake and violation, companies need to look beyond the obvious immediate causes and examine the root causes to identify the management system elements that need fixing. The only way to prevent the accident from reoccurring is to identify the root cause, address it within the management system and verify that the correction has been effectively implemented and is sustainable.
It is also important to involve those employees in creating that change and that is one of the key revisions of SEMS is the employee participation element; since they do the work and they know it best. It does no good to fire the employee and bring in someone new. It is a better approach to include that person with the most knowledge about the incident and include them in the fix. It can be a mistake to bring in a new person who may not know anything about that incident, since the incident is likely to be repeated unless the investigation can dive down into the management system to determine what went wrong. Human error can always be mitigated by the management system, and I always get a lot of push back when I make that statement. People will say the person knows what they were supposed to do, but they still didn’t do it correctly and that is the problem.
With the turnover rate in the industry, we are also losing a lot of experienced individuals. The people who do the work know the hazards and risks related to their tasks. Whenever a company does a change in work procedures or has a near miss in the work place, those lessons learned when revising policies and procedures or guidance notes must include those who do the actual work. Under the employee participation element, this approach ensures the company retains key knowledge by involving those key individuals in rewriting those policies and procedures resulting from audits or near miss incidents.
SEMS for Contractors
API RP 75 is currently being revised and the next version of SEMS will focus on managing contractors. SEMS regulations will likely be revised again when API RP 75 changes are finalized. For some time, it has been recommended for contractors to make sure their management system meets the requirements of SEMS. The operators have to “bridge” their management system to the contractor’s management system. There is a push in the industry for contractors to get their SEMS programs in place, but it is not required by BSEE; however, it can be contractually required by operators.
The operator is ultimately responsible for whatever happens on their facilities, even if they contract out all of the work to their contractors. The operator has to look at the contractor’s management system. For example, let’s take management of change and assume the operator has a good process in their management system, but let’s assume the contractor doesn’t. The operator may specify that when it comes to management of change, the contractor will use the operator’s processes. However, when it comes to job safety analysis, it may be the contractor has a much better system in place for their operations. The end result is piecing together parts of the operator’s and contractor’s management system to create a “fit for purpose” management system.
The problem with the “fit for purpose” management system that includes operator and contractor elements is the requirement for retraining those personnel in the “fit for purpose” management system. But if the contractors move forward with putting a SEMS program in place, they should go through the same processes operators would follow such as audits by an ASP. If they follow the same exact procedures and processes under SEMS, then when they come to contractual negotiations and go through that bridging process it is going to save that contractor a considerable amount of resources.
The largest improvement in SEMS will be in managing your contractors to ensure they are conducting safe operations. Today, about 90% of the work being performed on offshore facilities is by contractors. It makes sense for contractors to have a SEMS program in place. I see this as the biggest change going forward with SEMS and the overall management of those contractors.
Currently, operators have to go out and do performance audits of their contractors to make sure they are meeting their goals. Those goals may be operational or health and safety. With SEMS, some contractors are audited 20 or 30 times a year by different companies to meet the same SEMS requirement. It can take up an enormous amount of resources for the contractor and operator to manage that process.
There is a large benefit to a contractor getting a SEMS certificate. Some operators have modified their management systems to say if a contractor has a SEMS certificate, then there is no need to be audited again, or may not audit you as frequently or may not dive down as deep into your system when performing an audit.
SEMS is geared to spending the majority of the audit at the lower levels of the organization, where the majority of the work is performed. An audit determines if the workers are effectively implementing the management system. An auditor looks at the records, observes the work, and interviews employees on their roles and responsibilities to make sure they understand what those are. An auditor checks the company is doing what they said they would do under their management system.
Summary
SEMS can be a cost saver for contractors and operators. SEMS can take some of the pressure off the operators to assure that all of their contract audits are performed. A typical operator may have 30 or 40 contractors at any given time. In addition, a large contractor may also get audited 20 or 30 times by different operators. A SEMS certificate is beneficial for a contractor to have and will improve their operations.
When it comes to SEMS, it comes down to what the company says they are going to do. An audit is a snapshot in time. If a company has an incident and BSEE starts an investigation, they will look closely at the SEMS program. If BSEE sees examples where a company violated their own laws, then the management system is broken. The management system is the company’s law.
Management systems are made up of two types of documentation. First, policies, procedures, work instructions, etc. that describe how the organization does business and the appropriate pass-fail criteria or metrics to measure performance. Second, records which substantiate work is being done the way it is intended. SEMS has had a positive impact on the management system and has resulted in greater safety and environmental stewardship for the oil and gas industry.
Author: Brady Austin is Quality, Health, Safety and Environment (QHSE) Service Line Owner for Lloyd’s Register in North America. In this position, he is responsible for overseeing items such as offshore safety training and is involved in a wide variety of industry task groups for the American Petroleum Institute, International Association of Drilling Contractors, Center for Offshore Safety and Ocean Energy Safety Institute. The majority of his background has been in production, primarily in Process Safety Management (PSM) offshore in the Gulf of Mexico. He started as an offshore entry level employee and worked his way up to facilities manager. He has also worked at the Bureau of Safety and Environmental Enforcement as a senior level inspector after the Macondo well integrity failure before joining Lloyd’s Register in 2012.
Comments