February 2012, Vol. 239 No. 2
Features
Developments In Diagnostic Capabilities Of DP Meters
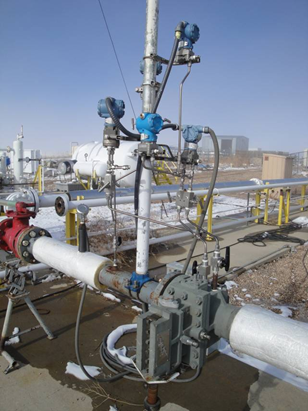
Differential Pressure (DP) flow meters have been widely used since Herschel first developed the Venturi meter in the 1880s. The orifice plate meter, possibly the most popular flow meter ever, is a derivative of the Venturi meter. Weymouth introduced the orifice meter a century ago.
There are also other successful DP meter designs developed from the original Herschel Venturi meter concept such as nozzle, Venturi nozzle, cone and wedge DP meters.
DP meter designs are widely considered simple, sturdy and therefore reliable. They are also usually relatively inexpensive flow meters. These traits have led to DP meters being one of the most widely used flow meters in the oil and gas industry. However, in recent years with the value of hydrocarbon product increasing, with more hydrocarbon assets owned by multiple parties, and with an increase in safety requirements, the need for precise flow metering throughout the production system has become more pressing. The industry has been increasing its demand for meters that have diagnostics internal to the meter system.
Figure 1 shows a 4-inch, 0.6 beta ratio dual chamber orifice meter at the CEESI wet gas flow test facility. Due to the DP meter’s simplicity it has long been held as an axiom that DP meters cannot have any diagnostic system. Traditionally, all DP meters operate by having an obstruction (primary element) in the pipe that changes the local pressure as the fluid passes the obstruction. For example, in Figure 1, the orifice plate is the primary element. Measuring the difference in pressure between upstream and in the vicinity of this obstruction gives the “differential pressure” or “DP”. This DP can be related to the flow rate through simple physical laws.
Due to the simplicity of this method of flow measurement, it was long assumed that a DP meter can have no significant diagnostics capabilities, as there apparently wasn’t enough information from the meter to work with. As such, in the last two decades other meter designs with various levels of internal diagnostics have taken significant market share. However, in 2009 the axiom that DP meters can have no diagnostics was challenged. DP Diagnostics released details of the successful development of a comprehensive diagnostic system internal to any DP meter system, e.g. orifice, Venturi, nozzle and cone meters.
In 2008 and 2009 DP Diagnostics carried out a substantial test program to research and develop the first ever diagnostic system for DP meters. These tests were supported by Colorado Engineering Experiment Station Inc. (CEESI). Every major CEESI flow test facility was utilized. CEESI even offered existing non-confidential DP meter data sets that could be of extra help in the diagnostic system development.
In 2009 this comprehensive DP meter diagnostic concept was revealed to the industry. By 2010 DP Diagnostics (a DP meter manufacturer) and Swinton Technology (a leading UK system integrator) had partnered to produce a DP meter diagnostic system. The initial disbelief through out the oil and gas industry was followed by questions of “just how does it work!?”
Figure 2: A single chamber orifice plate diagnostic ready meter.
Figure 2 shows a single chamber orifice meter with a downstream pressure tap and an extra DP transmitter. (A close inspection of Figure 1 also shows such a configuration.) A traditional DP meter has a single traditional DP read from the two pressure taps, i.e. the DP between an upstream pressure tap and a pressure tap in the vicinity of the obstruction. However, the addition of a third pressure tap allows three DPs to be read.
A second DP can be read between the upstream and downstream pressure tap (Figure 2).
A third DP can be read between the downstream pressure tap and the pressure tap in the vicinity of the obstruction. In Figure 2 the third DP is not represented as being measured, as the operator can choose to infer this value from the other two read DPs, i.e. it is the difference between them.
The three DPs from any generic DP meter make substantial diagnostic methods available. Through simple physical laws each of the three DPs can be independently related to the flow rate. That is, every DP meter has the potential to offer three flow rate predictions instead of the traditional single flow rate prediction. These three flow rate predictions can be inter-compared to produce diagnostic capabilities.
