June 2025, Vol. 252, No. 6
Features
What Does API 6DX Mean for the Energy Industry?
By Girish Dalbhanjan, Emerson
(P&GJ) — The American Petroleum Institute (API) has issued many standards covering a broad range of equipment across the oil and gas industry. Recently, API issued the 25th edition of their API 6D standard, which has expanded significantly from earlier editions.
One of the major changes includes a requirement to comply with the design specifications, testing and documentation of valve actuators as outlined in API 6DX.
Inclusion of API 6DX within API 6D is a significant step forward for the performance, safety, and reliability of applications throughout the energy industry. The combined requirements of both standards ensure that the entire actuated valve assembly is designed for the specific application, with the actuated valve package functionally tested as a complete package.
This article will discuss API 6D and 6DX, providing an overview of the standards, as well as details on the latest requirements and documentation one can expect to receive when they purchase an API 6DX compliant actuator or API 6D actuated valve assembly.
Brief History
The API 6D standard originated in 1936 and was titled “API 5G1 Specification for Pipeline Valves.” It sought to codify and standardize the minimum requirements for wedge gate, plug and swing check valves used in pipeline service. The fifth edition was released in 1947, with the standard’s code changed to API 6D, which has remained the same since then (Figure 1).
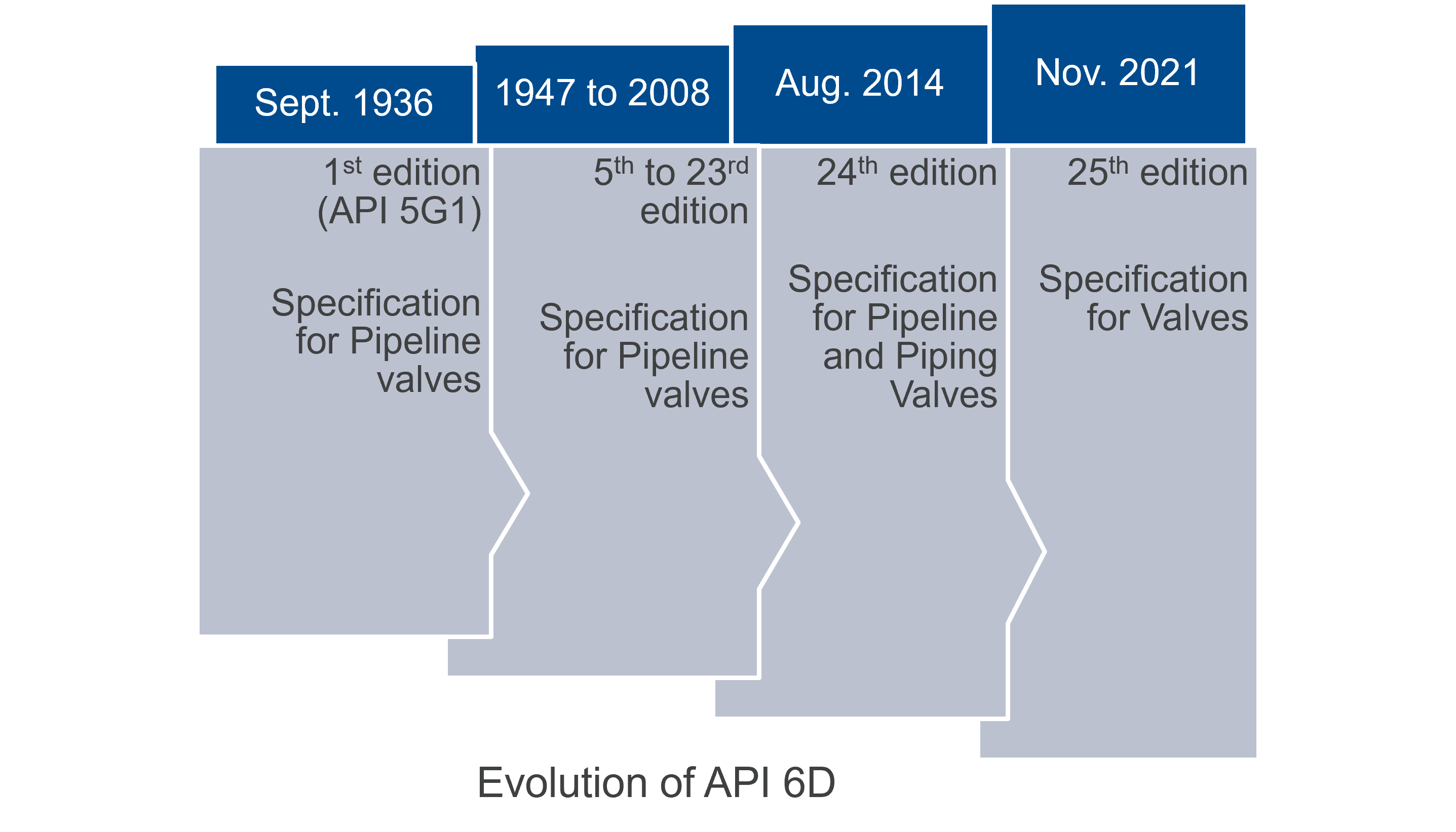
API 6D is a popular and frequently referenced standard, and it is used routinely worldwide. It has seen continuous updates and revisions, but it remained focused on pipeline valves until the 24th edition release in 2014. At this point, the title was changed to “Specification for Pipeline and Piping Valves,” and it began to reference the pipeline valve actuator standard API 6DX, released in 2012.
The API 6D scope expanded again with the 25th edition issued in 2021. This edition is titled “Specification for Valves,” and it now covers valves used in oil and gas service, as well as those associated with pipelines. It also mandates that all actuators used on 6D valves must comply with API 6DX.
