October 2022, Vol. 249, No. 10
Features
Pipeline Compressor Stations Reexamine Emissions, Efficiency
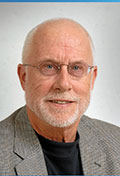
By Richard Nemec, P&GJ Contributing Editor, North America
(P&GJ) — In the global climate change-driven future for the pipeline industry, there is a vision of net-zero emissions compressor stations to transition to clean energy.
Work throughout the midstream sector in this regard has accelerated over the last three years, according to research organizations like the Pipeline Research Council International (PRCI) and the Gas Technology Institute (GTI). Net-zero emissions by mid-century has become a rallying cry for their member companies.
“Today, all the technology exists to have zero-emissions facilities; it just would be very, very expensive to do that with current technology,” said Gary Choquette, PRCI’s executive director for research and IT. “Our single biggest greenhouse gas [GHG] at compressor stations is carbon dioxide [CO2] that is emitted during combustion to drive the natural gas engines running the compressors,” Choquette said. “Fugitive methane emissions are an important part but are a relatively small percentage of the compressor station’s overall GHG footprint.”
Industry and environmental groups define “net zero” as achieving “an overall balance between GHG emissions produced and GHG emissions taken out of the atmosphere.”
It can be envisioned as a set of scales. Producing greenhouse gas emissions tips the scales. To address climate change, society wants to get those scales back into balance, which means no more GHG can be added to the atmosphere in any given year than is taken out.
At net zero, offset actions will reduce existing GHG already in the atmosphere. This is done by processes such as planting new forests or drawdown technologies like direct air capture. The more emissions that are produced, the more CO2 we need to remove from the atmosphere (called sequestration) to reach net zero.
There are strong business incentives for gas compression equipment manufacturers and for pipeline operators to address compressor station emissions, said Joel Moxley, CEO of GPA Midstream Association.
“Manufacturers know operators are focused on environmental-societal-governance [ESG] issues and are looking for solutions to cut emissions and boost efficiency,” Moxley said. “Operators understand that every molecule that escapes the processing stream is one that they can’t sell.”
There are more than 1,200 compressor stations on the U.S. interstate natural gas pipeline, and an estimated 50.7 Bcf (1.4 Bcm) of methane emissions leaks from the compressors and other related equipment annually, such as valves, flanges and connections. Replacing these facilities that typically are spaced every 50 to 100 miles (80 to 161 km) along pipelines would cost about $2 million/station, according to industry estimates.
At mid-year 2022, a project team from GTI and the U.S. Department of Energy (DOE) had begun work to design, build and test a fully functional linear motor leak recovery compressor to bolt onto a full leak recovery system designed specifically to gather and recompress methane emissions from midstream transmission and storage compressor stations.
“The leak recovery compressor is uniquely suited to provide variable flow capabilities to match the variable leak rates inherent in this application,” said Diane Miller, GTI’s communications director. “It has also been designed for a high-pressure discharge to compress that gas back to midstream operating pressures, often at more than 1,000 psi.”
The advanced compressor should capture a wide variety of leaks across the natural gas value chain, including reciprocating compressors and pneumatic controllers that are among the largest methane emitters, according to GTI engineers.
Leaks can be captured from the ventilation systems at legacy and newly installed transmission, storage, gathering and processing facilities, and compressed back into the pipeline. This project intends to validate what GTI terms as the effectiveness of the technology in a variety of relevant environments to identify and quantify the wide-ranging applications for its use.
“In addition, the leak recovery compressor must be reasonably priced and highly reliable to encourage voluntary adoption,” Miller emphasizes. “Existing, low-pressure leak recovery compressors, limited to discharge pressure of less than 100 psi, can cost in excess of $75,000 according to industry stakeholders exploring these options. The team’s goal is to develop a less-expensive unit capable of reaching several thousand psi.”
Covering both inter- and intrastate, gas pipelines stretch over 305,000 miles (491,000 km). In addition, another 185 oil pipelines totaling 190,000 miles (306,000 km) collectively are in operation with another 34 under construction.
Three interstate pipeline operators represent about a third of the U.S. interstate system, and one of the trio, Kinder, announced in July plans to add up to 2.6 Bcf/d (74 MMcm/d) capacity to serve the growing U.S. liquified natural gas (LNG) market.
Members of the Interstate Natural Gas Association of America (INGAA) have partnered with U.S. Environmental Protection Agency (EPA) programs to reduce methane and other GHG emissions.
