July 2024, Vol. 251, No. 7
Features
Hydrogen-Blend Pipelines: Integrity Readiness and the Role of ILI Inspection
By Jeff Sutherland, Products Portfolio Leader, Baker Hughes
(Editor’s note: Part 1 of this article was published in the June issue of P&GJ)
(P&GJ) — As cracking threats gained prominence in integrity planning, ILI and assessment methods were initiated and evolved. Attempts to apply non-destructive techniques started in the 1970s, with commercial systems pioneered and introduced by Baker Hughes for USCD (ultrasonic crack detection) for liquid pipelines in the 1990s and EMAT (Electromagnetic Acoustic Transduction) for gas pipelines in the 2000s. Integrity programs since then have evolved to reliably use high-performance crack ILI systems [Ref. 14,18,19,20].
Reported features from ILI related to cracking include “crack-like,” “crack field” and “weld anomalies” as the primary feature types of interest as axially oriented features (where a rupture threat from hoop stress is the expected failure mode). EMAT may also include indicators of localized coating damage.
EMAT ILI systems for crack detection and characterization are available today across most diameters of long-distance pipelines (8-42 inches) (Figure 5).
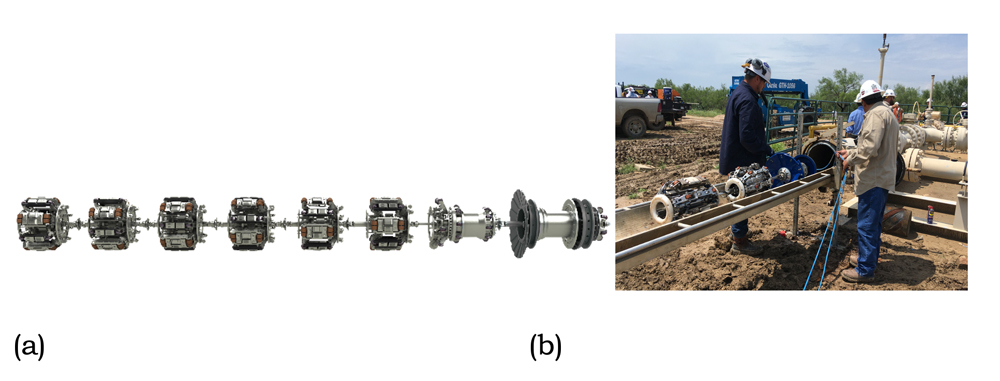
An ironic factor of early EMAT systems was the inability to discriminate material flaws and discontinuities from cracking [Ref 20,21]. EMAT systems today address, and report discriminated features distinctly. And for purposes of early detection of stress concentrators as preferred in the blended hydrogen scenario, the identification of inclusions, laminations and manufacturing flaws becomes preferential in collected data. This ability is an example of potential evolution of capabilities.
It is envisaged that crack ILI will continue to evolve with Hydrogen pipelines as well as form part of a robust integrity management program.
A core principle of Engineering Critical Assessment (ECA) of cracks (including SCC, seam weld cracks, girth weld cracking, laminations, and weld anomalies) is based in fracture mechanics and fatigue crack growth methodologies [Ref 10] as well as an understanding of reported ILI features and interpretations such as crack profiling and crack field statistics. [Ref 14].
Updates to ILI crack profiling was recently evaluated and validated [Ref 18] for achieving reduced conservatism in fitness-for-service assessments (Figure 6). Such approaches would apply to validation of cracking assessment in hydrogen pipelines.
