January 2022, Vol. 249, No. 1
Features
Safety Techniques for Aboveground Natural Gas Pipelines
By Richard McDonough, U.S. Correspondent
There are a variety of techniques used to enhance the safety of aboveground natural gas pipelines. Coatings to minimize corrosion are an example of a safety aspect used by natural gas operators. Robots are deployed to inspect sections of pipelines not easily reviewed by individuals. Bollards and fencing help keep motor vehicles away from key equipment that controls pipelines.
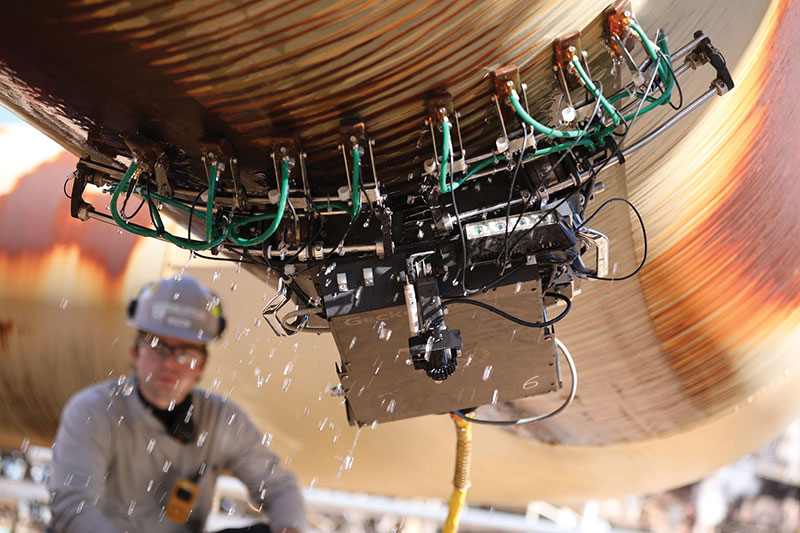
“Each operating company is required to have a written operating plan,” said James Anspach of the American Society of Civil Engineers. “Such protections would be included in their plan. Specific requirements are usually on the state government level, so you will have 50 different agencies for that.”
Additionally, for interstate transmission gas, there are a few safety provisions of aboveground structures in 18 CFR 2.55 Parts A and B. Local and state fire marshals may have even more local requirements.
Robotics
Gecko Robotics is one of the businesses that focuses on using the technology of robots to enhance the safety of natural gas pipelines. The company is headquartered in Pittsburgh, Pennsylvania.
It also has European Union headquarters in Rotterdam, The Netherlands. Currently, sales at Gecko Robotics are focused primarily in the United States; the firm indicated that it is also working with a number of strategic international customers.
The form “creates, organizes and makes useful the world’s physical data,” starting with critical industries, according to Jake Loosararian, CEO and co-founder of Gecko Robotics.
The wall-climbing robots acquire physical integrity data. The software portal enables clients to evaluate the health of their physical infrastructure in 3D, providing a holistic view of their assets and prioritizing areas that need urgent intervention.
“Our wall-climbing robot is only the face of the platform; what really sets us apart is the whole stack,” Loosararian said. “Our data processing pipelines ensure that we’re transmitting the same ground truth in a human-readable form. Our full-coverage corrosion maps and inspection reports leverage the irreplaceable data collected by our robots to identify exactly where a replacement is required, where repairs will be sufficient, and where to focus future monitoring efforts. Finally, our cloud platform allows operational data at the plant level to inform strategic decisions at the corporate level.”
Gecko’s robots climb the surfaces of infrastructure like pipes, tanks and towers, monitoring for structural weakness, weld cracks, corrosion and blistering. They can go places human inspectors either cannot or should not. When problems are detected, users are notified immediately.
Of course, external forces affected business operations in 2021.
“While COVID-19 forced budget and labor shortfalls in power and oil and gas, it increased budgets for our manufacturing and petrochemical customers, so we saw the most amount of corresponding growth in those areas,” Loosararian said. “With events ranging from the Texas power crisis to the ongoing supply chain difficulties, people are realizing that a lot of the things we take for granted, we no longer can. But there is a lot we can do to improve the reliability and resilience of our essential industries – beginning with infrastructure.”
Growth is anticipated to continue in 2022 at Gecko Robotics, with projections of more than two times revenue growth – much of that growth is anticipated due to infrastructure work.
From 2015 to 2020, the number of annual blackouts in the U.S. doubled. This trend will continue to accelerate with an increase in energy demand, age of the workforce, labor shortages and aging infrastructure, according to Loosararian.
