August 2024, Vol. 251, No. 8
Features
Corrosion Control: Enhancing Protection for Tanks and Pipelines with VCIs
[To explore the full digital edition, including the Page Raft version of this article, click here.]
By Julie Holmquist, Cortec Corporation
(P&GJ) — It is often the most difficult to reach areas that carry the largest corrosion concerns, primarily because they are inherently harder to protect and inspect and more likely to trap corrosives.
Aboveground storage tank (AST) bottoms, cased pipeline crossings and insulated surfaces are among those magnets for corrosion problems. While multiple forms of protection exist, their potential failures make VCIs a valuable technology that can serve as a significant complement to traditional methods of protection.
Oil and gas ASTs are abundant and varied in size, but it is always hard to tell what is going on in the space underneath, where moisture and other corrosives can incite deterioration and thinning of the metal bottom.
Because of the serious nature of this concern, building a tank on a sand pad equipped with cathodic protection (CP) is a standard practice, to reduce the risk of corrosion. At a recent conference hosted by NISTM — the National Institute for Storage Tank Management — one presentation mentioned how tank floors often have more flexing when they are holding less fluid than when they are full, thus bringing some of the metal out of contact with the tank pad.
The presentation also shared how poor choices for sand pad and anode material can result in early failures after just a few years in service, and it suggested that replacing the sand pad and using impressed current cathodic protection (ICCP), instead of sacrificial anodes, can be much more effective1.
These observations underscore some interesting points. First of all, the use of CP does not guarantee that all surfaces of the tank bottom will be protected by CP, since there may be air pockets prohibiting full contact with the sand pad current. Secondly, the installation of a new sand pad or ICCP after the tank is in service — even if effective — can be a costly, difficult procedure.
Another issue that is not mentioned above is the fact that ICCP does not work without a constant source of power, leaving ASTs without protection during a planned or unplanned power outage.
Vapor corrosion inhibitors (VCIs) serve as an excellent complement to traditional CP. Because of their vapor-phase characteristics, VCIs vaporize out of a solid (e.g., a powder) or liquid and disperse throughout void spaces, searching for equilibrium.
