October 2020, Vol. 247, No. 10
Features
Kentucky Utility Benefits from New PHMSA Mega Rule
Special to Pipeline & Gas Journal
High-pressure gas pipeline completed by Henderson Municipal Gas (HMG) in Kentucky utilized pipe made from polyamide 12 (PA 12), which is now approved for use under the new the U.S. Department of Transportation’s Pipeline and Hazardous Materials Safety administration (PHMSA) Mega Rule. The pipe is rated at 200 psi (14 bar), which can accommodate the pressure range HMG requires.
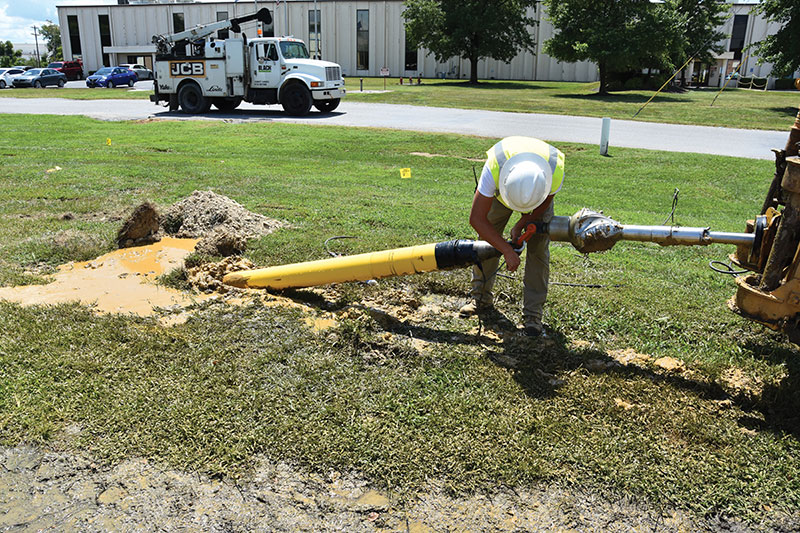
Completed in 2019, the multistage project saw a total of 2,720 feet (829 meters) of the 6-inch (152-mm) SDR 13.5 pipe manufactured by Teel Plastics, of Baraboo, Wisc., installed using trenching and horizontal directional drilling. The project won the Plastics Pipe Institute’s (PPI) Energy Piping Systems Division Project of the Year award for Teel.
“This project marked the first PA 12 installation under the PHMSA Mega Rule effective January 2019, which accepts PA 12,” said Randy Knapp, engineering director of the Energy Piping Systems Division of PPI. “Prior to being incorporated by reference into the federal code, PA 12 projects would require a special permit.”
Because an application would have to be filed for each individual project, the process was difficult and lengthy, requiring a coordinated effort between the pipe manufacturer, system designers, installers, state regulators and PHMSA.
“Naturally, this would take a lot of time and people,” Knapp added, “That is why the new PHMSA Mega Rule is significant and highly beneficial to utilities and their customers.”
PA 12 is an innovative material suited for high-pressure gas applications, which has been used internationally for years. In the United States, however, PA 12 had previously been installed only via special regulatory waivers. The new Mega Rule approved the use of plastic pipe for a greater range of high-pressure applications in the U.S., eliminating the waiver process for PA 12 and making it available for wider use.
HMG was drawn to PA 12 pipe with a 200-psi rating primarily for its ease of installation compared to steel. Considering all budgetary criteria for the project, the total installed cost for using the pipe was less expensive than steel, according to PPI. Plus, unlike steel, PA 12 does not require cathodic protection, saving extra labor, materials and long-term monitoring.
“The PA 12 fusion process was much easier and faster than welding steel would have been, saving HMG significant time and labor,” said Owen Reeves, gas system director of HMG.
Located on the Ohio River, west of Louisville, Henderson has a population of nearly 30,000. Established in 1859, Henderson Municipal Gas is the fifth-oldest system in the U.S. It serves the natural gas needs of the city of Henderson, adjacent areas and the City of Corydon. It has 8,400 residential, 1,100 commercial and 50 industrial customers. Annual throughput is 3.1 Bcf (88 MMcm). In July 2020, HMG was named a winner in the American Public Gas Association (AGA) for its safety record during 2019.
