December 2011, Vol. 238 No. 12
Features
Technical Prowess And Strength Make Bimodal PE Pipes A Top Gas Distribution Choice
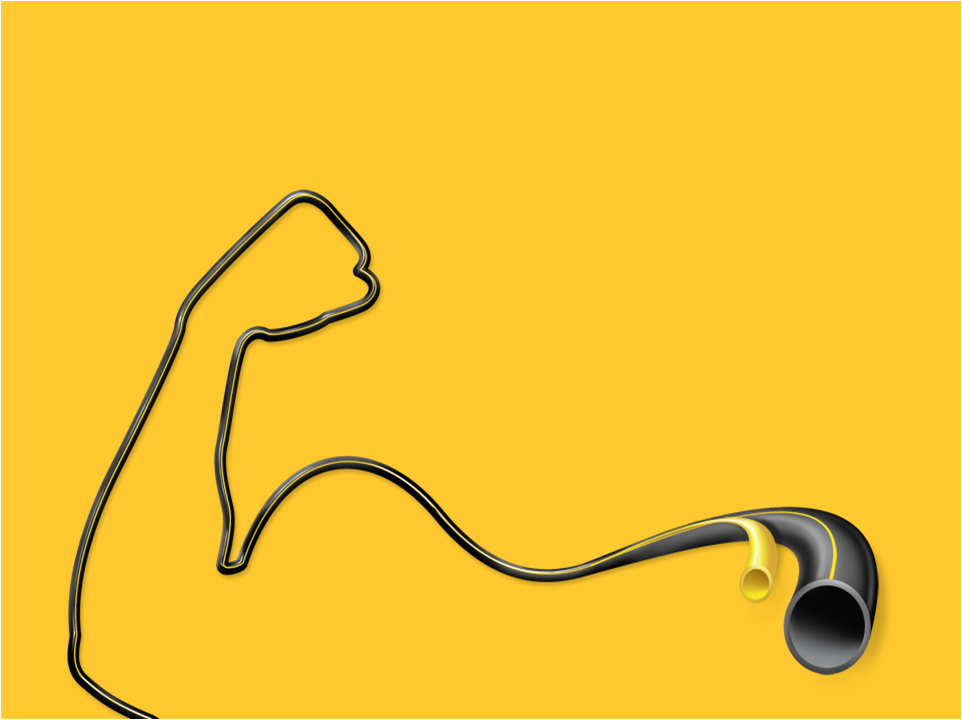
Pipeline leakage, breakage and other critical issues can create multiple environmental problems, cost utilities millions in lost revenue and delay important services to customers. There is no doubt that reliability is key – and that includes starting with the right pipeline distribution system manufactured with the right ingredients.
Gas utility distribution lines were historically crafted from cast iron or steel, but myriad issues – including corrosion and leakage – with certain systems made with these materials have proven them to be less reliable for the crucial and integrity-demanding application that major utilities and their customers require. However, technological materials advances in the 1960s ushered in the use of thermoplastic pipe systems – particularly those made of polyethylene (PE) – for gas distribution.
Long known for its class-leading properties and reliability in low pressure gas distribution systems, PE piping is now the most widely used plastic piping material for the safe, cost-effective transport of fuel gases for residential, commercial and industrial applications. Much of the attraction for the PE plastic pipe system ties to its corrosion resistance, but it is also a choice because of its handling ability and “no-dig” attributes when it comes to installation. The fusion-welded jointing commonly used in PE systems also contributes to a reliable, leak-free gas distribution system.
Extensive testing, more than 50 years of field experience, and an inertness to the external soil environment and to natural gas have proven polyethylene as the material of choice for the long term. Today, there are more than 2,000 gas utilities in North America, and more than 90% of those gas distribution pipe systems are made of polyethylene.
The Wave Of The Future: Bimodal MDPE And HDPE
Polyethylene production technology breakthroughs in recent years have translated into even more advances for gas distribution pipelines. Gas utilities are quickly discovering the benefits associated with bimodal medium-density (MDPE) and bimodal high-density polyethylene (HDPE) pipes.
Compared to unimodal materials, bimodal MDPE and HDPE materials show a significant increase in critical pressure and have considerably lower critical temperature values. Such differentiated performance properties like these are one reason that many industry experts and analysts believe that, in the future, all PE materials the gas industry uses will be bimodal.
Superior SCG, RCP Resistance
Chief among the benefits of bimodal over unimodal PE pipe systems is its resistance to slow crack growth (SCG), which translates into better service life and longer utility pipeline integrity. Another benefit of bimodal MDPE and HDPE systems is its ability to prevent rapid crack propagation (RCP) – a very fast fracture that can literally split hundreds of feet of pipe in seconds.
