April 2025, Vol. 252, No. 4
Features
Exploring Anode Performance in Presence of AC Source
By Dr. Ahmed Mahgoub, CP SME, and Ahmed Abdelbagi, CP SME, Saudi Aramco, Saudi Arabia.
Editor’s Note: This is the first of two parts of an article that focuses on cathodic protection and anode performance. Part 2 will be published in the May edition of P&GJ.
(P&GJ) — Cathodic protection (CP) is a technique to reduce the corrosion of a metal surface by making that surface the cathode of an electrochemical cell. The cathode in an electrochemical cell is the electrode where reduction (and no corrosion) occurs.
Prior to apply cathodic protection, corroding structures will have both cathodic areas and anodic areas (those areas where corrosion is occurring). It follows, then, that if all anodic areas can be converted to cathodic areas, the entire structure will become a cathode and corrosion will be eliminated. This can be achieved by direct current is forced onto all surfaces of the structure to be protected.
This CP current shifts the potential of the structure in the active (negative) direction, resulting in a reduction in the corrosion rate of the metal. When the amount of current flowing is adjusted properly, it will overpower the corrosion current discharging from the anodic areas on the pipeline, and there will be a net current flow onto the pipe surface at these points. The entire surface then will be a cathode and the corrosion rate will be reduced.
Al-based alloys are attractive as anodes in the CP of steels in seawater due to their low cost and high current capacity. The main disadvantage of Al as a sacrificial anode is its natural ability to form a very stable and passive oxide layer, which hinders corrosion of the metal itself and shifts the metal potential to less-active values.
Moreover, Mg anode is widely used to protect steel because it is more electronegative than it and hence it is capable to supply electrons to the more electropositive steel, providing CP of this metal surface. However, the Mg sacrificial anode performance is impacted in the presence of AC interference as the stray current accelerates the transmission and diffusion of oxygen, so the corrosion rate under AC interference is higher than that with no AC interference.
Furthermore, Zn ribbon anodes provide a very simple, cost effective, maintenance-free method of AC mitigation, however, Zn faces high consumption/corrosion rates in the presence of AC. Based on that, it is accessing the effectiveness of Al, Mg and Zn anodes in the presence of AC induced and stray current.
AC Stray Current
Hydrate formation is a well-known risk in subsea pipelines and several solutions are available to solve this problem. Hydrates can be prevented by using Subsea pipeline electrical heating technology. Direct electrical heating (DEH) controls the temperature on the pipeline and is expected to be an efficient and convenient way to deal with wax plug in the subsea pipeline.
At the far-end cable connection point of the DEH system, the cable current enters the steel pipe, while part of the current (around 20-40 %) leaves the pipe and is transferred to the sea through the anodes. The electrical current in the sea water enters the pipe again at the near-end connection point. Sacrificial anodes shall prevent AC corrosion in the current transfer zone (CTZ) in addition to provide adequate CP system for the subsea pipeline, the anodes act as effective grounding for the pipeline.
The use of this system is associated with drawbacks such as higher consumption of the sacrificial anodes of the CP system and the possible risk of AC corrosion of surrounding sacrificial anodes and the pipeline itself at coating defects [1].
Williams [2] reported a considerable increase in corrosion of Al conductors in water when an alternating current was applied, the extent of which was dependent on time and applied AC level. Corrosion occurred mainly during the initial test period and the corrosion rate increased with applied AC in the test range of 50 A/m2 to 2000 A/m2.
In addition, Forthun [3] focused to study further the effect of AC on corrosion of Al-Zn-In anodes, both in the presence and absence of connection to steel. In this regard, different test configurations were employed, i.e., a pair of coupled anodes (A/A experiments) and steel coupled to anode, which in turn was coupled to another identical pair of parallel-coupled anode and steel sample (SA/AS experiments).
In both cases, a constant AC density was applied and experiments are designated by the current density level that was applied (relative the area of one anode sample, and assuming the overall current was transferred only between anode samples).
Figure 1 demonstrated that there is a noticeable rise in anode corrosion rates as the applied AC level increases in both A/A and SA/AS tests. This trend continues until the applied AC level reaches iac 80-90 A/m2, after which the corrosion rates start decreasing with any additional increase in the applied AC level.
Observations from high AC level testing showed that the test solution experienced heat generation and increased thickness due to the creation of extreme quantities of corrosion product. Replicates were conducted at a current density of 10 A/m2. In the SA/AS experiments at this AC level, only one of the anodes exhibited corrosion. The extent of corrosion seen was similar to the combined corrosion rate of both anodes in the A/A experiments.
