March 2015, Vol. 242, No. 3
TechNotes
Cathodic Shielding Effects Tested: PipePillo vs. Foam
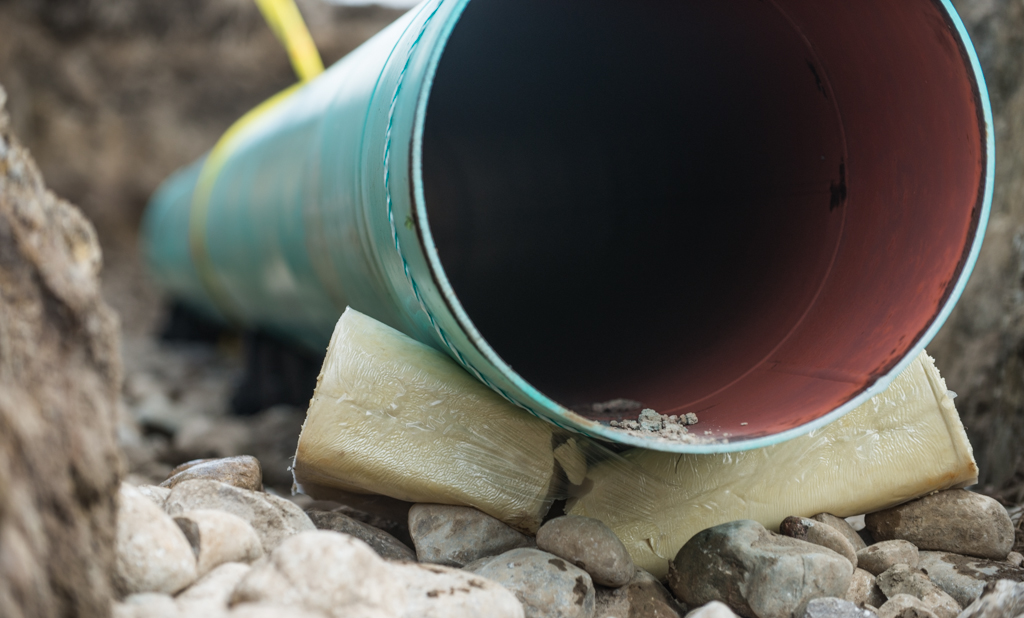
Perhaps one of the most important safe guards put in place to maintain the long-term integrity of buried pipelines is a cathodic protection system. Cathodic protection (CP) is an anti- corrosion technique used to prevent the corrosion of metals such as steel and iron in electrolytically conducting environments such as seawater and soils containing water.
In the case of buried pipelines, CP is achieved when one or more anodes (positive electrodes) discharge electric current to protect the pipeline, which acts as a cathode (negative electrode). If the CP system is electrically cut-off (shielded) from the pipeline where a holiday (a hole or gap in the pipeline coating) has occurred, then the CP cannot prevent corrosion.
There are many circumstances in which a holiday could occur, but one of the most obvious is a rocky trench bottom. Conventionally the pipe is protected from a rocky trench bottom by either adding a layer of sand or select backfill above and below the pipeline (sand padding) or by covering the pipe with a high-impact resistant, poly-type rock shield prior to installation.
To facilitate either method, some form of intermittent pipeline support (IPS) is required to elevate the pipeline off the rocky trench bottom. Over the years there have been several low-tech methods developed to elevate the pipe from the trench bottom, including sand piles, sand bags, and the most commonly used method, polyurethane closed-cell foam.
Polyurethane foam is either preformed into pillows (Figure 1) or sprayed directly into the trench (Figure 2). There are several serious draw backs with using foam as support. However, restricting the path for CP current, commonly referred to as cathodic shielding, is not routinely considered one of them. It is argued that the foam absorbs moisture over time, making it electrically conductive and allowing CP current to pass.
Although, in theory, this assumption sounds feasible, Geoff Connors, president and founder of PipeSak Incorporated, has always maintained that, through his experience building large-diameter pipelines, polyurethane foam does in-fact shield CP systems.
After collaborating with several of the largest engineering firms, contractors and pipeline-owning companies in North America, PipeSak Incorporated developed the first structured pipeline support – the PipePillo (Figure 3). Engineered to address all of the issues with traditional methods of in-trench pipeline supports, the PipePillo is lightweight, withstands flotation, is easy to install, resistant to UV and varying soil composition and pH, is softer than the pipe coating, and will maintain pipeline clearance for the life of the pipeline. But perhaps its most important design feature is that it does not impede CP systems.
To prove this, PipeSak Incorporated solicited the help of Corrosion Service Company Limited to carry out a comprehensive, unbiased experiment to test and compare the cathodic shielding effects of a PipePillo Structured Pipeline Pillow (SPP) and a standard spray-in polyurethane foam support. The methodology of the experiment was developed to test the cathodic shielding at a variety of CP operating points using a 1.2-m long section of fusion bond epoxy (FBE)-coated NPS24 pipe.
The pipe was instrumented with six steel coupons to simulate holidays in the pipe coating, with one coupon acting as a control by simulating an unshielded holiday between the supports. The experiment was designed to simulate an installed pipeline and was carried out over four months to address any uncertainty regarding the impact of time on foam’s shielding effects.
In order to conclusively evaluate the shielding effects of both the PipePillo® and the foam support, the experiment measured coupon-to-pipe resistances, coupon corrosion currents, and coupon polarized potentials at a variety of CP operating points. The experiment was carried out twice to determine whether increasing the load on the pipe would impact the shielding characteristics.
The test results clearly indicated that the PipePillo® (PP) coupons polarized more and received more CP current than the foam support (FS) coupons under all test conditions. In fact, the polarization characteristics of the PipePillo center and side coupons were almost identical to the polarization characteristics of the control coupon (simulated unshielded holiday).
Figure 4 shows the protection level of each test coupon represented as a comparison to the protection level of the control coupon (no shielding case). The polarized potentials of the PipePillo® coupons remained within 50 mV of the control coupon at all operating levels. By contrast, the polarized potentials of the foam support coupons were consistently both less electro-negative and subject to less polarization than the control coupon.
The test results are clear: the PipePillo support was determined to have negligible cathodic shielding effects while the foam support was determined to have significant shielding effects. Since aboveground measurement techniques are unable to detect shielded potentials, a holiday shielded from CP by a foam pipeline support could remain undetected while conducting potential surveys.
When combined with the propensity of foam supports to be crushed under the weight of the pipeline, which exposes the pipe coating to the rocky trench bottom, using foam as a pipeline support technique is a risk that pipeline-owning companies and contractors no longer have to take.
[inline:Fig 2_Polyurethane Spray-in Foam (2).jpg]
Figure 2: Polyurethane spray-in foam.
[inline:Fig 3_PipePillo Structured Pipeline Support.jpg]
Figure 3: PipePillo structured pipeline support pillow.
[inline:Fig 4_Coupon Polarized Potential vs Control Coupon Polarized Potential.jpg]
Figure 4: Coupon polarized potential vs. control coupon polarized potential.
Comments