November 2024, Vol. 251, No. 11
Features
P&GJ Executive Interview: PPI Chief Cites Benefits of Plastic Pipelines
By Michael Reed, Editor-in-Chief
(P&GJ) – David Fink was active for more than 20 years in the Plastics Pipe Institute (PPI) before becoming president of the Dallas-based organization in January 2020.
A chemical engineer and chemist by training, Fink has devoted his entire career to plastics, beginning with his work in polyethylene resin at Union Carbide (UC) Corporation and narrowing in focus to resins for pipe applications, after UC’s acquisition by Dow Chemical in 2001.
He then spent 13 years at WL Plastics, one of the largest polyethylene pipe manufacturers in North America, where he managed commercial sales, engineering and business development, serving on the PPI board for several of those years.
Despite taking the reins of PPI at the outset of a global pandemic, Fink saw a bright future for the plastics pipe industry and a growing role for its products across an expanding range of underground applications. He now works diligently to make that vision come true.
P&GJ: Can you tell us who your members are and tell us about the institute’s mission?
David M. Fink: The Plastics Pipe Institute, Inc. (PPI) is a non-profit trade association representing the interests of the plastics pipe industry. Our members are companies involved in the production of plastic resins, additives, pipes, fittings and conduits, as well as the manufacturing of related equipment and the distribution of plastic piping products. We also include industry professionals and international affiliates.
The mission of PPI is centered on improving the quality of life today and for future generations, by advancing the adoption and use of sustainable and resilient plastic pipe systems.
We are committed to advocacy, education and the development of standards that support the widespread use of plastic piping solutions, which are not only cost-effective but also environmentally friendly and durable. PPI operates through five membership divisions: Building & Construction, Drainage, Municipal & Industrial, Power & Communications and Energy Piping Systems, which focuses on gas and oil applications.
P&GJ: Is membership in PPI growing? What geographic regions have shown the most growth?
Fink: Yes, membership within PPI continues to grow steadily. Over the past several years, we have welcomed approximately 10 new member companies each year.
The demand for plastic piping systems has expanded across a variety of sectors, including water and sewer infrastructure, oil and gas, natural gas distribution, industrial and mining applications, telecommunications, and power conduit, as well as for applications like hot- and cold-water plumbing and geothermal systems.
One of the key drivers of this growth has been the recognition of plastic piping materials’ key features and benefits in infrastructure, including how these materials benefit social, environmental and governmental needs (see “Advantages of Plastic.”)
Plastic piping offers significant advantages over traditional materials like steel and reinforced fiberglass in terms of social impact, environmental sustainability, and governmental alignment. It provides safer, more durable, and cost-effective infrastructure solutions that meet the needs of modern energy markets while supporting climate and sustainability initiatives.
Geographically, the growth has been fairly distributed across North America, with new members coming from the United States, Canada, and Mexico. This reflects the broad acceptance of plastic piping solutions as both a practical and innovative approach to meet modern infrastructure needs.
P&GJ: Can you elaborate on the advantages of plastic piping systems in the oil and gas industry, especially regarding horizontal directional drilling (HDD)?
Fink: The oil and gas industry, particularly in applications like gas gathering, distribution and transmission, has increasingly turned to plastic pipe, particularly high-density polyethylene (HDPE) and other advanced polymer materials.
These materials offer distinct advantages over traditional piping options. Plastic pipes are lightweight, flexible and corrosion-resistant, making them ideal for challenging environments, such as those encountered during horizontal directional drilling (HDD).
HDD is a trenchless method of installing pipelines that requires precision and resilience in the materials used. Plastic pipes, with their ability to bend and adapt to the subterranean landscape without the risk of corrosion or joint failure, have proven to be highly effective in such applications.
Furthermore, their installation requires less energy and labor compared to traditional materials, which translates into cost savings and a reduced environmental footprint. Plastic pipes also have a longer service life, making them a more sustainable choice for long-term infrastructure projects in the energy sector.
Through initiatives like our Energy Transportation Advisory Group, PPI works closely with industry stakeholders to establish and refine standards that ensure the safe and reliable use of plastic piping systems in the energy sector. We are dedicated to continuing this work and expanding the role of plastic piping in the oil and gas industry, ensuring a sustainable and resilient future for our infrastructure.
P&GJ: Is membership in PPI growing? What geographic regions have shown the most growth?
Fink: Yes, membership in the Plastics Pipe Institute (PPI) continues to grow steadily, driven by the increasing demand for plastic piping systems across various sectors, including water and sewer infrastructure, oil and gas, natural gas distribution, industrial and mining applications, telecommunications and power conduits. Additionally, there has been strong growth in areas like hot and cold water plumbing, geothermal, and renewable energy infrastructure.