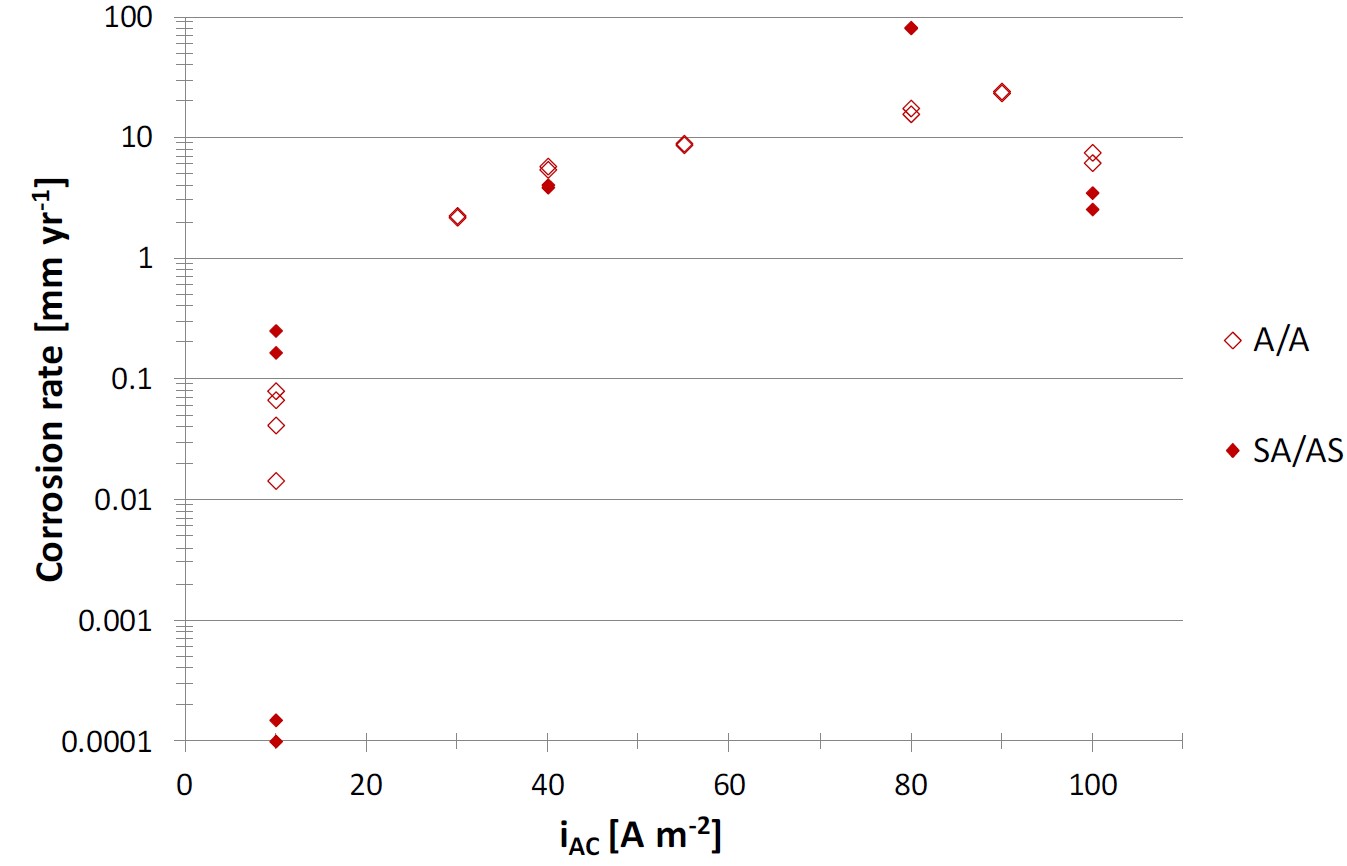
Figure 2 explained that when comparing tests conducted at the same alternating current (AC) level, there were no discernible variations between the anodes from the A/A and SA/AS experiments. In other words, the anodes’ appearance was not significantly impacted by their connection to steel. The corroded surfaces exhibited an irregularly dispersed form of deterioration. The formation of pits expanded in both extent and size, and further merged together as the level of AC increased correspondingly.
The study, reported in [3] clarified that the application of AC did not significantly affect the resulting anode efficiencies (standalone Al alloy) when low AC voltage was applied, however it was observed that at 2 V AC and higher, the anode capacity (and resulting current efficiency) was lower than the acceptance criteria set by DNV-B-401 [4] for testing the anode capacity of Al-based anodes (i.e., 2500 Ah/kg).
In addition, Thorsteinsen [5] investigated the behavior of Al-Zn-In sacrificial anode material in the presence of AC. The anode capacity can be determined from his findings. The anode capacities are significantly lower than the theoretical capacity, as illustrated in Figure-3 [6]. The anode current capacity is consistently less than 1000 Ah/kg, regardless of the varying AC current densities. These tests suggest that the introduction of AC results in a decrease in anode capacity.
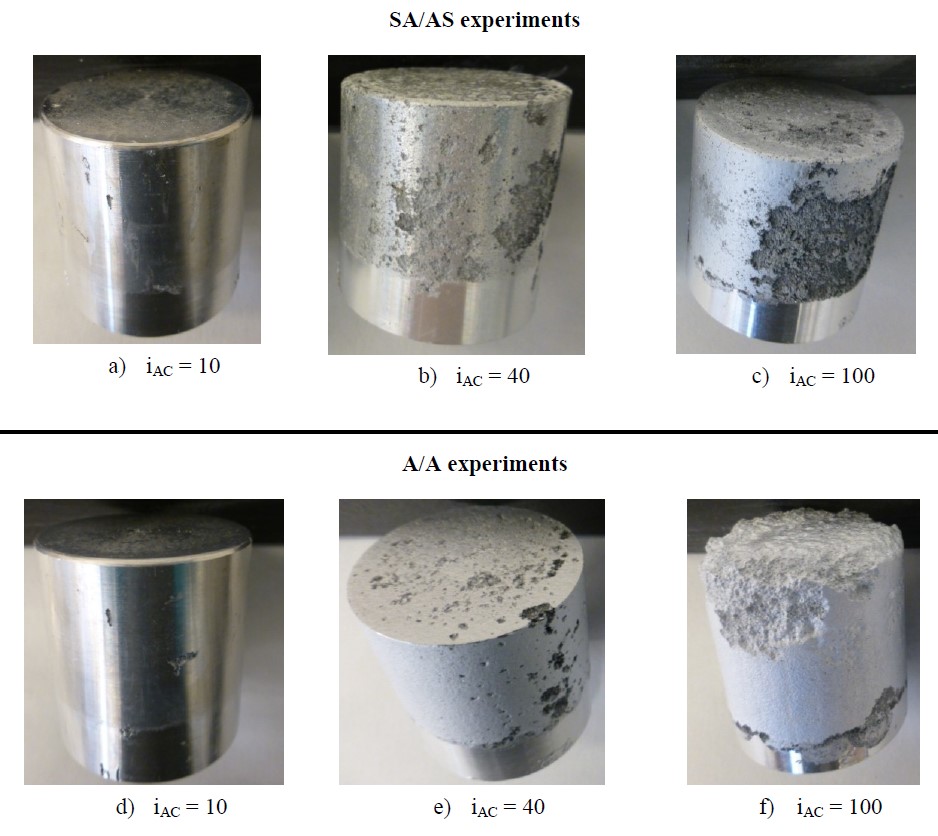
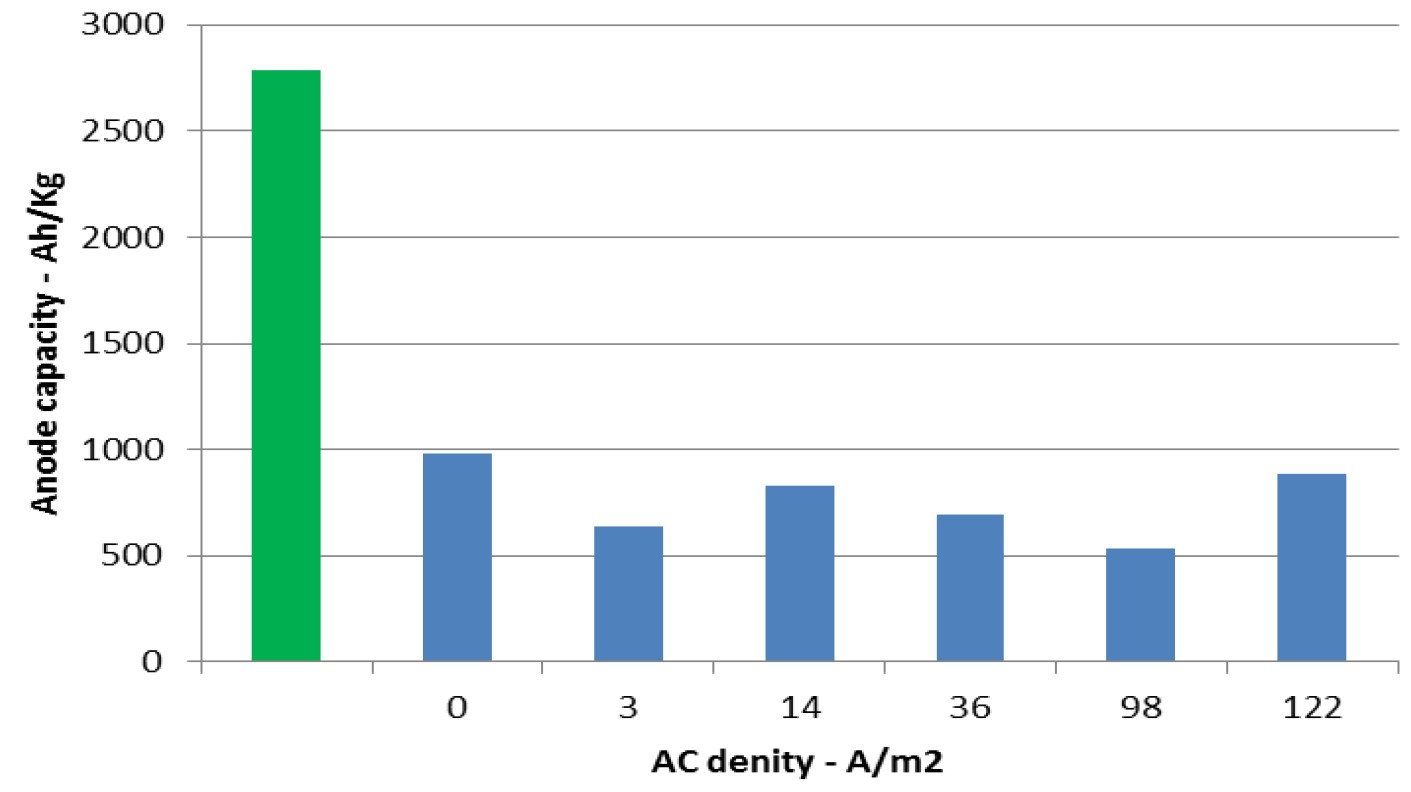
The author [1] conducts a thorough case study to assess the impact of DEH on the CP system of an 11.5km subsea pipeline.
The study highlights the necessary number of Al-Zn-In bracelet anodes needed to achieve the optimal level of protection in both the CTZ and the total length of the pipeline. This determination is based on the actual anode current capacity and corrosion rate, as demonstrated earlier. The conventional CP system only needed 40 anodes.
However, in the case of both CP and DEH systems under worst-case conditions, up to 324 anodes were required (eight times the number of anodes needed in the conventional case). The results indicate that the DEH system significantly impacts both the CP design and the performance of the Al sacrificial anodes.