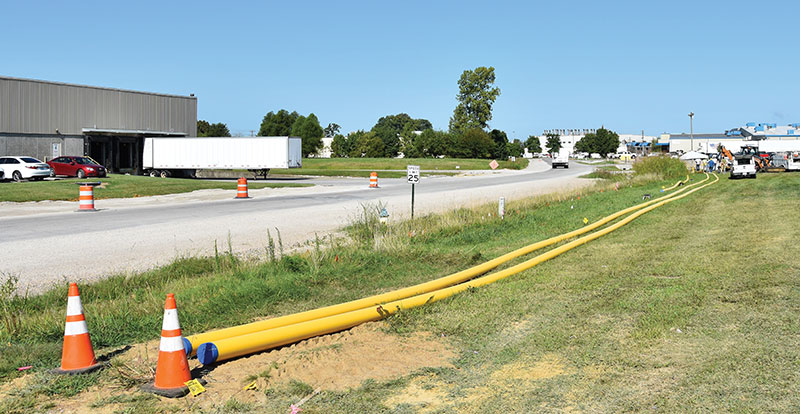
HMG installed the pipe through an industrialized area of the city, with the county and the city able to acquire a grant to widen the roadway in one of the industrial sectors.
“A lot of trucks and cars go up and down that road, and it was in poor condition,” Reeves said. “The issue was that the gas line was on the edge of the existing asphalt, and we didn’t want to be underneath the new, widened road.”
The existing line was steel, epoxy-coated pipe, which has been HMG’s traditional choice for 125 psi (8.62 bar) or greater pressure. The concern, however, was with several building entrances on either side of the road.
“Some of these companies run three shifts – a lot of vehicles run up and down that road,” Reeves said. “The problem was how were we going to stage the epoxy steel pipe for welding, get it connected, X-rayed and get it in the ground.”
In this area, HMG could operate at 90 psi (6.2 bar) with the prior pipe, but the company wanted the ability to go up to 200 psi, in case of future expansion. HMG considered increasing its capability to 250 psi using PA 12, but that would have been significantly more expensive and was deemed to be more than necessary.
Reeves said that PA 12 and PA 11 have been discussed in the industry for a long time, as it would make it feasible to fuse together in a faster manner, and make the overall job much easier.
“We called our state inspectors and said we would like to use PA 11 or PA 12,” he explained. “And because it had been used in other places, we asked them to take that into consideration because they had made special provisions for two other projects in the state. Those, however, were both 4-inch (102-mm) projects. We wanted to increase to 6-inch pipe as well as the higher pressure.”
The inspectors replied that such action would require a special exemption that would take 18 months. HMG decided to start the process and called around to get educated about the two different products. Among those calls were those to Teel and PA 12 resin producer, Evonik.
“The bottom line was that PA 11 comes from castor oil, which might be in limited quantities, and there was really only one manufacturer in the United States at that point in time, and they weren’t producing 6-inch,” he said. “We felt the future would be with the PA 12 so we decided to go with the PA 12 pipe, if our timeframe could be met.”
At the eleventh hour, according to Reeves, PA 12 pipe was approved by the PHMSA Mega Rule, which was perfect timing for the project.
The project went forward because PA 12 can be fused together similarly to polyethylene (PE) which the company already had been using. It requires a little longer time for the PA 12, but the same type of equipment, same principle.
The project required three directional bores, one that connected two 750-foot (229-meter) sections of pipe and one that crossed under the road. The rest was done by a trencher, and some areas were excavated with a backhoe. In all, 2,720 feet of installation was required.
Teel, one of only two PA 12 gas pipe manufacturers in the U.S., provided a specially designed “weak link” mechanism to aid in the installation. These were used in each section of the pipe to help ensure that as it was pulled through the holes, the links would stretch or break in the event of a snag instead of stressing the pipe itself. The installation went smoothly, and the links or pipe were not damaged.
“This project demonstrates the benefits and costs savings of a new plastic pipe material that could open new opportunities to plastic pipe manufacturers as they seek to offer viable alternatives to steel,” offered David Fink, president of PPI. “It serves as a feature project that can be referenced in seeking the wider acceptance and prevalence of PA 12 now that certain legal barriers to its installation have been removed. In short, the success of Henderson’s project helps blaze a trail for an innovative plastic pipe product.”
With a 200-psi rating, PA 12 pipe benefitted HMG as a steel pipe alternative. “Pulling steel pipe, the bored holes would have been more difficult,” Reeves stated, “and the welding required to join steel pipe sections would have required additional manpower and prolonged time in the field. The PA 12 butt fusion process HMG used was much easier and faster, saving HMG significant time and labor.”
Reeves estimated that welding steel pipe would have taken two to three weeks during the first phase of the project, while the PA 12 butt fusion process took only about three days. Each fusion required only about an hour to complete, including alignment and placement.
“The job came in on time and under budget. We saved on the welding time that would have been done in the field and so we viewed it as a very good project,” Reeves said. “I would use PA 12 pipe in a heartbeat anywhere under conditions that are more than 125 psi, less than 250 psi and where you do not have very many valves in the line.” Reeves said.
Comments