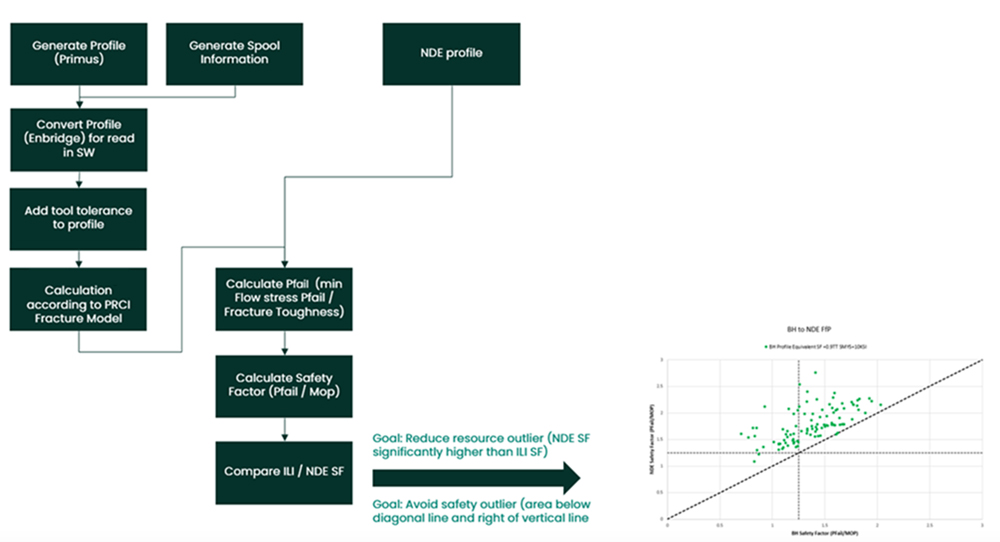
Hard Spots
Hard spots are distinguished as localized areas of material in pipe that is typically of higher “hardness” than the line pipe specification. As material hardness is identified as a potential threat susceptibility condition for blended H2 operations, the identification of hard spot areas becomes a factor to address higher risks of failure from defects due to a localized reduction in material fracture toughness.
ILI technologies specifically for localized material difference detection have existed since the1990s, with even early ILI technologies being sensitive to localized material differences since the 1970s. The most common measurement approach is from remnant magnetic field detection and interpretation.
An example of an ILI signal response for a confirmed hard spot area (Figure 7). Note that signals are distinctive and repeatable. In some cases, other material impurities may also be detectable.
Detected and reported areas of interest may also then be aligned with ILI crack, corrosion, deformation and strain data for a more comprehensive evaluation and assessment.
Corrosion, Gouging
Monitoring for corrosion and external damage (mechanical damage) remains a prominent activity for pipeline integrity as it predicates early detection of conditions, primarily as corrosion and volumetric wall anomaly characterization but also for external cracking (SCC) susceptibility.
As with cracking threats, the threat of corrosion or gouging may be presumed to be an indicator to cracking initiation and accelerated embrittlement crack failure, even from internally permeated hydrogen. For gas pipelines, high-performance MFL (magnetic flux leakage) (Figure 8), is recognized as the most reliable means of ILI inspection for corrosion and gouging/damage threats.
With presumed more conservative acceptability criteria for the case of flaws in hydrogen pipelines, the presence of any such flaws through detection by ILI, is presumed to trigger response and remediation activities. Defect specific sizing tolerances per reported defect has been recently introduced.
As a per-defect tolerance, it provides less conservatism and enables a better understanding of risk and prioritization of severity. Such methods will also certainly likely be advantageous to the critical assessment of metal loss features in the presence of hydrogen.
Advanced MFL systems have the capability for girth weld anomaly assessment, where circumferential crack-like features may be detected and reported.
Pipeline Strain
There is a premise and assumption that pipeline force cycling may not solely be from pressure but potentially in conjunction with external forces/geotechnical forces that may also cause pipeline damage, even with low cycling frequencies.
In today’s MFL ILI platforms, they are typically run with associated high-performance “IMUs” (Inertial Measurement Units) to collect motion measurements of the tool in the pipeline which was pioneered by Baker Hughes in the late 1980s [Ref 22]. This inertial measurement data can be processed to provide continuous GPS location data of the center line of the pipeline, provide independent insight for characterization of dents and other deformation features that may be present, and be interpreted for representative bending strain (curvature) of the pipeline at all points.
Abnormal or unexpected levels of bending strain are indicators of external force/geotechnical forces on the pipeline which may pose an imminent threat.
A primary use for this method includes geotechnically active areas (prone to landslides), areas near active geological faults or areas prone to large pipeline movements due to seasonal changes such as muskeg/swamp conditions, offshore oceanic forces, or ground frost-heave (such as in northern Canada and Alaska) [Ref 24].
And when such strain events are coincident with time dependent flaws (like cracking and corrosion) such as reported by MFL or EMAT systems, a more detailed engineering assessment is to be considered, as assessments of time-dependent flaws in isolation are not applicable [Ref 25].
