August 2018, Vol. 245, No. 8
Features
More Skin in the Game: New Technology to Find, Fix Leaks
By Richard Nemec, Contributing Editor
At the outset of summer 2018, it seemed fitting that the World Gas Conference (WGC), was holding its triennial week-long gathering in the United States for the first time in 30 years.
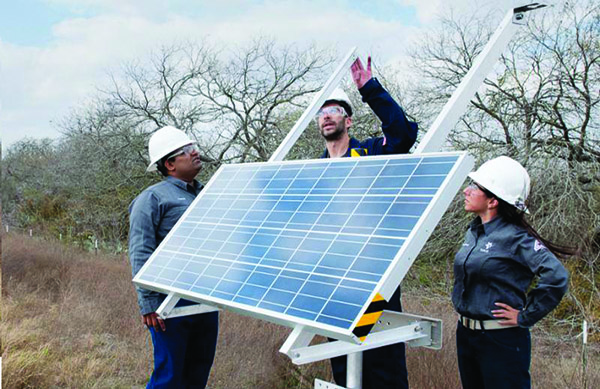
The global assemblage established by the International Gas Union (IGU) in 1931 was returning to the USA at a time when the nation has become the world’s biggest consumer and producer of natural gas, and arguably the center of innovation and technological advances that have launched an energy renaissance. WGC proved to highlight the breadth and depth of the technology advances that have indisputably re-energized the gas sector of the global energy economy.
An 86-year history and more than 12,000 participants were part of the landscape in Washington during the last week of June, with online interactive programs covering technology-rich subjects in transmission, distribution, storage, LNG, R&D and exploration and production (E&P).
In many cases, outside organizations from the environmental, finance and research sectors showed major presences at the global industry sessions that can at times become dry and arcane. But in 2018 in the U.S. capital, it was far from business-as-usual, as evidenced by an environmental group outlining plans for launching a satellite by 2021 that will track methane leaks around the globe. Others displayed space-age technologies now aiding the oil and gas sector on the ground.
Using a theme of natural gas being a “foundation fuel” globally, the success story of the U.S. transformation through innovation played well on a world stage that was brought to Washington at a time, as American Gas Association (AGA) CEO Dave McCurdy and chair of the 2018 WGC organizing committee put it, when gas “has boosted the U.S. economy, enhanced its national security and supported renewable energy, leading to energy-related carbon dioxide (CO2) emissions hitting a 25-year low.” It’s a model that McCurdy indicates is expandable to the rest of the world.
Among more than 600 speakers from about 100 countries sharing their views on the most timely and topical, technical, commercial and strategic topics related to the natural gas industry was Ben Ratner, senior director at the Environmental Defense Fund (EDF), who is focused on the adoption of advanced methane detection and mitigation.
While talking with P&GJ, he was in the midst of strategy meetings with Equinor (formerly Statoil), one of the biggest global oil E&Ps. His organization, EDF – the same one planning a methane-detecting satellite launch – was one of the WGC’s exhibitors in a 40,000-square-meter exhibition hall housing 350 exhibitors, including separate pavilions for sustainable energy, robotics, automation and gas-for-transportation.
In the shadow of this international gathering, Ratner was mapping plans with Equinor engineers on a program called the “Methane Detectors Challenge” that began back in 2015 with an effort to spark development of a continuous methane monitoring power system.
“It’s a technology that can sit at your well pad or compressor station and provide continuous 24/7 monitoring and alerts if there is a significant leak,” said Ratner, noting the technology has been catalyzed and is on the market. “Now Equinor and others (a unit of Royal Dutch Shell and Pacific Gas and Electric Co.) are beginning to use the technology in their ongoing operations.”
Unfolding Tale
The start-up behind this technology, which is now also being tested by parts of General Electric’s Baker Hughes unit, is Colorado-based Quanta3 LLC, maker of a laser-based sensor system providing 24/7 monitoring of energy infrastructure. The long-standing and deepening relationship between EDF and other major environmental organizations, particularly in the deployment of advanced technology, is a continuously unfolding tale. One area is in the deployment of drones, and EDF is squarely in the middle of research in this sector.