PPI has added approximately ten new member companies annually during the past several years. During the COVID-19 pandemic, plastic piping was deemed essential, allowing the industry to continue its work on both new installations and the rehabilitation of aging infrastructure. This essential designation helped maintain industry momentum, despite global challenges.
Geographically, growth has been fairly evenly distributed across North America, with new members joining from the United States, Canada, and Mexico. However, demand for plastic pipe systems is also rising globally, as the benefits of plastic infrastructure solutions become more widely recognized.
P&GJ: How is demand for plastic pipes in the oil and gas industry compared to five years ago?
Fink: In gas gathering, the demand is currently about 50% lower than in 2018, which was a record year for the industry. However, it has rebounded by 50 percent since the COVID-19 low in 2020. In gas distribution, the demand in 2022 reached an all-time high, surpassing even the strong numbers of 2018. This demonstrates the growing reliance on plastic piping in the energy sector, particularly in distribution networks where the need for safe, durable and cost-effective solutions is critical.
P&GJ: To what degree is PPI involved in establishing industry standards?
Fink: Establishing and maintaining industry standards is a core function of PPI. We are involved in nearly every standards organization across North America, frequently taking leadership roles.
In the oil and gas industry, we work closely with organizations such as ASTM, API, CSA, APGA, ASME and ISO, among others. These collaborations ensure that plastic piping systems meet the highest standards of safety, performance and sustainability, helping to foster wider adoption across energy infrastructure projects.
P&GJ: Are there any other specific challenges or pending regulations facing the industry that PPI and its members are trying to address?
Fink: One of the key challenges we are working on is gaining broader acceptance for spoolable composite piping in regulated applications. We have been collaborating with PHMSA and other regulatory bodies to include these materials in 49 CFR, Part 192. Additionally, as regulatory focus on methane reduction intensifies, plastic piping is well positioned to help utilities meet stricter requirements.
However, we are also facing challenges from efforts to limit natural gas usage in favor of electrification. Despite these challenges, we remain confident that plastic piping will continue to play a critical role in modernizing and improving energy infrastructure.
Advantages of Plastic
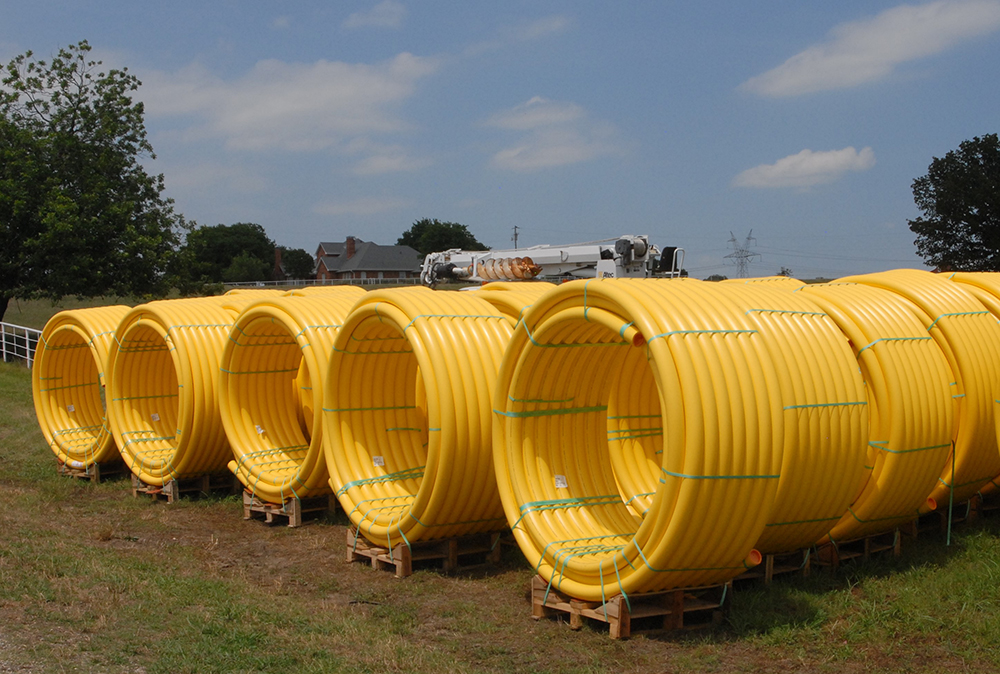
Social, Environmental, and Governmental Advantages of Plastic Piping
Solutions for Energy Markets vs. Traditional Materials (Steel, Reinforced Fiberglass, etc.)