An alternative diagnostic approach is to consider the three ratios of DPs produced. All correctly operating generic DP meters produce known DP ratio values. Hence, these known values can be compared to the actual values. Therefore, by reading these three DPs instead of the traditional single DP, six diagnostic checks can be produced, i.e. the three flow rate prediction comparisons and the three DP ratio value checks. These combined methods have been shown to make a very powerful generic DP meter diagnostic system.
Figure 3: A graphical representation of the DP meter diagnostic results.
A DP meter diagnostic system is only practical if the average operator can easily utilize it. Hence, it is important that if these diagnostics are to be of practical use throughout industry the average user must understand what the diagnostic system is saying without the need for any specialist skills or substantial training. For this reason a very simple graphical representation of the diagnostic results has been developed. The three DPs produce three DP pairs, each pair having the two diagnostic checks of the flow rate comparison and the DP ratio check. Hence, the two checks per DP pair can be represented by a single point on a graph (with two co-ordinates).
Therefore, the three DP pairs produce three points. A box is drawn around the origin of such a graph (Figure 3). The box indicates the allowable performance limits of the meter. If there is a meter malfunction, one or more of the points leave the interior of the box and the meter malfunction warning is raised.
In 2008 DP Diagnostics tested multiple DP meters at CEESI. Figures 4 shows a 4-inch, 0.6 beta ratio Venturi meter under test at the CEESI wet natural gas flow facility. Figure 5 shows a 4-inch, 0.6 beta ratio cone meter under test in one of CEESI’s air blowdown facilities. Note both have downstream pressure taps. For all correctly operating DP meters the diagnostic system indicated correct operation, i.e. all points in the diagnostic box (Figure 3).
With the exception of the orifice meter, all the diagnostic parameters for all generic DP meters were found with the same meter calibration as is required for the standard operation of DP meters. However, the orifice meter was a special case. The international standards (e.g. ISO, ASME, API, AGA etc.) give enough information so that an orifice meter can have all the required diagnostic parameters derived from the information given in these standards. That is, the orifice meter does not have to be calibrated to be made diagnostic capable. Importantly, this means all orifice meters with an available downstream pressure tap currently in service can be retrofitted with the diagnostic system.
Figure 4: 4-inch, 0.6 beta ratio Venturi meter being tested with a downstream pressure tap at the CEESI wet natural gas flow facility.
Figure 5: 4-inch, 0.6 beta ratio DP Diagnostics-manufactured cone meter being tested for diagnostics at a CEESI air blow down test facility.
Figure 6: Buckled orifice plate and diagnostic result.
Figure 7: Nut trapped at cone element and diagnostic result.
Figure 8: Wet gas flow through Venturi meter and diagnostic result.
Naturally, no DP meter diagnostic system development program was complete without the fun of deliberately introducing various common malfunctions to various DP meter designs and checking the diagnostic system reaction. After proving that the diagnostics showed each correctly operating meter to have no malfunction, various malfunctions were deliberately introduced. Figures 6, 7 and 8 show randomly selected sample diagnostic tests for three DP meters.
Figure 6 shows a buckled orifice plate producing a negative error on the flow rate prediction and the corresponding diagnostic result.
Figure 7 shows a nut trapped at a cone producing a positive error on the flow rate prediction and the corresponding diagnostic result.
Figure 8 shows wet gas flow and the corresponding diagnostic result when the wet gas flow induces a Venturi meter to over-read the gas flow rate. These are just random examples out of a large test series. A large variety of common DP meter malfunctions were induced and the diagnostic system indicated a problem existed for all malfunctions tested.
The system’s sensitivity to the magnitude of errors is dependent on the type of DP meter and the particular malfunction that has occurred. The tests showed that most common malfunctions of DP meters will be seen by the diagnostics before the induced flow rate prediction bias is 1% beyond the stated calibrated uncertainty.
In 2009 Swinton Technology partnered with DP Diagnostics to create the industry ready “Prognosis” DP meter diagnostic system. A field trial was required and it was offered by BP at the Central Area Transmission System (CATS) gas terminal in the UK (Figure 9). BP CATS operates 16-inch orifice meters for natural gas flow measurement (Figure 10). “Prognosis” used with orifice meters solely requires the orifice meter standards to supply enough information to characterize the orifice meter diagnostic system. Therefore, the tests could commence by retrofitting “Prognosis” to a BP 16-inch orifice meter, with no meter calibration required.
