July 2012, Vol. 239 No. 7
Features
Wireless Sensor Networks Enable Remote Condition Monitoring
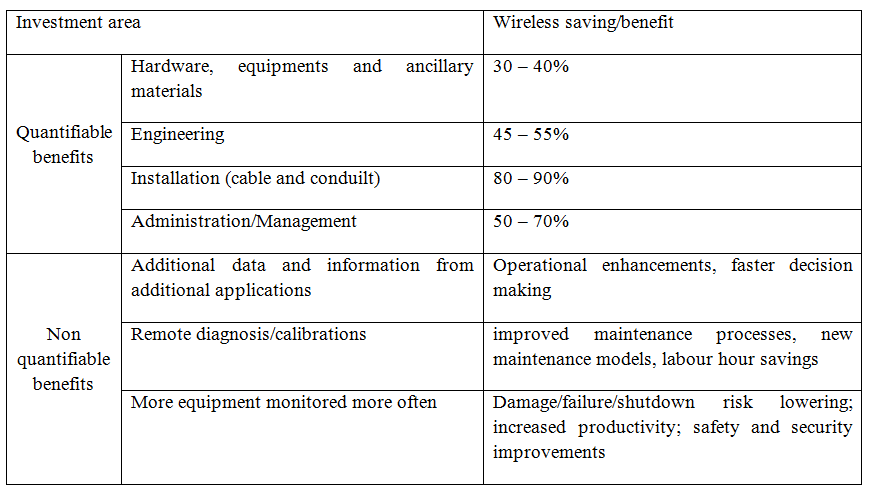
With world population growing at a steady pace (the earth will be home to more than 9 billion people by 2050), global demand for energy is rapidly increasing and the untapped oil reserves lying in Africa are more and more attractive. Africa nowadays supplies around 11% of the world’s oil, but it is expected to pass North America soon to become the third-largest producing area after the Middle East and Central and Eastern Europe.
West and sub-Saharan Africa are exciting lands for exploration, expected to provide great volumes to meet the mounting energy need of fast-growing economies such as Asia. However, increasing volumes don’t necessarily mean increasing profits: oil and gas companies nowadays need to improve control over sites performance and maximize production efficiency if they want to achieve their financial goals. No doubt the evolution of technologies is fundamental to increase production while cutting costs, but relevant results can be obtained by revising data management processes to ensure that decisions are made as quickly as possible and, above all, based on consistent and reliable information.
The increasing need for real-time production monitoring can be satisfied through a comprehensive and secure approach to data collection, transport and analysis. Companies can unlock the value of information coming from the production workflow only if they have a solid infrastructure to collect data from wells, refineries, production plants, pipelines and facilities, and streamline this huge amount of information into their Information and Communication Technologies (ICT) systems, where it will be stored and processed in order to extract key and relevant information to increase efficiency and prevent loss in production.
The challenge of condition monitoring is even more complex if we consider that oil exploration interests tend to move to harsh areas, such as the deepwater fields off West African coasts or the prolific fields in Angola and Nigeria. How to collect and transport data coming from these remote and even hazardous environments? In many cases, wired infrastructures are already in place, and companies are unlikely to upgrade the network or add new data points because of their expensive costs. In a typical oil or gas facility, thousands of sensors and data points are needed to ensure a proper asset monitoring, with hundreds of kilometers of cables used to connect these devices – if we calculate that a new offshore platform has approximately 800 km of wiring and that cable costs alone may vary from US$120 to 6,000 per meter, it is easy to understand why oil and gas companies are eager to protect their past investments and are not open to possible alternatives.
However, being stuck to wired process and sensor networks may prevent companies from successfully facing emerging challenges such as market demands or regulatory changes, which require more performance and efficiency by increasing data collection frequency or installing additional data points (i.e. to monitor emissions or new security parameters). Traditional infrastructures are generally complex to expand or integrate and above all in hard-to-reach locations or harsh environments where wired connectivity and wired network could be difficult, unreliable, too expensive or simply not viable.
Reaching Next Level
Wireless sensor networks offer oil and gas companies immediate and measurable benefits, including improved performance, greater flexibility and reduced costs for installation and on-going maintenance. Wireless data acquisition and transmission allow companies to have deeper, more granular and accurate information from production assets, therefore enabling effective plant monitoring and supporting real-time decisions thanks to the possibility to feed all data directly into corporate ICT systems.
As for the initial investment, a wireless technology project can cost up to 50-70% less than the wired option – considering hardware/material costs, engineering, installation, and global administration and management; in addition, several benefits are interesting to highlight: increased operational reliability and system uptime, increased operator and engineer productivity, improved asset utilization, personnel safety and many others.
Out of several options on the market, the most interesting approach seems to be to go for open standard, scalable and vendor independent wireless networks, in order to offer the best risk/return for the investment. For example, they would not force any change to existing data points, allowing wireless devices to be implemented directly over the current sensor infrastructure, without requiring any infrastructure upgrade. They would allow the building of one network and adding additional applications when needed, at a fraction of the initial cost, in a plug and play mode.
RF penetration, noise immunity, dynamic adaptation of network topology should be evaluated, since both parameters are particularly critical for reliable data transmission in oil and gas plants. Industrial wireless sensor network solutions generally use radio frequency (RF) transmission on 2.4 GHz or above, which often proves to be inefficient in congested environments and features a low penetration factor. Solutions based on Internet Engineering Task Force (IETF) open standards – such as 6lowPAN – on sub-GHz Industrial, Scientific and Medical (ISM) band with full mesh topologies should be preferred, since they grant higher penetration, noise immunity and dynamic adaptability to changes in the surrounding environments.
Other benefits of wireless sensor network solutions are more difficult to quantify, but still worthy to list: as the system grows and more points are monitored and additional applications added, more data will be added into the company knowledge systems; if the choice has been for a bidirectional, M2M wireless network, instrument calibration and equipment diagnosis can be performed remotely and more often – thus reducing equipment failures or forced shutdowns.
To further support the above listed benefits, most valid wireless sensor network solutions require no software to install, no heavy server side operations, little maintenance – in brief, they provide almost unmanned deployment coupled a self-organizing, self-healing, adaptive and fault tolerant network. This is important for all industries, but particularly relevant for oil and gas companies considering the harsh locations where plants are usually installed, shrinking workforce and budget constraints, no complexity in implementation and roll out and maintenance processes can be afforded.
Authentication, authorization, strong encryption – in a word, security – complete the set of features together with extended range of temperature and hazard/explosion safe hardware, web-based management applications to further streamline configuration and management, and ultra low power technology coupled with long life battery operation (more than eight years) further help to streamline labor and personnel intervention, and overall efficiency.
One final remark concerns the choice of connectivity technologies: selecting a wireless sensor network that is ready to scale from narrow band to broad band for data uplinking to the HQ is an attractive alternative to having highly reliable connectivity in typical oil and gas plant locations, where landlines are unreliable, difficult to access or non-existent. Working with a satellite network provider – and better yet — with a virtual network operator, is an interesting option to consider to develop tailored solutions and, if necessary, hybrid infrastructures for business continuity applications and redundant communications.
The oil and gas industry represents an example of very high complexity in real-time production and condition monitoring, where wireless sensor network solutions can be particularly successful in providing an effective approach to data collection and transport for overall plant efficiency. Thanks to innovative wireless sensor network technologies, oil and gas companies have the opportunity to leverage all the value of information coming from their assets and production workflow. However, lessons from this market are useful and applicable for all industrial organizations having dispersed plants and facilities to be monitored.
Author
Gianni Minetti is president and CEO of Paradox Engineering SA, and founded the company in 2005.
Comments