Social Advantages
Reduced Installation Disruption
Plastic Piping: Enables trenchless installation methods like horizontal directional drilling (HDD), pipe bursting and slip-lining, minimizing surface disruptions.
Traditional Materials: Often require open trenching, leading to significant disruptions in urban areas or busy environments.
Benefit: Reduces the impact on local communities, traffic and businesses during construction, making infrastructure upgrades less disruptive to daily life.
Improved Safety
Plastic Piping: Corrosion-resistant and leak-free when properly fused, reducing the risk of system failures, accidents and hazardous leaks, especially in natural gas distribution.
Traditional Materials: Prone to corrosion, leading to leaks, potential explosions and contamination in pipelines.
Benefit: Enhances public safety by reducing the risk of accidents and environmental hazards caused by leaks or system failures.
Job Creation in Emerging Technologies
Plastic Piping: The growing demand for plastic piping systems in energy markets has spurred innovation in installation techniques and technologies, creating new job opportunities.
Traditional Materials: Heavier and more labor-intensive, but lacking the rapid growth seen in advanced plastics and trenchless methods.
Benefit: Supports workforce development in emerging fields, promoting long-term employment opportunities in energy infrastructure.
Environmental Advantages
Lower Carbon Footprint
Plastic Piping: Requires less energy to manufacture, transport and install due to its lightweight properties compared to steel and reinforced fiberglass.
Traditional Materials: Steel and fiberglass have higher production and transportation energy requirements, leading to greater greenhouse gas emissions.
Benefit: Contributes to the reduction of carbon emissions across the energy sector, aligning with global efforts to meet climate change targets.
Corrosion Resistance
Plastic Piping: Does not corrode, eliminating the need for anti-corrosion coatings or frequent maintenance, which can be environmentally damaging.
Traditional Materials: Steel and reinforced fiberglass are susceptible to corrosion, leading to environmental risks from chemical leaks and frequent repairs.
Benefit: Protects ecosystems and water sources from contamination and reduces environmental damage from corrosion-related failures.
Reduced Methane Emissions
Plastic Piping: Monolithic, leak-free installations reduce methane emissions, particularly in natural gas distribution where leaks from older materials are a major concern.
Traditional Materials: Prone to leaks due to joint failures and corrosion, contributing to significant methane emissions.
Benefit: Helps reduce the environmental impact of methane, a potent greenhouse gas, supporting global climate goals.
Sustainable Lifespan and Recyclability
Plastic Piping: Typically has a lifespan of 50–100 years and is often recyclable at the end of its lifecycle.
Traditional Materials: Steel and fiberglass can have a shorter lifespan due to corrosion and are more difficult to recycle without significant energy use.
Benefit: Promotes sustainability by reducing waste, minimizing the need for frequent replacements and supporting a circular economy through recycling.
Governmental Advantages
Regulatory Compliance and Support for Methane Emission Reduction
Plastic Piping: Helps meet government regulations aimed at reducing methane leaks, especially in the natural gas sector where newer materials like polyethylene (PE) and polyamide (PA12) are proven to help lower emissions by keeping the gas/fluid inside the pipe.
Traditional Materials: Steel and fiberglass systems, due to their tendency to leak, struggle to meet increasingly stringent environmental regulations.
Benefit: Plastic piping solutions align with governmental goals to reduce methane emissions and support environmental sustainability.
Easier Regulatory Approvals for Trenchless Technology
Plastic Piping: Recognized by regulatory bodies like PHMSA (Pipeline and Hazardous Materials Safety Administration) for use in trenchless installations, speeding up approval processes for new projects.
Traditional Materials: Often require more invasive installation techniques that face stricter environmental scrutiny and longer approval timelines.
Benefit: Accelerates project approval times and reduces costs, aligning with governmental infrastructure improvement initiatives.
Lower Infrastructure Costs for Public Projects
Plastic Piping: Lower material, transportation, and installation costs make plastic pipes an attractive option for public infrastructure projects, helping governments manage tight budgets.
Traditional Materials: Steel and fiberglass are more expensive to produce, transport and install, placing a greater burden on public infrastructure budgets.
Benefit: Enables governments to maximize investments in energy infrastructure while reducing taxpayer burden and optimizing resource allocation.
Alignment with Sustainability and Climate Goals
Plastic Piping: Supports global and national sustainability goals through energy efficiency, reduced carbon emissions and long-term performance in infrastructure.
Traditional Materials: Require more energy-intensive production and maintenance, making them less compatible with sustainability-focused policies.
Benefit: Governments can use plastic piping as a tool to meet environmental commitments, such as those outlined in the Paris Agreement and national climate action plans.
Comments