API 6DX covers electric (including secondary gearbox), electro-hydraulic, pneumatic and hydraulic valve actuators, as well as their mounting kits, but it does not cover control valves. The second edition of API 6DX was updated with Addendum 1 in 2023, and it details a wide range of specific design calculations, testing protocols, and requirements, along with required documentation for any actuator installed on an API 6D compliant valve.
The third edition of API 6DX includes new updates addressing third-party distributors and integrators. It outlines requirements for organizations that assemble actuators using modules provided by actuator manufacturers.
API 6DX Overview
A detailed description of the entire API 6DX standard is beyond the scope of this article. However, it is important for users to understand the overall requirements of the standard, appreciate the benefits of actuators compliant with API 6DX, and know what additional documentation and test results they should receive when they order an API 6D/6DX valve assembly.
At a high level, API 6DX covers the design of the actuator, fabrication and inspection requirements of the actuator components/modules, testing of the final assembly, and provision of a list of the documentation necessary to certify the actuator meets the standard.
API 6DX starts with the design of the actuator. Whether it is pneumatic, electric, or hydraulic, the actuator must be designed to deliver a specific amount of torque over a specified range of motion utilizing a specific source of energy. For instance, a pneumatic actuator uses a defined range of air pressure to drive a piston, which is connected to a mechanical assembly that turns the valve.
Springs are used to oppose the air pressure and drive the piston to the valve fail-safe position (Figure 2). The torque delivered to the valve varies significantly as the valve strokes, so the starting air torque is different from the end-of-stroke air torque, and both of those values are dependent on the supplied air pressure. The spring torque varies from starting torque to end-of-torque as well.

Details matter when designing an actuator and API 6DX defines those details. The housing itself must be rated for the maximum air or hydraulic pressure it will encounter. The actuator must provide the necessary opening and closing torque across the full range of motion yet not provide more than the valve can handle.
