December 2011, Vol. 238 No. 12
Features
Do You Know What You Have In the Ground?
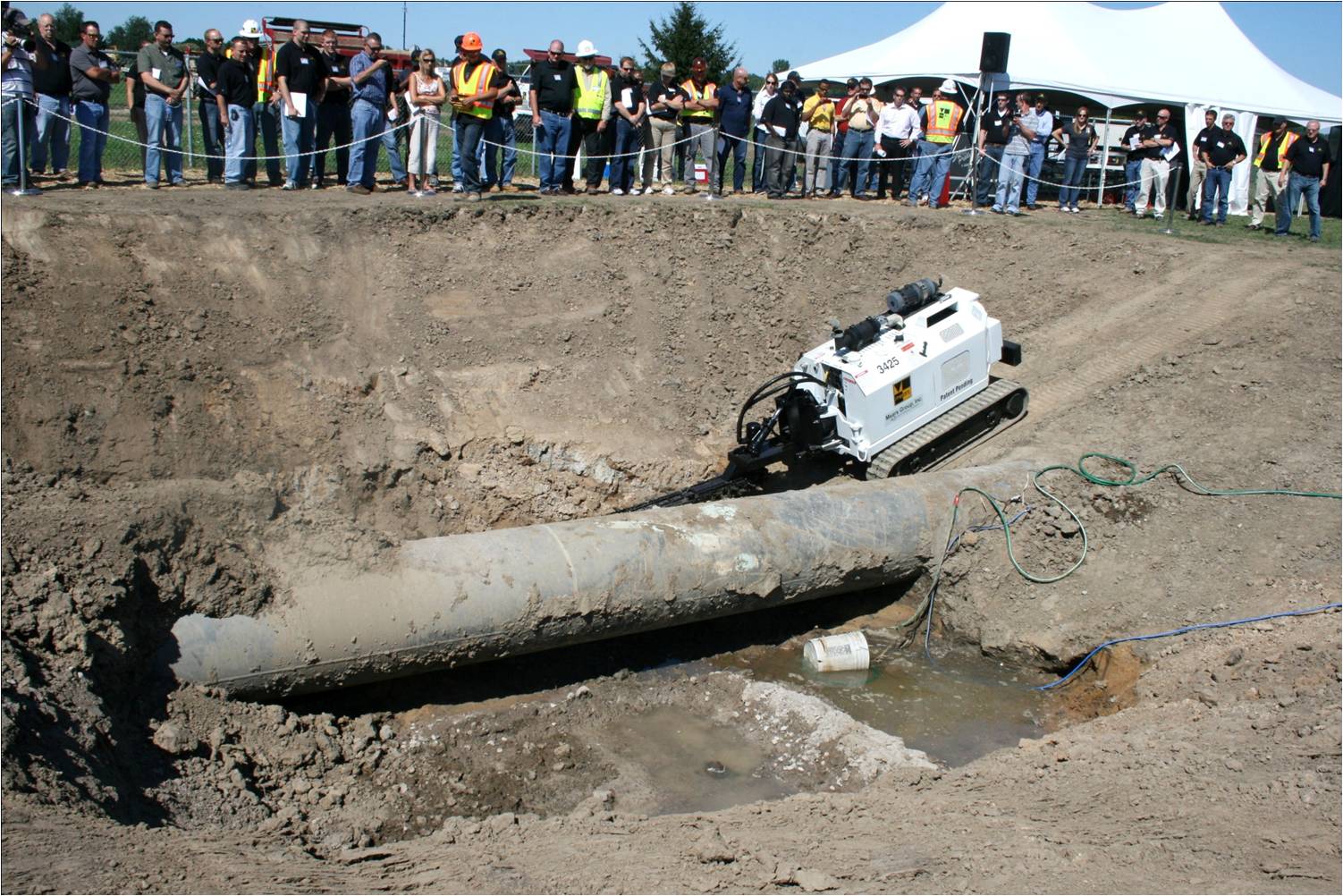
At its recent Integrity Educational Seminar, Mears Group Inc., personnel focused on the topic of establishing the maximum allowable operating pressure (MAOP) of a gas pipeline and the general concept of operating margin of safety.
It included an historic look at how MAOP has been determined and what future regulatory requirements and industry initiatives are certain to be. Speakers included Alan Eastman, Chris Warner and Kevin Garrity of Mears, Doug Spencer from Microline Technology Corporation and Bob Travers of Spectra Energy.
Eastman explained that the recent PHMSA advisory notice on MAOP instructed companies to use recorded evidence and integrity management risk identification, assessment, prevention and mitigation when determining MAOP. Operators follow regulation 192.619 which states that a steel pipeline cannot be operated at a pressure that exceeds the lowest of the following conditions:
- Design pressure of the weakest component;
- Pressure test divided by factors associated with class locations;
- The highest actual operating pressure realized during the five years preceding Nov. 11, 1970; and
- The pressure determined by the operator to be the maximum safe pressure after considering the history of the segment, known corrosion and the actual operating pressure.
