September 2017, Vol. 244, No. 9
Features
DTE Energy Finds Communication a Key in Replacement Effort
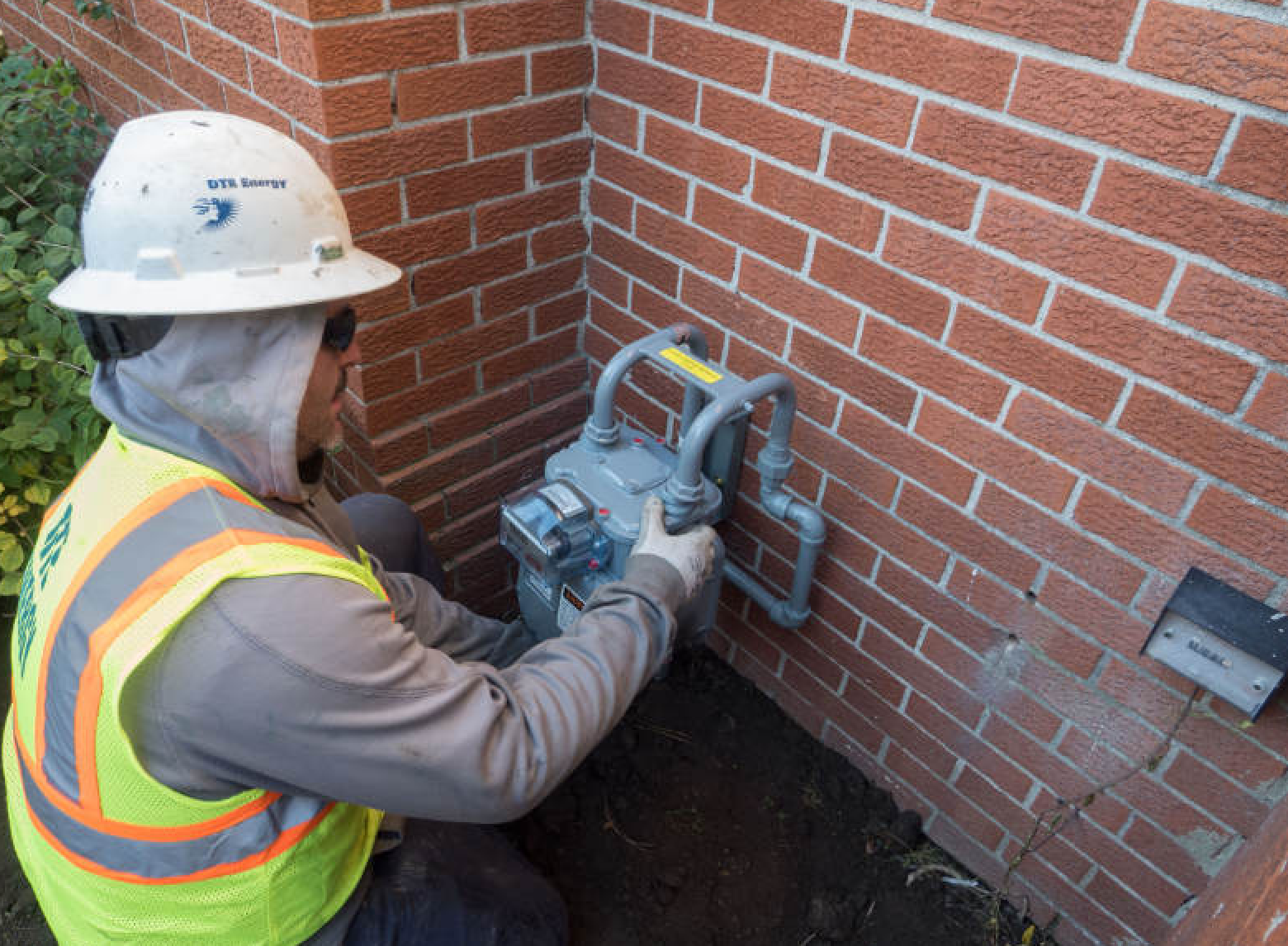
When it comes to huge long-term infrastructure replacement programs, few equal that of DTE Energy’s ongoing effort in Michigan.
Not only is the service territory massive – 20,000 square miles spread across the state – there is also the not-so simple matter of trying to upgrade 20,000 copper gas meters annually.
“Many of the meters we are changing are still located within the home or business and are being moved to an exterior wall of the building,” said Joi Harris, vice president of gas operations at DTE told P&GJ in a recent interview. “The work inside takes two to three hours, so we have to arrange for someone who is an adult to be inside during that time.”
In addition, DTE Energy, which ranked as16th largest distribution company in nation with over 1.2 million customers in the annual P&GJ 500 Report, plans to replace nearly 4,000 miles of pipe over the next 25 years as well, and the utility said it is still looking for ways to improve efficiencies in order to pick up this already assertive pace.
The upgrades, which involve replacing cast-iron and bare steel mains and services with polyurethane materials, is primarily in southeast Michigan’s Wayne County, which includes Detroit. The program also includes the west side of the state and other large communities, such as Muskegon and Grand Rapids, as well as some Upper Peninsula communities, including Escanaba and Iron Mountain.