Mg Anode Effectiveness
Inductive AC interference on new and existing pipeline systems from crossing or parallelisms with overhead power lines is a serious concern [7]. Meanwhile, Mg anode is widely used to protect steel because it is more electronegative than it and hence it is capable to supply electrons to the more electropositive steel, providing CP of this metal surface. The effect of AC on the performance of Mg sacrificial anode, i.e., the DC potential, the output CP current as well as the corrosion rate by AC interference experiment shall be evaluated.
Currently, it is unequivocal that AC significantly influences the electrochemical performance of Mg sacrificial anodes. Pookote [8] indicated that AC may lead to the potential shift of Mg sacrificial anode and expedite its decomposition. Freiman [9] examined the impact of AC current on the efficacy of Mg anode associated with onshore pipelines.
Experimental results indicated that both the DC potentials of Mg and the pipeline exhibited a positive shift under AC. At the same time, the current efficiency of Mg sacrificial anode was decreased significantly. Furthermore, Bruchner [10] discovered that the polarity of the pipeline-Mg sacrificial anode CP system may be altered under AC. When the applied AC current density reached 39 A/m², the Mg anode became the cathode, while the shielded pipeline became the anode.
Ding [11] performed an extensive study on the impact of AC voltages of 0V, 1V, 3V, and 5V on Mg sacrificial anodes. The electrochemical properties of the examined anode were analyzed by open circuit potential (OCP) analysis, electrochemical impedance spectroscopy (EIS), and polarization curve measurements.
The sacrificial anode specimens utilized in this study were Mg alloy rods that were welded with wires and encased in electrical tubes. The test solution was extracted from the soil along the apron, with the following chemical concentrations: Na2CO3 0.1599 g/L, NaCl 0.5124 g/L, Na2SO4 0.1712 g/L, and NaHCO3 0.0864 g/L.
