June 2020, Vol. 247, No. 6
Features
Technology Meets Mega Rule Materials Verification Challenge Head On
By Parth Patel, Engineer, and Buddy Powers, Director of Development, Massachusetts Materials Technologies, LLC (MMT)
The pipeline industry has been aware for nearly a decade that the U.S. Department of Transportation’s Pipeline and Hazardous Materials Safety Administration (PHMSA) planned to introduce regulatory requirements to improve pipeline safety.
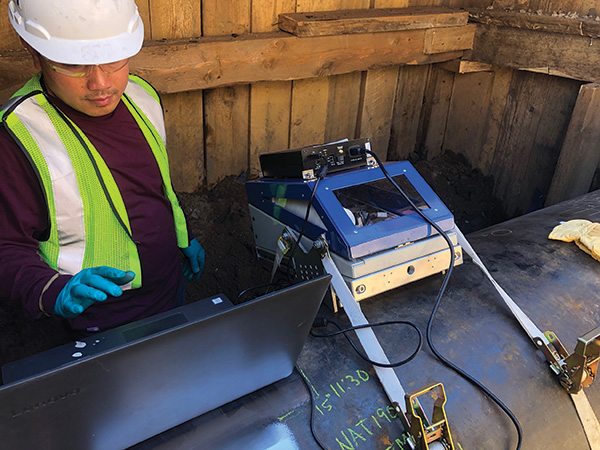
In October 2019, when the new requirements were unveiled, it became apparent that asset owners would face challenges verifying asset integrity to meet the regulator’s expectations when the rules go into effect in July 2020.
Extensive asset verification is required both in terms of material properties (§192.607) and maximum allowable pressure (MAOP) reconfirmation (§192.624). This verification on a large scale will be difficult and expensive using traditional destructive testing, which requires shutting down the pipe, cutting coupons and testing in a metallurgy lab. Yet, the alternative of segment replacement or pressure reduction of product flow through the pipe often is even less economically feasible.
Mega Challenges
With the implementation of the Mega Rule, U.S. pipeline owners and operators will be required to provide traceable, verifiable and complete (TVC) records that confirm the physical and operational characteristics of the pipeline meet the new requirements.
That in itself poses a challenge, but with a pipeline network that includes lines that were installed more than half a century ago, prior to the adoption of pipeline regulations that outline requirements for material records, asset owners have been presented with a formidable and very costly task.
Locating the original documents is one challenge. Providing correct, current documents is another. Changes have been made over the years, but where records exist for older lines, they often are available only in paper form, with no way to verify the records are up to date and accurate. In many cases, there are no records at all.
In the absence of TVC records, hundreds of thousands of miles of aging pipeline will have to be tested to ensure line safety. Because of the scope and complexity of this problem, validation will take place over time. Clearly, this is going to be an ongoing exercise, and it will require considerable investment.
In parallel, state and federal regulations for pipeline integrity management are becoming more stringent, which means compliance could be even more expensive in the coming years. As with most expenditures, putting off addressing the problem will likely mean that it will cost even more down the road.
This paints a sobering picture.
A component of this mandate is testing to accurately determine material records. More precisely, the rule states that for applicable assets without TVC documents, material verification must be implemented opportunistically and in conformance with §192.607 whenever the lines are exposed through ongoing integrity management operations. This includes pipelines subject to new requirements in §192.624 for reconfirming the MAOP. That is a tall order.
Still, the industry is committed to a “zero incidents” mission, and there is a broad mandate for improved safety and environmental stewardship through better integrity management. For the last decade, this has been a substantial need that could not be met effectively or within a reasonable timeframe using traditional verification methods. Pipeline owners need a safe and economical alternative to cutting a standardized sample of material for destructive tensile testing in a lab.
To address this situation, the industry has spent more than $3 million – contributed through Pipeline Research Council Institute (PRCI), Gas Technology Institute (GTI) and joint industry project (JIP) research, development and validation projects – to prove the concept of alternative in situ nondestructive evaluation (NDE) processes for materials verification. The goal is for new cost-effective technologies to enable reliable material verification without service interruption and pipe cutouts.
In Situ Testing
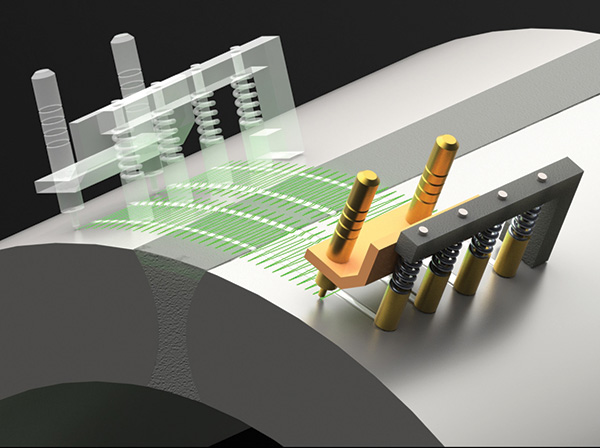
The three main methods that have been used in the pipeline industry for estimating material properties as part of NDE are hardness testing, instrumented indentation testing (IIT) and frictional sliding.
