April 2025, Vol. 252, No. 4
Features
Control Rooms Crucial to Pipeline Compliance Operations
By Russel Treat, President & CEO, EnerSys Corporation
(P&GJ) — In 2007, the Pipeline Hazardous Materials Safety Administration (PHMSA) released a Notice of Preliminary Rule Making (NPRM), known as the Control Room Management (CRM) rule. Since the CRM rule went into full effect in 2012, pipeline operators have seen significant transformation in the control room operation.
Initially, operators focused on compliance with CRM, updating policy and practice in the control room. As the operators learned through operating experience and PHMSA inspections, the focus began to shift to improving systems in the control room that would streamline compliance.
The Natural Compliance methodology prioritizes the seamless integration of compliance into routine procedures. This is accomplished by writing policy and procedure and building systems such that records demonstrating compliance are generated as a natural output of work as it is performed. While this integration represents a significant step forward, achieving true operational excellence necessitates a broader, more strategic perspective.
In 2014, API Recommended Practice 1173, Pipeline Safety Management System (PSMS) Requirements, was published. PSMS focuses on implementing continual improvement in process safety. Since the publication of API 1173, the industry has broadly endorsed PSMS and committed to its implementation.
Operational excellence is characterized by the continuous optimization of processes, driven by data analysis and strategic refinement. It represents a move from a reactive, compliance-focused culture to a proactive, performance-driven one. Operational excellence is closely related to safety performance. Where safety performance focuses on the avoidance of negative outcomes, operational performance focuses on accomplishing business objectives.
The distinction between simply meeting regulatory standards and achieving operational excellence is crucial. While compliance establishes a baseline, true excellence involves a commitment to ongoing improvement and data-informed decision-making. This approach necessitates a thorough understanding of underlying processes and a dedication to their continuous refinement, ultimately leading to enhanced safety and efficiency within the industry.
Defining the Foundations: Natural Compliance and Operations Performance
To effectively transition from compliance to performance, it is essential to establish clear definitions for both natural compliance and operations performance.
Natural Compliance
Natural compliance is characterized by the integration of regulatory requirements into routine operational tasks. It can be defined as the state in which “doing the work you ought to be doing anyway” results in the automatic generation of necessary records and documentation, thereby demonstrating compliance. This approach emphasizes efficiency by ensuring that compliance is a byproduct of standard operating procedures.
The implementation of natural compliance relies on a hierarchical structure:
- Program: establishes governance and foundational policies, providing the framework for all subsequent activities. This level is typically captured in the Control Room Management Plan.
- Process: establishes the sequence of activities required to accomplish specific outcomes, such as the Annual Alarm Program Effectiveness Review.
- Task: encompasses the day-to-day execution of specific activities, which generate the records necessary for demonstrating compliance.
A common challenge in achieving natural compliance is the “gravity” problem, which describes the tendency to prioritize task execution without sufficient understanding of program requirements and process outcomes. This can lead to challenges during internal reviews and third party inspections.
Operations Performance
Operations performance signifies a state of continuous optimization, where work is conducted safely, efficiently and effectively to meet organizational objectives. This goes beyond mere compliance, focusing on the ongoing enhancement of operational processes.
Achieving optimal operations performance requires a deep understanding of operations as a system of interconnected processes, a clear focus on achieving desired outcomes aligned with organizational goals and the elimination of functional silos through a cross-functional, process-centric approach. By establishing these foundational elements, organizations can transition from a compliance-driven to a performance-driven culture.
The Crucial Distinction: Compliance vs. Performance
A clear distinction between compliance and performance is essential for organizations seeking to advance beyond regulatory adherence and achieve operational excellence.
Compliance
Compliance emphasizes the development and implementation of documented policies and procedures, along with the creation of records that demonstrate adherence. It often operates as a “system of work,” where activities are structured to ensure that regulatory requirements are met and task execution and documentation to satisfy legal obligations are prioritized.