“Our grid is fragile,” he said. “Demand for solving real problems has accelerated in these critical industries … have high conviction that we’re building things that need to be built regardless and will aid in extending the life of legacy assets while facilitating transitions to new ones.”
The clear items hanging in the air are called ‘coupling water,’” according to a representative of Gecko Robotics. “It’s what allows the ultrasonic signal from the robot to enter the metal.”
Burnishing
Lambda Technologies, headquartered in Cincinnati, Ohio, provides a wide variety of laboratory services and highly controlled mechanical surface treatments and provides solutions to mitigate metal fatigue, stress corrosion cracking, corrosion fatigue, fretting, stress concentrations and other damage mechanisms.
“OEMs, end users and repair-overhaul service providers are trying to solve fatigue and stress corrosion cracking issues,” said Michael Prevéy, vice president of Engineering and Manufacturing at Surface Enhancement Technologies, a part of Lambda Technologies Group. “If it’s made of metal, then our surface treatments will improve the fatigue and stress corrosion performance without altering the material or design.”
Among the surface enhancement services offered by this firm are burnishing, low-plasticity burnishing (LPB), directed peening, optimized shot peening and residual stress engineering services.
“LPB and directed peening have both been used in applications to improve the service life of fracking pumps and general piping,” said Prevéy. “Fracking pumps can develop fatigue cracks in the cross-bore after enough erosion and pump cycles have taken place. The deep, stable compressive stress induced by surface treatment improved the damage tolerance of the cross-bore by 400%.”
Pipe couplings can develop cracks from pressure cycling and can be susceptible to stress corrosion cracking (SCC) in corrosive environments. The compressive residual stress from the LPB process improved pipe performance in a standard NACE SCC test by 20 times, he said.
Detecting damage in natural gas pipelines may be difficult and that damage can greatly reduce its service life. The damage can potentially lead to a fatigue crack initiation and a premature, unexpected failure of the component. An engineered compressive layer we provide by surface treatment increases the damage tolerance and fatigue life of components to eliminate failure and provide a more predictable fatigue life.
“This reduces part replacement costs and down time in any pipeline. Mitigating the various damage mechanisms facing aboveground pipelines keeps production rates steady, prevents leaks and saves money,” according to said Prevéy.
While the COVID-19 pandemic affected Lambda Technologies, business picked up before 2021 was over.
“Customers are interested in extending equipment life rather than just replacing it,” he said. “This is a trend across most of the industries we work in. We’ve seen an increase in interest of over 20% compared to 2020. We expect to see 40% growth in 2022 and beyond.”
Physical Barriers
One of the two largest causes of distribution incidents, according to Christina Same, senior vice president, Safety, Operations and Security of the American Gas Association, is “…vehicles that run into meters and other aboveground equipment.”
To prevent damage to meters and other aboveground equipment, operators install physical barriers, such as bollards and fences, or may plant thick bushes around the area to be protected.
Safety of natural gas pipelines and associated equipment is not just an important issue for operators. Property owners also have a stake in safety operations. This is especially true for connections to pipelines as well as for equipment controlling access to natural gas service.
A stationary engineer who works with a portfolio of commercial properties in Chicago, Illinois, and asked not to be named, noted examples of how he helped to enhance natural gas connections.
He explained that when he toured a commercial property, he “…found the natural gas main feeding the property completely unprotected from accidental vehicle strikes in the back alleyway of the facility.”
The alleyway that he spoke of is commonly used by service and customer vehicles to access various areas of the property, including a retail loading dock and a lower-level parking garage.
“I immediately prioritized the installation of eight, 6-inch concrete bollards around the gas main, regulators, and metering devices, which took place within a few months,” he said.
While waiting for bollard installation, he had the gas lines painted a high-visibility yellow color and added natural gas stickers and clear signage, adding that 8-foot-tall protective fencing was also planned.
Another property he oversees has an aboveground natural gas main feed located directly adjacent to its 400-space parking garage entrance.
“In this case, the bulk of the gas regulators and metering devices were protected within the parking garage structure, but the gas main itself is located outside the exterior wall of the structure, which runs along a busy street,” he said.
Installation of 6-foot concrete bollards was prioritized to protect the main from incidental vehicle strikes.
Author: Richard McDonough writes about energy infrastructure-related issues in the United States, including the column “The Nuacht Of Pipelines.” He can be reached at newsaboutamerica@gmx.us.
Comments