January 2011 Vol. 238 No. 1
Features
Identifying Time Constraints When Designing And Building A Strategic Pipeline
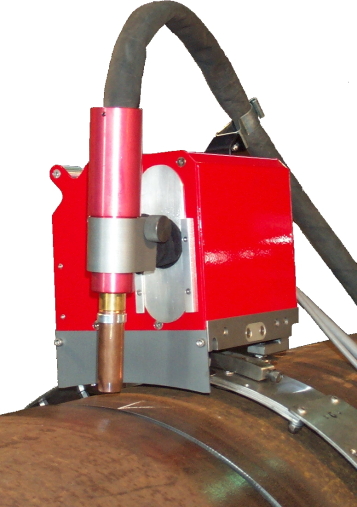
Time constraints in pipeline project execution can involve either the construction phase or the overall project cycle duration, which mainly depends on the root cause of the time constraint from several perspectives such as high risk due to construction in an unsecured area, government instructions or whether the project is part of a strategic program.
The knowledge of where the time constraint is assigned can help the project designers to create a design for a shorter execution duration. Value engineering is the most practical technique for implementing this orientation. It is a very useful tool for cost optimization in a pipeline or any other project, but its influence on project cost and duration is not considered. Thus, in this case, value engineering has to be performed with respect to time, cost and risk impact. It is highly recommended that one start value engineering at the early stage of the project where the front-end engineering design (FEED) is taking place.
The cost of the changes varies proportionally with project time. That means whenever changes are implemented earlier, the cost of the change is lower. Therefore, any time constraints should be identified as early as possible where they can be observed in the project objective, project charter or any other initial project documents.
The project manager is the primary individual responsible for identifying challenges and constraints based on his/her personal experience, records of similar projects and the judgment of other experts. Consequently, the message should be delivered to FEED engineers to start providing an alternative for the ways in which a project will be executed on the basis of different design proposals. Designs for shorter execution duration proposals should be presented along with a detailed cost and risk impact report for each proposal. In addition, workshops should be held involving the designer, project manager, project sponsor (owner) and other relevant stakeholders. The workshop results and recommendations will form the basis of the design, construction and contract agreements with the different suppliers.
Pipeline Route Selection
Depending on the pipeline project requirements, one or more distribution points will be necessary along the pipeline route. This selection process focuses on achieving the optimal location for a pipeline and its direct output from the project FEED phase. The designer’s intention is to keep the investment costs (for pipeline construction) and maintenance costs at a minimum. Hence, it is necessary to find and define a relatively direct connection and consequently short route between the start and end point, and if necessary, to the connection and distribution points in between. This intention focuses only on the cost. However, a long pipeline route execution sometimes is less direct than a shorter pipeline route due to difficult soil conditions or pipeline interfaces with the existing infrastructure.
Actually, many considerations from several perspectives are involved when selecting the pipeline route. However, only the main subjects that may be considered when selecting a route with respect to designing for a shorter execution duration are discussed here. Pipeline vents and drain stations have a high cost and time impact on pipeline construction, thus the route should be selected to minimize the number of high and low spots in the line where high spots may require vent stations and low spots in shallow lines may require drain stations.
Avoid Crossings Where Possible
Furthermore, pipeline crossings have to be avoided as much as possible in route selection when the designer is seeking a shorter execution duration, even if the alternative is a longer route. Regardless of whether the crossing is for another pipeline, roads, rivers or creeks, it always consumes more time not only in the construction process, but even in obtaining the work permit from the property owner and other preconstruction documents. A constructible pipeline route is not only the route that can be accessed by construction equipment. It also has to be flexible for changes concerning the minimizing of any possible pipeline bends.
Normally, the direction of the pipeline is changed by bending the line pipe on-site to field bends in accordance to relevant national regulations, whereas hot bends can be used at locations where the use of field bends is either unfeasible or unreasonable. Another type of elastic bends for regular radius is used in pipelines by a cold-bending machine.
All bends in the pipeline require a longer construction period than straight pipe laying. However, the hot bends take the longest procurement delivery time. Hence, minimizing pipeline bends in general, and hot bends in particular in pipeline route selection, is highly recommended when the design intention is for a shorter execution duration.
