November 2013, Vol. 240 No. 11
Features
Innovation: The Mothers Milk Of U.S. Energy Advancement
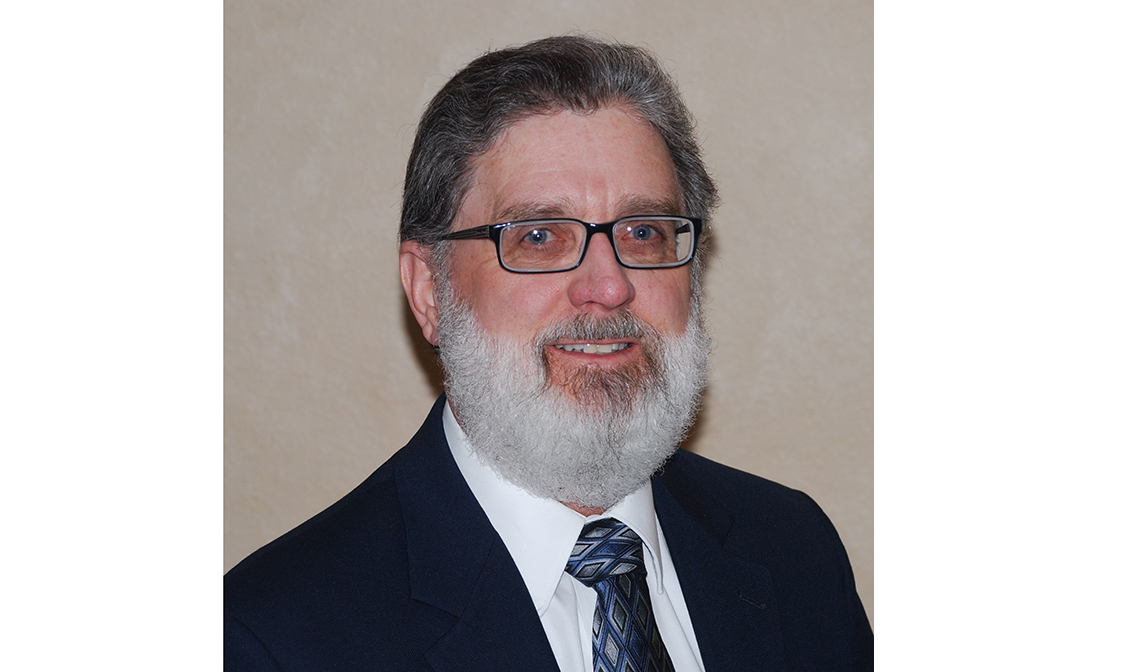
“Our business remains a technical business that still has to be based and driven on sound science.” –Lee Tillman, new CEO, Marathon Oil Corp.
Life in the natural gas pipeline business unit at the giant San Francisco-based combination utility Pacific Gas and Electric Co. (PG&E) changed irreversibly after Sept. 9, 2010 when one of its 30-inch diameter transmission lines ruptured and exploded in a quiet residential section of San Bruno, CA, about 10 miles south of the city. Since then, PG&E has spent billions of dollars trying to recover while it continues to be a public punching bag for regulators, politicians and consumers.
In the midst of this continuing free-for-all early in the summer, Mike Florio, one of five members of the California Public Utilities Commission (CPUC), which has been harsh on PG&E, uncharacteristically had something good to say about the beleaguered utility. His unsolicited praise was indicative of what the energy sector is doing right these days – applying advanced technology to improve the safety and efficiency of field operations.
Florio, who has had an adversarial relationship dating back 30 years with PG&E as a former top attorney for a major California utility consumer watchdog group, TURN, was effusive in publicly praising the utility for its partnership reached earlier in 2013 with Germany-based 3P Services to develop a custom smart pig tool for inspecting transmission pipelines. Florio was impressed with the tool’s customization and advanced technology.
“This customized smart pig is unique, and unlike standard inspection tools, this tool can navigate tight bends and turns in the pipelines ranging from 30 to 36 inches in diameter,” the California regulator told his colleagues at a CPUC business meeting. “It can provide highly sophisticated data to PG&E on pipeline conditions.”
What Florio was noticing is going on throughout the oil and gas sector these days, accounting for the robust growth in domestic U.S. oil and gas supplies, and making previously cumbersome work in the field more efficient and economic. It is simply a small revolution in applying advanced technology and worker training, and it is something the industry is taking with pretty much a ho-hum attitude, or with a measure of secretiveness that bids to keep proprietary advantages in place.