Longitudinal Strain
New ILI technology has been introduced that provides independent reporting of longitudinal strain distinctly from conventional ILI IMU methods [Ref 26]. It was initially motivated from a need to monitor for geohazard conditions beyond bending strain itself, such as for potential initiation of buckling and wrinkling due to compressive forces.
After H2 introduction, the strain capacity of both base material and girth welds may be affected by H2 embrittlement, further increasing the risk of failure.
Girth Weld Assessment
Girth weld anomaly analysis involves MFL, IMU and strain measurement data to provide prioritized assessment for potential girth weld cracking. Abilities for the identification of girth weld and spiral weld cracking based on advanced MFL ILI technologies was previously presented [Ref 27].
The adoption of these methods has grown from recent history in North America due to concerns of weld undermatching where a high rate of girth weld failures since 2019 has occurred in USA both in active pipelines and in newly constructed pipelines.
Causes are due to use of higher strength pipe than stated SMYS, and inconsistent infield welding procedures leading to HIC and HAZ softening, which significantly lowered the strain capacity for external forces and pipeline movement [Ref 28]. As a hydrogen enabled issue, this should be presumed to be more prominent and distinctive for hydrogen blended pipelines’ integrity.
Predictive Methods
All ILI data-based integrity assessment methods will have practices for monitoring, growth prediction and remaining life estimation. Criteria for feature response and action to identified change (growth) are then according to operator and industry practices.
Such methods are envisaged to be adoptable, and necessary, for blended hydrogen pipeline scenarios. Fundamentally for ILI based integrity programs, change detection is the basis for growth rate estimation.
Within the evolution of pipeline integrity practices, flaw growth methodologies started with corrosion. Baker Hughes were principal authors in the generation of the primary industry guidelines for corrosion growth including for deterministic and probabilistic treatments [Ref 29].
The key aspects of this method were to provide practical, consistent, and systematic means to establish rates of growth. It also identified the opportunities for managing localized and varied growth rates within a defect population, the direct use of ILI-based signal change detection for more accurate growth rate estimation over ILI reported box methods, and guidance to address and validate “very high” or “improbable” rates of predicted growth in practical terms [Ref 30].
The concepts and methods from corrosion (Figure 9) and have since been adapted and applied for other threat types.
An increasing direction of interest takes the form of more holistic assessment, where coincident features and conditions to overall threats take form in integrity programs, which address a high volume and variety of scenarios for potential loss of containment through any means (Figure 10) [Ref 25, 30].
For hydrogen pipeline integrity, such an approach may be necessary over conventional natural gas methods, as the sensitivities of threats and their combinations have a different interaction and set of outcomes over hydrocarbon scenarios.
Most significantly is the use and application of Machine Learning both to ILI signal interpretation but also to predictive analytics for significance of reported features and remaining defect populations. The availability of high count and variety of field validated samples lead to the opportunity for “Big Data” machine learning approaches [Ref 32,33].
Such techniques and methods are naturally structured to manage large volumes of disparate data. They may also involve engineering calculations, practices, and techniques as guiding principles as well as independent explicit checks as boundary conditions of predicted results and historic results.
Tool Readiness
In the context of ILI systems history, the readiness of ILI for blended or pure Hydrogen pipelines comes with the experience and perspective of readiness for other pipeline products. Over time this has come to include methane gases, including H2S, refined liquid products, CO2 & nonhydrocarbon gases, aromatics (ethylenes), ammonia, etc. [Ref 34].
For the blended hydrogen case, the first consideration is safety. As with hydrocarbon pipelines, areas of highest risk are typically the ILI/pigging launch and receive systems of pipelines, where conditions of explosive gas, air and fuel are present.
The application of ATEX practices for pipeline ILI/pigging activities has been used for several decades, where typically risk of a potential explosive environment is mitigated (removed) by purging of the facilities and access points, of the explosive gas by a non-flammable gas. Of note is decompression behaviors of hydrogen depending on pressure and state as would be found in ILI/pigging receiving traps.
In more extreme cases by analogy, there are similar and parallel procedures for ILI/pigging in sour-service (H2S) and hazardous product lines that have also been used for several decades.
For ILI tool system compatibility and run endurance within a blended Hydrogen environment, the assessment is like that for elements of the pipeline itself with initial assessments dating back to the EU Natural project of 2006-2009 [Ref 3,34]. A compatibility assessment includes the expected forms of Hydrogen as gaseous, aqueous/ionic, and scenarios of the presence of water, etc. It reviews effects on materials as the metallics, elastomers (seals), as notably mimics topics noted in the conversion of service of a pipeline.
