February 2012, Vol. 239 No. 2
Features
Completing A Challenging Directional Drill In The Marcellus Shale
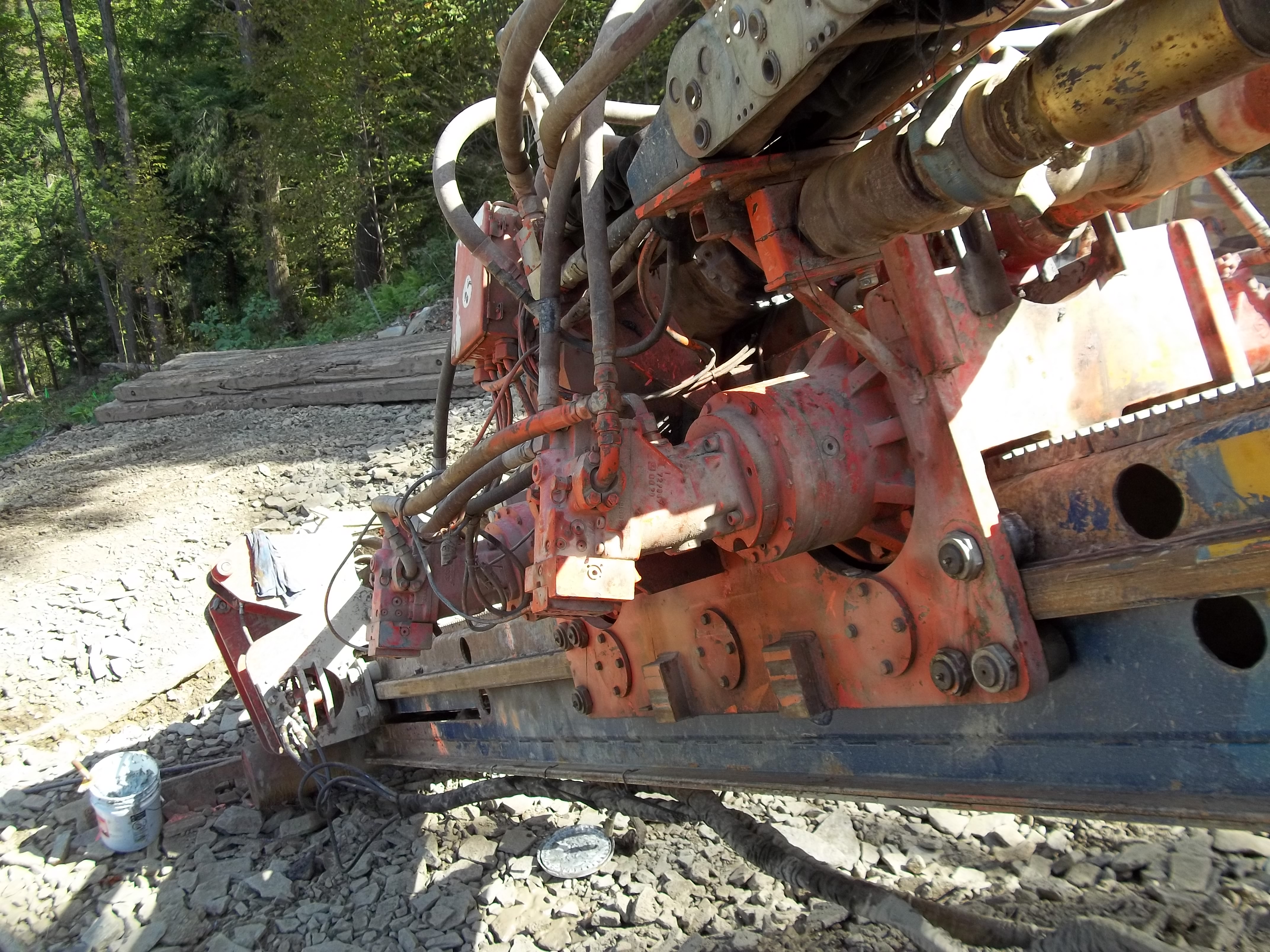
Your geologists found natural gas hiding thousands of feet underground. Your legal team negotiated rights of way with landowners. Your drilling team went down a mile or so, made a horizontal turn and “fracked” the shale bed, releasing the gas. Your well is producing. So now what?
Now you have to get the gas from the wellhead to the waiting world. It means laying gathering lines from the wells and connecting them to larger distribution lines. It means that every time you have to cross a stream, wetland, road, mountain or other obstacle, you’ll have to employ horizontal directional drilling (HDD) technology. That is, you will have to bore beneath it. In northeastern Pennsylvania, it means you’ll bore – plenty.
Trenchless technology covers a wide range of methods, materials and equipment for the installation of underground infrastructure with minimal surface disturbance. However, combine drilling underground with negotiating topography and you have the recipe for challenges which raise the question: “is this possible?” In one 8½-mile stretch Linde Corporation and Gabe’s Construction Company completed 13 different bores traveling more than three miles. It took place in an area in Susquehanna County that crews from the two companies now fondly refer to as “Death Mountain.”
Liberty Park’s Unusual Bore
A variety of issues complicated the so-called Liberty Park bore. First was the distance of the bore, as it was planned to run 1,332 feet in length, underground. The bore would have to drop more than 100 feet to get under the stream and road and then come back up the other side at a two to one angle.
