January 2024, Vol. 251, No. 1
Features
New Alternatives for Noise Reduction in Gas Pipelines
By Aida Bukvic, Experitec, Eli Harms, Industry Consultant, Shelby Daniels and Tyler Reeder, Emerson
Natural gas pipeline pressure reduction applications pose significant design challenges for engineers. Since flow varies considerably through these stations, control valves are required to throttle over a wide range, with large pressure drops at times, which create the potential for high noise.
Historically, pressure reduction stations have typically been installed in remote locations, so sound levels were not a significant concern — provided they remained below a destructive threshold. However, as neighborhoods begin to form around sites, sound reduction has become a much more pressing problem.
This article describes the difficulties of natural gas pipeline pressure reduction, and it discusses a new noise abatement solution, which one large utility company has been employing with a high level of success.
Pressure Challenges
Gas pipeline pressures are typically elevated to 800 psi or higher, to efficiently move the product through the transmission network. Once the gas reaches the point of use, the pressure must be reduced significantly, to meet user requirements. This task is accomplished by directing flow through one or more pressure control valves, located at the pipeline pressure reduction station (Figure 1).
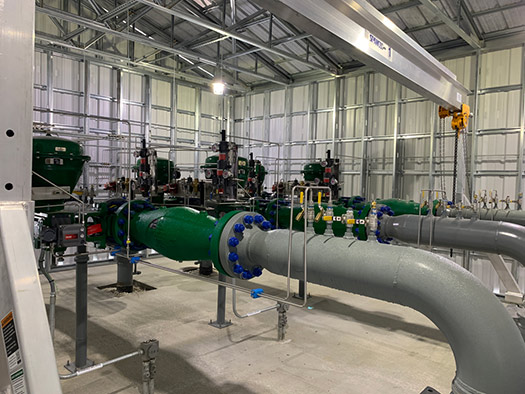
Two pressure control runs are typically used at a pressure reduction station. One run serves as the primary feed for the downstream system, and the other serves as a standby, if the primary run fails. In some cases, the flow rates, pressures — or a combination of both — require more runs. These additional runs are typically automated, to allow switching to the run best suited for current conditions. This run switching can help prevent valves from operating at the lower end of their control band, where much of the noise is created.
As natural gas passes through the restricted portion of the control valve, the pressure decreases, and gas velocity increases significantly. This turbulent flow generates noise that travels down the pipeline, radiating in all directions. While the turbulence will settle out, the noise tends to fall off much more slowly, and downstream equipment could face risk from the excess vibration.
Depending on the process conditions, noise levels can reach 110 dBA or greater. As sound levels rise above this threshold, the vibrations can create metal fatigue in internal components, which will shorten the life of the valve considerably, posing reliability problems for the station.
When a pressure reduction station is in a remote area, noise is less impactful — provided the sound levels stay below 110 dBA. As neighborhoods expand, some formerly remote sites become surrounded by residential and commercial properties. The public tends to be somewhat leery of pressurized natural gas pipelines in general, so complaints come quickly if the station is generating any significant noise at all.
Residents can be especially sensitive when the station is louder than normal, as tends to occur during low flow conditions, when a control valve is throttling in the lower portion of its control band. Large pressure reductions with high flow conditions can also create more sound than normal, due to the increased velocity through the valve.
As a result, design teams generally would like to keep the sound levels as low as possible, but achieving this in practice can be quite difficult. It requires a careful review of the range of expected flow conditions, along with details on site locations, piping geometry, applicable codes and regulations and company standards.
It is important to note that these valves tend to work continuously in various process conditions throughout the seasons. This makes reviewing calculations at various conditions important to ensure noise is low.
Silence Is Golden
Absolute silence from a pressure reduction station is not feasible, but one can spend a lot of gold in pursuit of it. Historically, there have been several ways to quiet a throttling control valve, and each comes with a tradeoff.
Pipeline insulation and site enclosures reduce noise, but these only serve to mask the problem, allowing the noise to continue to radiate downstream. A better solution, in many cases, is reducing the amount of noise propagation inside the pipe. This method also best protects downstream equipment from excess vibration created by the noise.
Low noise valve and regulator trims depend upon numerous small holes or slots to manage the turbulent, high-velocity flow — thereby reducing sound. Low noise trims operate across a wide range of flows, but they can also be quite restrictive, as they greatly reduce the flow capacity of the valve or regulator. Small flow passages are also more susceptible to plugging from particulates within the process. Inlet filters can remove some of the incoming particulates, but they must be cleaned frequently.
These low noise trim options are highly engineered solutions, and for the sizes common in natural gas pipeline service (NPS 6 and larger), they can be costly — especially if two control valves are required for each run. Another option is to split the flows across multiple pairs of parallel valves — sized for high and low flow conditions — but this requires a much more significant investment, increases the cost of maintenance and adds to the overall footprint.