Monitoring of ILI vehicles and components for damage is already built into active maintenance practices. Materials and technologies for sealing such as in valves and compression equipment are a source that ILI can also draw from, as such sealing materials become qualified for hydrogen service. There is strong confidence that compatibility can be addressed in ILI operations in hydrogen lines scaled to match hydrocarbon and/or other hazardous product pipelines.
Operationally, there is a significant change in ILI tool flow dynamics expected depending on the percent of hydrogen in the product mix, particularly as it will affect gas compressibility, drag, and bypass. For those ILI systems equipped with active variable bypass “speed control” systems, operations at high flow rates will need to be investigated and validated.
However, at one time, that was also an unknown and concern of active ILI speed control systems for hydrocarbon gas pipelines. Today, such systems are used several times every day in pipelines around the world.
Summary
The progression of current hydrocarbon integrity and inspection practices has occurred over the last 50-plus years. From that experienced basis, their applicability to blended hydrogen pipelines is expected to evolve to address the need of future energy transition pipelines.
Further stringent criteria and conservatism are envisaged for hydrogen pipeline integrity at least until experiences with hydrogen pipeline operations as core energy infrastructures become more prevalent and common.
Technologies that have been developed and advanced for monitoring of conventional pipelines are the basis for pipelines of the future energy transition. The application of current crack ILI inspection technologies is mature and will have application for hydrogen pipelines.
It is anticipated that the multitude of technologies needed to manage the threats are available and as a better understanding of critical flaw sizes and specific threats are better established by the pipeline industry, technologies will evolve to meet these potentially higher expectations.
Editor’s note: This paper was first published at the 36th Pipeline Pigging and Integrity Management Conference, February 2024. Organized by Clarion Technical Conferences. Used with permission.
References
- EU Hydrogen Backbone, https://ehb.eu/
- UK Government, “The Ten Point Plan for a Green Industrial Revolution,” Nov. 2020.
- NaturalHy consortium. “Preparing for the hydrogen economy by using the existing natural gas system as a catalyst,” project no.: SES6/CT/2004/5026 61, sixth EU framework, 2009.
- EU Hydrogen Alliance. https://energy.ec.europa.eu/topics/energy-systems-integration/hydrogen_en
- EU Commission “A hydrogen strategy for a climate-neutral Europe” Brussels 2020
- Huising, O.J.C, Krom, A.H.M. “H2 in an Existing Natural Gas Pipeline,” Proceedings of the 13th International Pipeline Conference, IPC2020-9205, 2020.
- ASME B31.12, “Hydrogen Piping and Pipelines,” The American Society of Mechanical Engineers, 2019.
- European Industrial Gases Association, “Hydrogen Pipeline Systems,” EIGA, IGS 121/14, Brussels, 2014.
- ASME B31.8S, “Managing System Integrity of Gas Pipelines,” The American Society of Mechanical Engineers, 2020
- API 579-1 Fitness for Service. American Petroleum Institute, 2021.
- API 1176 Recommended Practice for Assessment and Management of Cracking in Pipelines, 2021.
- Ramboll. G.A. “Hydrogen as Energy Carrier - Comparison with Gas and Electricity,” in Hydrogen in Pipelines, 2021.
- Adianto, R., Skow, J., Sutherland, J., “The Benefits of Accurate ILI Performance on Pipeline Integrity Programs for Axial Crack and Metal Loss Corrosion Threats,” Proceedings of International Pipeline Conference, Paper No. 2016-64612 2016
- Slaughter, M. Spencer, K. Dawson, S.J., Senf, P. “Comparison of multiple crack detection in-line inspection data to assess crack growth,” Pipeline Pigging and Integrity Management Conference, 2011.
- Canadian Energy Pipeline Association. “Stress Corrosion Cracking Recommended Practices,” SCC Working Group, 3rd ed, 2015.
- Pluvinage, G. “Mechanical Properties of a Wide Range of Pipe Steels Under Influence of Pure Hydrogen or Hydrogen Blended with Natural Gas,” International Journal of Pressure Vessels and Piping, vol. 190, 2021.
