August 2010 Vol. 237 No. 8
Features
Multi-diameter Inline Tool Inspects The Previously Unpiggable
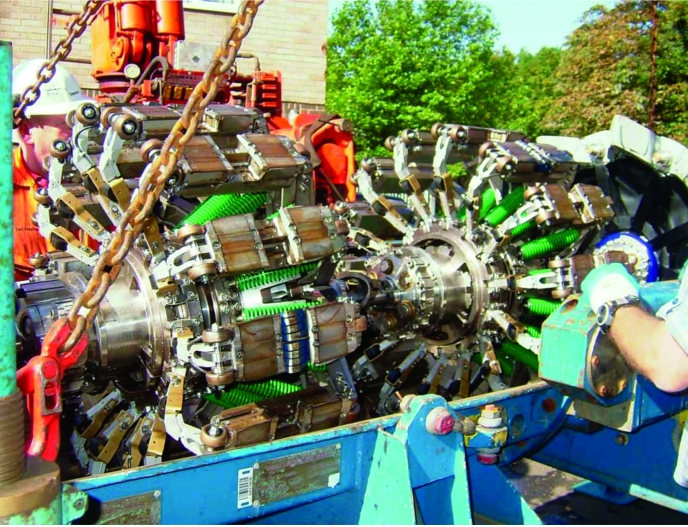
Around the world, almost 30% of oil and gas transmission pipelines are not suitable for inspection using conventional inline inspection (ILI) tools. In fact, many of these lines were built before intelligent pigging had even been invented. The challenges facing “unpiggable” pipelines are often associated with reduced bore valves, miter bends or changes in diameter. PII Pipeline Solutions has identified this as an opportunity to combine its pipeline inspection experience with the requirement of pipeline operating companies to develop technologies to inspect these challenging pipelines.
One example of this cooperation arose in 2007 when El Paso Pipeline Group contracted PII to conduct metal-loss inspections of 13 natural gas pipelines located in the United States.
The segments ranged in length from 30 to 89 miles with at least two diameters in each segment. Many of them contained full-bore tees and 1.5D back-to-back bends. Although the lines had been in service for several decades, none had been inspected previously. El Paso had a requirement to complete inspections mandated under U.S. Department of Transportation regulation CFR 49 Part 192 for High Consequence Areas (HCA) and also for internal requirements.
The project timeline required that GE be capable of designing, building and testing a fully functional, multi-diameter SmartScan tool within eight months. The tool was promised and expected to be on site ready for the first inspection by Nov. 7, 2007.
GE has developed its SmartScan inspection tool using the well-proven MFL (Magnetic Flux Leakage) principle. The tool is configured with extremely short and compact magnetizing modules compared with conventional ILI tools.
Pipeline configuration was among the challenges. Up to this effort, the typical solutions for inspecting a pipeline with diameter changes was to adapt an existing MFL single-diameter tool to inspect the nominal diameter and traverse through the other diameter(s) or break up the segment into multiple segments of single diameter pipeline by adding pig launcher/receiver sets. The limitation of this approach is largely due to the existing MFL technology and magnetizers designed for these tools. If the variation in bore is large, the data collected in the extreme diameters is usually compromised. Ultrasonic wall measurement inline inspection tools have performed better in these situations but costly tool modifications are often required and were not applicable in El Paso’s gas pipeline network.
Although there are several pipeline inspection companies that do have multi-diameter inspection tools, there were no tools on the market that could traverse and inspect these 24-inch through 31-inch pipelines. El Paso required that all diameters be inspected within the segment, preferably, within one run. Some of these pipelines contained full-bore offtakes, 1.5D bends and to further complicate the issue, there were lines with true 31-inch OD.
To satisfy El Paso’s requirements for inspecting all of the proposed pipelines, the tool had to meet the following criteria: (1) complete metal-loss (MFL) inspection; (2) detection specification: 10%wt in general corrosion and 20%wt in pitting corrosion (speed and wall thickness dependent); (3) depth sizing accuracy: 80% ±15%wt; (4) multidiameter inspection capable of 24-inch through 31-inch; (5) full-bore offtake passing; and (6) 1.5D back-to-back bends.
To quote Chris Whitney, Manager of Pipeline Services of El Paso, “We understood this was a significant challenge but previous experience with another size tool boosted our confidence that this endeavor could be successful. We had identified about 30 segments that this tool could be utilized (in) which would be a significant benefit to our inspection program.”