A good deal of the work by the major interstate pipeline operators is centered on compressor stations. A bottom line to the ongoing INGAA efforts is to help the federal government avoid reporting falsely that emissions from the stations are increasing, according to INGAA’s Sandra Snyder, vice president for the environment.
In the recent past, Snyder has urged EPA number crunchers to reform their methods for calculating GHG emissions from the transmission sector to avoid making false estimates of emissions increases.
“The estimated station count affects the activity data applied to several important emission sources for the transmission segment: station leaks, reciprocating and centrifugal compressor leaks, station blowdowns and pneumatic device counts,” Snyder told EPA in a formal response in 2021 to EPA’s Inventory of U.S. Greenhouse Gas Emissions and Sinks, 1990-2019. EPA’s past “erroneous paper increases” for transmission emissions is “very problematic and should be remedied,” she noted.
As one element in a four-pronged approach to reducing emissions, more than a dozen INGAA members participate in the ONE (Our Nation’s Energy) Future Coalition that aims to reduce U.S. natural gas emissions below 1% by 2025 collectively from the production, processing, transmission and distribution of gas. Compressor stations’ share of the reduction goal is determined by their proportional share of current emissions.
Transmission/storage looks to reduce its emissions down to 0.31% by 2025. The three other efforts involved EPA’s Natural Gas STAR and Methane Challenge programs, and the Environmental Partnership in the oil/gas industry.
In a “Lessons Learned” publication from the EPA’s STAR program, partners advocated simple changes in operating practices and in the design of pipeline blowdown systems as cutting costs and “significantly reducing methane emissions” while keeping systems pressurized. Although “pressurized systems may also leak from the closed blowdown valve and from reciprocating compressor rod packing, total emissions can be significantly reduced,” according to the EPA report.
The report notes four options for reducing emissions when taking compressors offline: (1) keeping compressors pressurized when offline; (2) connecting the blowdown vent lines to fuel gas system, recovering all or a portion of vented fuel gas; (3) installing static seals on compressor rod packing; and (4) installing ejectors on compressor blowdown vent lines.
INGAA members have made methane emissions reduction commitments covering pipelines, pneumatic controllers, gas storage wells, compressor stations and the development and sharing of information on effective practices. For compressor stations, this includes minimizing emissions for planned station maintenance.
It also means minimizing emissions from rod packing seals on all reciprocating compressors, according to INGAA’s website:
“Member companies agree to replace rod packing on all transmission/storage reciprocating compressors by utilizing one of the following options: (1) a condition-based replacement approach; (2) replacing packing every 26,000 hours of operation; or (3) replacing packing 36 months from the date of the last packing replacement work.”
According to INGAA, these collaborative efforts have resulted in a 31% drop in methane emissions from 2011 through 2019, during which time the number of compressor stations grew from 465 to 661. INGAA calls it “meaningful and measurable progress” that is equivalent to taking 1.5 million passenger cars off the road in the United States.
Clearly, efficiencies can be achieved, according to PRCI’s Choquette. “Anything you can do to improve efficiencies, whether on the engine, compressor or reducing pressure losses in the system, will reduce GHG emissions,” he said. “And in some cases, it will also lower your operating costs, especially from a fuel perspective. If you can find efficiency gains to reduce fuel consumption, there is an obvious economic benefit.”
Most compressor station GHG emissions come from CO2 that is emitted during combustion from the use of natural gas-fired engines running the compressors. Choquette said fugitive methane emissions are “an important part, but a relatively small percentage” of the compressor station’s overall GHG footprint.”
That has sparked a push to electric motors at compressor stations, and they have “some reliability issues that you don’t have with gas engines,” Choquette said. “The bigger issue from a GHG standpoint is that currently not all of electricity [used for those motors] is green,” he said. “If you were to install a new unit today, the best choice would be a gas engine as having a lower overall GHG footprint unless you happened to be in a location that has a very high percentage of renewable power sources.”
With electric motors on compressors supplying fuel to a gas-fired power plant, there is a loss of efficiency in having to transport the electricity over transmission lines to the compressor station. Although it is more efficient to drive the compressors directly with natural gas in this scenario, Choquette notes that 10 or 20 years from now, “if you have a large portion of renewables in the portfolio, electric motors then are a better GHG emissions reduction option.”
Canada’s TC Energy carries on a companywide campaign to reduce GHG emissions from its extensive pipeline and compressor station operations, modernizing, addressing efficiency and decarbonizing its operations.