New Technology
A gas utility in the Midwest knows this challenge all too well, so to minimize operator sound exposure and customer complaints, the company began designing their pressure reduction stations to a much lower sound level standard than had been used previously.
Initially, the company utilized all the typical techniques — thicker pipe, sound deadening enclosures, careful design of downstream piping to avoid resonance and more — but the calculated sound levels were still too high.
The company has multiple gas distribution sites with wide open monitor stations that directly affect the amount of natural gas they can supply to the region. They also need the capability to handle a wide range of flow rates, due to changing demand throughout the year, which requires large pressure drops at times, leading to high noise levels. The challenge was to reduce noise without limiting flow rates, while eliminating the need for additional runs of piping.
After various calculations were made on a broad range of noise solutions, the gas utility was introduced to Emerson’s newly designed modal attenuator — the Fisher WhisperTube — by their local Emerson Impact Partner Experitec. This new noise reduction technology was released in 2021. The solution is called a modal attenuator (Figure 2), and it is composed of a number of carefully designed resonant cavities, surrounding a straight through, full bore screen.
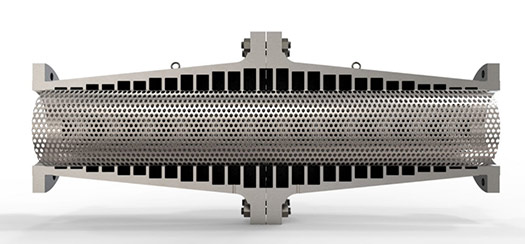
Each cavity in the modal attenuator is specifically designed to create destructive interference for a specific set of frequencies, with a net result of 10 to 15 dBA noise reduction. Unlike low noise trims, the modal attenuator achieves this noise reduction with virtually no pressure drop, and the straight-through design is much less susceptible to plugging.
The design also incorporates a drain channel for easy removal of any fluid present in the process media. All those features make the modal attenuator often the best choice for natural gas pressure reducing applications, as it was for this company.
The expected sound levels were calculated using a rotary ball valve design, with and without the modal attenuator (Figure 3). Based on the typical flow conditions, the new solution was expected to provide 12 dBA of overall sound level reduction, easily meeting the targets set by the design team. The modal attenuator reduced noise without affecting the flow capacity or characteristics of the process, so the gas utility company was able to address the noise without having to adjust their pressure or flow characteristics.

Experitec worked with the gas utility company to implement this new technology, bringing overall noise levels below 85 dBA — without having to add additional upstream filters — and enabling stations to run much longer between maintenance outages.
Since that successful installation, the modal attenuator has been incorporated into the gas utility’s standard pressure reducing station design. The gas utility’s technicians can safely perform maintenance, and their nearby residential customers can tune in to “Family Feud” without any distractions.
Conclusion
Safe, uninterrupted natural gas supply is a gas utilities’ top priority. Left unaddressed, noise levels in the process can be high enough to pose safety risks to workers, introduce non-compliance to environmental standards, provoke customer dissatisfaction and negatively affect mechanical integrity and system reliability.
If your application poses similar challenges, consult your valve automation vendor to determine which noise solution best fits your process. There are a number of viable noise solutions available to system design engineers, so selecting the best choice can be daunting; however, the right valve vendor can provide the answers you need.
Of these options, the modal attenuator is finding widespread use in a broad range of applications, and it is certainly well suited for natural gas reduction stations, where decreased noise levels are typically required. In this case, achieving 12 dBA noise reduction — with no-pressure-drop and no impact on the process conditions — enabled the gas utility’s design team to utilize lower cost control valves, while still meeting target performance specifications safely and reliably.
Authors:
Aida Bukvic is a sustainability/natural gas industry manager-final control at Experitec, an Emerson Impact Partner, where she serves as the natural gas industry and natural gas regulator subject matter expert. Previously, she was an applications engineer focusing on the sizing and selection of Pressure Management and Flow Control Products. Bukvic graduated from Saint Louis University in 2018, with a bachelor’s degree in mechanical engineering, and from Webster University in 2022, with an MBA.
Shelby Daniels is product marketing manager at Emerson, supporting Fisher Rotary products in severe and critical service. Previously she was a Senior Sales Engineer in Global Industry Sales supporting Flow Controls products in the refining and power industries. Daniels is a graduate of the University of Missouri with a bachelor’s degree in chemical engineering.
Tyler Reeder is a sales engineer at Emerson, working in Global Industry Sales. His focus is on the oil and gas industry, handling both the upstream and midstream markets. Reeder is a graduate of Iowa State University, with a bachelor’s degree in mechanical engineering.
Eli Harms is a measurement and control engineer for a utility providing natural gas to its customers in the Midwest region of the U.S., and he is the company’s subject matter expert for regulator and delivery stations. Harms spent a total of 11 years in the U.S. Marine Corps and Army National Guard, prior to graduating from Southern Illinois University–Carbondale, with a bachelor’s degree in mechanical engineering.
Comments