December 2015 Vol. 242, No. 12
Features
Steel vs. Plastic Pipe: Some Thoughts to Consider
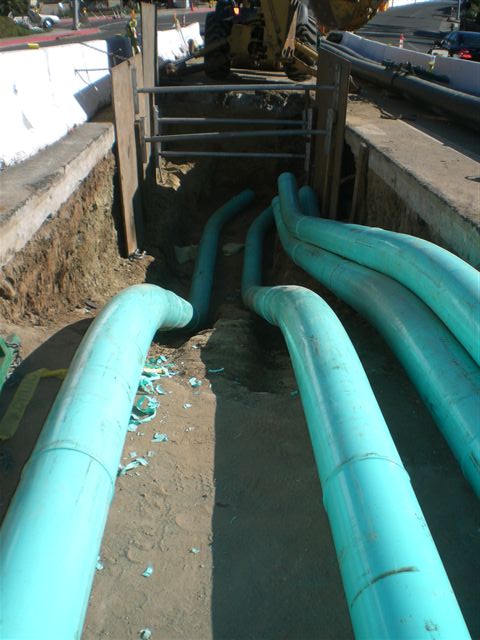
With oil prices hovering near $50 a barrel for the first time since the crash of 2008, oil and gas producers are watching to see if this is a temporary blip from the $80-100 range or closer to a “new normal” in which prices stay below $60.
For some, this price uncertainty has meant scaling back production, exploration and drilling with the looming possibility of halting some activities all together.
Traditional oil and gas companies are not the only ones feeling the squeeze. The Wall Street Journal recently reported that the U.S. Steel Corporation, which depends heavily on oil and gas companies to buy its steel pipe and tubes, might have to stall its Lorain, OH plant in March and lay off 614 of the plant’s 700 workers. The company also said it could temporarily end work at a plant in Houston, affecting 142 workers. Examples like this will be a hard hit for many workers across the country.
While methods vary from company to company, one thing holds true for oil and gas well operators no matter the price of their product: for revenue to keep flowing, production needs to occur. Price pressures are causing companies to look for steps in the process that can be reworked to save time and money.
One area for improvement is the installation of gathering lines that connect wells to production facilities. Because every day that a well is not producing is a day that a company is missing out on revenue, it is important that gathering lines are fast, easy and safe to install.
While gathering lines are traditionally made of steel, companies have been using plastic pipe as an alternative for years. With price uncertainty and the push for immediate revenue, the time is right to re-examine the question of steel or plastic to see if the oil and gas industry should change its status quo.
Though the core functionalities of each of the respective pipes are the same, their history and makeup are not. Before the invention of pipe bending for oil pipelines, oil was transported from wells to railway stations by horse in converted wooden whiskey barrels. According to Pipeline Equities, it is because of these that we still measure oil by the barrel.
With wood and metal pipelines replacing barrels in 1865, the steel pipeline has deep roots in the U.S. oil and gas industry. Of the more than 185,000 miles of liquid petroleum pipelines, nearly 320,000 miles of gas transmission pipelines, and over 2 million miles of gas distribution pipelines, the overwhelming majority are made of steel.
Steel pipe may still be the go-to choice for oil field operators but plastic pipe is growing in popularity. Initially developed in the early 1990s, reinforced thermoplastic pipe (RTP) is a generic term referring to a pipe constructed of plastic polymers and reinforced with Aramid, polyester, or glass.
It was developed to replace medium-pressure steel pipe in response to growing demand for non-corrosive conduits for application in the onshore oil and gas industry, particularly in the Middle East. The combination provides a corrosive-resistant pipe for oil and gas applications with the strength to replace steel pipes in low- and medium-pressure situations.
While both get the job done, there are several benefits to both plastic and steel pipe for oil and gas production. RTP is lightweight and flexible, whereas steel is heavy, requiring much more manpower, equipment and energy to transport and install.
Unlike RTP, the strength of steel makes it difficult to bend and manipulate. RTP is also more cost-effective than steel pipe and can save companies from spending unnecessary dollars, allowing companies to cut costs instead of cutting activity. With spending on oil exploration and production expected to fall 20% this year compared to 2014 according to the OCTG Situation Report, making the move away from steel can provide significant bottom-line benefits.
Arguably, one of the most significant advantages to RTP is its highly corrosion-resistant components. Plastic pipe is low maintenance and will never fail due to rust-like steel pipe can. In fact, corrosion inhibitors are never needed as they are with traditional steel pipelines.
While steel can deliver unmatched temperature and pressure service levels, RTP has made advances in this area that make it usable in a majority of use cases.
There are several prominent players in the plastic pipe space that are making major headway against the steel industry with RTP and composite pipe. While ultimately it’s up to each field operator to determine whether plastic or steel pipe works best for their business plan, it’s easy to see the benefits in using RTP piping: speed to get wells flowing and producing for its operators, lower operating costs, increased corrosion resistance, and easier to work with and transport.
With the uncertainty in the oil and gas industry as well as related industries (like steel), it’s a smart to consider plastic pipe for gathering lines and other applications in the oilfield to keep production flowing at a lower cost.
Comments