- Ronevich J. and C. S. Marchi, “Hydrogen Blending into Natural Gas,” Sandia National Laboratories, 2019.
- Tappert, S. Lamborn, L. “Leveraging ILI Crack Profiles,” Pipeline Pigging and Integrity Management Conference, 2023.
- Bott, S., Foreman, G., Hubert, Y., Senf, P., Sutherland, J., “A Study of Crack Detection Ultrasonic Calls Relating to the Different Types of Cracking Discovered in Pipelines When using Crack Detection ILI,” Pipeline Pigging and Integrity Management Conference, 2016.
- Sutherland, J. Tappert, S. Kania, R. Kashammer, K. Marr, J. Mann, A. Rosca, G. Garth, C. “The role of effective collaboration in the Advancement of EMAT inline inspection technology for pipeline integrity management -A case study,” Proceedings of International Pipeline Conference, Paper No. 2012-90021, 2012
- Tappert, S. Allen, D. Mann, A. Balzer, M. Van Boven, G. “Inline Inspection for crack in gas pipelines – Enhancements derived from 5 years operational experience” Proceedings of International Pipeline Conference, Paper No. 2008-64087, 2008.
- U.S. Patent 4945775 “Interial Based Pipeline Monitoring System. 1990.
- Czyz, J. Wainselboin, S. “Monitoring Pipeline Movement and its Effect on Pipe integrity using initial/caliper inline inspection” IBP575_03, Rio Pipeline Conference, 2003.
- Czyz J.A., Fraccaroli C., Sergeant A.P., “Measuring Pipeline Movement in Geotechnically Unstable Areas Using an Inertial Geometry Pipeline Inspection Pig,” ASME 1-st International Pipeline Conference, 1996.
- Yablonskikh, Y. ElSeify, M. Dawson, J. “Strain Demand and Capacity Assessment Based on In Line Inspection of Axial and Bending Strains,” Pipeline Pigging and Integrity Management Conference, 2021.
- Dewar, D. Elseify M. “ILI of Axial strain, technique, case studies and best practices.” Pipeline Technology Conference, 2017.
- Feng, Q. Gu, B., Sutherland, J., Tao, C., Wei, Y., “Evolution of Triax Magnetic Flux Leakage Inspection for Mitigation of Spiral Weld Anomalies” Proceedings of International Pipeline Conference, 2010.
- USA Pipeline and Hazardous Materials Safety Administration “Low strength in High Grade Pipe,” Advisory bulletin ABD 10-03.
- Dawson, S.J., Wharf, J., Nessim, M. “Development of Detailed Procedures for Comparing Successive ILI Runs to Establish Corrosion Growth Rates,” PRCI EC 1-2 Final Report, 2008.
- Dawson, J., Hurd, G., ‘Assessing Repeat ILI Data Using Signal-to-Signal Comparison Techniques.’ Pipeline Pigging and Integrity Management Conference, 2018
- Bluck, M., Dawson, J., Fisher, I., Sutherland, J., “Holistic Data Approach & Results: How the Latest Enhancements in Ili Technology Benefit Engineering Criticality Assessments,” Proceedings of International Pipeline Conference, Paper No. 2010-31284, 2010
- Hurd, G. Elliott, J. Farnie, S. Sutherland, J. “Advancing In-line Inspection technology and Pipeline Risk Management through Advanced Analytics of Big Data” Pipeline Pigging and Integrity Management Conference, 2019.
- Hurd, G. Miller, S. “Exceeding Performance Standards of Pipeline Inspection and Integrity with Complex and Challenging Defects,” Pipeline Pigging and Integrity Management Conference, 2021.
- Pipeline Products Compatibility Assessment. Baker Hughes internal practices.
- USA Department of Energy. “Department of Energy Hydrogen Program Plan,” 2020. (https://www.hydrogen.energy.gov/docs/hydrogenprogramlibraries/pdfs/hydrogen-program-plan-2020.pdf)
- USA Department of Energy, “US National Clean Hydrogen Strategy and Roadmap” , June 2023. (https://www.hydrogen.energy.gov/library/roadmaps-vision/clean-hydrogen-strategy-roadmap)
- COAG Council (Government of Australia), “Australia’s National Hydrogen Strategy,” 2019.
- Department of Natural Resources (Government of Canada), “Hydrogen Strategy for Canada,” Dec 2020.
Comments