Working with Stanford University, EDF is involved in a global monitoring challenge to test the validity of advanced mobile methods for detecting and tracking methane. Companies such as ExxonMobil, Schlumberger and GE-Baker Hughes are involved. The program has examined various tracking technology mounted on trucks and aircraft, in addition to drones, and there was competition in both California and Colorado among various technologies with the intention to publish the results by the end of 2018.
“This can really help industry make decisions about how they manage their methane emissions,” Ratner said. “They can decide on their use of emerging tools, some of which they may agree to pilot test.
“Operators are already using drowns for other jobs, such as monitoring their assets, so with increasing scrutiny on methane emissions it made sense to apply the technology there. The jury is still out on when drone-based methane monitoring will become a big part of the methane solution, but there are many people who think that day will come.”
Visual Line of Sight
Jim Cieplak, director of business development and strategy for Harris Corp., and Brad Tomer, interim CEO and operations vice president at GE’s Avitas Systems, both have strong opinions on unmanned aerial systems (UAS) and unmanned aerial vehicles (UAV) or drones. And both are making the rounds of energy conferences this year explaining the step-changes coming in the oil and gas sector from the deployment of these tools with the right advance data gathering system.
Harris, which works closely with the Federal Aviation Administration (FAA), has been instrumental in introducing “beyond visual line-of-sight (BVLOS)” to the transmission pipeline and electric transmission sectors with the first such applications in the country. Cieplak works with public and private sector clients near many of the major U.S. oil and gas basins. In May, Harris rolled out a BVLOS UAS network concept for the Bakken Shale in North Dakota, including a proof-of-concept demonstration project with the goal of setting business plans and testing of a Bakken-specific deployment-ready wide-scale implementation plan.
“UAS network deployment will generate multiple benefits for the oil/gas industry,” Cieplak said. “A single investment will be generating multiple value streams for multiple energy sector companies. Whether the need is infrastructure inspection, environmental compliance, or reduced lost revenue [from leaks] this technology can make a contribution.”
Avitas Systems’ Tomer emphasizes that drone technology and ultimately artificial intelligence sit as the tip of an iceberg, and exponential changes are coming. UAS is becoming a factor faster than many people in the oil and gas sector realize in 2018. Avitas’ overall UAS approach includes various camera combinations, weather stations, controlled flight, inspections plans, real-time data analysis, repeatable data collection processes, Cloud-based storage and reporting, and the ability to mount RGB (wide color variety) and infrared cameras on the drones.
Tomer and other advocates of the technology stress its better overall and safer inspections, reduced labor and operating costs, faster processes, and data that meet the latest U.S. Environmental Protection Agency requirements. Ultimately, these types of surveys offer the latest in OGI (optical gas imagining) camera work, thermal picture-takers essentially that offer a comprehensive overview of a pipeline or gathering and processing infrastructure.
The goals are lofty, and the payback is potentially big. One goal is to make North Dakota, the nation’s second biggest oil producing state, a leader in UAS research and operations, spreading its applications to the state’s oil and gas industry.
Unlike in the past perhaps, in 2018 outside organizations such as EDF seem to be more on the same page with the industry as evidenced by Ratner who said that there is a significant role for natural gas in today’s global economy and he quotes independent sources like the International Energy Administration (IEA) as predicting that gas will be significant, meaning getting more sophisticated about the identification and mitigation of methane leaks. Ratner sees it as a combination of competitive pressure on the gas sector and economic opportunities that emerge from the challenges.
Away from WGC’s international stage and global focus, in the nation’s heartland and second largest oil-producing state, North Dakota, is the melding together of a string of oil and gas sector technology advances, including a pipeline integrity initiative through a unique industry-state partnership centered on the state Energy and Environmental Research Center (EERC) at the University of North Dakota. Jay Almlie, the EERC’s principal engineer, keeps track of a powerful number of joint projects that have been quietly paying off for the oil and gas sector, launching pre-commercial companies that hold promise for pipeline, midstream and E&P operators alike.
As a research management facilitator for pre-commercial technology, the EERC is helping many large E&P and midstream operators who work in a number of basins aside from North Dakota’s Bakken shale play to translate today’s technology advances into more efficient, value-driven operations. It is done with a heavy dose of collaboration tied to thinking outside the box. The costs, risks and rewards are all shared. The approach is embodied in a program Almlie outlined for P&GJ in early summer called “The Hunt for New Technology to Prevent and Detect Liquids Gathering Pipeline Leaks.” The emphasis, he said, is for practical solutions.