PHMSA is pushing operators to re-validate a minimum current operating margin of safety and to take actions to prevent future degradation of that margin. Its notice asks operators if they are fully cognizant and have accurate records of factors such as location, pipe material and seam type, coating, cathodic protection history, repair history, previous pressure testing or operational pressure history, and other assessment information, incident data, soil type and environment, operational history or other key risk factors. If not, and the pipeline is operating at or above 30% specified minimum yield strength, then take the following steps:
- Institute an aggressive program to obtain this information;
- Assess the risks;
- Take proper mitigation measures based on the operators IM program; and
- Take an immediate or interim mitigation measure which could include pressure reduction to 80% of the operating pressure for the previous month, run a hydro test or create a remediation program to address risks.
PHMSA says records must be reliable, verifiable and traceable. Historically, operators have relied on pressure testing to validate the required operating margin of safety. This includes mill and field testing – where standards have varied over the years. Field testing has ranged from MAOP to >90% SMYS. Some pipelines built prior to the 1960s may have only received a “leak test” at MAOP.
There are numerous other factors affecting MAOP, some of which are time-dependent. These include external, internal corrosion and stress corrosion cracking. Non-time dependent factors are manufacturing defects, fabrication and construction defects, equipment related defects, third-party or mechanical damage, incorrect operations and weather or outside force-related events. Considering all factors, operators have options ranging from replacing the line to re-pressure testing or instituting an ILI or DA program.
The key is to developing a strategy going forward is to know and maintain your margin of safety, which is based on recorded and verifiable data. Based on numerous factors, this could involve anything from replacing the line, to re-pressure test, instituting an ILI or DA program.
Tethered Pipeline Inspection
Mears announced a working alliance with Microline to offer tethered ILI. The Microline Group consists of six companies including: Microline: NDT Research & Development; Inline Devices: ILI Technology & Services; IonEarth: SBD Satellite Communications.
Their technology came from the oilfield, developing tools to inspect drill pipe and casing. Technology exists for lines two to 32 inches. Tethered systems were developed for lines that are considered unpiggable – shorter line segments or lines without pig launchers and receivers. This can include oil and gas production lines, gas storage and distribution lines, airport fuel lines and other product lines, power generation and water process lines, refinery piping, river crossings, cased crossing in HCA areas. Lengths can go from hundreds of feet to 20,000 feet under the right conditions. The limiting factor is dynamic friction affecting the tool and tether.
There are purpose-built tethered inspection systems and “tether-optimized” ILI systems, and all can be configured to provide the type of information companies are looking for on their pipelines. Tethered ILI systems meet the API 1163 standard, which provides requirements for qualification of inline and tethered -inspection systems; ANSI/ASNT ILI-PQ, which establishes the minimum requirements for qualification of inspection personnel; and NACE Standard RP0102-2002, which outlines a process of activities that ILI vendors and pipeline operators can use to plan and execute an inspection project.
INGAA Action Plan on Pipeline Safety
Bob Travers, Director – Pipeline Integrity for Spectra Energy Transmission, gave an overview of the “INGAA Action Plan to Build Confidence in Pipeline Safety.”
The plan commits members to a goal of zero incidents, a safety culture, a relentless pursuit of improving safety by learning from the past and anticipating the future, applying integrity management principles on a system-wide basis, and to engage all stakeholders to help them understand and participate in reducing risk.
There are nine steps in the plan. The first is to apply risk management principles beyond high consequence areas. The goal is to continue to expand the program over the coming years to ultimately cover 100% of the population within the PIR by 2030. Again, the second step is to raise the standards for corrosion anomaly management by applying the same HCA standard to areas outside the HCAs.
Step three is to demonstrate fitness for service on pre-regulation pipelines. This involves validating records and MAOP for pipelines in HCAs that pre-date federal regulation. If records are inadequate, they need to be assessed and the situation remediated.
The next step is to shorten pipeline isolation and response time to one hour in the event of an accident. This involves remote control valves and/or auto close valves. Improving communications and coordination with emergency responders is another one of the steps of the plan.
Improving integrity management communications and performance data and translating this into meaningful industry information and communicating it to stakeholders is the next step. The remaining ones are to implement the pipelines and PIPA guidance; evaluate, refine and improve threat assessment and mitigation; implement management systems across INGAA members and to provide forums for stakeholder engagement and emergency officials.
Indirect Inspections For Grounded Pipeline Facilities
Kevin Garrity presented preliminary results of the research project to assess detection capabilities of indirect inspection tools in compressor, regulator and metering stations.
New TCAT System
Mears introduced “The Corrosion Analysis Tool (TCAT)” at the seminar. TCAT is a unified management system for the collection of direct examination (bellhole) inspection data, the associated images and performing remaining strength analyses. TCAT offers enhanced data quality and management, GIS integration, enhanced efficiency and real time data access for clients.
The hardware consists of a tablet computer and a GPS-enabled 8 mega-pixel camera. The tablet and camera are resistant to water, dust and shock. The data collection and viewing software can be customized for individual clients. In the field the software performs automatic data checks and alerts the technician to data errors, and missing data or required photos.
TCAT interfaces with pit depth tools and ultrasonic thickness instruments for immediate data input. The corrosion grids interface with KAPA (the program that runs RStreng which determines the remaining strength of a corroded area) to provide failure pressure calculations as soon as the corrosion mapping is completed. As data is collected it is sent to a Mears secure server that can be remotely accessed by clients. A full rollout of the pipeline software will occur in 2012.
Comments