Among the industry research centers, the Des Plaines, IL-based Gas Technology Institute (GTI) has made data and integrity management a core focus for its work. GTI engineers tout their initiatives for increasing the quality and accessibility of data and helping gas pipeline operators meet their integrity management requirements. Examples are the enhancement of field data collection, better technologies for tracking pipeline assets and better ways to prevent excavation damage to these energy arteries.
“You see a lot of emphasis on the integrity area; we have a very large network of pipes in the ground, and it is not going away any time soon,” said Cliff Johnson, president of the Virginia-based Pipeline Research Council International (PRCI).
“Our members [70] want to make sure those pipes stay in place as long as possible so our research is geared to making sure that things we have working well continue to do so as long as possible,” he said.
The U.S. industry is beginning to focus on construction of new systems and what those systems are going to look like when the industry starts building again, Johnson said. “In other parts of the world – in China and Europe – there is more growth and expansion of the systems, so the research we are going to be bringing to the table real soon will look a lot different involving new construction techniques and new higher grade steels to be able to move to the next level.”
The pipe industry in the United States is primed to move from maintenance and upgrade emphasis to building a lot of new systems, according to the PRCI leader.
“Any changes in pipeline systems are more evolutionary,” said Rod Osborne, manager of the E&P pipeline group at Battelle’s Columbus, OH headquarters. “Operators are using some better materials, some better manufacturing methods and welding methods to create the pipelines. And they are using better coatings, but none of this was really driven by the shale boom.”
GTI engineers disagree somewhat, citing ongoing pilot tests on advanced means for sulfur removal in the midstream and better purification of gas in the pipeline or in floating liquefied natural gas production facilities.
“A novel sulfur removal process is ready for pilot plant testing that will treat tonnage levels of H2S, replacing acid gas removal, sulfur recovery and tail gas treating processes in one step,” GTI engineers contend. Separately, GTI is partnering with PoroGen Corp. to develop a small-scale, lower cost gas purification technology.
While they are doing some great things, such industry stalwarts as Schlumberger, Halliburton and Continental Resources are reluctant to talk in much specificity about their latest advancements in equipment, processes and training. Regardless, the advances are taking places as verified by energy officials such as Lynn Helms, director of the North Dakota Department of Mineral Resources, overseeing the oil and natural gas liquids boom in his state.
Helms talked about various industry responses to North Dakota’s stubborn wellhead flared gas problem caused by runaway oil and NGL production that has outpaced the industry’s ability to build more processing, pipeline and gathering infrastructure to handle the record production growth. Companies like Continental are leading efforts to lower the percentage of flared gas, which has hovered around 30% for the past few years.
Fertilizer plants that need large quantities of natural gas as a feedstock, oilfield power generation schemes and natural gas-fired hydraulic fracking equipment are all being pursued to find outlets other than flaring for the associated gas produced with robust oil supplies. North Dakota has formed an Oil/Gas Research Council, composed mostly of industry representatives, but as an extension of the North Dakota Industrial Commission, of which Helms’ DMR is part.
Last summer, Helms was looking forward to the research council vetting a number of new projects aimed at cutting flaring volumes, which he predicts will be down to 10% or less in the next few years.
“Routinely, we have people bringing us new technology, and the market responds to companies out there with very innovative products and ideas,” said Norwegian-based Statoil’s Kevin O’Donnell, vice president for drilling, well and operations support in the U.S. onshore. Statoil has made the application of technology advances a strategic part of its growing operations in U.S. shale plays in the Bakken, Marcellus and Eagle Ford formations.
“We want to really make sure we are on top of what [technology advances] are out there, and using them in the best way we can for our operations and adding value,” said O’Donnell, noting that the company’s Houston office includes an internal research group that works exclusively on U.S. shale-related technology developments.
“Oilfield services giant Baker Hughes Inc. BH [a cooperative technology partner with Statoil] has led the way in several areas in recent years,” North Dakota’s Helms said. One program integrated the use of natural gas in bifuel hydraulic fracturing equipment to replace the more costly and polluting diesel-powered units. A BH business unit, Baker Hughes Oilfield Operations, applied the bifuel fracking pumps and found improved operating efficiency, lower costs, and reduced health, safety and environmental impacts.
Mike Davis, BH’s president for pressure pumping in U.S. land operations, called the environmental benefits “significant,” citing reduced emissions from the engines driving the stimulation pumps and less fuel required to keep the pumps going. Safety is also enhanced, Davis said, because with bifuel equipment there are no demands for refueling during operations.
At the Colorado Oil and Gas Association (COGA) annual summit this past summer, a panel of experts concluded that while technology advances have driven the shale boom as they have driven past booms during the industry’s 150-year history, there is still more to be discovered and applied.