Most valve and actuator assemblies have some kind of mounting kit that connects the valve and actuator together. All those components must be sized to handle the maximum torque and forces that the actuator will generate. A short list of key design features of API 6DX include:
- Design calculations for any pressure-containing components.
- Design calculations for any thrust/torque/mechanical load-bearing components.
- Minimum torque requirements and maximum torque, allowed for the valve assembly in both directions.
- Specific requirements for handwheels, position indicators and locking features.
- Specific material of construction requirements for various applications.
The standard also provides the minimum sizing requirements for different types of valves (Figure 3), and high integrity pressure protection system (HIPPS) valves must be sized significantly more conservatively than valves in standard process applications.
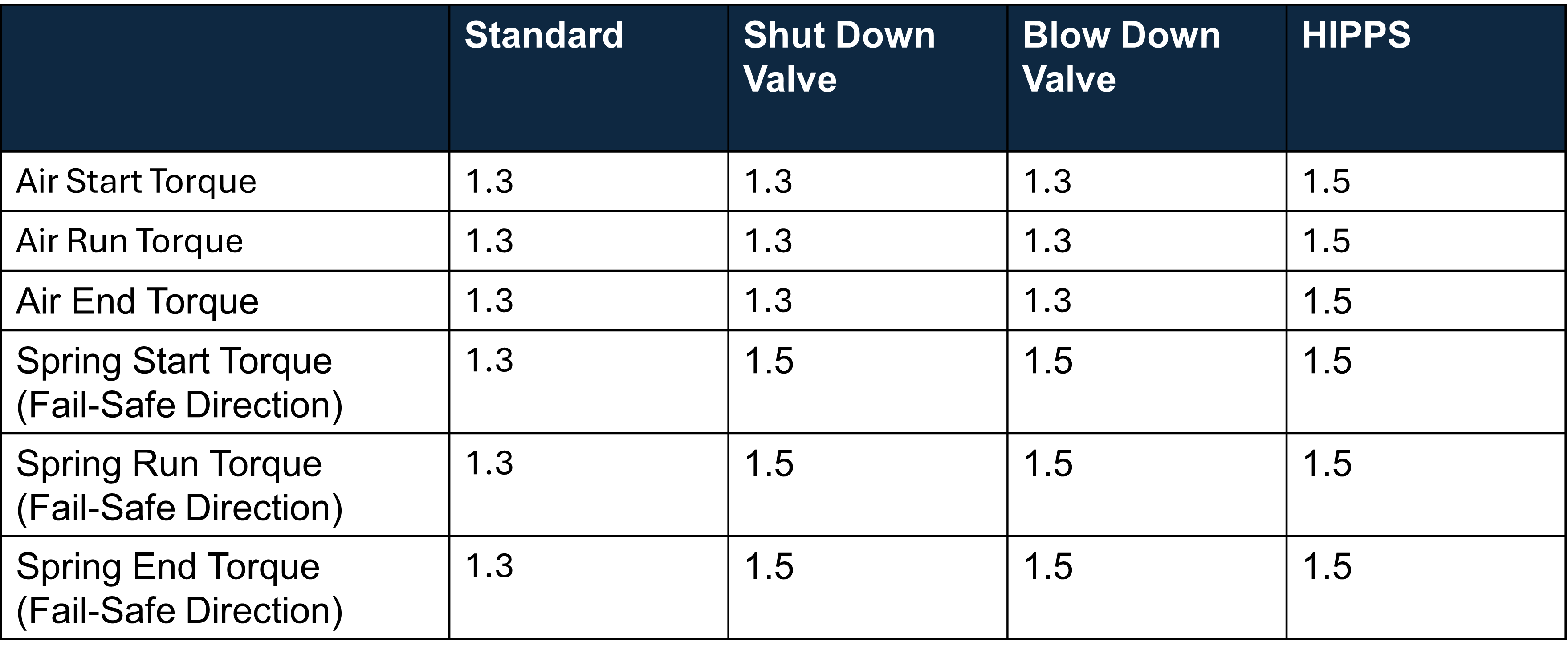
Once a valve actuator has been adequately designed, it must be fabricated, inspected, and tested to ensure the final product delivers the performance and reliability required by the application. API 6DX covers a wide range of requirements and protocols for welding, heat treating, non-destructive examination, and material testing.
