June 2018, Vol. 245, No. 6
Features
‘Cradle-to-Grave’ Documentation Enhances Safety in Pipeline Projects
By Richard D. Phillips, Senior Director, Pipeline Safety Enhancement Plan, SoCalGas
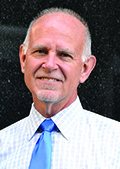
Following a major gas pipeline explosion in 2010, the California Public Utilities Commission sought to ensure that every gas utility meets strict specifications for pipeline safety. One important aspect of pipeline safety is ensuring materials are tracked through installation. Southern California Gas Company’s (SoCalGas) and San Diego Gas & Electric Company’s (SDG&E) joint Pipeline Safety Enhancement Plan (PSEP) decided to implement rigid “cradle to grave” documentation tracking.
From the time a section of pipe is manufactured until it is placed into service, PSEP has a detailed process to follow it every step of the way.
It’s common practice to identify and log materials when they are delivered by the manufacturer and upon installation in the ground. What’s less common is PSEP’s approach, in which the documentation travels with the materials at all times.
Pressure-carrying materials (pipes, valves, fittings and equipment) used in high-pressure gas transmission, distribution and storage systems are traceable from initial receipt from a supplier through installation. For purposes of this article, we’ll use pipe to communicate the process.
When a specific size and length of pipe are identified by engineering, PSEP sends representatives to where the pipe segment is manufactured to do a physical inspection. A company representative makes sure it meets the required certification and signs the documentation. The initial documentation then accompanies the pipe to SoCalGas’ warehouse in Bakersfield, Calif. Upon arrival, the pipe segment is unloaded, the signed documentation is checked and the pipe is stored.
When the warehouse receives a request for that particular pipe segment, the paperwork is pulled and sent with the pipe to the worksite. Before the pipe is installed, its unique manufacturer’s number and other key identifying information are recorded and entered into the SoCalGas Geographic Information System (GIS), from where any company asset can be immediately located.
Leveraging Technology
As with most things in business today, the materials documentation process relies on technology for efficiency. Here are the key systems PSEP uses to track materials:
- Delcon: This is a document management tool used to house records during the project lifecycle and automate the transfer of records to SoCalGas’ central asset management system. Delcon houses the final copy of the document with the data needed to facilitate direct transfer into GIS and other document retention systems
- Barcoding: A barcode is attached to the pipe upon receipt at the warehouse. PSEP scans the barcode on a piece of pipe from the time it arrives at the storage warehouse until the time it leaves for the job site and is placed in the ground
- Survey: This is a tool that helps PSEP survey every weld in the ground so the crew can record each piece of pipe they see. Using Survey, the crew records the numbers assigned to each pipe segment, weld, etc. All segments and fittings are accounted for to allow future pinpoint accuracy
- SAP: SoCalGas uses SAP for most IT applications. For materials documentation, SAP is used to manage logistics from initial procurement through the time the material leaves the warehouse. SAP will be leveraged further in the materials traceability project.
Materials Traceability
Implementing an end-to-end materials traceability (MT) process reduces manual data entry and institutes standard naming conventions and material characteristics throughout the system.
The MT process encompasses several distinct stages:
Engineering and design: standardize codes for all high-pressure PVFE, formalize a code creation process, and manage approved manufacturers in SAP; identify material requirements; and use standardized material codes in all designs
Procurement: procure all materials by standardized material code, request and receive material traceability documentation electronically from vendors and ensure vendors properly test and mark materials
Quality inspection and logistics: receive materials in SAP, inspect PVFE, generate batch bar code labels and manage inventory/issue materials to field by batch bar code labels
Construction: receive materials in field by batch bar code label, stage / install materials, maintain and record batch label information and manage excess inventory
Reconciliation and closeout: automate material reconciliation and closeout processes using standardized material code and characteristic data from SAP
The “cradle-to-grave” documentation process has resulted in gained efficiencies and the ability to locate installed materials. Tracking assets via this process improves safety and reduces risk. That’s why the current MT policy requirements used by PSEP are followed by all SoCalGas high-pressure construction programs and teams, including pipeline integrity, major projects, storage, gas transmission and gas distribution high-pressure construction.
Background on Plan
On June 12, 2014, the California Public Utilities Commission (CPUC) approved SoCalGas’ and SDG&E’s joint PSEP. The PSEP work is in response to new requirements adopted by the State of California and the CPUC to enhance the safety of California’s natural gas transmission pipeline system.
PSEP is one of the largest pipeline safety projects in the U.S. As required by the CPUC, all natural gas pipelines in the SoCalGas transmission system that have not already been tested, or do not have adequate records of a pressure test, will be tested or replaced.
The current phase of PSEP calls for SoCalGas to hydrostatically pressure test or replace about 180 miles of transmission pipelines in populated areas, and retrofit over 300 valves to be automatically or remotely controlled.
Safety is, and has always been, paramount at SoCalGas and SDG&E, and the Pipeline Safety Enhancement Plan enhances the system integrity and further protects customers and employees. Safety is a core value that the company demonstrates through action and investment. SoCalGas’ five-year capital plan includes $6 billion in infrastructure investments for improvements to distribution, transmission and storage systems and for pipeline safety. P&GJ
Comments