The OCP of the sacrificial anode under different AC voltages was examined over a period of eight days, as depicted in Figure-4. The OCP of Mg anode experiences a sudden negative shift during the initial experimental phase in case of AC voltage, with the most significant potential offset occurring under an AC interference value of 5V, while NO potential offset is observed in the absence of AC interference.
Subsequently, the corrosion potential begins to exhibit a positive change across all experimental circumstances. The activity on the sacrificial anode surface diminished over time, regardless of AC interference. The OCP exhibited greatest positive migration under 5V AC interference and minimum migration under 0V voltage.
Furthermore, to examine the sacrificial anodic corrosion process and assess the variation in corrosion product film resistance (RC) under varying AC interference voltages. Figure 5 illustrated the variation of RC under various AC interference voltages based on EIS analysis. During the experiment, corrosion products build on the surface of the sacrificial anode, increasing the resistance of the corrosion reaction. In the absence of AC interference and with 1V AC interference, the rate of increase of RC diminishes throughout the experiment.
The rate of RC initially slows and subsequently accelerates during the experiment when the AC interference voltages are 3V and 5V. The increased AC stray current alters the corrosion condition of the Mg sacrificial anode surface. The value of RC progressively grew over the duration of the trial. The greater the AC voltage, the more significant the change in resistance.
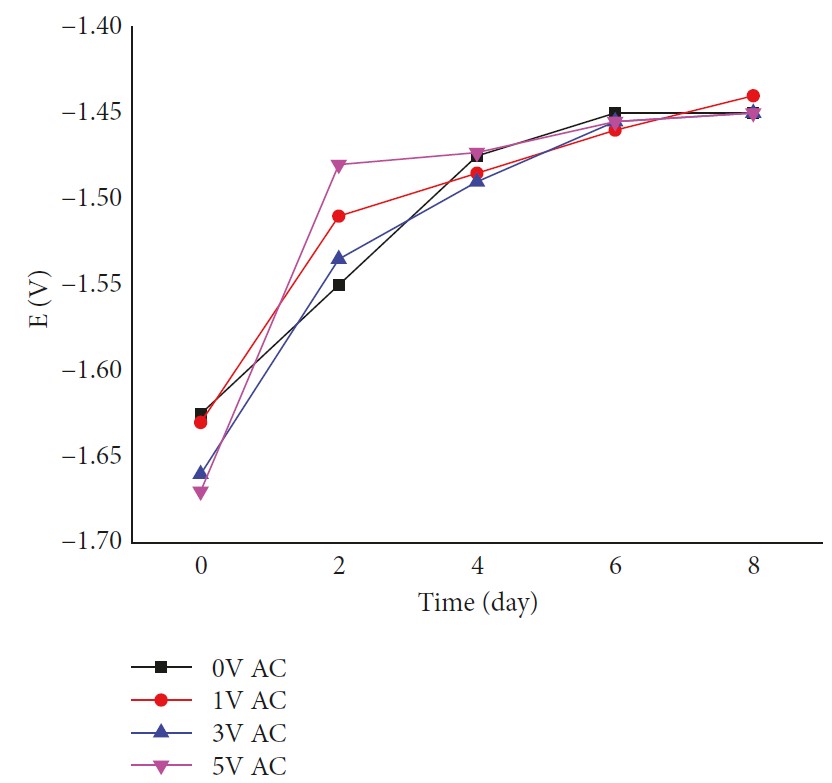
The polarization resistance progressively increased as the corrosion current diminished throughout the experiment. The corrosion tendency and rate of the sacrificial anode decreased with the extension of the experimental duration. In comparison to the polarization resistance and corrosion current measured at the same experimental duration, it is evident that the polarization resistance was diminished under AC interference, while the corrosion current was elevated relative to conditions without AC interference.
It proof that AC interference voltage will diminish the corrosion propensity of the sacrificial anode while accelerating the dissolution rate of Mg anodic. The greater the AC interference voltage, the more pronounced the promotional impact. Furthermore, the control of the sacrificial anode can be discerned from the slope trends of the cathode and anode polarization curves. Following a designated experimental duration, the slope of the anodic polarization curve increasingly surpassed that of the cathodic polarization curve due to the AC stray current enhancing the transmission and diffusion of oxygen.
Consequently, the corrosion rate under AC interference exceeds that without AC interference; moreover, a higher AC interference voltage correlates with an accelerated corrosion rate.
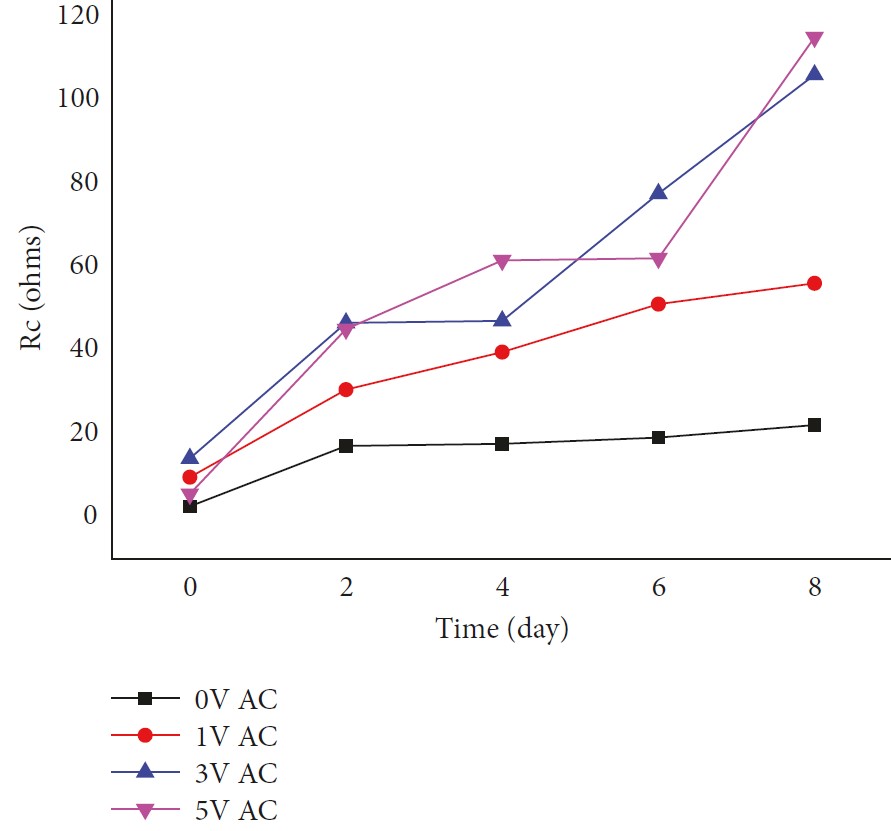
Tang [12] focused to study further the effect of AC on the performance of Mg sacrificial anode used to provide CP for buried pipeline, i.e., the DC potential, the output CP current as well as the corrosion rate combined with electrochemical measurements by AC interference experiment. Mg and steel were employed in this work with a simulated backfill solution of 4 g/L Na2SO4 was adopted as the aggressive solution, which was made from analytic grade reagents and deionized water.
