July 2015, Vol. 242, No. 7
Features
Measuring Hydrocarbon Fluids Using Wet Gas, Watercut and Multiphase Meters
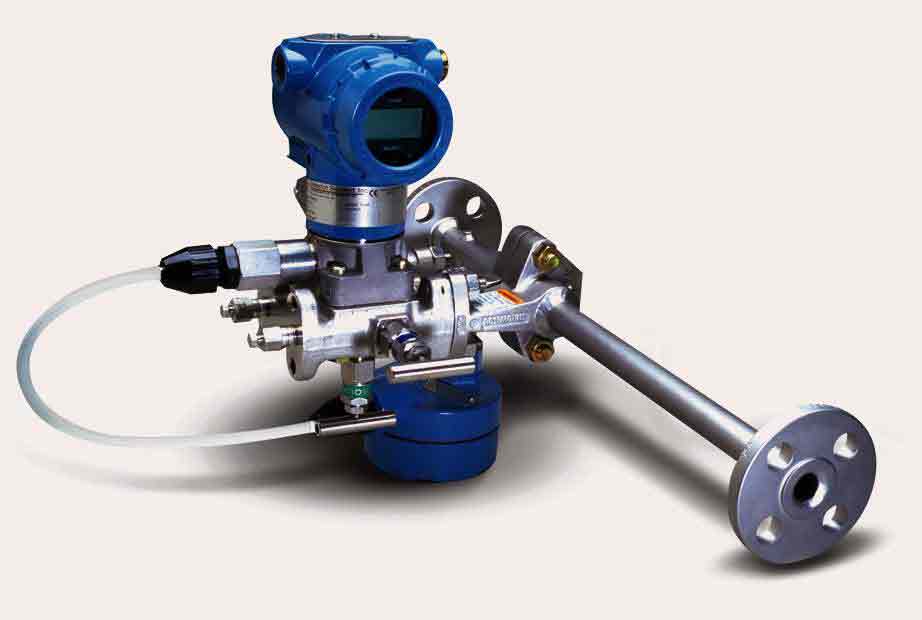
Oil and natural gas are two fossil fuels that account for a great deal of the energy used in the world. What they have in common is that they are found deep in the earth, sometimes underneath the ocean bed, and they have to be extracted through the drilling process. The fluids that come out of these wells generally include a mixture of gas, water, and oil. In addition, they may contain sand and sediment. These components eventually have to be separated and measured before they can be usefully processed. The instruments that play the main roles in this separation and measurement process include separators, wet gas meters, watercut meters, and multiphase meters.
Land-based, Offshore and Subsea Wells
Crude oil and natural gas are found in many locations in the ground. They are found by drilling wells, which are either on land, offshore, or subsea. Drilling on land is less complex than subsea drilling. Subsea drilling is more difficult and expensive than drilling on land. Oil was first discovered on land in 1859 near Titusville, PA by Col. Edwin Drake, who drilled a well to a depth of 69 feet. Offshore drilling, which is typically drilling within sight of land, began in the 1890s. The first subsea oil well was drilled in the Gulf of Mexico in 1947.
The push for new sources of oil was brought about in part by the increase in fuel demand after the end of World War II. The day after the war ended, gasoline and fuel rations were lifted. This resulted in a tremendous increase in the demand for gasoline and other petroleum products, as Americans began driving freely again. New roads were built, and suburban neighborhoods were developed. This increase in fuel demand led companies such as Kerr-McGee Oil Industries and Shell to push for new sources of supply. The first subsea oil well was drilled in the Gulf of Mexico in 1947.
Separators: First Step in Measurement
Whether oil and gas originates beneath the ocean, within sight of land, or on the land, it has to be measured once it reaches the surface. Because the fluid coming out of a well is typically a mixture of varying amounts of oil, water, and gas, various means are used to measure it. These include the use of separators, wet gas meters, watercut meters and multiphase meters.
One of the most common approaches to measuring the fluid from a well is to use a separator to physically separate the fluid into three or even four separate components. Three phase separators are used to separate the fluid into gas, oil and water. Four phase separators are used when, in addition to gas, oil and water, the fluid also contains sand or other solid particles. Separators can be installed either horizontally or vertically.
The principle of operation of a three-phase separator is fairly straightforward. A three-phase separator relies on gravity to physically separate the components of the fluid. As the fluid enters a horizontal separator, the gas, which is lighter than either the oil or water, is routed upwards into a separate section of the separator. This can be done through an inlet diverter. The liquid, which is a mixture of oil and water, is routed to the bottom of the separator. Given sufficient time, the oil forms a layer above the water.