Space, Weight and Angle Issues
Then a new wrinkle appeared – a conventional pullback of the pipe couldn’t be done. Ordinarily, the pipe sections would all be welded together and the continuous string would be pulled back as one piece through the bore hole. This was not possible at Liberty Park because of space and weight factors. First, the exit angle was too severe. This was caused by right-of-way restrictions and by power lines just 150 feet from the entry point of the pipe that would be in the way if all the lengths were welded beforehand in the conventional style.
Officials with Linde and Gabe’s decided to weld the pipe together in sections while suspending each length of pipe in the air during welding. Complicating the plan was the fact that each length of pipe was three sections of 42 feet each, just less than 130 feet in length. The 16-inch steel pipe weighs about 65 pounds per foot, which means each length of pipe tipped the scales in excess of five tons.
Gabe’s Construction, formed in 1942, has been actively involved in the trenchless field since 1989. Pittston-based Linde Corporation has a 14-year history in boring and claims it has never failed to complete a bore. “If we say we’ll do a bore, then we’re all in,” said Linde HDD Manager Fred Ostroski. “Once we start, we’ve never walked away from a job. We’ve known the people from Gabe’s a long time. They’re the same way.”
Solving Unique Problems
After walking around the problem for a day, Linde and Gabe’s chose what they say was their most sensible approach. Using a 150-ton crane and an excavator, they would simply suspend each 130-foot length of pipe motionless in the air at an angle of exactly 41 degrees. Then they would weld it to the pipe length sticking out of the ground.
There would just be two potential problems: Wind and water. Any breeze of more than a couple of miles an hour would make the pipe unstable in the air. And rain might make the five-ton pipe too slippery to be held safely in place. Indeed, the bore would take place near the top of one of the highest hills in the county, during the summer of the wettest year ever recorded in Pennsylvania.
“You could move a suspended length of pipe with your fingertips,” explained Linde Vice President Bob McGraw. “Any movement and the welds would fail the x-ray test. And rain water on the pipe would make it impossible to weld.”
In the end, it was a delicate moving act, choreographed by subtle hand signals to communicate with the crane and excavator operators and steer the multi-ton length of steel pipe into a lineup clamp and hold it stationary. Some crane and excavator movements were mere fractions of an inch.
Once the pipe length was in the lineup clamp, it was welded and the welded area was x-rayed, sandblasted smooth, covered with a two-part epoxy-based coating to protect the welded areas from rusting and then pulled through the exit hole while the next length was moved into place. Crews performed nine such mid-welds with each pipe section suspended in the air. Each of these “mid-air” welds took about three hours from beginning to end.
In a conventional bore pullback, this one string could have been pulled through the bore in less than an eight-hour shift. In this case, “conventional” was out of the question. The pullback of the pipe in this bore took about 33 hours to complete. Linde and Gabe’s crews say they believe this procedure is unique to the practice of horizontal directional drilling.
Another Unique Challenge
Not a quarter of a mile away from the Liberty Park bore was another unique challenge. In this case, it wasn’t the pipe but the directional drill itself that had to be radically altered to do the job.
As bores go, there have been longer ones: 1,035 feet MD (measured distance along the bore path) would have been relatively routine had it been flat, open ground. But the ground wasn’t open, it was far from flat, and as a result this section of horizontal directional drilling received the nickname “Death Mountain.”
Almost nothing about this bore was normal. First was the elevation change, a 220- foot vertical drop in just 500 linear feet from the drilling rig to the low point, then back up 50 feet to the exit point.
Groundwater was higher after Hurricane Lee and the water infiltrated the bore path, diluting the drilling fluid. A thinner fluid means less suspension which is less effective at removing cuttings from the hole. Removing the cuttings wasn’t the hardest part.
Just to get the drilling fluid from the containment area 220 feet up to the drill required a series of three relay pumps. However, that wasn’t the hardest part.
The hardest part was setting up the horizontal directional drill at the correct angle to attack the slope and then extending the boom length to keep the drilling platform stable. This bore required the drill to tilt at an angle of 37 degrees. Problem was this drill was designed to achieve a maximum tilt angle of only 18 degrees. Linde and Gabe’s would have to alter the machine and the ground to make the bore work.
First, they built a sloped pad which let the drill unit tilt at a full 10.8 degrees from horizontal. The power unit was held in place by anchor plates. That took the total tilt of the drill to 29 degrees. The rest of the tilt would have to come from changing the machine itself.
To further increase the angle of the drill, the hydraulic cylinders had to be disconnected. To achieve the proper boom length and maintain a stable platform, the boom had to be moved forward. The only way to do that – cut off the hose supports with a torch so the boom could telescope out further. At the end of this process the drill had to have the proper angle to bore under the wetland and enough stability to pull tons of welded pipe back through the hole.
Gabe’s HDD operator Patrick “Hopper” Thomasen showed the finished product, a rig which sloped 37 degrees from horizontal. The new configuration exceeded the normal slope angle of this rig by 19 degrees and exceeded the normal boom length by three feet. The drill was able to complete the bore and allow the pipe to be pulled through the opening.
Negotiating one hill required standing multi-ton pipes on their ends. Negotiating the other hill required altering the very nature of a million-dollar directional drill. The Gabe’s driller says his machine was functioning at well beyond the normal operating parameters of these drills. Linde HDD manager Fred Ostroski said Linde was operating at the “limits of constructability.” In other words, it was just a typical day wrestling with Death Mountain.
Comments