When they reach this state of even dispersion, they adsorb on the surface of the metal, creating a molecular hydrophobic protective layer that inhibits the corrosion reaction. This allows the VCIs to protect areas of the tank that are not in contact with the sand pad and to continue providing protection, even if the ICCP has to be turned off.
VCIs can be injected under the tank without disturbing the structure, even after the tank has been filled — a major cost savings for in-service ASTs. When used along with ER probes, VCIs are designed for a 10-year preservation period.
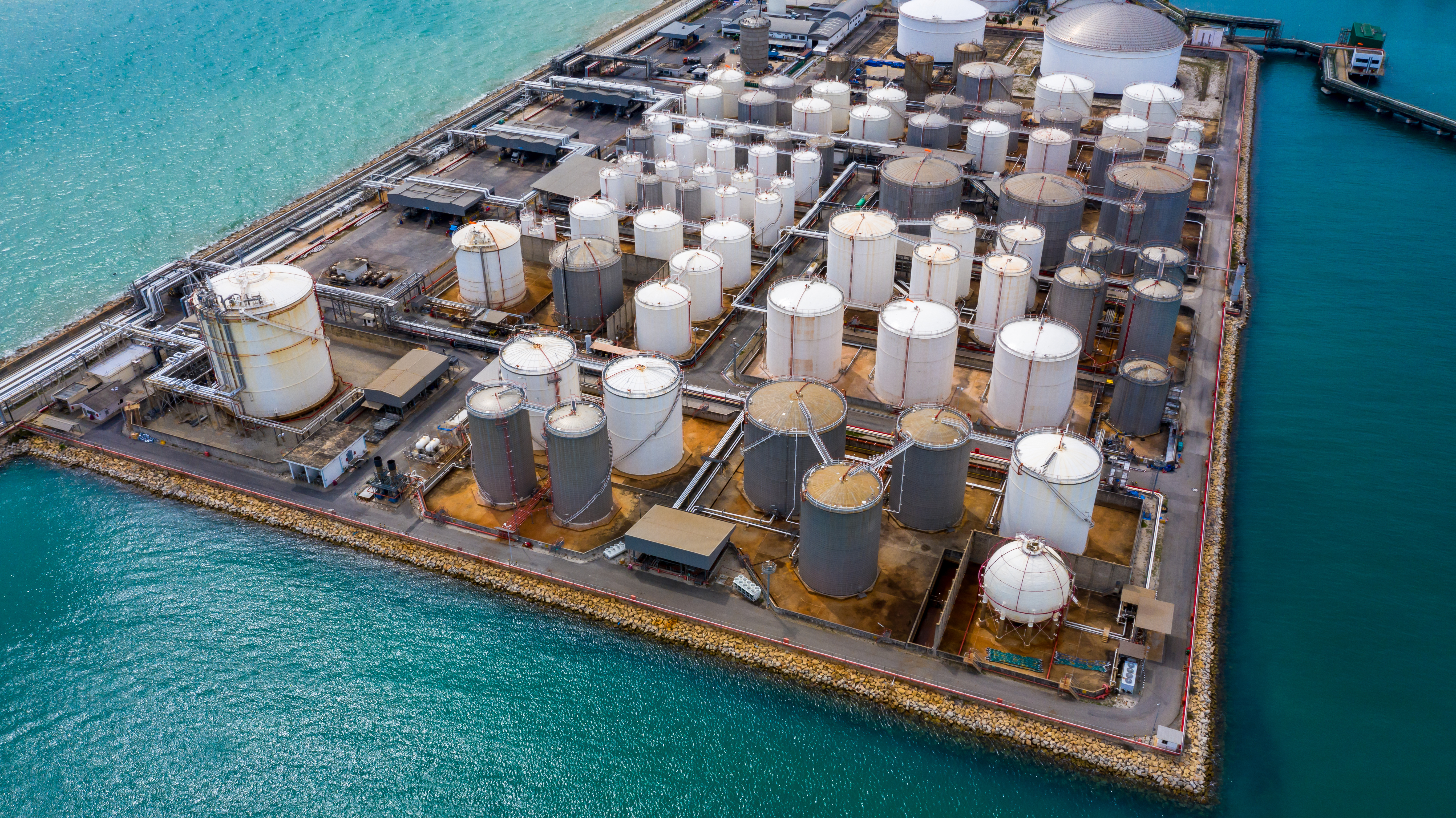
VCIs, as a means for AST protection, have been under observation for more than two decades, and they have recently been enshrined in two industry standards, API Technical Report 6552 and AMPP SP21474-20233, testifying to their growing acceptance.
VCIs have also been used alongside CP, as in the Cushing terminal tank project, where the injection of a VCI slurry in conjunction with CP resulted in much fewer corrosion indications over a five year period than CP alone over the previous three years.4 The time is therefore ripe for expanding the use of VCI technology in the realm of ASTs.
Crossing Conundrum
Another common corrosion challenge for the oil and gas industry is cased pipeline crossings. In 2019, a topic paper for the National Petroleum Council (NPC) identified four possible cased pipeline crossing conditions resulting from the following factors: a wet or dry environment, combined with either an electrically isolated casing or an electrical short (e.g., casing touching the carrier pipe).
Unfortunately, the most corrosive scenario — wet with an electrical short that shields the pipe from cathodic protection — is the most corrosive, and it is a fact of life in the US.5 Coatings can also prove deficient.
Here again, VCIs offer a complementary solution where other protective methods are lacking in hard-to-reach areas. Cortec Corporation introduced and patented the concept of adding VCIs to a gel filler that is pumped into the pipeline casing.
The gel helps protect against the ingress of various contaminants and water. However, the liquid-phase and vapor-phase action of the inhibitor molecules means they do not need to be directly applied to the carrier pipe in order to provide protection. The VCIs have freedom to migrate through air space or water and under disbonded coatings, to offer protection even when CP and coatings fail, thus offering a complementary source of corrosion inhibition.
