July 2012, Vol. 239 No. 7
Features
Clamp-on Ultrasonics Solve Storage Well Measuring Challenges
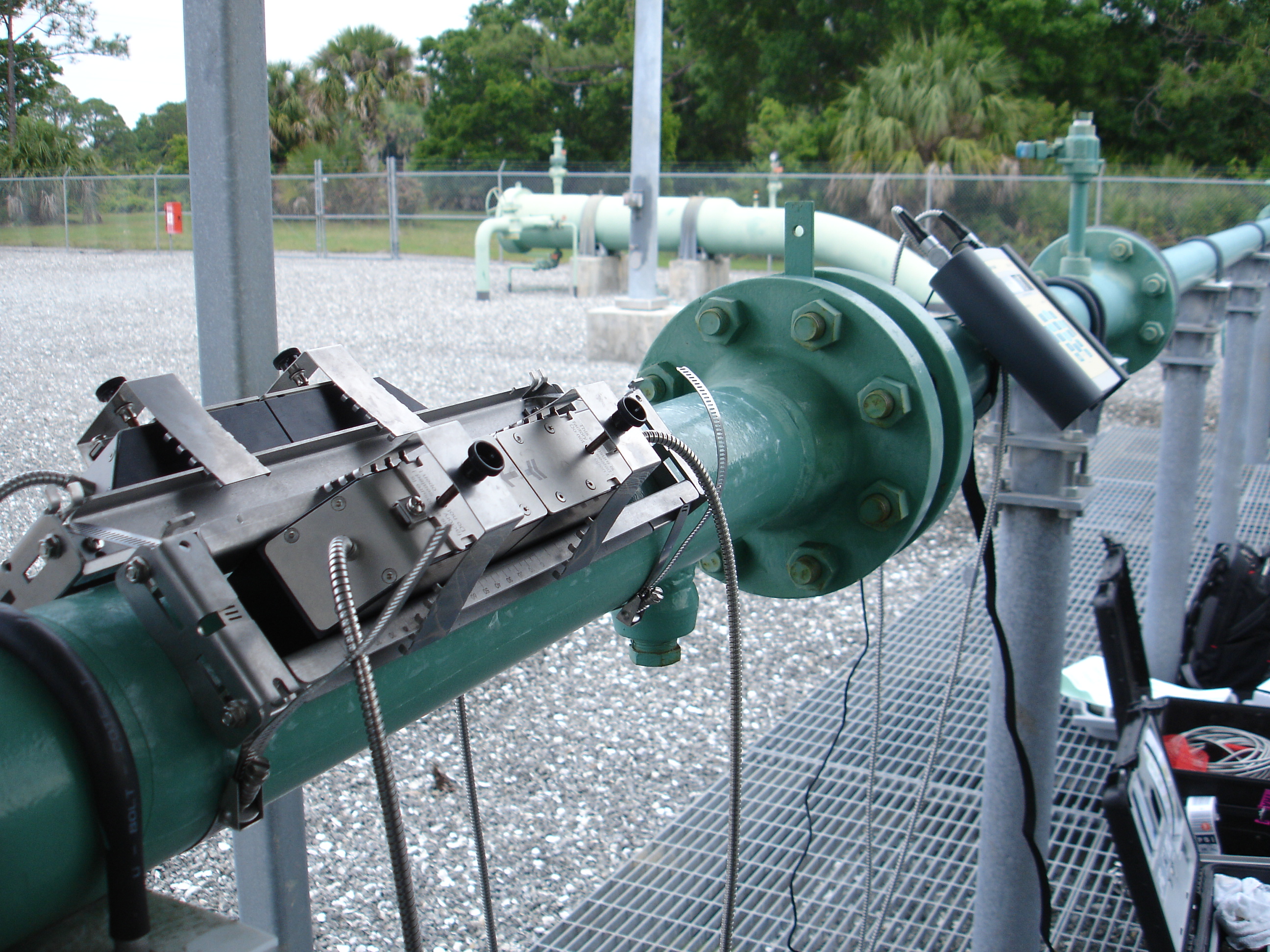
Clamp-on ultrasonic meters provide accurate measurement for natural gas reservoir storage wells and in several other applications. Natural gas is stored during the warm months so it is available when demand increases.
The most used storage facility for natural gas is depleted gas wells. Because it is mandatory for gas producers to know the quantity of the gas being stored and the pressure, they may hire specialty companies to monitor the transfer of natural gas into and out of the reservoir wells.
Eastern Reservoir Services (ERS) is one such company that provides flowback, slickline and testing services for some of the leading gas producers, including EQT, Dominion, Columbia Gas and National Fuel.
Bram Alackness, ERS field engineer, explains, “We use a variety of monitoring systems to test the flow into and out of the storage wells. The tests are called Deliverability/Performance Tests and basically help determine at what rate the gas will flow based on varying pressures.
The test results can also help determine well characteristics like skin factors, permeability, porosity and reservoir capacity. The client uses the data we gather to determine the performance they can expect from each well – what each well can provide under what pressures when it is time to get the gas out of the storage well. We use a variety of meters including orifice meters, turbine meters and gas flow provers.”
