March 2024, Vol. 251, No. 3
Features
Experts See Polymers Among Keys to Better Pipe Protection
By Richard McDonough, U.S. Correspondent
(P&GJ) — Leaders within the coatings industry have indicated that there are a number of innovative products and services that have been developed recently, which enhance corrosion control and provide better pipeline coatings. In addition, several technologies are being tested, along with research projects underway both in the lab and in the field.
“Some of the products that have been developed are remote monitoring, to provide real-time 24-hour monitoring of corrosion prevention systems installed on assets, for pipelines and storage tanks in hazardous and nonhazardous areas,” said Dr. Kimberly-Joy Harris, Manager, Pipeline Integrity and Corrosion at EnLink Midstream and Vice Chair of the Board of Directors for the Association for Materials Protection and Performance (AMPP).
She noted that “Power BI database technology is recently being used to monitor several systems in real-time and for providing KPIs [Key Performance Indicators] on progress of both corrosion prevention and coating assessments.”
With more than 30 years of expertise in the energy sector, Harris has specialized in leading and consulting on projects that enhance asset integrity and sustainability, efficiency and innovation. She holds two master’s degrees — one in energy transition from the University of Texas at Austin and the other in organizational leadership from Colorado Christian University.
Harris said several innovative products are being tested to determine if they may enhance corrosion control and provide better pipeline coatings. Among those are “…advanced long-range drone monitoring, smartpipe technologies that will in some cases replace traditional pipeline systems, [and] remote monitoring technology for corrosion control being used to monitor buried leak detection sensor systems via the web.”
She noted that “…nanocoating technology systems are constantly being tested/evaluated for their ability to self-clean, self-repair.”
A number of research projects that are also underway involve technologies focused on pipelines. One that she cited involves digital-twinning, to replicate pipeline systems using machine learning with virtual modeling.
She explained that this technology “could take data for corrosion prevention [internal/external corrosion prevention data and various types of coating] and determine threat areas of focus along the system, to ensure correct placement of devices for monitoring as well as coating-type applicability.”
In addition, Harris said that there is constant research with inline inspection tool technology, for corrosion prevention monitoring and coating assessments, as well as the continued evolution of Power BI technology.
Coating Innovation
Among those actively involved in providing coatings for use in pipelines is MacDermid Enthone Industrial Solutions, a developer of electroless nickel (EN) use for pipeline corrosion protection. EN coatings are highly corrosion- and virtually pore-free barriers.
“These coatings have been used to protect specialized components in this highly demanding market for many decades,” said Ambrose Schaffer, global product line manager of Electroless Nickel at the company. “Recent advancements in this exciting technology have shown the exceptional chemical inertness electroless nickel typically demonstrates, especially in the corrosive environments associated with petrochemicals.”
He said that High P (phosphorus) electroless nickel (>10.5% weight by weight [w/w] P) is the alloy of choice for pipeline and related component applications.
“The next generation of alloys incorporates an additional alloying constituent into the High P matrix at relatively low concentrations (i.e., 1-2% w/w) to significantly reduce porosity and improve the amorphous nature of the deposit,” Schaffer said. “This results in enhanced corrosion resistance of the coating by a dramatic margin.”
Alloy Performance
Different types of alloys can be considered high-performing for use in pipelines.
“Generally speaking, there is a spectrum of alloys that can be used for transporting hydrocarbons, depending on how corrosive the hydrocarbons are,” said Gary Whelan, a senior materials design engineer at QuesTek Innovations. “If the hydrocarbons are relatively non-corrosive, simple carbon-steel can be used, and as the corrosiveness increases, you would want to include more chromium, tending toward stainless steel, which is inherently more expensive but also higher performance.”
He added that for highly corrosive hydrocarbons we might consider nickel alloys, which are sometimes referred to as corrosion-resistant alloys in the oil and gas business.
Whelan has experience using integrated computational materials engineering (ICME), to model process-structure-property relationships for metal alloys of various material classes, including steel, aluminum, nickel and titanium. His research has primarily focused on physics-based simulation and machine learning applied to fatigue in metallic components, with an emphasis on additive manufacturing.
Among the innovative products that have been developed recently, which enhance corrosion control and provide better pipeline coatings, are ones focused on ICME — a methodology developed over the past 10–20 years to utilize physics-based modeling and simulation to predict process-structure-property relationships in materials.
