July 2012, Vol. 239 No. 7
Features
Oil and Gas Measurement Still Dominate the Energy Markets
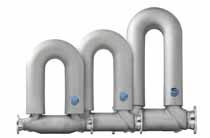
The world’s energy picture is a complex mixture of factors. For years, oil has been the dominant source of energy in many countries. But in the past ten years, it has become clear that the world’s supply of oil is not unlimited, and that over time alternative sources of energy must be found.
At the same time, it has become widely accepted that carbon emissions and greenhouse gases are damaging the earth’s environment, and that something must be done to protect the environment. Petroleum products and coal are the two main sources of carbon emissions and greenhouses gases.
In this context, renewable sources of energy such as wind, solar energy, and geothermal seem very attractive. They are clean, seemingly unlimited in supply, and do not have the same harmful effects on the environment as fossil fuels. The main problem with renewable energy is that the development of these energy sources is still in the early phases, and most of these energy resources are still too expensive to compete effectively with fossil fuels. There are also issues related to creating the infrastructure necessary to deliver alternative energy effectively where it is needed and in a form it can be used. And different forms of alternative energy are used for different applications. For example, batteries and fuel cells have been developed to power cars, while solar panels are used to heat houses.
In part because of the difficulties in moving quickly to renewable energy, natural gas has emerged as a very attractive alternative to petroleum products. Natural gas burns cleaner than oil, and new drilling technologies have greatly increased the amount of natural gas, including shale gas, that can potentially be drawn from the earth.
New-Technology and Traditional Technology Meters
Flowmeters can conveniently be divided into new-technology and traditional technology flowmeters. New-technology flowmeters were introduced after 1950, and are more the focus of new product development than traditional meters. Their performance, including criteria such as accuracy and reliability, is typically at a higher level than that of traditional flowmeters. Traditional technology flowmeters were introduced before 1950, and are less the focus of product development than new-technology meters. While some traditional meters can achieve high accuracy levels, they generally do not have the same accuracy and reliability levels as new-technology meters.
The main types of new-technology meters used to measure oil and gas flow are ultrasonic and Coriolis. The three main types of traditional technology flowmeters used to measure oil and gas flow include differential pressure (DP), turbine, and positive displacement. DP and turbine flowmeters are widely used for upstream applications, as well as some downstream applications. Positive displacement flowmeters, by contrast, are mainly used for downstream applications.
DP Flowmeters
DP flowmeters rely on a constriction placed in the flow line that creates reduced pressure in the line downstream from the constriction. A DP flowmeter requires a means to detect the difference in upstream vs. downstream pressure in the flow line. While this can be done with a manometer, today’s DP flowmeters use differential pressure transmitters that sense the difference in pressure, and then use this value to compute flowrate. This calculation is based on Bernoulli’s theorem.
A variety of devices, called primary elements, are used to create a constriction in the flowstream. Orifice plates are the most common and most studied type. Other types include Venturi tubes, flow nozzles, Pitot tubes, and wedge elements. When a primary element is united with a DP transmitter, a DP flowmeter is formed. DP flowmeters are widely used for upstream applications in oil and gas fields. They can typically handle the dirty fluids that come out of an oil well. They are also used for subsea applications, where they are capable of withstanding the high pressures associated with subsea drilling. Averaging Pitot tubes are used to measure stack gas and exhaust gas emissions.
One advantage that DP flowmeters have is that they have approvals from bodies such as the American Gas Association (AGA) for custody transfer applications. The AGA standard for orifice plate flowmeters is known as AGA-3. This study was most recently issued in complete form in 1992, although the work underlying this standard goes back to the late 1920s. AGA-1, a predecessor of AGA-3, was first issued in 1930. This was the first standard issued by AGA for custody transfer measurement, and it helps explain why DP flowmeters with orifice plates have such a large installed based in the oil & gas industry.
The development of orifice fittings has enhanced the use of DP flowmeters in the oil & gas industry. Orifice fittings include an orifice plate that is mounted in a holder. They are used for custody transfer, although they have other applications as well. The leading suppliers of orifice fittings are Emerson Daniel, Canalta Controls, and The Measurement Company.
Turbine Flowmeters
Turbine flowmeters rely on a spinning rotor that turns in proportion to flowrate. While they were first developed in the 1790s, it wasn’t until the 1940s that they came to be widely used. Turbine meters were used during World War II to measure the use of fuel on military planes. After this time, they came to be used for industrial applications.
Turbine flowmeters are best used for steady, medium to high-speed flows. The presence of a rotor in the flowstream causes some pressure drop. It also means that turbine meters cannot effectively be used with fluids containing particles or impurities, since these can damage the rotor. The rotor is a moving part that is subject to wear. Suppliers have addressed this issue by making turbine meters made from more durable bearings, such as ceramic and sapphire.
While research by AGA on the use of DP flowmeters with orifice plates goes back to the late 1920s, the AGA did not issue its first report on turbine meters until 1981. This report was called Measurement of Fuel Gas by Turbine Meters, and was called AGA-7. The most recent version of this report was called Measurement of Natural Gas by Turbine Meters, and it was released in 2006.
Turbine meters are widely used for custody transfer of natural gas in natural gas pipelines. They are highly accurate, and can be made as inline meters in sizes that accommodate the large sizes of natural gas pipelines. Many of these pipelines have sizes in the 20 – 42 inch range. Turbine meters may also be less expensive than DP flowmeters for some applications, especially where one turbine meter can replace several DP flowmeters.