TC executives concede that a “significant portion” of its emissions is produced in fuel combustion used by compressor units, so the company is working “to gradually convert [its] compressor fleet to electric motor drives, where feasible.”
This requires using a company such as Dual Drive Technologies LTD on compressor units, according to TC Energy’s website.
In addition to switching to electric motors, industry groups also recommend that operators consider other options, such as (a) recovering vapor gas, (b) installing carbon monoxide catalysts and selective catalytic reduction (SCR) technology on exhaust system equipment, and (c) implementing aggressive leak detection/repair programs.
In June, GPA Midstream Association and its affiliated supplier organization launched a new program, “Let’s Clear the Air,” to start a wider dialogue and public education campaign supporting the ongoing energy transition, including addressing compressor station issues. The groups have committed to engaging all 60,000 midstream professionals in the multifaceted effort. “We all have a voice and a story to tell,” said GPA Midstream’s CEO Moxley.
“Companies are always looking for ways to reduce emissions, including the nature of emissions,” said Moxley, citing the examples of wet seals in the past for stopping escaping gas from the compressor casing, and, since the 1990s, the switch to dry gas seals. “We are also looking at different processes that might allow operators to efficiently recover leaked methane so it can be reinjected into the processing stream.”
Moxley said the inherent nature of gas compression will result in some emissions, so the goal of net zero is also dependent on operators earning offsets. The challenge is access to capital, and that varies with each operator and operating system. “Each station is its own unique mix of capacity, usage levels, age of equipment, and technology,” he said.
From Choquette’s perspective, efficiencies, investment and technology advances eventually all will lead to net-zero compressor stations, and PRCI researching projects that can help make a difference. Technology advances on efficiency improvements can be made relative to bringing back data from compressor station equipment and analyzing it to see if the equipment is operating as efficiently as expected, he noted.
If the equipment is underperforming, the analysis looks at what point would it be economic to make changes, and PRCI published its CO2-E economic tool last year, a spreadsheet for operators to determine which change options have the biggest bang for the buck, according to Choquette.
“It is similar to a net-present-value calculation in an economic model, but it is specifically focused on the reduction of GHG emissions on a dollar-per-ton basis,” Choquette said.
In the hydrogen realm, there are many more technology advances, according to Choquette. “There are hundreds of issues needing to be addressed with hydrogen,” he said. For compressor stations, hydrogen’s lower ignition temperature becomes an issue; the flame is often hard to see, creating some added safety risks. The rebuilding of electrical systems also may be required in switching over to pure hydrogen, he said.
“It affects whether you can repurpose existing equipment to use hydrogen and cut replacement costs,” Choquette said. In mid-2022, PRCI and Sandia National Laboratory in New Mexico were putting together a proposed project to address this issue.
Choquette calls the emissions from compressor stations “a very big and complex issue,” particularly when the envisioned transition to a hydrogen economy is included in the mix. He noted that the more hydrogen is added to the U.S. energy system, the more pipeline compression is needed across the board.
Although historically, the U.S. energy sector has been more regulatory-driven, Choquette thinks the current climate change-stimulated push is more societal-driven, with investors and other stakeholders pushing energy companies. PRCI has multiple research projects addressing this area.
It has a multiyear, multimillion-dollar GHG Strategic Research Priority effort looking at modifying compressor facilities as well as the pipelines developing repair techniques that don’t require shutting down sections of pipe, and the better identification and stoppage of leaks. “It’s a really large effort,” according to Choquette.
Paul Spadone, an industry commentator, concluded that “significant results” have been produced by voluntary emissions programs in partnership with EPA over recent years. He points to programs like the EPA Natural Gas STAR effort, the Methane Challenge program and ONE Future Coalition, among others, estimating that they have decreased average methane emissions from transmission and storage natural gas compressor stations by about a third from 2011 to 2019, despite the addition of close to 200 new facilities during the same period.
“Both voluntary and required compliance actions are achieving these results,” Spadone wrote in January this year. “Most owner/operators of cross-country pipelines are actively addressing emissions through programs like compressor station modernization, focusing on aging pipeline infrastructure where newer technology can significantly lower emissions and increase operational efficiencies.”
Richard Nemec is P&GJ’s Los Angeles-based contributing editor and a frequent contributor to the publication. He can be reached at
rnemec@ca.rr.com.
Comments