Liberty Resources LLC CEO Chris Wright thinks North America’s shale revolution has a long way to go with advances in nonconventional wells and hydraulic fracturing only starting to build momentum. Statoil’s O’Donnell shares the view with other industry and research executives that it is still very early in the game with U.S. shale production.
A Halliburton Co. Fellow who worked for affiliate Pinnacle Technologies, Norm Warpinski, said fracking becomes more complex in accordance with the level of complexity of the reservoir being worked. He is working to develop new tools and analyses for frack mapping, reservoir monitoring, frack designs and reservoir development. Even with the continuing advances, Warpinski sees many “uncertainties” still surrounding unconventional drilling, a further incentive for continued innovation in the industry.
GTI, along with the late industry hydraulic fracturing pioneer George Mitchell and the U.S. Department of Energy, has been one of the early research organizations helping to unlock unconventional resources, which accounted for nearly 60% of the U.S. domestic gas supplies. GTI was one of the key organizations in helping the shale boom develop as a result of the integration of three technological advances in: horizontal drilling, hydraulic fracturing and seismic imaging.
“You put those three things together and you have gas coming out in big quantities,” said the research engineering team at GTI.
Those gas researchers reason that the shale space is ripe for continuing technology advancements simply because there are tens of thousands of wells yet to be drilled. North America has three to four more decades of drilling, so the value of any technical solutions is multiplied by tens of thousands of wells over three or four decades, according to GTI.
GTI’s working list of R&D areas to focus on include various operational, economic, and environmental issues tied to the shale boom – micro-seismic hydraulic fracturing, fracking design modeling, measurement-while-working (MWD) technologies, along with surface, subsurface, water, waste management and air emissions mitigation technologies.
“We’re focused on R&D work necessary to develop the next generation of shale gas technology for increased efficiency, safety and environmental sustainability,” GTI’s engineers maintain.
Innovations that Warpinski sees coming, include: (a) fiber optic technology using distributed optics and distributed temperature sensing to enable “micro-deformation” of surface tiltmeters and downhole tiltmeters that measure small changes from the horizontal level, either on the ground or in structures; (b) tracers that rely on chemicals and radioactive tracers; and (c) pressure interference using tiltmeters, adding micro-seismic tools for analyzing a formation.
With the targets of E&P companies getting ever-deeper into formations, it is going to take better training of personnel, but there is also a crying need for new equipment to deal with harsh environments and greater depths, according to Torrance Haggerty, Battelle’s oil/gas program leader in Houston. “There is more automation throughout all of the new equipment being used.”
More automation is coming, he thinks, for both risk mitigation and integrity management. “That’s quite important, especially when you consider both the people and technology needs,” he said.
“It is more what you put into the well bore that is going to speak to the successes and the result you bring out of that hole,” Haggerty said. He thinks improved training is needed to provide a better overall understanding of the technologies and capabilities that are coming to bear.
On a quarterly earnings conference call last summer, Continental’s COO Rick Bott said the company’s ongoing aggressive test drilling in the Bakken/Three Forks has been made possible by “cutting edge micro-seismic technology.” Bott said it gives his company “additional data on how we are assessing a given reservoir.”
“The micro-seismic program has set many firsts for our industry,” Bott said. “As far as we can determine, ours is the first monitoring program to date involving unconventional reservoirs worldwide.”
He offers examples, such as Continental’s ability to simultaneously monitor hydraulic fracturing through three surrounding horizontal well bores. This provided the company what Bott referred to as “exceptional triangulation capabilities” for more accurately mapping fractures propagated during the fracking process.
There is a need to make the facilities more ‘operator friendly’ and that pushes the need for technology that calls for building smarter, more efficient facilities, said Jim Witte, a staff engineer at the Southwest Research Institute (SwRI) in San Antonio, TX. He called these “self-prompting” technologies that alert operators of things they need to pay attention to.
“A lot of the technologies being employed are using the micro computer technologies in various operating devices,” Witte said. “That is a trend that has been going on for several years now.” He offered some examples: ultrasonic meters for gas and liquids measurement, technologies that have embedded computers in them, with some units having more than one.
“Unconventional reservoirs ultimately require unconventional characterization,” said John Harju, associate research director for the Energy and Environmental Research Center (EERC) at the University of North Dakota, explaining to his listener that the work of his center is closely aligned with the oil/gas industry. Harju stressed that the characterization techniques developed over the past 150 years in the petroleum geology space all apply to conventional reservoirs.
