September 2013, Vol. 240 No. 9
Features
MSC Unleashes Safety Report On Pipeline Boring Practices
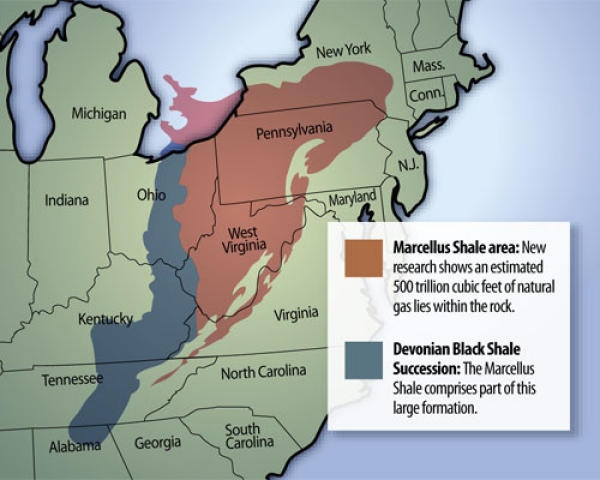
The Marcellus Shale Coalition (MSC) released “Recommended Practices for Pipeline Boring,” the seventh in a series of content-rich guidance documents developed by the coalition’s various subject-specific committees.
While pipelines are usually installed by digging a trench and placing the line deep underground there is an alternative pipeline practice called pipeline boring. Pipeline boring, also referred to as horizontal directional drilling (HDD), is a trenchless practice that is used when installing a line where trenching isn’t feasible, such as under highways, railways and water bodies.
The MSC gives six cardinal rules for pipeline boring, first and foremost being planning. A feasibility study must be performed before initiating a pipeline bore. The land’s elevation, structural features and the presence of any existing surface features, such as utility lines, must be thoroughly evaluated. A geotechnical investigation may be necessary if damage has occurred in the targeted area to prevent the pipeline from shifting with the soil, settling, or becoming buoyant, stresses the report.
Once the feasibility study meets required standards, the path of the bore must be surveyed. The survey delineates the spatial limitations of the right-of-way and any extra workspace that will be needed on the entry and exit sides of the bore, says the report. The bore profile must be planned after the right-of-way survey. All surrounding buried utilities must be accounted for so the bore doesn’t interfere with existing lines causing safety hazards.
The MSC says all of the proper permits and authorizations must be earned prior to construction, most notably a green light from the Federal Energy Regulatory Commission. The final portion of the planning stage is developing an alternative backup plan in case the initial plan goes awry, referred to as a contingency plan.
The second stage of pipeline boring is the kick-off of construction. First, a small-diameter pilot hole is drilled along the bore path. The pilot hole’s diameter is enlarged as necessary to serve the pipeline(s), which may entail multiple “reaming” passes to accommodate the bore, according to the report.
Pipeline inspection is a crucial step in the construction process. Analysis of coating damage to the pipe, a radiographic inspection to measure the thickness of the welds and a hydrostatic test to assess pipeline durability for potential leaks are all a necessary part of the inspection. Once all is clear and the pipeline passes inspection, the pipeline is then pulled into the pre-drilled pilot hole. The MSC stresses that a post-installation inspection of the pipeline must also be executed following the initial pipeline inspection tests. If the boring is done underwater, the State Regulatory Agency (SRA) may require advance notice prior to installation, says the MSC.
The boring fluid or boring mud is a mixture of about 4% bentonite clay, a non-hazardous matter, and 96% fresh water, according to the report. Pipeline boring flushes boring fluid through drilling equipment on the surface of the land through the underground drill pipe and then back to the surface through the area between the drill pipe and bore hole sides, also referred to as the “drilled annulus.” The report states that the drilled annulus becomes the path of least resistance for the boring fluid, but at times a fracture or crack in the bore’s drill path may be a catalyst for circulation loss. If circulation loss occurs, the boring fluid will enter a new path of least resistance and cause a leak, called an inadvertent return.
An inadvertent return is a chief environmental concern linked with pipeline boring. If an inadvertent return takes place, the boring mud should be restrained and cleaned up immediately before its spreads into other areas. Tools necessary to clean up an inadvertent return are hay bales, pails, sand bags, silt fences, push brooms, plastic sheeting, pumps, shovels, storage tanks, squeegees and a vacuum truck, lists the report. If an inadvertent return spills into a waterway, for example, it could negatively affect the plant and aquatic animal life, the MSC warns. The report urges construction personnel to strictly monitor the ground’s surface around the bore to steer clear of loss of circulation to prevent any hazardous leaks.
If the boring fluid spills into a waterway, it will likely need to be reported to the SRA immediately. The report says that in Pennsylvania the spill must be filed with the Department of Environmental Protection. The MSC stresses that all affected water users and downstream landowners must swiftly be informed of the situation. All contact information in the case of an inadvertent return in a waterway must be documented in the company’s initial contingency plan.
The MSC says that if the spill cannot be adequately cleaned up and directed, the borehole can be sealed, another hole can be drilled along a different pathway or all boring activity must come to a halt and be abandoned. To abandon a borehole the MSC gives the following guidelines: thick drilling fluid should be driven into the hole as drilling equipment is removed and a cement grout should be used as a plug; soil should be used within 10 feet of the entry and exit holes to fill the bore; and the entry pit of the bore should be refurbished back to its original state after abandonment.
“Building the required pipeline infrastructure to safely transport natural gas from the wellhead to the marketplace is a huge undertaking and one that requires much due diligence,” said Coalition CEO Officer Kathryn Klaber. “These “Recommended Practices for Pipeline Boring” provide operators with a road map to ensure that these projects are constructed with the highest degree of integrity, that operators plan appropriately prior to construction and that contingency plans are in place.”
Continued Klaber, “While bentonite is a non-hazardous compound that has many common applications, it’s important that the public has a good, fact-based understanding of this process, and that operators plan accordingly should they experience an inadvertent return during pipeline boring. MSC member companies are dedicated to operating transparently and in a safe and environmentally responsible manner.”
Comments