September 2017, Vol. 244, No. 9
Features
New Gas Machinery Research Council Guideline Developed
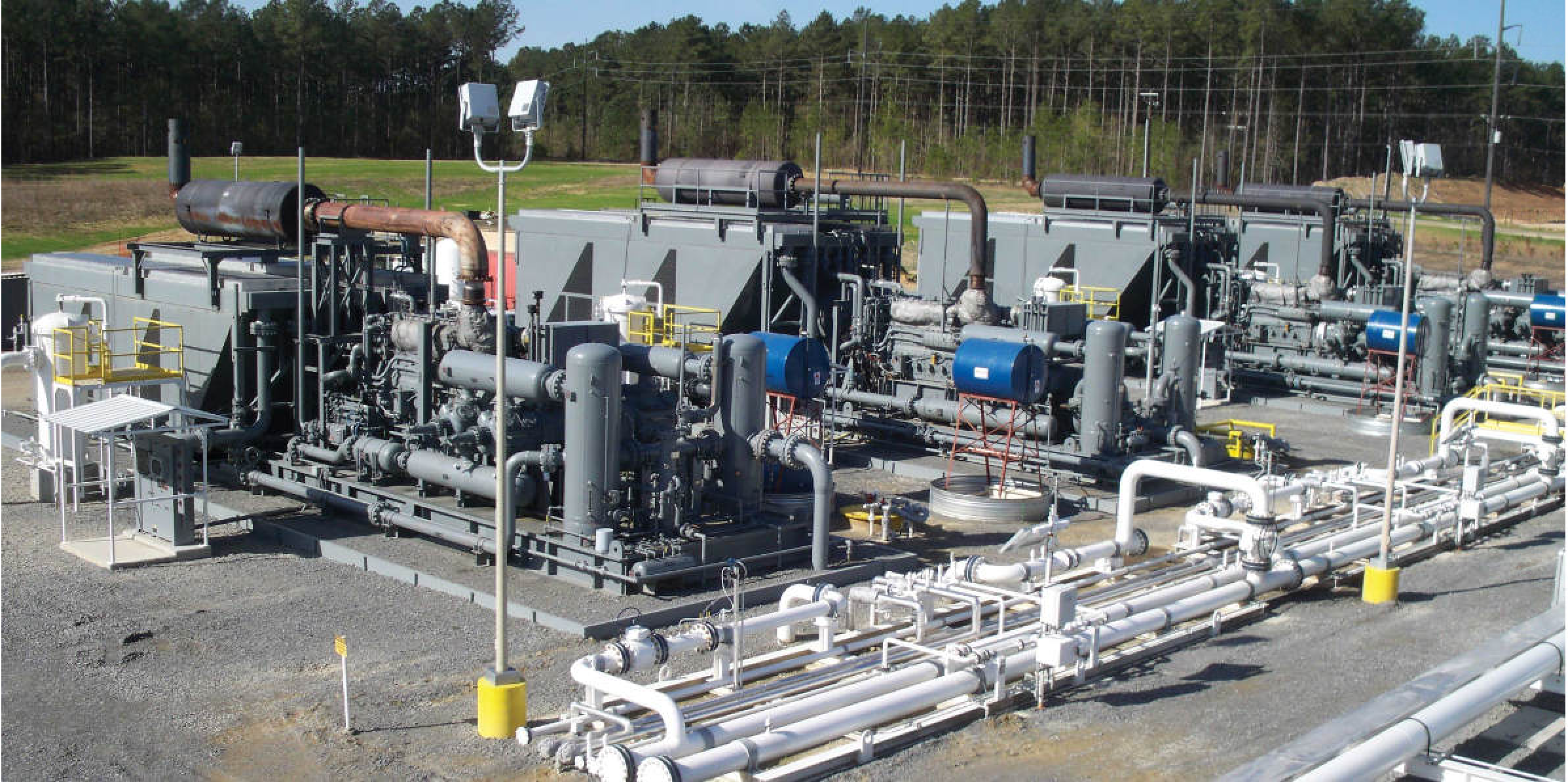
With the widespread use of high-speed separable reciprocating compressors throughout the oil and natural industry, the Gas Machinery Research Council (GMRC) has been active in developing better guidelines and practices for the specification, design and application of this type of compression equipment.
Two documents were developed previously in multi-year projects. First was the GMRC Guideline for High-Speed Reciprocating Compressor Packages for Natural Gas Storage and Transmission Applications, released in October 2013. Then in 2015 came the GMRC Guideline and Recommended Practice for Control of Torsional Vibrations in Direct-Driven Separable Reciprocating Compressors.
These guidelines, which have been well-received by the industry, focused on large compressors used in gas pipeline and storage applications. When the original 2013 guideline was developed, there was a request from several operating companies and compressor packagers to make them applicable to upstream, or field gas, compressor packages or to create separate guidelines for compressors in field gas applications.