The experimental setup was adopted to conduct the AC interference experiment of steel – Mg sacrificial anode CP system under AC of 100 and 300 A/m2 for various times.
After 96 hours of exposure in the simulated backfill solution, the corrosion rates of Mg and carbon steel were measured by weight-loss measurements and plotted against AC current density (iac). The results are shown in Table-1. It was observed that as iac increased, the corrosion rates of both Mg and carbon steel also increased.
When AC was not present, the corrosion rate of Mg was 6.88 mm/yr. Applying AC to the system, the corrosion rate was accelerated dramatically to 34.9 mm/yr at applied AC current density 300 A/m2. Moreover, it was concluded that Mg sacrificial anode could not provide enough protection under AC interference of 50 A/m2 (or larger).
Reference
- Ahmed Mahgoub. “Direct electrical heating impaction for subsea pipeline integrity,” Materials Performance Magazine. Vol. 60, No. 4, (2021), pp. 28-31.
- J.F. Williams, Alternating Current and Aluminum. Materials Protection, 1967: p. 50-52.
- Kari Forthun. “Alternating current corrosion of aluminum sacrificial anodes,” NTNU, Master Degree, 2013.
- DNV-RP-B401. “Cathodic Protection design,” 2021.
- Andreas Thorsteinsen. “Alternating current corrosion of cathodically protected steel in marine environment,” NTNU, Master Degree, 2012.
- Hesjevik & Olsen. “Cathodic protection design of submarine pipelines with direct electric heating,” Corrosion 2013, NACE, Paper No. 2443.
- Ahmed Mahgoub. “Mitigation of AC Induced Voltages on Buried Pipelines Influenced by E.H.V Power Lines. A Journal of Institute of Corrosion,” Corrosion Management, Issue 165, January/February 2022.
- S.R. Pookote, D.T. Chin. “Effect of alternating current on the underground corrosion of steels,” Mater. Perform. 17 (1978) 9–15.
- L.I. Freiman, M. Yunovich. “Special behavior of steel cathode in soil and protection assessment of underground pipe with a buried coupon,” Prot.Met. 27 (1991) 437–447.
- W.H. Bruchner, Soil corrosion of steel by AC, Mater. Protec. 4 (1965).
- Q. Ding, I. Chu, T. Shen. “Study on the Electrochemical Performance of Sacrificial Anode Interfered by Alternating Current Voltage,” International Journal of Corrosion Volume 2018.
- D. Tang, Y. Du, X. Li, Y. Liang, and M. Lu, “Effect of alternating current on the performance of magnesium sacrificial anode,” Materials and Corrosion, vol. 93, pp. 133–145, 2016.
- Lindemuth, H. Hernandez. “AC Mitigation and Cathodic Protection for a Long Regulated Pipeline,” CORROSION 2010, paper no. 105 (Houston, TX: NACE, 2010).
- Y. Du, and D. Tang. “Investigation on corrosion of zinc ribbon under alternating current,” Corrosion Engineering Science and Technology, vol. 50, 2015.
- M. Lu, and Y. Du. “Electrochemical Studies on the Performance of Zinc Used for Alternating Current Mitigation,” Corrosion, Vol. 71, No. 6, 2015.
Part 2: Cathodic Protection
Exploring Sacrificial Anode Performance in Presence of AC Source
By Ahmed Mahgoub, CSD, Saudi Aramco
Editor’s Note: This is the second of two parts of an article that focuses on cathodic protection and anode performance. Part 1 was published in the April edition of P&GJ.
(P&GJ) — The polarization curves of Mg and carbon steel in the absence of AC to understand the impact of AC on the CP parameters of the carbon steel-Mg sacrificial anode CP system was investigated. Two distinct areas, designated as the “anodic A” and “anodic B” regions seen on the Mg anodic polarization curve. In comparison to the anodic (A) region, the slope of the anodic (B) region was substantially steeper.
After being subjected to AC at 100 and 300 A/m2 for different durations, the polarization curve of Mg varied as a function of interference duration. Slopes for the cathodic Tafel, anodic (A), and anodic (B) regions were displayed in Table 2.
Table 2: Anodic B region slope (kB-Mg), anodic A region slope (kA-Mg), cathodic Tafel slope (kc-Mg) [12].
iac (A/m2) |
Time (hrs) |
kB-Mg |
kA-Mg |
kc-Mg |
100 |
3 |
4.59 |
0.14 |
0.36 |
24 |
1.28 |
0.25 |
0.40 |
|
72 |
2.2 |
0.23 |
0.35 |
|
300 |
3 |
14.06 |
0.92 |
0.44 |
24 |
5.88 |
0.99 |
0.39 |
|
72 |
7.73 |
0.98 |
0.48 |
The range of oscillation for the Mg real-time potential was narrow, spanning only the anodic B and A regions, when the applied AC current density was relatively low, at 50 A/m2. A positive change in Mg time-average occurred because the positive change in Mg real-time potential in the anodic AC cycle was substantially greater than the negative change in the cathodic cycle.
Compared to carbon steel, this positive offset of Mg DC potential was substantially larger. Consequently, there was a smaller DC potential difference between Mg and carbon steel.
