SwRI Patents New Pipeline Inspection Technology

The Southwest Research Institute (SwRI) has patented a new technology to inspect coatings of pipelines installed through horizontal directional drilling.
The technology can determine both the extent and the configuration of any damage to the coating that occurs during HDD installation,” said Dr. Pavan Shukla, one of the two SwRI engineers who invented the technology. “Our system provides a significant improvement over existing technologies that are only capable of estimating the extent of coating damage but do not provide information about the configuration of that damage.”
Traditionally, workers install pipelines in open trenches, a method that disturbs roads, sidewalks, and environmentally sensitive areas. With this installation method, coating damage is more easily detected using various conventional techniques from the surface above the pipeline.
HDD is used for pipelines that run under surface features, such as rivers, roadways, and railways, where trenching is not desirable or practical. Special methods and devices to detect coating damage and corrosion of HDD-installed pipelines are necessary because access to the surface above the pipeline is limited. Additionally, the HDD installation itself tends to damage coatings as pipeline segments are pulled through a borehole and contact soil, rock and other debris. The SwRI-patented technology can determine damage to the coating along both the length and around the circumference of the pipeline. Additional field testing is needed before the technology can be licensed for commercial use.
SwRI’s “Detection of Coating Defects on Buried Pipelines Using Magnetic Field Variations within the Pipeline” (Patent No. 9,638,667) technology inspects pipeline segments for coating damage immediately after HDD installation. With this technology, engineers place a magnetic field sensor array within the pipeline. The sensor array generally matches the interior profile of the pipeline but is smaller. As the array moves along the pipeline, engineers analyze the output from each sensor to determine location, configuration, and the extent of coating damage.
“It is important to determine the condition of the coating on the pipeline segment immediately after installation,” said Dr. Jay Fisher, the co-inventor of the technology. “Understanding the extent of any damage to the coating will help determine if it is too severe to be protected by a cathodic protection system, which inhibits the oxidation process and prevents corrosion, or whether it can be repaired or needs to be replaced before it is placed into service.”
Related News
Related News
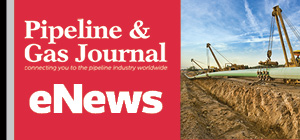
- Kinder Morgan Proposes 290-Mile Gas Pipeline Expansion Spanning Three States
- Valero Plans to Shut California Refinery, Takes $1.1 Billion Hit
- Three Killed, Two Injured in Accident at LNG Construction Site in Texas
- Tallgrass to Build New Permian-to-Rockies Pipeline, Targets 2028 Startup with 2.4 Bcf Capacity
- TC Energy Approves $900 Million Northwoods Pipeline Expansion for U.S. Midwest
- U.S. Pipeline Expansion to Add 99 Bcf/d, Mostly for LNG Export, Report Finds
- Enbridge Adds Turboexpanders at Pipeline Sites to Power Data Centers in Canada, Pennsylvania
- Great Basin Gas Expansion Draws Strong Shipper Demand in Northern Nevada
- Cheniere Seeks FERC Approval to Expand Sabine Pass LNG Facility
- Heath Consultants Exits Locate Business to Expand Methane Leak Detection Portfolio
Comments