Although that was not within the scope of the 2013 guideline project, the request was raised again by operators and packagers in 2015. At the same time, the Gas Compressor Association (GCA) asked for a better specification document to cover the siting and installation of contract compression (i.e., rental) packages.
The GMRC responded with a project to develop a guideline specifically for field gas compressor packages. The contractor for both of the earlier guidelines, ACI Services Inc., was enlisted to lead the development of the new guideline as well.
GMRC, a subsidiary of the Southern Gas Association (SGA), is a not-for-profit research corporation founded in 1952. It provides member companies and industry with the benefits of an applied research and technology program directed toward improving reliability and cost-effectiveness of the design, construction and operation of mechanical and fluid systems. GMRC also serves the industry through technical training programs and conferences, including its annual Gas Machinery Conference & Exhibit.
Compression Evolution
Gas compression for natural gas pipelines and wellhead applications has continually evolved since first emerging in the late 1800s. The first gas compressors were heavy, slow-speed, single-throw horizontal compressors that were belt-driven by steam or gas engines.
In 1899, the first horizontal integral reciprocating gas engine compressor was introduced on a natural gas pipeline. In the 1930s, manufacturers introduced angle integral reciprocating gas engine compressors that were comparatively easier to transport and install. Over the next four decades, larger and larger integral units were introduced, with the largest exceeding 10,000 horsepower (hp). These conservative, reliable and versatile engine compressors, most of which operated in the range of 250-330 rpm, were installed by the thousands as the interstate pipeline infrastructure was developed throughout the country.
In the 1950s, centrifugal compressors began to be applied on mainline systems. With the development of aircraft derivative gas turbines in the 1960s and beyond, gas turbine-driven centrifugal compressors gradually displaced large integrals on new pipelines and expansions. The manufacture of new integral engine compressors ended in the 1990s as the U.S. pipeline infrastructure was essentially built-out, and gas turbine-driven centrifugal compressors filled most expansion needs.
Extensive expansion of the U.S. pipeline infrastructure from the 1940s to the early 1970s drove a need for more field gas compressors. Manufacturers introduced smaller, higher-speed integrals, which together with belt-driven reciprocating units, temporarily filled the need for more portable field gas units.
Beginning in the late 1950s, high-speed gas engines direct-driving separable reciprocating compressors, packaged as ready to install skidded systems, steadily gained acceptance for field gas compression applications. As technology improved, these units increased in rated power and speed. By the 1970s, high-speed separable engines and matching compressors dominated field gas applications.
In the 1980s, rotary screw compressors, which were common in air and refrigeration compression, began to be adapted to field gas compression applications. These grew in acceptance and became common for lower pressure field gas applications by the mid-1990s.
Upstream Sector
The upstream compression sector applies high-speed (up to 1,800 rpm) reciprocating and rotary screw compressor packages that range from about 50-2,000 horsepower (hp). Field gas applications, which include wellhead gas gathering and boosting, gas lift and central gas gathering, have a number of characteristics not covered in the 2013 guideline.
These include handling wet gas, dirty gas and wider variations in gas composition including sour (H2S), CO2 and N2 content, as well as on-skid fuel gas conditioning, high-pressure ratios requiring multiple compression stages with gas intercooling, engine accessory end drives for auxiliary equipment, portability, outdoor unenclosed or partially enclosed packages and integrated enclosures for cold weather applications.
Economics is a major factor that drives the behavior of the supply chain. While the presence of a number of competent packagers in the industry makes for a competitive procurement environment, this is not necessarily an advantage when the procurement specification is not sufficient.
With a continuing and accelerating decline in average engineering experience throughout the industry, many best practices are being lost. In addition, more packagers, with varying levels of experience and capability, serve the upstream reciprocating compressor market that demands large quantities of units as the shale industry grows.
Since the advent of the shale boom, more aggregate new horsepower has been placed in the upstream than in the natural gas pipeline and storage industry each year. Purchasing decisions in much of the upstream are usually driven by price and lead time (availability). Packagers indicate they often have better solutions to offer, but the lack of adequate industry standards, inexperience of end users and the competitive nature of the market make it difficult for them to include and charge for improvements that are not specified by end users.
The field gas market is also characterized by the majority of the new compression installations being provided by contract compression companies that use standard, flexible packages that may or may not be optimal for specific compression applications.
Reciprocating Guidelines
The development of the aforementioned GMRC Guidelines filled significant gaps that existed in the gas transmission and storage sectors. But these and other existing industry specifications are of limited value for the purposes of procuring, designing and applying high-speed upstream compressor packages.
Some end users, and especially engineering companies, specify API 618, which is intended for low-speed, hydrogen-rich, process gas compressors. It is generally too complex; much of it is not applicable to high-speed compressors and it lacks enough detail in some important areas.