With the three components of the fluid in physically separate locations, each fluid type is then routed out of the separator. The water is drained out through the bottom of the separator to a water-processing system. The gas is routed through the top of the separator to a gas-processing system. Likewise, the oil is routed separately to an oil-processing system. In most cases, the water, gas and oil are measured by a single-phase flowmeter to determine the amount of water, gas and oil produced by the well. These flowmeters can be differential pressure with an orifice plate, ultrasonic, turbine, or vortex flowmeters.
Vertical separators operate on similar principles as a horizontal separator. A horizontal separator does a better job of handling large volumes of gas than a vertical separator. It also can achieve better phase separation due to its large interfacial areas. However, a horizontal separator has more difficulty handling solids, and takes up more space than a vertical separator. A vertical separator handles solids more easily than its horizontal counterpart and takes up less space. However, it can be more difficult to service.
Separators are also divided into test separators and production separators. The main difference has to do with how much fluid is being handled. Test separators handle relatively small amounts of oil and gas. They can either be permanent or portable. Test separators are also called well checkers or well testers. Production separators are used to separate the fluid from a well, a group of wells, or a lease on a daily or continuous basis. They can be horizontal or vertical, like a test separator, but can typically handle more fluid than a test separator.
Besides three- and four-phase separators, two-phase separators are used to separate the gas from the liquid in well fluids. With two-phase separators, the gas is routed to a gas-processing system. However, the oil and water are not physically separated, but instead are routed out of the separator for processing downstream of the separator.
Measuring Wet Gas
Three- and four-phase separators are still widely used to divide up the fluid from a well and consequently to measure it with a flowmeter. However, new technologies have emerged in the past 20 years that may in some cases reduce the need to physically separate the components of well fluids. These include wet gas meters and watercut meters. These meters are designed to measure the flow of single-phase and two-phase fluids.
Wet gas consists of any gas that is composed of roughly 10% or less of water or hydrocarbon liquids. This percentage is not fixed, but 10% is generally regarded as the limiting amount of liquids for a fluid to qualify as wet gas. In metering wet gas, it is important to know what type of measurement is desired:
• Gas flowrate only
• Gas + liquid flowrate
• Gas + liquid hydrocarbon + water flowrates
Different types of meters are used, depending on the desired measurement. Different types of measurement include single-phase, two-phase, and three-phase measurement.
Single-Phase Measurement of Wet Gas
When single-phase measurement of wet gas occurs, it is generally to determine the flow of the gas, rather than the liquid. Even if the liquid does not have to be measured, its effect on the gas flow measurement may need to be taken into account. This depends on the required uncertainty of the measurement.
Differential pressure (DP) flowmeters with an orifice plate and DP meters with a Venturi element are commonly used for single-phase wet gas measurement. Still another type of DP meter used for wet gas is the V-Cone and other cone type meters. DP flowmeters used to measure wet gas tend to over-read the amount of gas passing through them. This means they need to be corrected with an appropriate correction equation to get the actual amount of wet gas that is being measured. There are several different equations for this.
When orifice plates are used for wet gas measurement, they should be checked periodically for damage or erosion, since these conditions can impact measurement accuracy. Orifice plates are often used for topside (land-based) applications. Venturi tubes have the advantages of being more durable, of resisting erosion, and can also withstand higher pressures than orifice plates. V-Cones and other cone type meters are also used, but they are not as well studied as are orifice plates and Venturis.
Ultrasonic and vortex flowmeters are also used to measure wet gas flow. Like DP meters, vortex meters tend to over-read the amount of gas flow present, and the amount of liquid present may affect the functioning of the meter. Coriolis meters are also used to measure wet gas, although the presence of liquid in the gas being measured has traditionally been a challenge for Coriolis meters.
2- and 3-Phase Measurement of Wet Gas
One method of two-phase measurement to measure both the gas and liquid flow is to use a DP meter and a non-DP meter and to base the flowrate on the difference in response by these two meters. Other technologies used to determine the amount of water content present include gamma ray, infrared and microwave. Some meters use separators to separate the gas from the liquid streams and then meter each stream separately. The water may also be separated from the hydrocarbon-based liquid with each fluid measured individually. This is a method employed in multiphase systems.
