October 2023, Vol. 250, No. 10
Features
Composite Repairs Effective for Various Pipeline Defects
By Russell Giudici, Advanced FRP Systems
(P&GJ) — Composite repairs are an effective method for repairing various defects in pipes and continue to gain widespread acceptance in critical industries, like midstream oil and gas, because of the multitude of benefits they offer.
These benefits include 1) being quick to install, 2) can be installed while assets are online, 3) providing structural reinforcement and corrosion prevention/inhibition, and 4) can be installed at ambient temperatures without heat, unlike steel sleeves.
In this article, multiple types of defects are reviewed with a discussion on their compatibility with composite repairs. The defects discussed include external and internal corrosion, crack-like defect (including stress corrosion cracking), dents, and gouges. Relevant testing and established key concepts are discussed to understand why composite repairs may be right for different types of defects.
Composite repairs are an effective method for repairing various defects in pipes and are gaining widespread acceptance in midstream oil and gas, because of a multitude of benefits:
- Composites are quick to install.
- They can be installed while assets are online, eliminating downtime.
- They provide structural reinforcement and corrosion prevention and inhibition.
- They can be installed at ambient temperature without heat, unlike steel sleeves that require welding.
This article will review the types of pipeline defects that can be repaired with composite repair systems for long-term effectiveness, including external and internal corrosion, crack-like defects, dents and gouges.
External Corrosion
External corrosion is the deterioration of the pipeline due to the chemical reactions between the pipeline material (steel) and its environment. Corrosion is typically prevented and mitigated using coatings or cathodic protection. However, in the case of damaging corrosion that progresses unchecked, pipelines can experience through-wall failures from the resulting loss of material and strength.
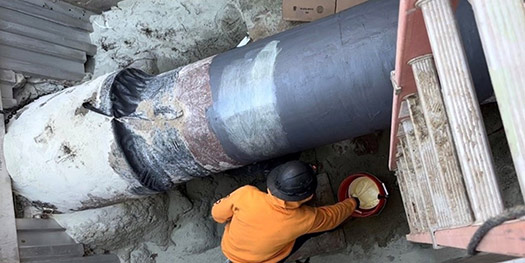
The integrity of a pipeline is threatened when external corrosion causes excessive degradation. According to PHMSA, fewer than 40% of all pipeline incidents are caused by external corrosion. Composite repairs can inhibit further degradation by acting as a corrosion barrier, while also providing structural reinforcement.
The selected repair system is fully validated through third-party testing and engineered to withstand the maximum operating pressure, plus the required safety factor, composite repairs provide a permanent repair solution, and the pipeline can continue to operate.
Internal Corrosion
Internal corrosion is a major cause of pipeline incidents. In 2022, 13.3% of all reported pipeline incidents were caused by internal corrosion, according to PHMSA records.
Crude oil pipelines are especially vulnerable to internal corrosion because of the presence of water and a wide array of other chemicals. Sweet crude oil can cause corrosion when dissolved carbon dioxide reacts with water to form carbonic acid. Sour crude – an even more aggressive service – has hydrogen sulfide present, which can react with moisture to create sulfuric acid.
External composite repairs on a pipe that is suffering from internal corrosion will not address the underlying cause of corrosion. Since the internal pipe will eventually lose pressure containment, a long-term composite repair can only be offered if a structurally independent pipe is created around the existing pipe.
Special consideration and much more extensive testing are required to verify the performance of a structurally-independent pipe. Critical characteristics for long-term, external repairs include the adhesion value to the host pipe, as well as the adhesion between layers of the composite – the interlaminar shear value.
Only composite repairs that have undergone rigorous testing for pipes with through-wall failures should be considered as a permanent repair on pipes with internal corrosion.
Crack-Type Defects
Cracks are stress-induced separations of the pipeline metal. There is a wide range of causes, including the manufacturing methods originally used to create the pipe. Pipe manufactured before 1970, otherwise known as “vintage” pipe, used historic manufacturing methods, such as furnace butt-welding, lap and hammer welding, and low-frequency electric-resistant welding (ERW). Each manufacturing method results in its own risks, including the risk of different modes of cracking.