Anodic (B) region and cathodic Tafel region fluctuations in Mg real-time potential were produced by the applied AC current density, which was considerably large at 100 A/m2. Of Mg, the time-average potential changed for the better.
Compared to carbon steel, Mg’s positive DC potential offset was substantially larger. Consequently, Mg has a positive DC potential compared to carbon steel. Therefore, the potential difference became negative, meaning that carbon steel served as the anode and Mg as the cathode. Mg experienced a flip of polarity. Consequently, Mg went through anodic depolarization, which caused DC potential alterations in the negative direction.
Anodic depolarization produced a smaller positive offset than AC oscillation, which led to the conclusion that the former was more significant. AC oscillation predominated over the DC potential shift of Mg when subjected to AC.
Furthermore, it can be inferred that the direct current potentials of Mg and carbon steel exhibited a positive shift with the augmentation of alternating current density, leading to a negative increase in the potential difference. The negative value of potential difference signifies that polarity reversal happened in Mg.
Consequently, the elevated AC current density facilitated the polarity reversal of Mg when iac ≥ 100 A/m². Consequently, it was observed that the direct current potentials of Mg and carbon steel exhibited a positive change immediately upon the application of alternating current to the system. The disparity in polarity between Mg and carbon steel led to a distinct DC potential offset for each, which in turn caused a change in their DC potential differential and thus affecting the direction and magnitude of the CP current. Additionally, the DC potential shifts of Mg and carbon steel were influenced by the changing CP current.
Zn Ribbon Anode
AC voltages are conveyed to the pipeline by conductive or inductive interference. Magnetic induction occurs along the pipeline or pipeline segment that is nearly parallel to the power line, potentially generating significant pipeline potentials even at considerable separation distances. Progress in interference management has led to the gradient control wire technique.
This approach involves one or more exposed Zn conductors buried parallel to and in proximity to the pipeline, which are periodically linked to it. The Zn ribbon anode employed in this interference control is highly effective in eliminating excessive pipeline potentials caused by both inductive and conductive interference. Zn ribbon can be electrically connected to pipeline directly or through a direct current DC decoupler [13].
Tang, Minxu and Yanxia [14&15] investigated the effects of AC on the galvanic coupling Zn /pipeline steel in 4g/L Na2SO4 simulated backfill solution by weight-loss measurements, electrochemical measurements, and surface examinations with two scenarios, i.e., with or without dc decoupler, were considered.
In Scenario 1, the DC decoupler was put in place and the DC potential of Zn was measured under a variety of alternating currents. The results of these measurements are presented in Figure-6. DC potential of -1.06 V was present in Zn before the application of AC. A negative shift occurred in the direct current potential when alternating current was applied to the system.
The AC density was 50 A/m2, and the voltage was -1.14 V. The direct current potential dropped to -1.16 V when the AC current density reached 100 A/m2. The DC potential of Zn reached -1.19 and -1.21 V, respectively, as the density of the AC current increased to 200 and 300 A/m2. The DC potential of Zn will then shift in a positive direction to a steady state value after that.

Figure 6: Records on DC potential of Zn anode under various AC [14].
In both cases, the corrosion rate was measured by weight loss experiments on Zn following exposure to different conditions for 7 days as depicted in Figure 7. The fact that AC greatly accelerated up Zn corrosion is self-evident. In the first scenario, in the absence of AC, the Zn corrosion rate was 0.14 mm/yr.
The corrosion rate climbed to 0.73 mm/yr, which is four times higher than the rate without AC, when the applied AC density reached 100 A/m2. When the ac density was 300 A/m2, it reached 0.83 mm/yr.
Furthermore, it is essential to point out that the rate of Zn corrosion in Scenario 2 was significantly higher than the rate of Zn corrosion in scenario-1 under varied AC conditions. The rate of corrosion in scenario-2 was 0.77 mm/yr when there no AC was applied, which was five times higher than the rate in Scenario 1.
Under the conditions of an AC density of 50 A/m2, the rate of corrosion in Scenario 2 climbed to 1.95 mm/yr, which was much higher than the rate in Scenario 1, which was 0.58 mm/yr. The corrosion rate in Scenario 2 was 4.05 mm/yr due to an AC density of 200 A/m2, but the corrosion rate in Scenario 1 was much lower, coming in at 0.80 mm/yr.
At the point where the applied AC density reached 300 A/m2, the rate of corrosion in Scenario 2 was six times higher than the rate in Scenario1.

Figure 7: Corrosion rate determined by weight loss tests of Zn after being exposed to various AC for 7 days in both scenarios [14].
Within the context of scenario-1, additional research was conducted to investigate the rate of corrosion and the weight loss of the Zn ribbon anode. It was discovered in Figure-8 that the free-corrosion rate without AC was 0.15 mm/yr. As soon as AC was applied, the rate of corrosion increased. The corrosion rate was 0.44 mm/yr when the AC current density was 20 A/m2, but it reached 0.58 mm/yr when the current density was 50 A/m2 and 0.73 mm/yr when the current density was 100 A/m2.
The corrosion rate reached 0.8 mm/y for 200 A/m2 and 0.83 mm/yr for 300 A/m2, respectively. One possible equation that may be used to explain the link between the rate of corrosion and the AC current density is as follows [15]:
Where,
Vcorr: is the corrosion rate of Zn, mm/yr.
Iac: is the RMS value of AC current density, A/m2.
a = -0.65.
b = 43.48.
and c = 0.81.

Figure 8. Corrosion rate obtained by weight loss tests of Zn subjected to various AC current densities [15].
The results of the weight loss tests demonstrated that the rate of corrosion of Zn under AC conditions of 100 A/m2 in scenario-1 was comparable to that of the Zn sacrificial anode, which had a current density of 0.46 A/m2 in the CP configuration.
During the course of the work, AC current efficiency (CE%) was researched in order to further investigate the reason and provide a realistic reference for the service life of the design of Zn ribbon. CE% was defined as the ratio of weight loss caused by AC to weight loss caused by an equivalent level of DC. Figure-9 illustrated the percentage of AC current efficiency that occurs during the Zn corrosion process.