Measuring Watercut in Oil and Water
The term “watercut” can be confusing, but it means measuring the percentage or amount of water or liquid that exists in hydrocarbon fluids. The term “cut” refers to the content of the water in the hydrocarbon fluid. This percentage is extremely important for fluid coming off the wellhead and passing through a separator. When the liquid is separated from the gas, and the petroleum liquid is physically separated from the water, then the amount of water can be measured separately with a single-phase meter. However, there are some situations in which it is desirable to determine the water content or “cut” of hydrocarbon liquids without physically separating the fluids, and that is where a watercut meter can be used.
Different technologies are used to measure watercut. These include dielectric measurements, microwave, infrared, optical sensor, and other inferential technologies. The advantage of a watercut meter is that the percentage of water in the hydrocarbon liquid can be determined without physically separating the two liquids. A watercut meter does not typically measure flowrate – only the percent of water in the hydrocarbon mixture. For this reason, a watercut meter is often paired up with a flowmeter that measures the flowrate of the total fluid. The amount of water and oil or other hydrocarbon fluid can then be determined by combining the results of the two measurements.
There are many applications for watercut meters. These include process control on test separators, export metering, fiscal metering, on- and off-loading of hydrocarbon liquids, desalting in refineries, emulsion control, aviation fuel, oil quality control and two-phase flow measurements. The utility of watercut meters extends far beyond the test separator coming off a wellhead. In fact, these meters are used for many upstream, midstream, and downstream applications.
Measuring Multiphase Flows
While some people consider two-phase flow, such as oil and water, a form of multiphase measurement, the term is generally reserved for three or more phases: most typically gas, oil and water. Most fluid that comes out of a wellhead is three-phase flow, consisting of gas, water, and oil. These three components have to be separated so they can be processed individually. This is typically done with a separator.
There is nothing wrong with talking about multiphase flowmeters. The only problem is that this conjures up an image of a single flowmeter like a Coriolis or turbine meter with a single sensor and a transmitter. In reality, a multiphase flowmeter is a complex system of instruments that work together to measure three or more phases of flow. They involve more than one technology because it takes different technologies to accurately meter gas, water and oil, whether they are combined or separated.
A simple definition of a multiphase flowmeter is that it is a device that meters the individual gas, water and oil flowrates in fluids composed of three or more phases. In this sense, a test separator can be considered a type of multiphase flowmeter, since it separates the gas, water, and oil into three phases and then measures the flow of each with a single-phase meter. However, the advantage of many modern multiphase systems is that they can make these measurements without physically separating the fluids, or at least without separating all of them.
Multiphase flowmeters typically have several of the following components:
• Differential pressure flowmeters that measure the flowrate of the total mixture, often using a Venturi tube, or to derive the density of the fluid.
• Cross correlation sensors that look for disturbances, such as slugs and bubbles. Types of sensors used include densitometers, electrical sensors and pressure gages.
• Electrical property measurements that measure the conductivity and conductance of the multiphase mixture. The conductivity and a property called permittivity vary with the individual phases.
• Microwaves are used to measure the resonance and absorption of the multiphase mixture. Microwaves also rely on the permittivity of the different components to determine the individual phase fractions in the mixture.
• Gamma rays are passed through the multiphase mixture. The number of gamma rays that pass through the mixture depends on the mixture’s composition. Water is a strong absorber of gamma rays while gas is a weak absorber.
Research on multiphase meters began in 1982 with the Christian Michelsen Research of Norway and has continued ever since. Some of the main participants in this market today include Emerson Process Management (Roxar), Schlumberger/Framo, and FMC. This is a fast-paced and fast-developing technology, and many changes have occurred in the market just in the past few years. These include both new products and new entrants into the market.
Even though multiphase systems are still far from perfect, the measurement they perform is so valuable that many companies are working to find the optimal product solution. Some companies such as Schneider Electric, are aiming their product at a subset of the market, while others, such as KROHNE are partnering with petroleum giants such as Shell.
Even though there are risks and significant expense in committing to a multiphase research program, the rewards will be high for the company or companies that find a truly effective and reliable multiphase flowmeter system.
Author: Jesse Yoder, Ph.D., is president of Flow Research Inc. in Wakefield, MA, He has 25 years of experience as an analyst in process control and is a frequent contributor to Pipeline & Gas Journal Dr. Yoder can be reached at jesse@flowresearch.com.
DP Venturi flowmeter
Jesse Yoder
Comments