“They really aren’t applicable to shales. So we do a lot of work to help companies better understand how the rocks behave when various stresses are applied to them through different drilling and completion technologies.” Harju and his fellow researchers have looked at a whole suite of technologies that might be contemplated for reducing wellsite flaring of associated gas as an example. “That is a space we have been very busy in,” he said.
In conjunction with Continental Resources and other private sector, state and federal government entities, the EERC evaluated preliminary laboratory testing and eventual field testing of gas-powered drilling operations. The results of its 47-day demonstration program showed that using wellhead gas in bifuel applications works well. It can power a drilling rig while decreasing overall diesel fuel use, fuel cost and truck transport of liquid fuel “without adversely impacting drilling operations.”
Implemented more broadly, the bifuel approach applied to 200 rigs in the Williston Basin could result in eliminating up to 1.8 Bcf of wellhead gas that would otherwise be flared, saving 18 million gallons of diesel fuel, and cutting $72 million from annual drilling fuel costs.
Ultimately, the key for Harju, and Battelle’s Haggerty and engineers at GTI is how operators are engaging their respective shale formations. In conventional operations, only about 15% of the resources in place will get extracted, in the unconventional plays, up to 80% of the resources are thought to be extractable.
“Well design is being turned into an automated process, using sensors at the wellhead and in the well bore,” Haggerty said. “Now we can assess the ongoing work without having to shut down operations, so the key to design is automation.” The longer-term key is to transfer the onshore advancements, including chemical innovations, to a deepwater, offshore environment, he said.
Besides well design, two other areas Haggerty thinks the industry generally and Battelle in particular, will be focused on in the onshore space are flowback and produced water, along with enhanced oil recovery (EOR). Battelle and its subsidiary, Winner Water Services, is promoting some of its own in-house developed technologies for recycling produced water and advancing EOR processes with carbon dioxide and so-called microbial EOR (MEOR).
That’s another area to keep an eye on – the transfer of “tool kits” developed in other industries, such as health care, chemicals, advanced materials and environmental sciences into the oil/gas industry. Many of the organizations contributing to this article hope to lead those technology transfers.
This is what happens when there is a rebirth of an industrial sector, such as shale oil and gas plays have experienced. Many new faces and ideas have come calling as a result. How the industry answers is still to be determined.
Rod Osborne, Battelle Institute, Columbus, OH: “Operators are using some better materials, some better manufacturing methods and welding methods to create the pipelines. And they are using better coatings, but none of this was really driven by the shale boom.”
Cliff Johnson, PRCI: “You see a lot of emphasis on the integrity area; we have a very large network of pipes in the ground, and it is not going away any time soon.”
Mike Florio, CPUC: “This customized smart pig is unique, and unlike standard inspection tools, this tool can navigate tight bends and turns in the pipelines ranging from 30 to 36 inches in diameter. It can provide highly sophisticated data to PG&E on pipeline conditions.”
Rick Bott, Continental Resources: “The micro-seismic program has set many firsts for our industry. As far as we can determine, ours is the first monitoring program to date involving unconventional reservoirs worldwide.”
Jim Witte, SwRI: “A lot of the technologies being employed are using the micro computer technologies in various operating devices. That is a trend that has been going on for several years now.”
Lynn Helms, State of North Dakota: Predicts new projects aimed at cutting flaring volumes will reduce problem to 10% or less in the next few years.
Kevin O’Donnell, Statoil: “Routinely, we have people bringing us new technology, and the market responds to companies out there with very innovative products and ideas. We want to really make sure we are on top of what [technology advances] are out there, and using them in the best way we can for our operations and adding value.”
Mike Davis, BH: Environmental benefits “significant,” citing reduced emissions from the engines driving the stimulation pumps and less fuel required to keep the pumps going. Safety is also enhanced, Davis said, because with bifuel equipment there are no demands for refueling during operations.
Torrance Haggerty, Battelle Institute, Houston: “Now we can assess the ongoing work without having to shut down operations, so the key to design is automation.”
John Harju, EERC: “Unconventional reservoirs ultimately require unconventional characterization. They really aren’t applicable to shales. So we do a lot of work to help companies better understand how the rocks behave when various stresses are applied to them through different drilling and completion technologies.”
Norm Warpinski, Halliburton: Even with the continuing advances, Warpinski sees many “uncertainties” still surrounding unconventional drilling, a further incentive for continued innovation in the industry.
Chris Wright, Liberty Resources: North America’s shale revolution has a long way to go with advances in nonconventional wells and hydraulic fracturing only starting to build momentum.
Author: Richard Nemec is a West Coast Contributing Editor for P&GJ. He can be reached at: rnemec@ca.rr.com.
Comments