Ultrasonic Flowmeters
The first commercially viable ultrasonic flowmeter was introduced in Japan in 1963 by Tokyo Keiki. In the United States, Controlotron popularized their use in the 1970s, especially in clamp-on form. During this period, Panametrics developed both inline and clamp-on technology. Ultrasonic meters send an ultrasonic pulse across a pipe and back. When the pulse travels with the flow, it travels faster than when it travels against the flow. Ultrasonic flowmeters time the difference in these “transit times,” and use this difference to compute flowrate.
Ultrasonic flowmeters received their first approval for use in gas flow measurement from a European group called Groupe Europeen de Recherches Gaziers (GERG). In the mid-1990s, GERG published a report on using ultrasonic flowmeters to measure gas flow. AGA followed suit in 1998 by publishing AGA-9, which describes the use of multipath ultrasonic flowmeters for custody transfer of natural gas. The publication of AGA-9 gave a major boost to the development of multipath ultrasonic flowmeters for gas flow measurement. Suppliers also later developed multipath ultrasonic meters for measuring liquid flows as well.
Multipath ultrasonic flowmeters rely on three or more ultrasonic pulses that cross a pipe and then bounce back to the other side. This is typically done at an angle. Each path is associated with a pair of transducers. One transducer sends the pulse and the other transducer receives it. Multipath meters are more accurate than single and dual path meters because they measure the flow at multiple locations. Mutipath flowmeters typically have four, five, or six paths, although some have been developed with eight or more paths.
The terminology of multipath ultrasonic meters has become somewhat confusing because some suppliers have introduced the term ‘chord’ to describe their multipath meters. The term ‘chord’ refers to an ultrasonic pulse that travels from one side of a pipe to the other. In this sense, a chord is half a path. The new Elster Q-Sonic Plus has 16 chords and six paths. There is nothing wrong with the “chord” terminology, as long as it is understood that a chord does not equal a path.
Many companies are changing from DP and turbine meters to ultrasonic meters because of their marked advantages. Ultrasonic meters are nonintrusive, cause virtually no pressure drop, do not have moving parts, are highly reliable, and are very accurate. Leading suppliers of ultrasonic flowmeters for custody transfer of natural gas are Emerson Daniel, Elster, and SICK. KROHNE has also entered this field. These meters are widely used for pipeline measurement of natural gas. Like turbine meters, they can accommodate the large sizes of gas pipelines, but they can more easily handle particles and impurities in the flowstream than turbine meters. The market for custody transfer of natural gas has become the fastest growing niche in flowmeters, with the possible exception of the market for multiphase meters.
One issue that has remained unresolved is how often ultrasonic flowmeters need to be recalibrated. Some companies look for a period of years, such as five years or seven years, as a guide. So far none of the standards bodies, such as AGA, the American Petroleum Institute (API), or the International Organization for Standardization (ISO) have adopted such a standard. While the number of years would be a convenient guide, there are also diagnostic tests that can be run that may provide a better guide to the need for recalibration of an ultrasonic flowmeter than a standard that is stated in terms of a number of years.
Coriolis Flowmeters
Coriolis flowmeters are the most accurate type of flowmeter made. However, they have an easier time measuring liquid flows than gas flows. Coriolis meters rely on the momentum of the fluid to cause a tube to vibrate. Since gases are less dense than liquids, they have a more difficult time causing the Coriolis meter to vibrate. Even so, Coriolis meters have been developed to reliably measure gas flow. Their accuracy, however, is typically not as high as Coriolis meters for liquids.
One of the major barriers to using Coriolis flowmeters for liquid measurement has been that their line sizes have not been large enough to accommodate the line sizes in the oil & gas industry. For many years, almost all Coriolis meters were for line sizes of six inches and under, and only a few were made for larger line sizes. These were made by a single supplier, Rheonik.
In the past few years, several Coriolis suppliers have begun making Coriolis meters for line sizes above six inches. These include Endress+Hauser, Micro Motion, and KROHNE. In the meantime, GE Sensing has acquired Rheonik, and is continuing to make large size Coriolis meters. Currently, the largest Coriolis meters are made for 16 inch lines.
Because of their accuracy and reliability, these large line size meters may begin to penetrate the market for measuring petroleum liquids. Most of them are designed for custody transfer applications. Coriolis meters are already displacing positive displacement meters for liquid petroleum applications involving downstream delivery of petroleum to tankers, ships, trains, planes, and trucks. It remains to be seen, though, how widely they will be used for upstream oil applications in the oil fields.
Positive Displacement
Positive displacement (PD) flowmeters have been around for several hundred years. They actually capture the fluid in a compartment of known quantity and count how many times this is done. This method allows them to achieve very high accuracy. However, they do have the disadvantage of having moving parts, and are classified as a traditional technology flowmeter.
For gas applications, positive displacement flowmeters are widely used for making gas utility flow measurements. The main type of PD meter used for gas flows is the diaphragm meter. However, diaphragm meters are being replaced by rotary PD meters for many applications. Elster is the leading supplier of positive displacement flowmeters for gas utility purposes.
For petroleum applications, positive displacement meters are widely used in downstream distribution applications involving the delivery of petroleum to trains, ships, planes, trains, and trucks. Their high accuracy and reliability have given them a strong foothold in downstream oil delivery. While they are quite entrenched in oil delivery, Coriolis meters with their high accuracy and lack of moving parts have begun displacing positive displacement flowmeters in the downstream petroleum delivery market.
The Need for Energy Measurement will Continue
While many people are in favor of renewable energy, and the time for renewable energy will come, the reality is that fossil fuels will provide the bulk of the world’s energy needs for at least the next ten to twenty years. As a result, the race to create the most accurate and reliable way to measure oil and gas without breaking the bank will continue. Competition can be very healthy when it encourages companies to innovate and to generate ever better products. That is what is happening today in the flowmeter world, and the result is better and better flowmeters. This is a win-win situation for both suppliers and end-users.
Comments