“This approach is useful in developing coating technology, but more importantly, it is useful in developing high performing alloys, which in many cases subvert the need for coatings in challenging environments like pipelines,” said Whelan.
ICME has been used to develop high-strength corrosion resistant alloys for many applications including those in the oil and gas industry. Recently, QuesTek used this methodology in a software tool called simply ICMD, which is a user-friendly, web-based environment for engineers to use resolving materials challenges.
Whelan noted that additional research is underway on ways to enhance corrosion control and pipeline coatings and on the effects of various alloying elements on general corrosion resistance and grain boundary cohesion in metal alloys.
“Particularly for the latter, there are density functional theory (DFT) simulations and atom probe experiments that can predict and measure the segregation of alloying elements to grain boundaries in metal alloys,” Whelan said, as well as “predicting the effects of those elements on the cohesion of grain boundaries when they are present in high densities.”
He described these efforts like a ball at the top of a hill.
It is kinetically more favorable for the ball to be at the bottom of the hill, so it will tend to roll down the hill; however, if you make the hill less steep, make it sticky or add impediments along the hill to stop the ball, then you can prevent the ball from rolling down the hill.
“In the case of corrosion cracking, hydrogen wants to make free surfaces out of grain boundaries, which means grains separating, which is a form of the overall material cracking,” he said.
This tendency for hydrogen to make grains separate more easily makes the material brittle. The current research focuses on adding impediments to this process, by alloying the metal with elements that will take up all of the spots at the grain boundary and act as cohesive forces to hold the grain boundary together.
The current research focuses on understanding how each element behaves in common materials like steel, nickel, and aluminum, so that we can better design new alloys which are resistant to corrosion cracking, he added.
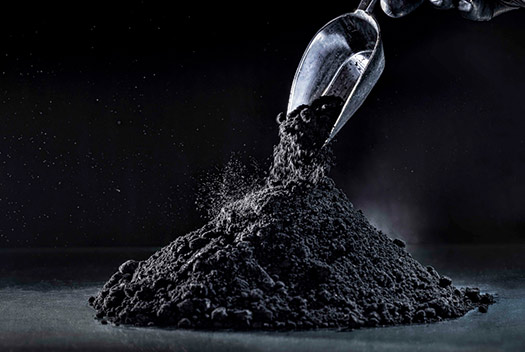
Graphene Driven
A product that may become a major option for enhancing pipeline strengths is graphene, which has been the focus of research in a number of industries.
“Graphene is a powder,” said Dr. Ranjith Divigalpitiya, chief science officer of HydroGraph Clean Power. “It is carbon in its purest form.”
He added that graphene, discovered about 20 years ago, could improve the strengths of coatings on pipelines in certain cases. Specifically, the impact of moisture and the soils could be lessened by the addition of graphene to epoxy coatings.
The company said the exclusive license it acquired from Kansas State University allows it to produce both graphene and hydrogen through a patented detonation process. The graphene produced by HydroGraph is manufactured in Manhattan, Kansas.
“We have seen others working on ways to strengthen steel through the addition of additives to coatings,” Divigalpitiya said. “We have not been approached yet to study the use of graphene in coatings for pipelines. We would be interested if there was a customer demand.”
The graphene produced by HydroGraph is currently being utilized in other ways, some of which impact the oil and gas industry, though.
For example, he said, graphene can be added to oil and grease in lubrication fluids that can prolong the life of equipment using those lubricants.
“The amount of graphene added to another polymer is relatively modest,” said Randall Zajac, director of Business Development – Resins and Composites at HydroGraph. “Graphene is a type of nano-additive. It is both small in size and the percentage used as an addition in a polymer is small. A general range would be 0.1% to 3% added to an epoxy coating.”
The company is currently testing graphene for use in a number of uses in energy, communications, and defense devices and equipment, adding graphene makes improvements in mechanical strengths when used with polymers for energy storage equipment.
“Lots of people are working on polymers to enhance coatings for items like pipelines,” said Divigalpitiya. “We have lots of hope for this technology.”
Author: Richard McDonough writes about energy infrastructure-related issues in the United States, including the column The Nuacht of Pipelines. He can be reached at newsaboutamerica@gmx.us.
Comments