DTE Energy began a small pilot replacement project covering 33 miles in 2007, ramping up significantly four years later. Over a five-year period, DTE Energy plans to spend $1.7 billion on new mains, relocated meters and other pipeline integrity work.
“Beginning in 2011, we began increasing our pace exponentially,” Harris told P&GJ. “We are up to about 140 miles this year. It’s rather aggressive, but that comes with challenges, as you can well imagine.”
Urban Complications
Because much of the renewal work is in urban areas, coordinating with customers and municipal entities to minimize inconvenience is paramount. There are further complications involving planned city roadwork and ongoing projects of other utilities.
“Let’s just say, for example, there is a road the state wants to replace and we have a main in the same location that we want to renew. We work with the state and align our schedules to minimize the impact to our community,” Harris said. “The terrain [in our territories] isn’t so challenging, but the work requires us to get inside every single home within that target area, so there is a bit of coordination required.”
To address this point, DTE Energy makes a practice of working with community leaders well in advance of its project schedules to identify the best locations for equipment staging. If possible, the company uses its own land in that capacity.
Early Notice
To deliver the message well in advance, DTE Energy makes a practice of sending out lots of notifications that workers are coming, as well as providing an explanation of what customers and commuters should expect and how long the work will last.
“It is creating that awareness upfront that is one of the major challenges. That and making sure our plans align with the community leaders within that target geography – that too is a challenge,” Harris said.
Though utilizing directional boring for pipe replacement work minimizes the effect on sidewalks and roadways, there are still situations that require rerouting of traffic. When such an eventuality arises, the company stages work in a manner that allows each area to be cleared before another is disrupted.
“We are working in residential areas, and we experience a few backups here and there while we are in the process of boring in the main,” Harris said. “It settles down once there is less construction equipment on a particular street.”
Arranging access to customers’ homes to replace gas meters has posed logistical challenges as well. DTE Energy begins by sending notices out two months in advance of its schedule, then intensifies communication efforts about two weeks in advance of the work with door hangers that encourage customers to contact the company to make arrangements.
“The work inside the home takes two to three hours, so we actually need to have someone inside the home who is over the age of 18 before we can perform the meter relocation and reattach the fuel line,” Harris said.
DTE has found town halls to be extremely beneficial, not just as a means to field questions and provide information, but also to acquaint customers with the technicians who will be doing the work. The company also shows visuals of what the work entails and the type of equipment that will be used.
“It’s just a really good way to education the community in advance of beginning the work as well as to cultivate a relationship,” Harris said.
Despite its northern location, DTE Energy works on replacement projects year-round, though the pace changes from season to season.
“During the winter months we scale back, but there is main that is still being installed,” Harris said. “Frost becomes an issue but the past couple of winters have been mild, so it has not been a problem. We try to finish up heavy construction by October and complete all of our restoration before Thanksgiving.”
After that’s accomplished, crews start pre-construction for the coming year in locations where the next round of boring will take place. That, essentially, will only require two excavations for each line.
With the volume of replacement work expanding, DTE Energy began increasing its related workforce, not only increasing the number of internal, full-time employees by about 150, but also adding three more contractors for a total of four. In addition to skilled trade workers, Harris said, the company has brought in engineers, project managers, schedulers and draftsmen.
With the growth of natural gas as a less-expensive fuel source, the company’s customer count has grown to 1.3 million for the first time, with that expansion occurring primarily in the upper-central part of Michigan. Last year, DTE Energy installed 8,000 new customer attachments. Additionally, the company is still attaching business customers as industry moves to the state and the regional economy improves.
“The exciting part is that we are still extending our main to communities that are currently being served by alternative fuels like propane, even wood in some cases,” Harris said. “When propane spikes in the fall, we see a number of attachment requests, and we are still attaching business customers.”
DTE Energy has invested in the region as well, buying from Michigan-based suppliers as part of the Pure Michigan Business Connect (PMBC). In 2013, the company increased its five-year commitment to $1.1 billion. There is also a formal supplier diversity program that is targeting smaller, second-tier companies and supporting them with advocacy training and mentoring.
“The diversity program tries to make sure that even if a company works with others outside of DTE, it has the right business model to be successful,” Harris said. “That program has been in place several years and we have been recognized for our efforts.”
As far as diversity in employment goes, DTE has several initiatives within Detroit that are designed to expose women and minority members to careers in energy and other skilled trades. The company has partnered with businesses to provide specific training for the opportunities expected due to the utility’s growth and the improving Michigan business climate. There are still difficulties in this area that Harris and DTE Energy hope to improve.
“One thing I’ve observed is that many of our youths are not interested, so the question becomes how do you expose and then prepare them for roles in skilled trades, many of which are available right now?” she asked.
Harris, who was born and raised in Detroit, began her relationship with her employer early in life. By 15, she had developed an interest in engineering, which resulted in her being assigned to shadow DTE Energy engineers as a class assignment.
“For just about a semester, I visited with them almost every Friday,” she said. “I was hooked.”
When Harris left for college, she was a co-op student for DTE Energy. Once she completed her studies, she was hired by the company as a full-time employee. It’s the kind of career path she would like to help make a reality for other young people, she said.
Editor’s note: This article is part of P&GJ’s ongoing series focused on local distribution companies’ infrastructure replacement projects.
Comments