Hardness testing has a number of limitations and generally correlates better with other properties than the yield strength, which defines the grade of the pipeline and is specifically required by the new regulation.
IIT uses a spherical stylus subjected to a series of indentations with increasing loads to measure the flow strength of a material under increasing strain. By evaluating the collected data, it is possible to measure the ability of a material to resist permanent plastic deformation.
Frictional sliding tests use styluses to engage a sample surface under a known load and then travels along the surface at a constant velocity to generate a permanent shadow groove. During a test, the normal force applied to the stylus and the width of the groove is measured and used to calculate the hardness of the material being tested.
Compared to IIT methods, frictional sliding samples more data during a single test and monitors local changes in material properties during the course of a test.
The Hardness, Strength and Ductility (HSD) Tester, developed by Massachusetts Materials Technol-ogies, LLC (MMT), was designed on the foundation of frictional sliding technology and takes in situ NDE to a greater level of precision. The HSD Tester is distinct from alternative NDE instruments because it performs a frictional sliding experiment in which multiple styluses with dissimilar geometries travel along a sample surface to continuously measure the material response.
The combination of styluses collects more than 800 data points per sample to reliably measure the material response. In addition to an abundance of data, frictional sliding allows the HSD Tester to detect material variation, and the patented design is not affected by vibrations, making the results more dependable than other test methods.
The tester can identify low-frequency or high-frequency electric-resistance-welded (ERW) seams and accurately measure yield strength and ultimate tensile strength of in-service pipelines without sample removal or service interruption. It reliably tests seamless or seam-welded pipes and can test complex shapes and fittings like elbows and T-joints.
The tool is portable and, because the tool requires fewer dig locations to meet new regulatory confidence requirements than other competing technologies, it can quickly deliver reliable data for improved decision-making. With this technology, it is possible to get lab-quality data in the field without cutouts or service disruption.
PRCI Validation
A PRCI validation program, which was carried out in 2017, evaluated the HSD Tester in a blind testing study to ascertain its ability to accurately determine pipeline strength. The study evaluated other portable NDE solutions and methods that combine ball indentation with measurements of the steel chemistry.
The program included testing on 50 pipe samples of varying grades, vintages, seam types and geometries that were selected to be representative of existing pipeline assets.
The results of the PRCI program show the HSD Tester exceeds all other methods in all performance criteria and has the fewest nonconservative predictions, where the NDE method determines a higher strength than the actual lab value.
Source |
Average Difference from Lab |
Tool Uncertainty |
Correlation Coefficient |
MMT (PRCI) |
7.0% |
4.0 ksi |
0.70 |
MMT (2019) |
5.2% |
3.0 ksi |
0.85 |
Putting the Tool to Work
In 2018, MMT began helping a company develop quality TVC records on gas transmission systems in five states with varying levels of existing documentation. Following an integrity management program developed from external corrosion direct assessment (ECDA) and inline inspection (ILI) results, technicians used the HSD Tester at more than 80 dig locations, including areas where the exposed pipeline had ERW long-seam welds.
Results confirmed strength above the expected grade in every instance except for one, where a joint was identified as having lower than the minimum expected yield strength. This finding was verified by the operator through additional assessment, which concluded the sample had been expanded from a prior pressure test.
Using field data gathered in situ, the owner capitalized on this technology to develop an accurate asset-specific integrity database. The company is using this data to enable informed capital allocation for specific, targeted improvements and repairs.
On field implementation in more than 50 line segments in which the pipeline operator communicated with MMT the expected grade for the pipeline, the results returned with lower than expected grade on only one line segment. In the context of the intent of the new regulation, it appears that testing for material properties most generally will lead to a confirmation rather than leading to more remedial actions than already required as part of integrity programs.
Collecting new material verification data also can lead to opportunities to reduce inspections and repairs. In one recent application, the HSD Tester provided critical hardness data at the bondline of an ERW weld for a pipeline operator who needed to characterize the seam type and evaluate the potential risk.
The operator was able to rapidly isolate welds with bondline hardness above the maximum criteria and greatly reduce the remedial actions associated with a long seam rupture threat for this asset.
Cost-Effective Compliance
Gathering high-quality data using frictional sliding technology improves decision-making and helps companies intelligently allocate financial resources to achieve compliance goals.
With the enormous amount of work that needs to be done to meet Mega Rule requirements, pipeline owners need to get the best results in the shortest time with the least disruption to day-to-day operations. Having the ability to quickly test pipelines in situ using frictional sliding technology enables owners to focus their efforts on at-risk pipelines and avoid spending unnecessary time making repairs and replacements.
Preparation for new regulations through industry-sponsored R&D programs, such as the work by PRCI and recent case studies of field implementation, have laid the groundwork for the industry. This foundation will provide support for pipeline operators working to meet the added challenges posed by the new regulation.
Comments