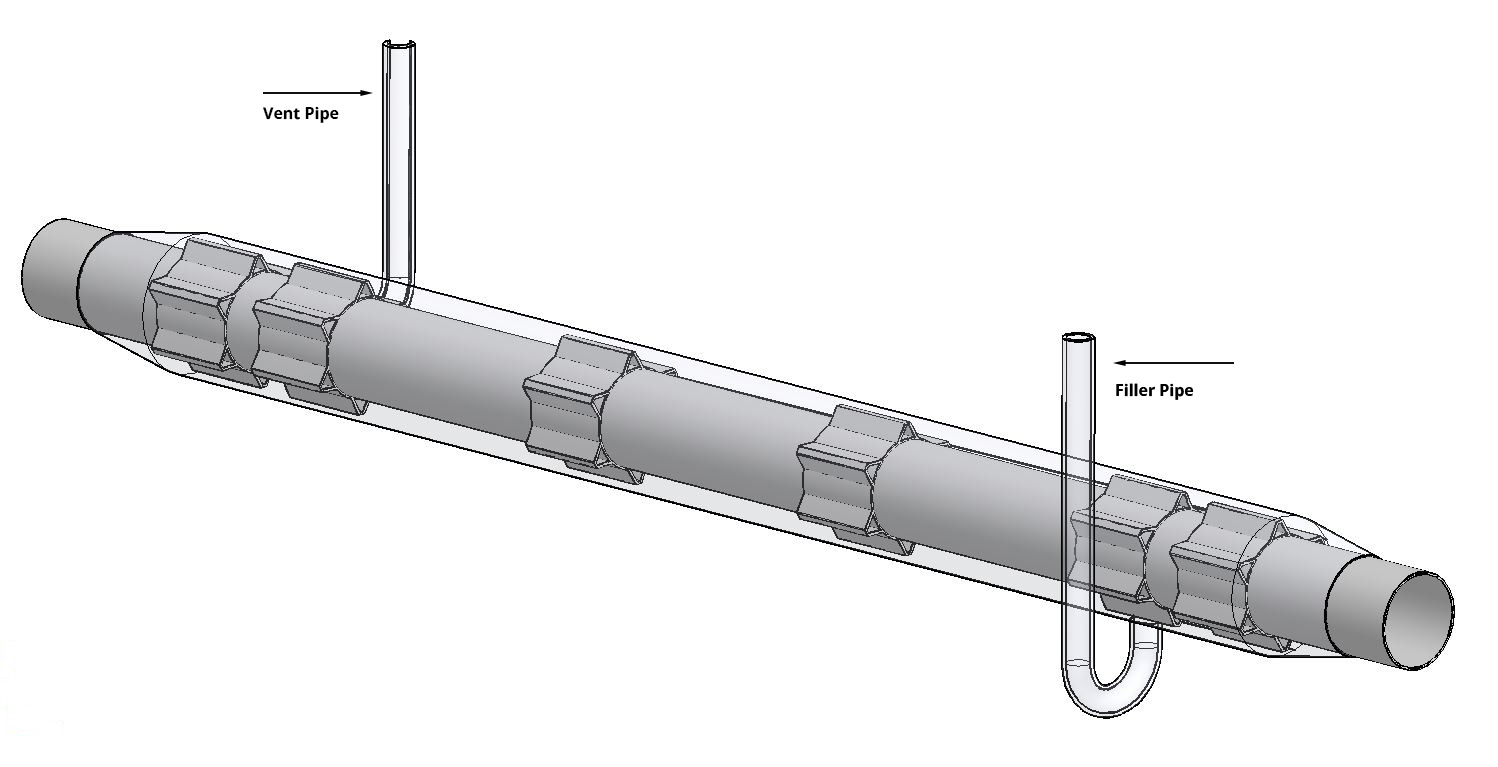
Beneath the Insulation
A third area of concern is the insulation on pipelines or tanks, which traps moisture and other corrosives next to the surface of the metal and hides any corrosion problems that may follow. Temperature cycling and cold surfaces further aggravate the risk, by increasing the likelihood of condensation on the insulated surface.
A PHMSA advisory bulletin offers a startling reminder of the seriousness of this type of problem by relating an incident in 2015, when a buried, insulated crude oil pipeline in Santa Barbara County, California, ruptured due to corrosion under an insulated coating.
Even though the pipeline had been recently inspected, thinning of the wall, due to corrosion at the site of the rupture, was much more serious than detected. The rupture was sudden, releasing approximately 2,934 barrels of oil into the environment. The pipeline had been coated with a coal tar urethane coating, followed by foam insulation, tape wrap and shrink wrap sleeves.