Bimodal MDPE and HDPE distribution systems are also stronger and more durable at low temperatures – a critical component in colder climates that unimodal materials do not have.
Leak-Free, Bimodal Durability For Tough Installs
MDPE and HDPE piping is leak-free when produced properly – even at the joints, which can be as strong as the pipe itself when manufacturers use a heat fusion joining technique. Both are corrosion- and chemical-resistant – and resist rot, pit, tuberculation and biological growth. MDPE and HDPE pipes also offer seismic resistance – safely accommodating repetitive pressure surges above traditional static pressure ratings, making them ideally suited for seismic loading because of their natural flexibility.
In addition, the flexibility of MDPE and HDPE material has proven more cost-effective for installation compared to steel. Because of its ability to stand up to horizontal directional drilling and boring, crews can direct-drill or bore under roads or rivers instead of having to tear up roads and sidewalks for installation – saving utilities money in the long run.
It is the strength and durability of bimodal MDPE and HDPE material that allow it to survive the abuse that naturally accompanies installation, as well as a range of tough and rocky environmental conditions.
Bimodal MDPE Pipe Delivers Hard-Working Performance In Nebraska
For the Metropolitan Utilities District (MUD) in Omaha, cost efficiency and top performance is critical. The rate payer-owned utility has more than 200,000 commercial, industrial and residential gas customers and is in the midst of an infrastructure upgrade to replace hundreds of miles of outdated cast iron pipe, the newest of which is 60 years old, and the oldest being 120 years old.
Originally scheduled as a 30-year plan, the utility is trying to shorten its upgrade timeframe to 15 years. Part of MUD’s upgrade initiative has included switching to bimodal MDPE pipe from the traditional unimodal MDPE pipe for its SCG and RCP resistance.
“We started exploring options and immediately saw the obvious benefits of the bimodal MDPE pipe,” said Denise Dolezal, senior gas design engineer, MUD. “We saw the potential for long-term lifecycle benefits, especially the rapid crack resistance aspect, which is critical in our climate.”
Since making the switch, the utility has installed more than 155,000 feet of bimodal MDPE pipe, which ranges from 1.25 to 4 inches. Since the installation and fusion procedures for the bimodal are essentially the same as those for unimodal, there has been no disruption for crews or the installation process.
“It’s about value for the dollar and responsibility to our rate payers, and what we earn goes back into the system,” continued Dolezal. “The primary reason for the switch from unimodal was because of the bigger benefits of bimodal. Given the similar pricing between bimodal and unimodal, it was a very simple decision. ”
Bimodal HDPE Success In New Mexico
Given its durability, some gas companies are using PE pipe in more demanding applications, such as larger pipe diameters and in higher operating pressures. This makes the resistance to RCP an even more important requirement – and bimodal HDPE pipe in particular has delivered just that for the last six years for New Mexico Gas.
In New Mexico, the climate and conditions differ from one end of the state to the other, with significant snow up north, desert to the south, and extremely rocky conditions in the eastern part of the state. As a result, reliable resistance to RCP and SCG is critical for the safe operation of the utility’s gas distribution pipeline system. The state has also experienced explosive growth in recent years, with 150 new gas installs per month in the Albuquerque area alone, underscoring the need for additional capacity and flexible, hassle-free installation.
“Both the RCP and SCG resistance properties gave us a huge benefit for the state’s rocky conditions and diverse climate,” said Angela Serrano De Rivera, senior engineer for New Mexico Gas. “Because of our environmental climate, we go through rigorous testing before we do anything – and the bimodal HDPE performance has been a big benefit.”
Today, the utility serves more than 200,000 customers across the state and, over the last six years, has installed and operated more than 14,300 miles of bimodal HDPE pipeline – which ranges in size from 12-inch to ¼ inch – without incident. Based on its overall performance and safety record, New Mexico Gas requires all of its pipe manufacturers to use the bimodal HDPE resin.
“It’s better for the environment and helps minimize rock impingement concerns, so we don’t have any issues with slow crack growth,” explained Serrano De Rivera. “We’re continuing to grow and using the bimodal HDPE resin for our distribution pipe system is our first choice.”
An Economic Win
Utilities such as MUD and New Mexico Gas realize the short- and long-term benefits that MDPE and HDPE piping can serve to actualize. The properties of bimodal MDPE and HDPE resins make them ideal for the manufacture of gas distribution piping. Its strength and durability, improved pipeline system integrity and resulting longer pipeline service/shelf life – translates into long-term economic benefits – and are advantages for gas utilities across the country to consider.
Author
Alan Radwanski is market manager – Pipe and Irrigation, Performance Plastics North America, The Dow Chemical Company.
Comments