The former and no longer available API 11P and ISO 13631 are intended for field gas compressors, but lack important guidance in many areas. API 11P is obsolete and no longer available. ISO 13631, which was last revised in 2002, is no longer supported by U.S. companies due to government restrictions on technology transfer to embargo countries.
API is considering development of a new field gas compressor specification, however the development and approval cycle typically takes many years. Operators wanted more immediate help to meet the rapidly growing demand for new packages for oil and gas shale plays.
Responding to that need, GMRC recently completed development of a new field gas compressor package guideline, entitled GMRC High-Speed Compressor Package Guideline for Field Gas Applications. GMRC also completed a significant update of the 2013 GMRC Guideline for larger (2,000 hp and above), high-speed (≥700 rpm and above) reciprocating compressor packages.
Like the previous guidelines, development of the new GMRC High-Speed Compressor Package Guideline for Field Gas Applications was an extensive collaborative project.
The research and data collection phase involved completion of questionnaires by personnel and follow-up interviews at nine end-user companies, six rental compression fleet companies, (10 compressor packagers, three compressor OEMs, three engine OEMs, two air-cooled heat exchanger OEMs, two electric motor OEMs, an exhaust silencer and catalyst OEM, and three engineering/analysis companies.
In addition, 10 field gas compressor sites were inspected, including 35 different high-speed compressor packages. From this information, a long list of problems, solutions, preferences and suggested practices were documented, serving as the foundation for development of the new guideline. An extensive literature search was also conducted to evaluate existing material that might be cited and referenced in the guideline.
Along the way, it was decided to include considerations that apply to rotary screw compressor packages for the upstream sector. This effort was consolidated into an extensive report that served as in important reference for development of the actual guideline.
Development of the guideline over the past year involved 58 individuals at 41 different companies serving on project work teams or involved in providing input or conducting reviews of sections of the guideline.
Best Practice
The new GMRC High-Speed Compressor Package Guideline for Field Gas Applications outlines the responsibilities of key stakeholders, schedule development and project management. It provides extensive tutorial information and recommended practices for request-for-proposal (RFP) development, bid evaluation, design, fabrication, installation and commissioning.
Separate sections focus on compressor selection and specification for both reciprocating and rotary screw compressors as well as gas engine and electric motor driver selection and specification. Sections are dedicated to capacity control and automation design and to cooler selection and specification. A section that is especially important for field gas applications covers gas filtration and separation, including oil separators for rotary screw compressors. It includes a simplified procedure for preliminary sizing of package inlet scrubbers.
Another extensive section covers the selection and design of appropriate foundations and skids. For field gas packages, foundations range from crushed gravel or caliche pads to reinforced concrete pads to driven piles and screw piles. Selection of the appropriate foundation is a critical success factor and best practice starts with a geotechnical study of the soil and drainage present at the proposed compressor package installation site.
Examples of successful specifications are provided, along with tutorial information. The skid design depends on the type of foundation and guidance provides a high probability of success. A related section covers recommended pulsation and vibration analyses and control methods, including a checklist of studies and the required engineering data. A newly developed spreadsheet is provided for preliminary (pre-bid) sizing of pulsation bottles, which can be used to make packagers’ bids more consistent.
Field gas compressor packages may be completely open to the atmosphere, partially enclosed, or completely enclosed and protected from harsh environments. To cover these widely different scenarios, the largest section of the new guideline covers pressure vessels, piping and package/building design and assembly.
Among the many topics covered are fuel gas conditioning, pressure vessel design and fabrication, pressure safety valve selection and mounting, enclosures, ventilation and heating, gas and fire detection, noise control, intake and exhaust systems, starting systems, coolers, piping, and conduit and wiring. A special emphasis is placed on skid and building layout to ensure functionality and accessibility for operation and maintenance.
An instrumentation and control section provides recommendations for three different levels of packages, ranging from small, bare-bones units to mission-critical units. Minimum instrumentation and minimum alarm and shutdown recommendations are provided for gas engine and electric motor drivers, reciprocating and rotary screw compressors, coolers, scrubbers and the balance of the package.
Sections on equipment safety, accessibility and maintainability and onsite considerations, installation and commissioning were developed in close cooperation with member GCA companies. They include many best practices that apply to contract compression units as well as to end user/operator-owned packages. Sections on inspection and testing and operation and maintenance round out the 358-page guideline that includes 15 sections, plus four extensive appendices.
Both the new GMRC High-Speed Compressor Package Guideline for Field Gas Applications and the newly updated GMRC Guideline for High-Speed Reciprocating Compressor Packages for Natural Gas Storage and Transmission Applications are scheduled for formal release in early October at the annual Gas Machinery Conference.
(The 2017 GMRC conference will be held Oct. 1-4 at the
David L. Lawrence Convention Center in Pittsburgh, PA. For more information visit www.southerngas.org).
Comments