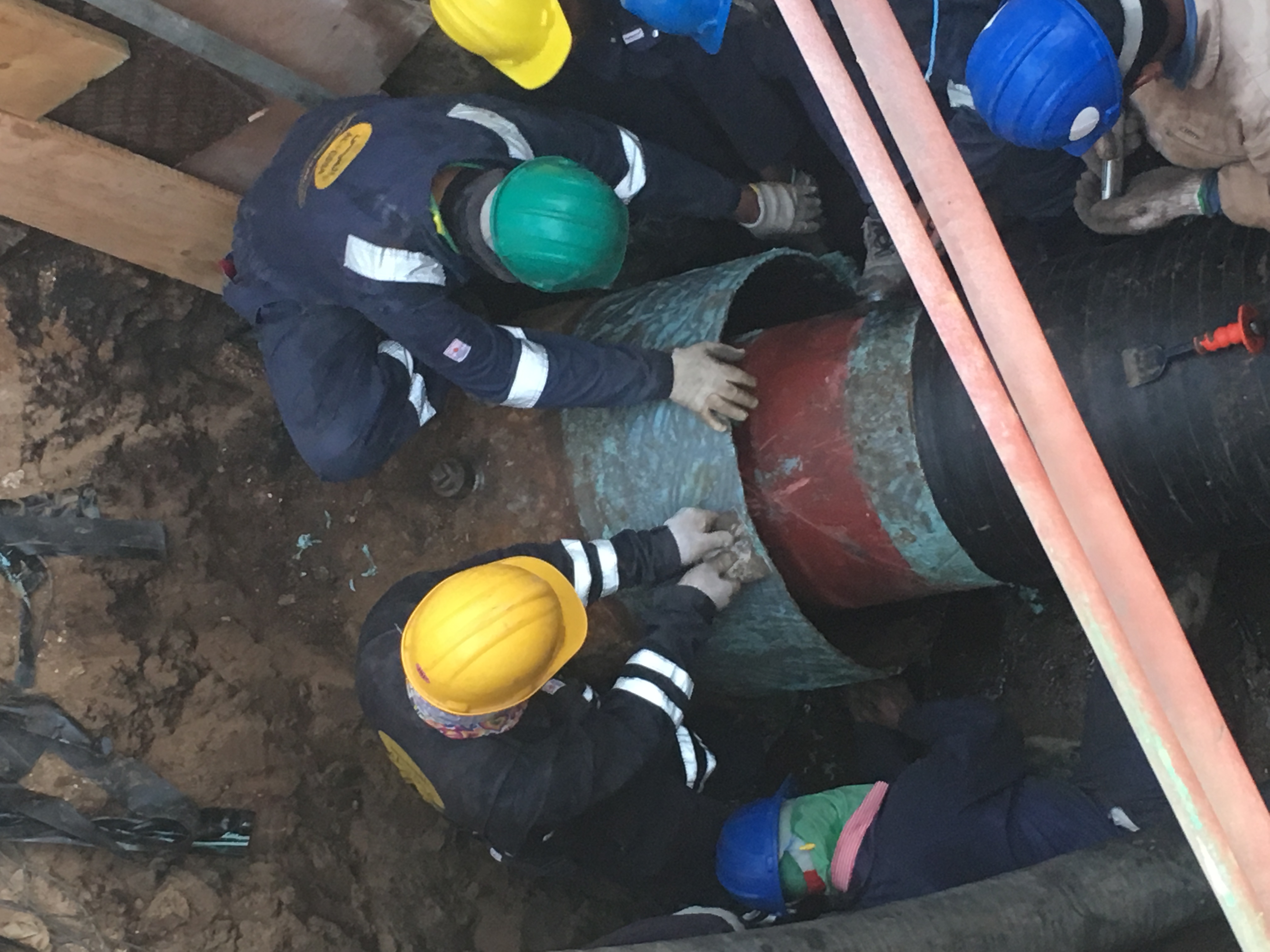
Moisture was found under the insulation, and wet-dry cycling was also blamed. CP was deemed ineffective, and the advisory note stated that “Corrosion under insulation (CUI) is recognized as an integrity threat difficult to address through conventional cathodic protection systems and can lead to accelerated wall-loss corrosion and stress corrosion cracking of the pipe steel6.”
As with cased pipeline crossings, coatings and CP for insulated surfaces are protection strategies that are not failproof. In fact, insulation can be a shielding mechanism for CP, by creating resistance to the CP current7.
Another challenge is that coatings can be applied to new surfaces but cannot be applied to those that are already insulated — without removing and replacing the insulation, very much limiting options for mitigation under existing insulation. VCIs offer a third approach that can adapt to this obstacle.
Again, because of their ability to migrate through air spaces, VCIs can be injected directly into insulation at periodic intervals and allowed to diffuse and form a protective molecular layer along the insulated metal surface. Injectable VCIs for CUI have been developed for surfaces reaching temperatures as high as 662° F (350° C). This technology is one that should be explored further for its potential benefits to pipelines and tanks where CP shielding is feared or where renewal of corrosion protection is desired, but where it does not yet make sense to remove or replace the insulation.
Complement Time
The oil and gas industry continues to assess and adopt new methods of corrosion protection in a variety of areas. While corrosion will never fully go away, there are many ways to lessen its seriousness.
VCIs stand out as an important means to complement traditional methods of corrosion protection, especially in difficult-to-reach areas, and they should be considered by those responsible for ASTs, cased pipeline crossings and insulated surfaces.
Author: Julie Holmquist (jholmquist@cortecvci.com) has been writing about corrosion problems and solutions in oil and gas and many other industries since starting at Cortec® Corporation (https://www.cortecvci.com/) in 2015.
Comments