Under the case that no AC was being applied, it was clear that the CE% was approximately 1.7%. In addition, the drop in CE% was a direct result of the rise in the density of AC current. Approximately 1.63% of the CE was present when the applied AC current density was 20 A/m2.
The percentage of CE decreased to 0.87% when the AC current density was 50 A/m2. The percentage of CE decreased even further, going from 0.54% to 0.21% for 100 A/m2, 200 A/m2, and 300 A/m2.

Figure 9: AC Current efficiency (CE%) of Zn at various AC current densities [15].
The author presents the results of a further investigation, which are presented in Table 2. This table illustrates the estimated rate of AC corrosion of Zn ribbon anode under a wide range of AC current density, the equivalent DC current density (defined as the DC current density will cause the same rate of corrosion caused by the corresponding AC current density), the percentage of the DC current density to the AC current density, and finally the estimated annual weight loss per unit surface area.
The corrosion rate is 0.175mm/yr when the AC current density is 1A/m2, but it reached 0.217mm/yr when the current density is 4A/m2 and 0.294mm/yr when the current density is 10A/m2. At an AC current density of 50A/m2, it increased to 0.60mm/yr which is approximately three times higher than the rate without AC.
The corrosion rate climbed to 0.74mm/yr, which is approximately four times higher than the rate without AC, when the applied AC current density reached 100A/m2. At AC density 200A/m2 and above; the variance of the estimated corrosion rate is minimized and could be considered that the maximum corrosion rate of Zn ribbon anode is approximately 0.81mm/yr regardless the value of AC current density.
The results of the estimated corrosion rate demonstrated that the rate of corrosion of Zn under AC conditions of 1A/m2 is comparable to that of the Zn sacrificial anode, which had a current density of 0.117 A/m2 in the CP configuration with a ration of DC to AC current density is 11.7%. In addition, the drop in ratio of DC to AC current density is a direct result of the rise in the density of AC current.
Approximately 6.34% of the ratio of DC to AC current density is present when the applied AC current density is 2A/m2. The ratio is decreased to 3.09% when the AC current density is 5A/m2. The ratio is decreased even further, going from 1.97% to 0.81% for 10A/m2 and 50A/m2.
The predicted annual weight loss per unit surface area is a significant aspect that should be taken into consideration. In situations where the current density is 1A/m2, the value is 1.25kg, whereas in situations where the current density is 15A/m2, the value is 2.5kg. When compared to the weight loss that would occur in the event of a current density of 1A/m2, this is nearly twice as much.
Compared to the weight loss that is linked with a current density of 1A/m2, the weight loss that occurs when the AC current density is 100A/m2 is nearly four times more. To be more specific, it climbed to 5.3kg at this current density.
Table 3: Estimated AC corrosion rate, DC to AC current density ratio and annual weight loss per unit surface area.
AC current density (A/m2) |
Corrosion rate in (mm/Yr) |
Equivalent DC current density (A/m2) |
Equivalent DC to AC current density ratio (%) |
Weight loss in (Kg/m2/Yr) |
0.1 |
0.160 |
0.108 |
108 |
1.156 |
1 |
0.175 |
0.117 |
11.71 |
1.251 |
2 |
0.189 |
0.127 |
6.34 |
1.354 |
3 |
0.203 |
0.136 |
4.54 |
1.455 |
4 |
0.217 |
0.146 |
3.64 |
1.554 |
5 |
0.231 |
0.155 |
3.09 |
1.651 |
6 |
0.244 |
0.163 |
2.72 |
1.745 |
7 |
0.257 |
0.172 |
2.46 |
1.837 |
8 |
0.269 |
0.180 |
2.26 |
1.927 |
9 |
0.282 |
0.189 |
2.10 |
2.015 |
10 |
0.294 |
0.197 |
1.97 |
2.101 |
15 |
0.350 |
0.234 |
1.56 |
2.503 |
20 |
0.400 |
0.268 |
1.34 |
2.860 |
50 |
0.604 |
0.405 |
0.81 |
4.324 |
100 |
0.745 |
0.499 |
0.50 |
5.331 |
200 |
0.803 |
0.539 |
0.27 |
5.751 |
250 |
0.808 |
0.541 |
0.22 |
5.783 |
AC current density (A/m2) |
Corrosion rate in (mm/Yr) |
Equivalent DC current density (A/m2) |
Equivalent DC to AC current density ratio (%) |
Weight loss in (Kg/m2/Yr) |
0.1 |
0.160 |
0.108 |
108 |
1.156 |
1 |
0.175 |
0.117 |
11.71 |
1.251 |
2 |
0.189 |
0.127 |
6.34 |
1.354 |
3 |
0.203 |
0.136 |
4.54 |
1.455 |
4 |
0.217 |
0.146 |
3.64 |
1.554 |
5 |
0.231 |
0.155 |
3.09 |
1.651 |
6 |
0.244 |
0.163 |
2.72 |
1.745 |
7 |
0.257 |
0.172 |
2.46 |
1.837 |
8 |
0.269 |
0.180 |
2.26 |
1.927 |
9 |
0.282 |
0.189 |
2.10 |
2.015 |
10 |
0.294 |
0.197 |
1.97 |
2.101 |
15 |
0.350 |
0.234 |
1.56 |
2.503 |
20 |
0.400 |
0.268 |
1.34 |
2.860 |
50 |
0.604 |
0.405 |
0.81 |
4.324 |
100 |
0.745 |
0.499 |
0.50 |
5.331 |
200 |
0.803 |
0.539 |
0.27 |
5.751 |
250 |
0.808 |
0.541 |
0.22 |
5.783 |
Conclusions
The effect of DEH on the Al anode performance should be given higher attention as a significant influence was illustrated for the corrosion behavior of sacrificial Al anodes under application of AC. Corrosion of the anodes, resulting from current provided for the protection of the steel and self-corrosion, occurred at an increasing rate with applied AC level.
The experimental study [3] has demonstrated that steel does not receive adequate protection from sacrificial anodes when AC is applied. This demonstrates that there is a drop in the efficiency of the anode when AC current is present.
Furthermore, the author [1] described the impacts of the DEH system on the performance of the Al anodes; this is evidence that the effects of the CP anodes on the DEH system and vice versa should be taken into consideration.