Many lab and field programs have tested and subsequently demonstrated the success of composite repairs of individual cracks running axially on a pipeline.
Two critical concepts explain composite repairs’ effectiveness for crack axially oriented cracks; first, these cracks grow due to increased stresses, which lead to crack propagation. Second, composite repairs share load with the substrate pipe if designed correctly.
One critical characteristic for designing an effective composite repair for an axially oriented crack is the modulus of the composite. By employing a high modulus repair, the composite takes the load, as opposed to the metal, arresting the growth of crack-type defects.
If the correct repair system is designed with the proper adhesive and using the right installation methods, composites can be considered a permanent solution for individual cracks running axially on the pipeline.
Stress Corrosion Cracking
There are other causes for cracking besides manufacturing methods. Stress corrosion cracking (SCC) is the formation of cracks caused by multiple factors, including the presence of corrosion and tensile stress. SCC manifests in groups of cracks, called colonies.
Composite repair of SCC should be engineered and designed to account for the unique challenges associated with crack colonies. Key factors to consider include crack characteristics (depth, for example) and traits of the composite repair.
While composite repairs show promising results for colonies formed by SCC, additional research and development is being done to further validate this repair methodology.
Dents, Gouges
Dents cause increased stress and strain and a reduction in pipe diameter. There are different types of dents, including plain dents or dents combined with other defects, such as gouges, also referred to as mechanical damage.
Not all dents pose a significant structural problem, but some dents may pose more of a threat than others. The effects of the dent on strength and fatigue life depend on its characteristics (e.g., length and width) and the type of dent.
For example, plain dents generally do not significantly reduce burst strength, but dents with gouges have significantly lower burst pressures. Even though some types of dents might not pose immediate, severe threats, they can hinder in-line inspections or reduce flow rates.
Composites repairs are widely used and accepted to address both dents and gouges in pipelines. Repairing severe dents requires rebuilding and repairing the structure of the pipe. If the dent is present with a gouge, the repair requires addressing the resulting wall loss.
Right Choices
Choosing the right composite repair requires a firm understanding of the following elements:
- Installation efficiency
- Cost, especially related to the number of layers needed for an effective repair
- Validation of chosen composite technology to withstand maximum operating pressures
- Environment and unique circumstances (high-temperature environments, complex geometries, etc.)
Engineered Design
The engineered design of the composite repair system will make a difference in the effectiveness of your chosen technology. The number of required layers for a repair depends on the pipe, operating pressure, wall loss, the composite’s strength, and ply thickness. For example, thin-ply composites may require more layers to provide the thickness required by ASME PCC-2.
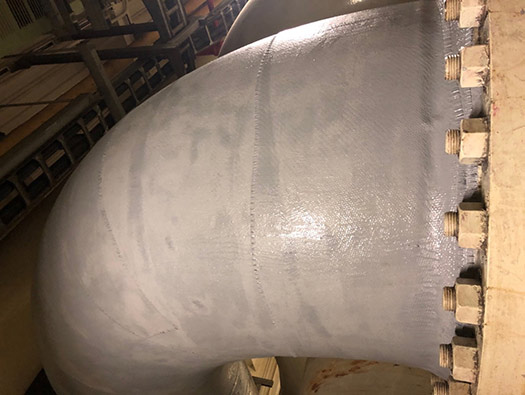
Thicker composites require fewer layers to achieve the same thickness. Thin composites may also increase inefficiencies in installation, due to the increased amount of labor and time to apply many layers of composite to one section of pipeline.
Composite repairs are a cost-effective and reliable way to address a variety of pipeline defects, including cracks, corrosion, dents, and gouges. These repairs can be performed quickly and easily, with minimal disruption to operations, as long as the right composite repair system is chosen.
Comments