Cleanliness of the lines was another challenge. One of the greatest challenges for inline inspection of an “unpiggable” pipeline is assuring that the line is clean enough to allow the inspection tool to pass undamaged and to collect quality inspection data. Some of these pipelines were built over 40 years ago and there was potential for excessive wear and/or damage to sensors that have to be kept in close contact with the pipe wall to do their job. Early runs with the SmartScan tool did show such damage and the feedback was used by GE to refine the sensor design and improve running life.
It is critical to address the cleaning issue as early as possible in the project. A solution for cleaning the proposed lines had to be devised prior to running the inspection tool in the pipeline. Since most of the El Paso pipelines had been in service for several decades and none had ever been inspected, GE estimated that a significant amount of cleaning would be required to ensure a suitable inspection could take place. In parallel with the design, building and testing of the in-line inspection tool, GE also worked on a cleaning solution to be provided for El Paso, and the agreed methodology, documented by a flow chart, described the recommended step-by-step cleaning process to be executed.
GE recommended that all of the lines be chemically cleaned, followed by running a multi-diameter cleaning pig to determine if the line was clean enough for a SmartScan inspection. Chemical cleaning is known to be one of the best ways of ensuring the cleanliness of a pipeline. To supplement this, a multi-diameter cleaning pig was designed with multi-diameter brushes and strong magnets to remove debris from the pipeline.
Regulatory and internal deadlines loomed. El Paso needed to complete at least two inspections by Dec. 17, 2007 in order to meet internal and DOT requirements. To ensure these goals were met they required that the tool be on site and ready to launch by Nov. 7, 2007. GE agreed to the tight schedule and allocated resources accordingly in order to meet the run date. The following program was devised and managed rigorously keeping in close contact with the client: (1) complete tool design: March 2007; (2) complete tool build: August 2007; (3) complete testing: October 2007; and (4) launch first live tool: Nov. 7, 2007.
Initially, monthly updates were held with the client and as the program neared the run date, the frequency of the updates moved to weekly and then daily.
The design and building of the tool went according to schedule and was completed on time. During the testing phase the major components and the fully assembled tool went through a rigorous evaluation process. Throughout the testing phase, areas of possible improvement were identified and were acted upon as the program progressed.
Pump-through testing answered questions. In order to confirm the passage of the whole tool through specific pipeline features, a mock pipeline was set up and the tool was pumped through it utilizing water as the medium. The features in the line included a selection of obstacles such as offtakes, 1.5D back-to-back bends, minimum ID spools and a section to confirm that the tool would drive in the 31-inch pipe.
Mechanical proving also answered questions. The mechanical proving tests were conducted in the same line layout as per the pump-through testing, with additional obstacle features added, including a valve void of 9.75 inches, 60-degree step of 1-inch and full-bore offtake of 31 inches. The tool was pulled using a winch and each test was conducted at speeds of 1 m/s, 3 m/s and 5 m/s.
A defect database was generated. To develop the defect sizing algorithms, a series of manufactured defects were put into 24-inch, 26-inch, 28-inch, 30-inch, and 31-inch diameter pipes. The tool was then pulled through the pipes at various speeds to determine the effect of velocity on the sizing algorithms. The results from these runs were used to build a statistical sizing model for the tool in the various diameters and wall thicknesses of pipe.
First Inspection Runs
The tested tool was ready for its first inspection run on time on Nov. 7, 2007, the exact date indicated almost a year earlier. The GE crews were able to inspect three pipelines prior to the end of 2007, thereby allowing El Paso to meet DOT inspection requirements for HCA mileage and company goals for total mileage. The tool was the only one on the market capable of traversing and inspecting 24-to-31-inch pipe with full-bore offtakes, and 1.5D back-to-back bends – all in a single run. The inspection reports were delivered on time and data verification was initiated.
Outcome
Key pipeline operators and regulatory authorities acknowledge that partnering between pipeline operators and inspection companies is the most proactive and productive way of developing tools for ensuring the long-term integrity of pipeline systems. This project was a good example of successful partnering for El Paso and GE Oil & Gas.
SmartScan has cleared a path for El Paso’s enhanced safety and asset management plans for these, some of the most challenging of pipelines. The team was pleased with the way the partnership worked, and with the inspection results obtained.
To quote Chris Whitney of El Paso, “We have worked with GE for about six years on this concept of multi-diameter inspection tools and this particular project was very challenging, but the GE team was driven to succeed and ultimately produced a durable and reliable inspection tool for 24-inch to 31-inch pipelines.”
Early in 2008, the tool was returned to Cramlington, UK to modify the metal-loss sensors to improve their robustness and wear characteristics. Since the completion of the sensor modification in the summer of 2008, El Paso and GE have completed 16 additional inspections with the tool in pipelines that would have otherwise been considered “unpiggable.”
Comments