EERC is managing an industry driven, competitive program in North Dakota called “iPIPE: Intelligent Pipeline Integrity Program” that is aimed at advancing emerging technologies on the cusp of commercialization to provide additional tools for preventing and detecting leaks. “This program is to get over the ‘valley of death’ of pre-commercialization to the final step where it can be commercial,” Almlie said. “If these pipeline operators were not seriously interested in applying new technologies to help them do their jobs better, they wouldn’t be involved in iPIPE.”
Testing Technology
Various potential suppliers with technological solutions to market that fit iPIPE are invited to make a pitch to a rotating executive review committee of participating oilfield operators with the best two or three presentations getting their technology pilot tested in the Bakken. “If these technologies prove successful, the sponsoring operating companies are waiting with even a little drool coming from their mouths,” said Almlie.
Using a version of the network television program "Shark Tank," more than a half-dozen companies were invited to make their case for their technology being tested as part of iPIPE. Almlie was preparing for a review again in the fall after selecting two “winners” in May of 2018, a Canadian and a U.S. company.
Calgary, Alberta-based Ingu Solutions has developed a new product called Pipers, golf-ball sized, free-floating tools for inline inspection that follow the flow of fluid through a liquid pipeline. “Ingu claims to be compatible with liquids gathering pipelines generally,” Almlie said. “iPIPE and Ingu plan to demonstrate the ability of Pipers to geolocate buried pipelines, sense small leaks in pipelines, and measure wall deformations and wall corrosion in small-diameter pipelines.”
These demonstrations will be conducted on 15 separate segments of small-diameter, highly-networked liquids gathering pipelines in North Dakota. These are operating pipelines that were volunteered for this effort by several sponsoring members of iPIPE.
“These companies are all interested in getting their brethren to play in the same sandbox and bring their checkbook,” Almlie said. “In all fairness, these development costs should be shared by everyone working in this space.”
The second selected project this spring was Toledo, Ohio-based Satelytics, which applies deep machine learning to very large sets of data purchased from a variety of sources to discern signs of underground pipeline leaks. This data can come from commercial satellites, commercial aircraft overflights, drones, or other sources. Satelytics will scan a thousand-square-mile area repeatedly over three months this summer, looking for anomalies that will indicate possible subsurface pipeline leaks. “Satelytics claims to be able to identify potential pipeline leaks with little human analysis required,” Almlie said.
How do these ongoing efforts in North Dakota fit in nationally? Almlie thinks they are complementary, and he is not aware of much duplication. In fact, other oil and gas producing states have been knocking on North Dakota’s door in recent years from Colorado, Oklahoma, Texas and New Mexico seeking additional information on given programs and demonstration efforts, according to Almlie. He cites the Pipeline Research Council International (PRCI) as doing “great work” but with a global focus that is looking at millions of miles of transmission pipeline as opposed to gathering infrastructure.
‘Bring Some Skin’
Nationally, pipeline integrity programs are focused on both internal and external technology. “It is a wide open playing field, and iPIPE is agnostic regarding those preferences,” Almlie said. “What the operators want are technologies that help them do their jobs better.”
For the technology providers testing their pre-commercial mousetraps in the iPIPE program, Almlie said he emphasizes this is a “co-development” technology advancement program. “So the developer better bring some skin to the game. For every demonstration or development activity, you better bring some skin; if you’re proposing a million-dollar effort, you better bring at least $500,000 of in-kind or cash resources.”
This is particularly true, Almlie said, where he sees the bulk of the future advances in pipeline technology coming from – artificial intelligence (AI).
Thus, the real future is artificial intelligence. “Many people don’t recognize it, but it is here now,” Almlie said. “The wave is already crashing on us. Elon Musk and Bill Gates and others have expressed their concerns about AI because it is here right now. Of the seven presentations at our May Shark Tank, four of them involved AI. That is probably a good bet for the exciting breakthrough that’s coming.”
Managers like Avitas’ Brad Tomer see a broadening of the inspection capabilities from today’s research efforts that seek to harness AI. Three key exponential technology areas are converging – smaller improved sensors, deep learning analytics advances including AI, and improved platforms in robotics.
