October 2023, Vol. 250, No. 10
Features
Plugging the Leak: Tackling Methane Emissions
By Benjamin Fuentes, Thermo Fisher Scientific
(P&GJ) — The oil and gas industry is heavily regulated by a number of governing bodies, including the U.S. Federal Energy Regulatory Commission, to ensure pipelines run efficiently and safely. However, no matter how controlled operations are, toxic vapors from fugitive emissions continue to be a problem.
They pose a serious threat to staff, the wider population and the environment, as well as contributing to loss and unaccounted for (LAUF) product that, in some cases, can add up to thousands or millions of dollars each year.
Added to this issue is the expansive territory where oil and gas pipelines are found, and the minuscule leaks that are potentially scattered throughout, making identification especially troublesome. The industry is, therefore, looking for novel technologies to develop better leak detection and repair (LDAR) strategies.
This article delves into the challenges of LDAR and highlights some solutions that could help companies to minimize waste, increase efficiency and maintain environmentally friendly operations.
The oil industry was revolutionized in the early 1860s by the introduction of pipeline transport, which drastically decreased its reliance on wagons and boats to transport this precious cargo, not only lowering transportation costs but delivering ‘on tap’ oil where required.
Today, the U.S. is home to the largest expanse of oil and gas pipelines in the world – over 250,000 miles – with Russia coming in a distant second with well under half that figure.
However, the same technology that provides such convenience also holds the potential to devastate the local environment. A catastrophic California pipeline leak in 2021 spilled over 126,000 gallons of oil into the Pacific Ocean, killing swathes of local wildlife which washed up on the shores of Huntington Beach. Leaks like this can irreparably damage the environment, decimate profits and erode the already ebbing public support for fossil fuels.
The use of these fuels is set to take a back seat in favor of renewable alternatives over the next few decades in response to clean energy initiatives, and natural gas is primed to play a supporting role in this transition by replacing some of the more polluting fossil fuels. The U.S. Environmental Protection Agency has stated that natural gas and petroleum systems produced 28% of all U.S. greenhouse gas emissions in 2020 and, in response, issued new national standards for hazardous air pollutants, which the industry can’t afford to fall foul of.
Since methane, a major component of natural gas, is estimated to be over 80 times more damaging to the environment than carbon dioxide, many of the oil and gas industry’s key players have pledged to take steps to minimize natural gas emissions of all types.
Sin of Emission
Methane emissions due to the accidental release of natural gas are known as “fugitive emissions” and can be caused by everything from pipe corrosion and earthquakes to unintentional pipe excavation and equipment failure. Unfortunately, natural gas is much harder to visually detect than an oil spill, even in cases of extremely large leaks.
However, leaks don’t necessarily have to be catastrophic to be damaging to the environment. Even small volumes of fugitive emissions can represent vast amounts of gas over time, making it essential to be able to detect and fix emission hotspots as quickly as possible.
Unfortunately, the detection of these small leaks can prove challenging, since the corresponding pressure changes are far too small to register on the pipeline’s widely spaced pressure gauges, which are calibrated to monitor routine pressure variations.
The most efficient method of surveying vast lengths of remote pipeline for small leaks is to use thermal imaging helicopters or drones to search for clouds of methane that indicate pipeline damage. Specially trained sniffer dogs can then be sent to pinpoint the exact location of the leak, allowing necessary repairs to be carried out.
However, the use of sniffer dogs makes it challenging to comply with strict industrial standards, and handheld laser methane detectors, as well as optical gas imaging cameras, are increasingly being used in their place.
Several modern techniques to reduce the manual nature of searching for leaks have been gaining traction recently, such as acoustic leak detection, which uses externally mounted sensors to identify the acoustic signature of gas flowing through cracks or holes. With systems like this, the pipeline can be continuously monitored, and leaks detected as soon as they occur, rather than relying on sporadic manual searches.
Lightweight, portable gas leak detectors are another way to quickly detect fugitive emissions of organic and inorganic compounds for Method 21 compliance, LDAR applications and site remediation. Some systems, such as the Thermo Scientific TVA2020 Toxic Vapor Analyzer (Figure 1), can be configured as either an FID (flame ionization detector) analyzer or dual detection FID and PID (photo ionization detector) analyzers.