The standard also dictates a series of tests each actuator component and assembly must pass to meet certification. The specific tests will vary with actuator type, but a partial list of functional tests include:
- Spring production tests: Each spring must be cycled five times under full load.
- Shell pressure/hydraulic test: Pressure-containing parts must be tested at 1.43x design pressure.
- Piston seal test: Pneumatic actuator pistons must be tested for leaks at 1.1x maximum rated pressure for a duration of 60 seconds.
- Torque test: Actuator starting and ending torques for pneumatic actuators must be measured in both directions. With electric actuators, and using a calibrated tool set to 100% of the specified torque, the measured torque must confirm that it matches the manufacturer's stated torque or thrust output.
- Actuator functional test: The entire assembly must be torqued to confirm smooth movement.
During these tests and inspections, certification documentation must be generated to prove the tests and inspections were performed by certified personnel. If a user specifies and purchases an API 6DX actuator, they should receive the following certification and test result documents with the unit:
- Torque test report
- Pressure test report
- Piston leak test report
- Certification of conformance with the actuator type, model and serial number listed
- General Arrangement drawing with dimensions
Failure to provide certified documents with the actuator to end-user purchasers will render the actuator non-compliant with API 6DX. Each actuator must have a securely affixed, easily accessible nameplate with permanent, legible markings, including the API 6DX mark.
When actuators are assembled using modules by a distributor or integrator, API 6DX 3rd Edition includes provisions for a set of functional and performance tests for actuators and valves, as outlined in the manufacturer’s or distributor’s documented procedures. This new section in the API 6DX 3rd Edition provides clear guidance, allowing distributors or integrators to supply actuators and mounting kits for maintenance, repair, overhaul, or emergency service requests by end users.
API 6DX Benefits
The main purpose of API 6D is to ensure each valve compliant with the standard meets a minimum set of qualifications for the application. API 6DX simply extends that concept to the actuators installed on API 6D valves because the actuator is an integral part of the overall valve package.
An API 6DX actuator has been carefully designed to meet the specific requirements of the application. That actuator is then fabricated from components that have met specific requirements for materials of construction, inspection, and testing.
The final assembly is again tested by certified personnel to confirm the final actuating assembly will perform as expected when installed. If an API 6D actuated valve assembly has been specified, then the entire actuated valve package will be tested to confirm it meets the standard.
All these extra steps take extra time and effort, so an API 6DX actuator or API 6D certified valve assembly will cost more than a similar actuator/valve that does not comply with the standards. However, the final product will provide dependable and reliable service in the specific application for which it was designed, and it will satisfy regulatory requirements. This is particularly important for mission- and safety-critical applications in the energy industry.
Conclusion
API 6DX certified actuators and API 6D compliant actuated valve assemblies are an essential component of many gas, oil, and pipeline applications. The inspections and testing requirements for these components can be onerous, but the end result is reliable valve and actuator components that are well suited for the intended service.
End users should demand the full suite of certification documents when they buy an API 6DX compliant actuator and be dubious of any vendor offering API 6DX compliant actuators without certified documents, or at no additional cost. The inspection, testing, and documentation do come at a price, but the fit-for-purpose performance, reliability, and dependability easily justify the investment.
Author: Girish Dalbhanjan is an engineering director at Emerson with 22 years of experience in the valve actuation industry. He has a strong track record of leading global teams in the development of new products and technology platforms, driving innovation and fostering growth in the engineering function. He represented Emerson's Technical Authority, influencing industry standards through participation in technical specification committees, such as API, ISO, JIP33 and industry-specific groups.
Comments