Tomer offers an analytics platform that brings together various disparate data sets, provides risk-based asset management planning for oil and gas infrastructure operators and creates 3- and 4-D modeling for assessing various business options. Feeding into this platform are asset performance data, systems data and inspection data.
Ultimately, the advances in applying AI and drones will surface in the energy infrastructure build-out that promises to get increasingly robust, whether in the Northeast adding transmission pipes, in the West Texas/Gulf Coast area for more gathering and processing, or North Dakota where the nation’s first greenfield refinery is set to start construction later this year. The ability to gather and analyze data will be a continuing test for operators.
Irvine, Calif.-based Meridian Energy Group Inc. in the summer of 2018 obtained a permit to construct the Davis Refinery in Belfield, N.D., the first U.S. oil refinery to be constructed from the ground up in more than 40 years, according to Lance Medlin, a Cut and Shoot, Texas, native son who is Meridian’s executive vice president in charge of the refinery project, which will be the cleanest of its kind on the planet, employing cutting-edge technology throughout. Aside from the critically needed 49,500 bpd capacity available in the heart of the Bakken Shale play, the technology as the “cleanest in the world” will provide a blueprint for future refining needs globally.
“The refinery’s innovative design at Davis will achieve emission rates so low that it has been qualified as a synthetic minor source by the North Dakota Department of Health’s (NDDOH) air quality division,” Medlin told an energy conference audience in Bismarck, N.D., earlier this year. “This is the first time in the history of a refining project of this complexity that it was permitted this way.”
According to Medlin, the $1 billion refinery is calculated to have emissions of about one-tenth the total of those calculated at a neighboring state park from the nearly 100,000 cars visiting the park annually. It will take 12 to 18 months to construct and a lot of the facility will be fabricated off-site and assembled onsite.
“The Davis refinery will be truly unique in its comprehensive use of emission control technology throughout the plant,” Medlin said. “Innovation and significant advances in technology will enable the refinery to regularly operation without any significant external flaring.”
Cut Operating Costs
Among the various state-of-art technologies will be ultra-low nitrogen oxide (NO2) burners installed in all boilers and heaters, OGI cameras, an available monitoring technology to detect volatile organic compound (VOC) leaks, and highly advanced enhanced leak detection monitoring and repair. The U.S. Environmental Protection Agency has in essence certified OGI (optical gas imaging) as the “best system of emission reduction” for detecting fugitive emissions for new equipment installations, upgrades and modified equipment.
Similarly, heavy equipment used in the oil and gas fields is the focus of various technology upgrades to cut operating costs and to provide more remote monitoring to avoid major breakdowns. At the center of all this is Dave Dunlevy, general manager with Caterpillar Oil & Gas. In mid-2018, Dunlevy outlined some advances Caterpillar has made in the digital technology, along with integrated drive trains.
Three areas the heavy equipment manufacturer is helping address are electronic monitoring systems for pumps used in the oil patch; dynamic transmission output controls; and engine idle reduction systems. Caterpillar spends about $2 billion annually on R&D and has about 600,000 pieces of equipment spread across the globe at both customers and company facilities. It is another, albeit somewhat hidden, area where technology advances are driving cost-savings and operating efficiencies in oil and gas operations.
Dunlevy said there are an estimated nearly $1 million in annual savings per-hydraulic fracturing fleet from pump electronic monitoring providing warnings to operators of a leak or cavitation to prevent unnecessarily damaging a pump. There are also dynamic transmission output controls, including transmission software, direct control of flow rates, economy mode shifting, and engine idle reduction (EIR) systems to reduce idle times by 60% and save 8.5% on annual fuel bills for various heavy equipment.
Caterpillar equipment is involved in all major fracking stages, and Dunlevy lists examples of remote monitoring and early notification allowing a low coolant level to be spotted, reported and fixed to avoid down time and added costs. Even remote detection of improper maintenance carries real savings, significant down time and unscheduled costs. The trouble can be first identified and reported all with a manager’s cell phone with the right apps.
Welcome to a new world that continues to be made easier to management because we are applying so much more intelligence – artificial and otherwise. P&GJ
Richard Nemec is a P&GJ contributing editor based in Los Angeles. He can be reached at rnemec@ca.rr.com
Comments