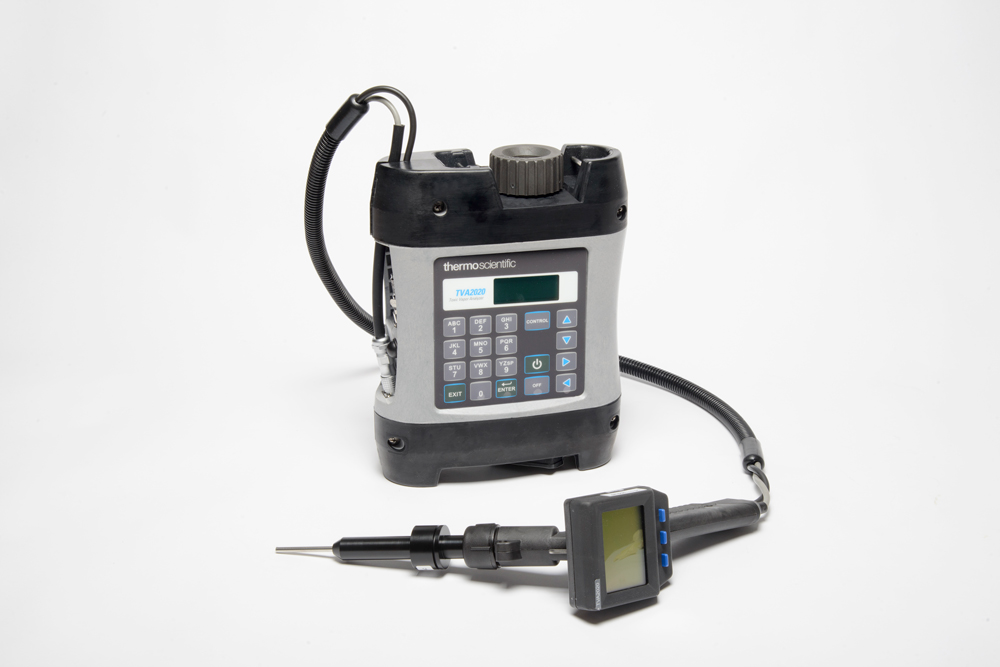
FID analyzers enable highly sensitive measurement of organic compounds and allow for a wide dynamic and linear range that produces stable and repeatable responses.
The enhanced capabilities of systems configured with both FID and PID technologies offers a more rapid reading of organic and inorganic compounds compared to a single detector technology, and more comprehensive gas coverage than similar-sized individual PID and FID analyzers.
Larger leaks, on the other hand, are often easier to diagnose, due to the inherently large pressure changes that can be detected by in-line pressure gauges. If this occurs, the gas flow to any damaged sections of pipeline can be restricted, but to fix the leak, damaged sections of pipeline must be removed and replaced.
It is also common practice to purge the contents of the removed section for safety reasons, venting large amounts of methane into the atmosphere.
To avoid this, it is increasingly common to insert a pig – a cylindrical or spherical device with an outer diameter that forms a seal against the inner diameter of the pipe, upstream of the affected section.
Inert gas is then pumped into the pipeline behind it, propelling the pig forward and forcing the downstream natural gas beyond a shutoff valve. The damaged section of pipeline can then be removed – and replaced – leaving only inert gas to be purged into the atmosphere.
Want Not
A further source of fugitive emissions present in almost all areas of natural gas processing, transport and storage is the centrifugal compressors used to maintain a constant pipeline pressure. Although highly effective, the seals surrounding the rotating shaft can still leak small amounts of methane and, with the industry continuously operating an estimated 25,000 compressors, this can add up to a considerable amount.
Fortunately, techniques like recompression, which captures the leakage across the seals and injects it back into the gas stream via an electric motor-driven compressor, can be employed to negate this.
However, fugitive emissions aren’t the only issue with compressors and, like most combustion engines, they emit exhaust fumes containing greenhouse gases. These are referred to as combustion emissions, and it isn’t just compressors which are at fault; these exhaust fumes also come from generators, gas-fueled equipment and flares. Flaring is used to burn waste gas which would otherwise be vented into the atmosphere and, according to the Methane Guiding Principles consortium, it accounts for two percent of the total emissions from oil and gas production.