Figure 9: Overview of BP Central Area Transmission System (CATS).
Figure 10: BP CATS 16-inch orifice meter runs.
The retrofitted “Prognosis” system immediately showed the BP CATS orifice meter to be working correctly. A series of malfunctions were then deliberately induced on the meter, i.e. incorrect keypad entry of the inlet diameter and then the orifice diameter, a DP transmitter was over ranged (or saturated), a DP transmitter was incorrectly spanned to simulate instrument drift, the plate was inserted backwards and a plate had wear applied to the orifice sharp edge. All malfunctions were clearly seen by Prognosis.
BP CATS has been running Prognosis continuously since May 2010. BP states that the most useful point about Prognosis is to tell them when the meter has not malfunctioned. A trustworthy source guaranteeing the meter is fully serviceable can vastly reduce the maintenance cycle thereby reducing maintenance costs. However, more importantly still, knowing the meter needs no maintenance keeps staff away from the dangerous environment of the large, high-pressure pipelines.
Figure 11: DP Diagnostics Venturi meter under standard calibration and diagnostic calibration at the CEESI multiphase wet gas flow loop for Petronas.
Figure 12: Solartron Venturi meter under standard calibration and diagnostic calibration at the GL Flow Center dry natural gas flow test facility for Centrica.
Prognosis is now in use with Venturi meters. Petronas in Malaysia and Centrica in the UK have both independently added the diagnostic system to Venturi meters destined for offshore platforms. Figure 11 shows the DP Diagnostics-manufactured 6-inch, Venturi meter under diagnostic calibration for Petronas at the CEESI multiphase wet natural gas flow test facility. The use of Prognosis with wet gas Venturi meters can be very attractive due to the diagnostic system’s high sensitivity to free liquid content in a gas flow.
Changes in the diagnostic plot can indicate shifts in the liquid to gas flow rate ratio, and the diagnostics are also good at monitoring the health of each DP transmitter. This is particularly useful for wet gas flow applications because wet gas flow can cause multiple problems for DP transmitters. The associated higher DPs caused by wet gas flow can cause transmitter saturation. Unsteady wet gas flow can cause significant and continuous DP fluctuations therefore inducing premature drift on the DP transmitter.
Furthermore, wet gas can produce hydrates, scale and salt deposits that can block impulse lines, etc. Therefore, a system that can monitor DP transmitter health in wet gas flow service can be very useful.
Figure 12 shows a Solartron-manufactured 6-inch Venturi meter under standard calibration and simultaneously diagnostic calibration for Centrica at the GL Flow Center natural gas flow test facility in the UK. These calibrations were the first third-party DP meters to be calibrated for diagnostics at a third-party test facility. Prognosis was found to work precisely as claimed.
Conclusion
DP meters have long been popular in the industry, yet there have been no diagnostic capabilities. There has been a widely held axiom that DP meters cannot have diagnostics because there is not enough information from the meter to analyze. However, there is now a simple but powerful diagnostic system based on just one extra pressure port and DP transmitter. From this, all generic DP meters have been found to not just have some diagnostics, but comprehensive and powerful diagnostics that can rival any modern meter’s diagnostic capability.
Until recently there were many in the oil and gas industry who believed the simple DP meter that had served industry so well for more than a century was finally reaching the end of it useful life and it would begin to get phased out. However, with the addition of the simple but powerful diagnostics, that belief has now been questioned by operators in major oil and gas conferences.
Authors
Jennifer Rabone joined Swinton Technology (UK) in 2009. She has nine years of experience in sales, marketing, customer relationships and after sales support in the metering industry. She graduated with a degree in pure mathematics (First Class Honors) and earned a master’s degree from the School of Mechanical Engineering at Cranfield University. She can be reached at jennifer.rabone@swintontechnology.com.
Kim Lewis, B.S., is a general partner in DP Diagnostics LLC, a DP meter manufacturer. He has 19 years of experience in flow measurement, manufacturing flow meters and 30 plus years working as an engineer in the aerospace, nuclear and general manufacturing industries. He can be reached at klewis@dpdiagnostics.com.
Comments