September 2023, Vol. 250, No. 9
Tech Notes
LNG Custody Transfer System Provides Transparency
By John de Viet, Solutions Development Manager, Krohne
(P&GJ) — With the skyrocketing cost of fuel, the value of any mistakes made while loading and unloading liquid natural gas (LNG) carriers is increasing. This makes it even more important for plant and instrumentation managers to have access to the most accurate measurement tools.
New automated systems provide transparency in measuring fuel quantity and quality, improving trust between buyer and seller. These new tools can reduce maintenance costs by as much as 25-50% annually and can also avoid costly disputes at terminals, estimated at between $1 million and $10 million per year.
Loading and unloading of liquid natural gas (LNG) carriers requires documentation of both the quantity and quality of the LNG transferred. As per gas sales purchase agreement (GSPA) this information, recorded in a quality certificate, and a bill of lading, is usually derived from multiple instruments and independently operated systems.
Plant managers have typically used manual data collection, calculation, and verification systems to obtain the required information.
Quantity is typically determined with level measurements taken on the LNG vessel; these measurements are the input for the bill of lading. Quality is determined in a laboratory using samples collected during the (un)loading operation, with the results used to prepare the quality certificate.
Data is manually processed primarily in Excel-based worksheets, without traceable references to instrument uncertainties and standards and with no dynamic validation.
Accurate calculations have been made even more complicated by the fact that LNG is a mixture of gas and liquid. Unlike transfer standards for oil or gas, which are well-defined and well known, those for LNG are less advanced.
Many operators have had to rely on collecting information from independent systems doing just a portion of the measurements, with no one fully integrated measurement system. The existing manual quantity and quality data collection systems have led to a variety of potential problems:
- Introduction of human error during data collection.
- Certificates of quality are produced using distributed control system (DCS) historians or external plant information systems, including the PI real-time data management software and MS Excel. None of these systems are designed and dedicated for custody transfer applications.
- Data is transferred through multiple interfaces with the possible loss of resolution or loss of data due to filtering (ISO demands up to sixth decimal point).
- Calculations have not been validated or certified by an independent body, such as NMi
- Quality data is not traceable, and measurements are often not in compliance with ISO/GPA standards
- There is no dynamic validation of data while LNG loading is in progress
- Validation of data is often done after the shipload, with no way of reconciling if equipment had developed faults during the loading
- Contractual clauses differ, which could lead to incorrect interpretations and calculations
- Overall loading system is difficult for authorities to audit
Eliminate Disputes
New automated systems are now available that eliminate uncertainty disputes, reduce maintenance costs, and make loading and unloading of LNG carriers at terminals easier and more efficient.
Among these is the Krohne LNG-Quality Release System (L-QRS), a software offering that collects all relevant information needed to determine the amount of energy transferred during LNG vessel loading and unloading operations. for a graphic (Figure 1) overview of typical loading/unloading points in the LNG value chain.
This automated system processes information in a flow computer to allow the operator real time monitoring of batch quantity and quality.
It uses on-line measurements and certified statistical calculations, including quality and outlier calculations, energy calculations, loading mass balance and billing reports on vapor returns. A gas chromatograph analyzes samples in real-time while the ship is being loaded (Figure 2).
The applied flow computer software provides the quality release certificate and the bill of lading instantaneously once the batch is completed. Instant availability of bill of lading and quality certificates avoids costly retrospective corrections of the bill of lading and quality certificates once the vessel has departed.
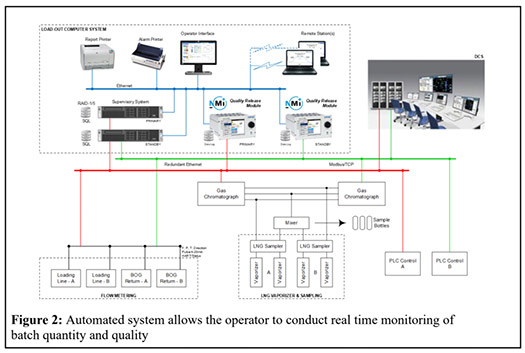
The system incorporates an analyzer management and data acquisition system, which ensures full traceability of the instrumentation and optimizes maintenance cycles. Estimates suggest that maintenance costs can be reduced by 25% to 50%. Data is securely stored and, together with the certified calculation, fully auditable.
The fully automated information flows eliminate human errors in the data processing that can arise when copying measurement data among different systems. Simply avoiding LNG quality disputes has the potential to save terminals from $1million to $10 million per year.
Because the automated system is certified by NMi and compliant with such international standards as ISO 8943, GPA 2172, ASTM 4784, GIIGNL, it also avoids discussions over the amount of energy transferred. Increased availability of critical instruments ensures constant and reliable quality measurements, resulting in less product give-away due to a lower system uncertainty.
Designed for mid-size and large liquefaction and regasification LNG terminals, it can be installed in both new and existing LNG terminals and can be sized to the available infrastructure.
Once the automated system is installed and operational, plant managers experience improvements in maintenance costs, a reduction in the number of disputes, and improved availability, resulting in less product give-away.
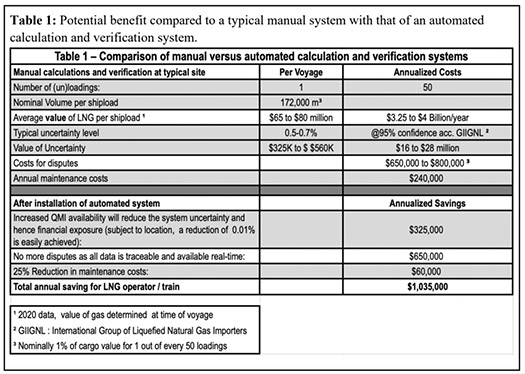
Basic L-QRS functionality is available using only the Summit 8800 flow computer in combination with existing instrumentation. Depending on the level of existing automation, this provides automated calculations, outlier detection, standard reporting and time stamped measurement registration.
The system can be further enhanced with a user-friendly HMI, customized reports and an integrated analyzer/instrument management system. The latter enables the operator to optimize its maintenance program and reduces costs, provides detailed information about instrument availability and full traceability of the calibration records.
Given the increasing expense of fuel and the transitioning of fuel types, LNG operators need more robust and reliable metering and measuring systems. New systems like the L-QRS can go a long way to meet traceable custody transfer data standards while avoiding costly disputes, retroactive corrections and product give-away.
Comments