Hydraulic Study
Commencing construction without line pipe available on-site does not make sense. Other predecessor activities before line pipe laying or stringing include survey, right of way and even trenching work in parallel with respect to the amount of lag time between each activity once the line pipe is delivered to the site. A hydraulic study report is the primary document for any pipeline project and is usually produced during the FEED phase. It may also be produced in parallel with the pipeline route selection as many factors interfere in both hydraulic study and route selection. The hydraulic study report contains the essential data which significantly affects the project duration in terms of the delivery period for the procurement of line pipes, valves, etc. Hence, a comparison sheet that includes all the applicable line pipe data such as “wall thickness, material, grade etc…” against the cost and delivery time for each item could be created during the hydraulic study.
This comparison sheet should be presented to the project manager and sponsor as part of the first step toward the design proposal assessment. In cases where large-diameter pipes are necessary, the designer may instead propose installing smaller twin-diameter pipelines instead of one large-diameter pipeline. This proposal should be presented in addition to the cost and expected delivery time for each scenario. The specific pipe roughness factor is another output parameter from the hydraulic study report, and it may require attention regarding the estimated execution time and cost for some applications that have to be coated internally with an internal pipeline lining.
Construction Methodology
Regarding construction techniques that may minimize the project execution duration, the first step is to identify critical activities on the expected critical path. The activities with the longest duration may be shortened by using appropriate and efficient construction techniques. In normal onshore carbon steel pipeline projects involving trenching, welding and NDT, the non-destructive tests are the most critical activities in the construction schedule, and each one has to be studied separately. For trenching, the ditcher is a timely and effective piece of equipment used for pipeline trenching but it has many constraints concerning the required trench size and soil conditions. These factors may be taken into consideration in the FEED process with regard to pipeline diameter and soil conditions of the route.
Automatic Welding
Using an automatic welding machine is also highly recommended for a rapid welding process during construction. This process has been developed by many companies in both onshore and offshore construction, but an automatic welding system with an arc sensor and a vision-based sensor has the ability to perform real-time seam tracking, oscillation width profiling, and back-bead formation control in the welding of narrow grooves in any welding position, in order to produce quality welded joints independent of the skills of welders or welding operators. This is very useful in terms of the weld quality and for higher-speed welding performance. After realizing a rapid welding technique, the NDT technique has to follow the same approach.
Recently, an automated ultrasonic technology system has achieved acceptance as a companion method to weld radiography. Technically, an automated ultrasonic test cannot replace the radiography test, as both techniques may be used at the same time. However, using the former will offer fast results in the case of repairing a UT-detectable repair instead of waiting for the radiography results.
Conclusion
Management and non-technical people always desire a fast-track project, but – considering the cost and risks in this kind of project – it should be studied properly before proceeding. As mentioned, when presenting the different design proposals, the cost impact should be demonstrated to the decision makers. Moreover, it is also necessary to present the associated risks for each proposal.
Regarding the risks, two different types may occur: the first type is the associated risks if the project is not completed on time, and the other type is the associated risk if the project is executed according to the proposed method. In reality, it is very difficult to incorporate the suggestions and recommendations that have been proposed in the FEED stage when designing a pipeline within a shorter execution duration. Nevertheless, FEED engineers have to implement whatever is possible and applicable in order to meet the execution duration target. Furthermore, the planning and design phase is normally shorter than the execution phase. Conversely, the planning and design phase may require a longer duration if the project has to be executed within a shorter than normal time frame.
Author
Ahmad Emam is senior planning engineer in ILF Consulting Engineers, Abu Dhabi, United Arab Emirates. He has handled planning and cost for several projects including onshore pipeline projects and his work has taken him to Egypt and Kuwait where the pipeline owners were BP, Kuwait Oil Company (KOC) and Saudi Aramco. He earned a bachelor’s degree in industrial engineering from Helwan University, Egypt and is pursuing his MBA from the Management Institute of Canada. He is certified as PMP and PMI-SP. He can be reached at e-mail: ahmademam@aim.com.
Comments