There is no doubt that the performance of the Mg anode is affected when AC power is present. If there was AC interference present, the DC potential of the Mg anode would move in a positive direction. In addition to this, the rate of corrosion of the Mg anode is increasing at a quicker and faster pace as the AC interference voltage increases.
The accumulation of corrosion products on the surface of the Mg anode has an effect on the amount of electric charge that is released. It was an indication that the cathode control was gradually transitioning into the anode control structure. It demonstrated that AC voltage played a significant part in the anodic polarization of the Mg anode [11&12].
The reported works [13,14&15] carried out to investigate the effect of AC on corrosion of Zn ribbon anode came to the conclusion that AC current significantly accelerated the corrosion of Zn in the scenarios with or without dc decoupler.
In both cases, the charge transfer resistance of Zn was significantly reduced as a result of alternating current, which would result in a significant rise in the rate of corrosion. This is despite the fact that the effects of AC on electrochemical corrosion of Zn ribbon anode are still not fully understood. It was demonstrated that the corrosion product film that was developed on the Zn surface first increased as a consequence of the effects of AC current, and then progressively disappeared as a result of AC oscillation.
An estimate was made for the ratio of the weight loss induced by AC current to that caused by a comparable steady-state direct current density. This ratio is referred to as the AC current efficiency. When the applied AC current density was 20 A/m2, the results showed that the efficiency of the AC current was no more than 1.6%, and it decreased as the AC current density increased beyond that point.
A common problem that arises when subterranean pipelines are erected in the same corridor or in close proximity to energized high voltage transmission line is the occurrence of induced AC voltage. Two distinct processes are responsible for the generation of AC power on a pipeline.
The electromagnetic field that is produced by high voltage transmission line is the source of inductive coupling, which is an indirect electrical connection that results in voltages being induced on the pipeline. Conductive coupling, on the other hand, is a direct resistive coupling that occurs between a power system and the pipeline. In most cases, this would include a link between a power line and the ground, which results in ground fault currents, or a lightning strike that travels through the earth to reach the pipeline.
In situations where the inductive (steady state) coupling is the only thing that needs to be considered, the safety of the workers should be the first priority. In order to accomplish this, the operator of the pipeline is required to supply a dedicated ground that has a low resistance to earth.
This ground is necessary in order to guarantee that the induced AC voltages are brought down to safe values. By installing a Zn ribbon anode in parallel and connecting it to the victim pipeline through DC decoupler that allows AC to pass through while providing DC isolation, this strategy has the potential to be a successful mitigation technique for a wide variety of interference situations.
To mitigate the steady-state induced voltage, standard industrial practice involves the installation of one or more zinc ribbon anodes (grounding system) in parallel throughout the full length of the affected pipeline. The efficacy of the grounding mitigation approach is assessed by its ability to diminish the induced voltage to acceptable criteria.
Nonetheless, only one Zn ribbon anode may yield an exceedingly low grounding resistance compared to the resistance necessary to achieve the mitigation criteria [7].
The optimal design approach for mitigating AC steady state induced voltage necessitates determining the ideal grounding resistance and accounting for the AC corrosion of the Zn ribbon anode [13,14&15] to accurately estimate the necessary length and weight of the Zn anode, rather than indiscriminately employing a ribbon anode along the entire pipeline length.
Reference
- Ahmed Mahgoub. “Direct electrical heating impaction for subsea pipeline integrity,” Materials Performance Magazine. Vol. 60, No. 4, (2021), pp. 28-31.
- J.F. Williams, Alternating Current and Aluminum. Materials Protection, 1967: p. 50-52.
- Kari Forthun. “Alternating current corrosion of aluminum sacrificial anodes,” NTNU, Master Degree, 2013.
- DNV-RP-B401. “Cathodic Protection design,” 2021.
- Andreas Thorsteinsen. “Alternating current corrosion of cathodically protected steel in marine environment,” NTNU, Master Degree, 2012.
- Hesjevik & Olsen. “Cathodic protection design of submarine pipelines with direct electric heating,” Corrosion 2013, NACE, Paper No. 2443.
- Ahmed Mahgoub. “Mitigation of AC Induced Voltages on Buried Pipelines Influenced by E.H.V Power Lines. A Journal of Institute of Corrosion,” Corrosion Management, Issue 165, January/February 2022.
- S.R. Pookote, D.T. Chin. “Effect of alternating current on the underground corrosion of steels,” Mater. Perform. 17 (1978) 9–15.
- L.I. Freiman, M. Yunovich. “Special behavior of steel cathode in soil and protection assessment of underground pipe with a buried coupon,” Prot.Met. 27 (1991) 437–447.
- W.H. Bruchner, Soil corrosion of steel by AC, Mater. Protec. 4 (1965).
- Q. Ding, I. Chu, T. Shen. “Study on the Electrochemical Performance of Sacrificial Anode Interfered by Alternating Current Voltage,” International Journal of Corrosion Volume 2018.
- D. Tang, Y. Du, X. Li, Y. Liang, and M. Lu, “Effect of alternating current on the performance of magnesium sacrificial anode,” Materials and Corrosion, vol. 93, pp. 133–145, 2016.
- Lindemuth, H. Hernandez. “AC Mitigation and Cathodic Protection for a Long Regulated Pipeline,” CORROSION 2010, paper no. 105 (Houston, TX: NACE, 2010).
- Y. Du, and D. Tang. “Investigation on corrosion of zinc ribbon under alternating current,” Corrosion Engineering Science and Technology, vol. 50, 2015.
- M. Lu, and Y. Du. “Electrochemical Studies on the Performance of Zinc Used for Alternating Current Mitigation,” Corrosion, Vol. 71, No. 6, 2015.
Author: Ahmed Mahgoub is cathodic protection subject matter expert for Saudi Arabian Oil Company (Saudi Aramco) in Dhahran, Saudi Arabia. He has more than 18 years of experience in the consulting, engineering, constructing and commissioning of different cathodic protection structures. He is a NACE/ AMPP CP Specialist, Icorr CP specialist, and NACE/AMPP senior corrosion technologist.
Comments