August 2013, Vol. 240 No. 8
TechNotes
Dry Fit Assembly At WeldFit Guarantees Alignment
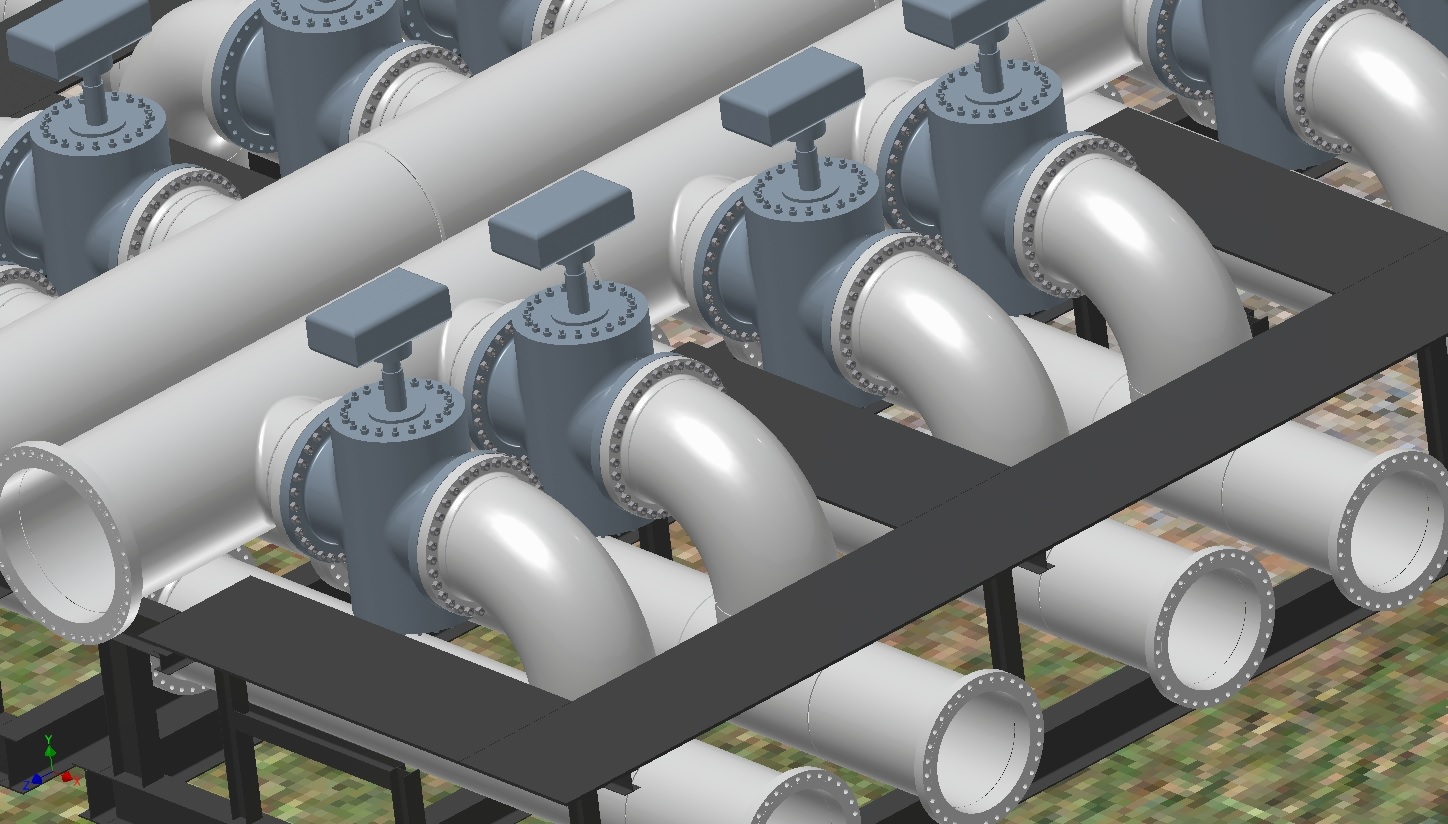
WeldFit Energy Group completed a valve manifold assembly for a tank farm expansion at a terminal near Edmonton, Alberta. The valve matrix is comprised of eleven 30-inch main line spools with various sizes of extruded inbound and outbound headers.
The extruded outlet design of the headers allows for maximum flexibility of outlet placement and reduces the tolerance variation associated with normal butt weld fittings. Meeting all CSA specifications, assembly was designed, fabricated, dry fit, inspected, hydro-tested and painted in sections before sending to the jobsite in Canada.
The dry fit assembly process ensured a proven fit and alignment. All fittings were placed in a mock-up assembly prior to shipping. Field crews only had to place the fabricated assemblies in their locations upon arrival. No welding or fabrication of the valve manifold parts was required in the field, resulting in reduced field assembly time and lower costs.
Houston-based WeldFit also provides corrosion-resistant weld overlay and has a fabrication facility with ASME-qualified welders and the ability to machine large and small specialty parts.
For further information, visit www.weldfit.com.
Comments