Consequently, it will be essential to reduce these emissions to meet future national standards, and flare gas recovery systems have been developed to capture and reuse this waste gas as fuel for a variety of other applications.
Powering Up
The remote locations of vast lengths of pipeline make it extremely challenging to supply electricity to equipment such as valves and gauges. So, to eliminate reliance on electrical power, most conventional pipelines employ passive natural gas-actuated valves, which operate by using the pressure of the pipeline’s natural gas to open and shut the valve as required.
However, once complete, the gas used for actuation is vented into the atmosphere. Though small, these methane emissions can add up to be significant, especially considering the countless valves contained in a typical pipeline.
One zero-emission alternative is to employ valves that operate electro-hydraulically, using a small electric motor to drive the actuator via pressurized hydraulic fluid. These valves require no natural gas for actuation, but do require electrical power which, for small valves, can be supplied via solar panels. Routing mains power to remote lengths of pipeline isn’t feasible, since the infrastructure costs would be too high so, for larger valves requiring more power to actuate, a modified version of natural gas-actuated valves can be used.
Much like gas-actuated valves, these also use the pressure in the pipeline to operate, but subsequently use a small electric motor to propel the natural gas back into the supply line, rather than venting it into the atmosphere. Again, due to the low power consumption, these motors can be powered via local solar panels.
Proactive Prevention
Detecting leaks is undoubtedly a vital part of pipeline maintenance. However, in an ideal world, issues would be able to be identified and fixed before a leak can even occur.
Conventional emission detection and prevention systems are often employed sporadically, and tend to be reactive rather than proactive, only being used when an issue is already suspected. For example, so called smart pigs can be used to scan concerning areas of pipeline in a process known as “magnetic flux leakage testing.”
As the pig traverses the pipe, it magnetizes the pipeline wall and observes the shape and strength of the corresponding magnetic flux lines. Any changes to the wall of the pipe – such as corrosion or pitting – will cause these flux lines to deviate from those of an undamaged pipe section, allowing areas of concern to be identified. If these issues are identified early enough, a protective composite sleeve can be wrapped around the exterior of the pipe to reinforce it, rather than having to remove and replace large sections of pipeline.
Transitioning from reactive to proactive maintenance has the potential to make a step-change in pipeline safety and reliability. This is where flow computers can help to maintain the efficiency and safety of pipeline systems. The latest generation flow computers (Figure 2) also incorporate the latest hydrocarbon measurement standards and calculations that enable tracking of the release of methane.
Fast processing speeds and improved memory capabilities mean that measurements can be performed every two minutes compared to every 15 minutes with previous systems.
The use of advanced computing methods – such as machine learning and artificial intelligence – to continuously analyze real-time data streams from a whole host of sensors is allowing the development of powerful predictive tools that can minimize manual process input and eliminate the chance of human error via rule-based strategies.
These tools are developed by analyzing historic data to determine failure indicators – like predefined temperature or pressure limits – that, if breached, will result in automatic adjustment or shutdown of the pipeline to mitigate the risk of damage. Similarly, with historical data to compare against, it is often possible to use real-time data to predict equipment malfunction before it happens, allowing preventative maintenance.
However, infrastructure upgrades will be essential to ensure the number, sensitivity and connectivity of these sensors is sufficient to create the vast monitoring network needed to detect even the most minute changes.
Future Investment
Environmental guidelines are set to become increasingly stringent in the near future, and it is essential for the oil and gas industry to invest in new technologies and methods to minimize emissions of all natures. Albert Einstein once noted that, while intellectuals merely solve problems, geniuses prevent them, and proactive maintenance combined with advanced computing techniques holds the key to revolutionizing the industry.
Closing the loop between real-time monitoring and process control will allow issues to be predicted and remedied before leaks can occur, safeguarding the environment, decreasing waste and boosting profits. Investing in these upgrades certainly won’t be cheap, especially with such huge expanses of pipeline to cover, but with prevention often cheaper than the cure, the oil and gas industry simply can’t afford not to.
Author: Benjamin Fuentes graduated from the University of Texas of Permian Basin in 2006 with a bachelor of Business Administration. He joined Thermo Fisher Scientific as a Regional Sales Manager in 2008, working in various positions across manufacturing operations, marketing and account management, before taking up his present position as business development manager in 2021.
Comments