July 2014, Vol. 241, No. 7
TechNotes
Porous Material Polymerizes Carbon Dioxide At Natural Gas Wellheads
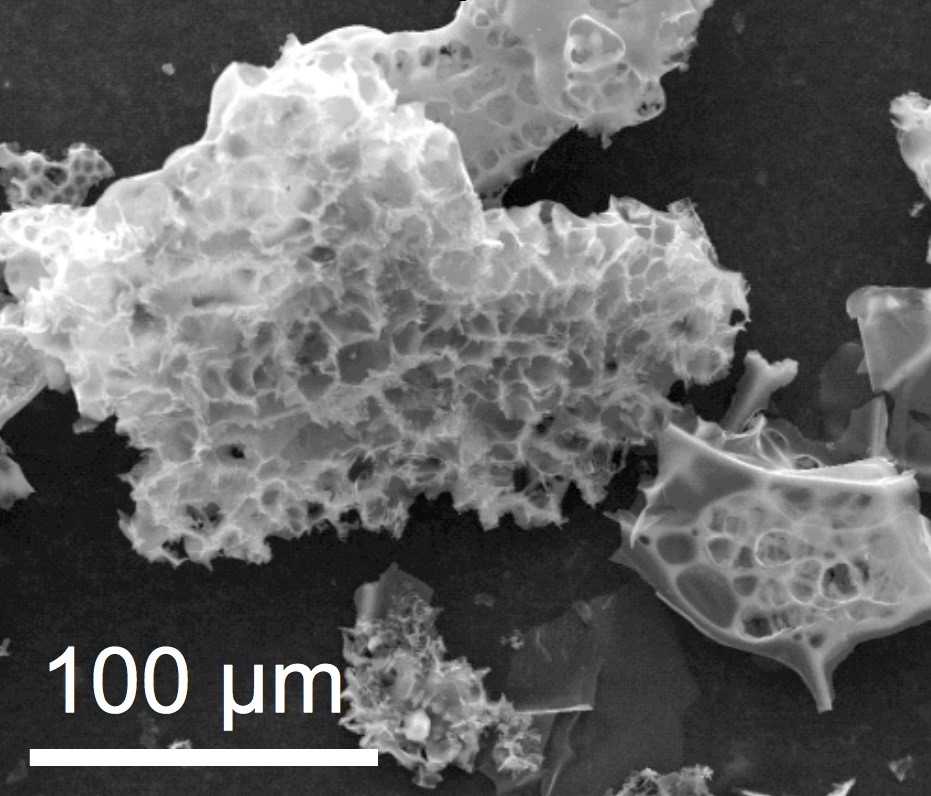
Rice University scientists have created an earth-friendly way to separate carbon dioxide from natural gas at wellheads.
A porous material invented by the Rice laboratory of chemist James Tour sequesters carbon dioxide, a greenhouse gas, at ambient temperature – with pressure provided by the wellhead – and lets it go once the pressure is released. The material shows promise as a replacement for more costly and energy-intensive processes.
Development of cost-effective means to separate carbon dioxide during the production process will improve this advantage over other fossil fuels and enable the economic production of gas resources with higher carbon dioxide content that would be too costly to recover using current carbon capture technologies, Tour said. Traditionally, carbon dioxide has been removed from natural gas to meet pipelines’ specifications.
The Tour lab, with assistance from the National Institute of Standards and Technology (NIST), produced the patented material that pulls only carbon dioxide molecules from flowing natural gas and polymerizes them while under pressure provided by the well.
When the pressure is released, the carbon dioxide spontaneously depolymerizes and frees the sorbent material to collect more. All of this works in ambient temperatures, unlike current high-temperature capture technologies that use up a significant portion of the energy being produced.
“If the oil and gas industry does not respond to concerns about carbon dioxide and other emissions, it could well face new regulations,” Tour said, noting the White House’s recent National Climate Assessment and new rules to cut carbon pollution from the nation’s power plants.
“Our technique allows one to specifically remove carbon dioxide at the source. It doesn’t have to be transported to a collection station to do the separation,” he said. “This will be especially effective offshore where the footprint of traditional methods that involve scrubbing towers or membranes are too cumbersome.”
The process will allow companies to pump carbon dioxide directly back downhole, use it for enhanced oil recovery to further the release of oil and natural gas or package and sell it for other industrial applications.
The Rice material, a nanoporous solid of carbon with nitrogen or sulfur, is inexpensive and simple to produce compared with the liquid amine-based scrubbers used now.
Rice graduate student Chih-Chau Hwang, lead author of a paper on the research, first tried to combine amines with porous carbon, but said he still needed to heat it to break the covalent bonds between the amine and carbon dioxide molecules. He also considered metal oxide frameworks that trap carbon dioxide molecules, but that process captured the desired methane as well and was far too expensive.
The porous carbon powder he settled on has massive surface area and turns the neat trick of converting gaseous carbon dioxide into solid polymer chains that nestle in the pores.
“Amines are corrosive and hard on equipment,” Tour said. “They do capture carbon dioxide, but they need to be heated to about 1400 C to release it for permanent storage. That’s a terrible waste of energy.”
The researchers treated the carbon source with potassium hydroxide at 6000 C to produce the powders with either sulfur or nitrogen atoms evenly distributed through the resulting porous material. The sulfur-infused powder performed best, absorbing 82% of its weight in carbon dioxide. The nitrogen-infused powder was nearly as good and improved with further processing. Tour said the material did not degrade over many cycles.
Apache Corp., a Houston-based oil and gas exploration and production company, funded the research at Rice and licensed the technology. Tour expected the process to take time and more work on manufacturing and engineering aspects to commercialize.
Comments