Alackness continues: “All have their problems, however. The most common meter type, orifice meters, are very accurate when conditions are ideal, but they can easily clog with sand and other contaminants. Moisture and wear on the orifice (also) affect accuracy.
“We had been looking for some time for a way to be able to test areas where we didn’t have permanent installed meters. Last year I was given the assignment to identify a portable meter that didn’t involve cutting into pipe or releasing gas into the atmosphere. It would have to be battery powered and have memory capability so we could get the readings back to our data technicians.
“It soon became apparent that clamp-on ultrasonic metering was the way to go. I researched all of the meters available and narrowed it down to FLEXIM. We had a few meters in for demonstrations and it won out because it had the features we needed, including a 16-hour battery. It was also the most intuitive and fast to install,” Alackness said.
How Ultrasonic Flow Meters Work
The technique most ultrasonic flow meters use is called transit-time difference. It exploits the fact that the transmission speed of an ultrasonic signal depends on the flow velocity of the carrier medium, kind of like a swimmer swimming against the current. The signal moves slower against the flow than with it.
When taking a measurement, the meter sends ultrasonic pulses through the medium, one in the flow direction and one against it. The exterior transducers alternate as transmitters and receivers. The transit time of the signal going with the flow is shorter than the one going against.
The meter measures transit-time difference and determines the average flow velocity of the medium. Since ultrasonic signals propagate in solids, the meter can be mounted directly on the pipe and measure flow non-invasively, eliminating any need to cut the pipe.
Overcoming Challenges
Alackness added, “So far we have used the ultrasonic meters to test more than 200 client storage wells and things have gone well. In the beginning we had a few cases where it was difficult to gather good data because of a poor signal. Not every well is the same, so gathering flow data is not completely foolproof. For example, on one well I was on a typical horizontal run (4.5-inch diameter, .197- inch wall) and I could not get a signal whatsoever with the transducers horizontal (direct mount) on the pipe (9 and 3 o’clock position), but when I moved them to the vertical (12 and 6 o’clock position) I had very good signal. With the new meters, you can get creative and always get a signal. The testing company that preceded us at one facility was reporting wells with zero flow when it was clear that was not the case.
“The problem is mostly with the piping. Some of it is quite old and has buildup on the inside. Sometimes the pipe has to be pressurized/ flowing to get a signal; sometimes it does not. I have been dealing with mostly 42-inch to 8-inch diameter pipe.
“The more we work with the ultrasonics, the better we get at what to do in different situations. I can say we have not had a well that we were not able to record flow data from. The manufacturer has been good at helping us with creative solutions. We’ve ended up with three different sets of transducers that enable us to measure flow in a variety of pipe sizes and application conditions. With the ultrasonic meters we are now able to give our clients more and better data,” he said.
Robert Haupt is a field technician for ERS who joined the company after they had purchased the ultrasonic meters. He said he had never used them before.
Said Haupt, “I used them from April into October and they work great measuring flow rate and pressure on injection lines for storage wells. What we do is we put hole pressure gages down in the well and then we inject the gas from the compressor station into it so we can tell if the well is going to be able to hold gas to store it.
“Our typical flow is about 4 MMcf/d so we use the ultrasonic meters to hold that flow rate so we can get a good graph on our down hole pressure gages and tell whether it is holding or leaking. We are also using the meters to tell how much gas we move.”
Ultrasonic For Production And Storage
Said product manager Izzy Rivera, “We’ve been having a lot of success with metering production and storage wells in the last few years primarily because the meters are capable of measuring gas that will contain contaminants (moisture and particulates). Maintenance of ‘wetted’ meters can be high in these environments. Another advantage is that ultrasonic meters have a very wide range of flow, typically greater than 100 to 1. Orifice meters have a narrow turn down range, typically 4 to 1. During the life of a gas well or different seasonal flow rates from a storage well, the orifice will have to be removed and re-sized. Then shut-down and maintenance can be costly.
“Once gas comes out of the well head it goes to a gas separator where gas and liquids are separated. Clamp-on ultrasonic flow meters are capable of metering liquids and gases. Using meter diagnostics, the meters can even make a distinction about the type of liquid coming out of the well. What’s interesting is that a two-channel meter is used after the separator to meter both the gas and liquid after it is separated. One meter handles both the liquid and the gas,” Rivera observed.
He added, “More companies are looking at clamp-on ultrasonic meters for applications that were typically serviced by other technologies. For over 15 years, gas transportation pipeline companies have been using multi-path wetted ultrasonic meters for high accuracy monitoring and custody transfer of natural gas.
“Clamp-on meters, which are typically 1% accurate, are rapidly becoming the meter of choice where fiscal type accuracy is not required. The last five years have seen rapid growth for clamp-on ultrasonic meters. They are being utilized in production, storage, pipelines, processing, utilities and power stations – every phase of distribution,” Rivera said.
Comments