Performance
Performance, in contrast, extends beyond mere adherence to regulations, focusing on the continuous improvement of operational processes. This involves analyzing operational data to identify trends and areas for improvement, fostering a culture of continuous evaluation and refinement. Operating within a “system of processes,” performance prioritizes the optimization of interconnected activities to achieve desired outcomes. Key performance indicators (KPIs) are crucial for monitoring performance and for critically evaluating and refining these KPIs ensures alignment with operational goals.
By understanding the fundamental differences between compliance and performance, organizations can develop strategies that not only ensure regulatory adherence but also drive continuous improvement and operational excellence. Understanding these fundamental differences is the first step. The next is to explore how to effectively bridge that gap.
Bridging the Gap
The transition from natural compliance to performance improvement requires building upon existing compliance practices and prioritizing human factors. This transition involves extending natural compliance with comprehensive data collection to enable detailed performance analysis, shifting the focus from merely generating records to actively using them for process optimization.
Operations Management Systems (OMS) play a crucial role in this transition by providing a structured framework for integrating data collection, analysis, and process improvement into routine operations.
Human Performance
Human performance is critical for operational excellence, especially in control room environments. Recognizing the personal nature of human performance necessitates human-centered solutions. This includes evaluating processes for improvement, minimizing unnecessary human interactions to reduce errors and incorporating data validation mechanisms.
Key human performance processes involve observation and coaching, verification procedures, cultivating a questioning attitude, implementing the Stop, Think, Act, Review (STAR) methodology and establishing time-out procedures.
Proactive management of human error requires identifying and mitigating error precursors, strengthening human error defenses and enhancing the capacity to fail safely. Monitoring for subtle signs of human performance decline serves as a leading indicator for serious injury and fatality (SIF) events.
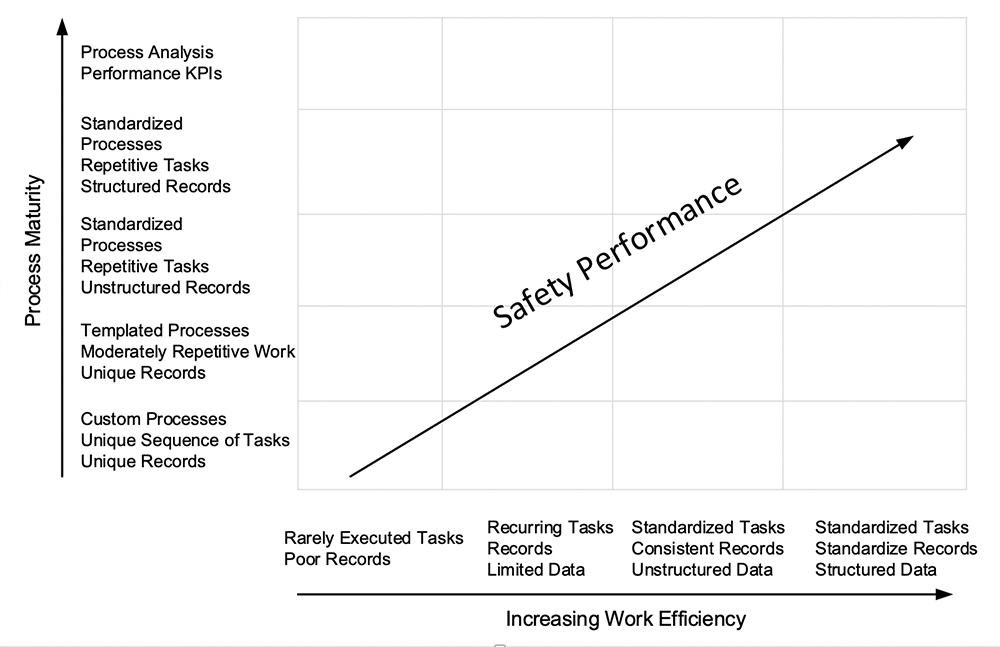
To effectively transition from compliance to performance, organizations must adopt a structured, process-driven approach.
Implementing a process-driven approach requires a systematic progression from policy to practice, ensuring actionable and effective safety management. This framework utilizes a structured methodology to translate high-level policies into practical procedures, ensuring alignment with strategic objectives.
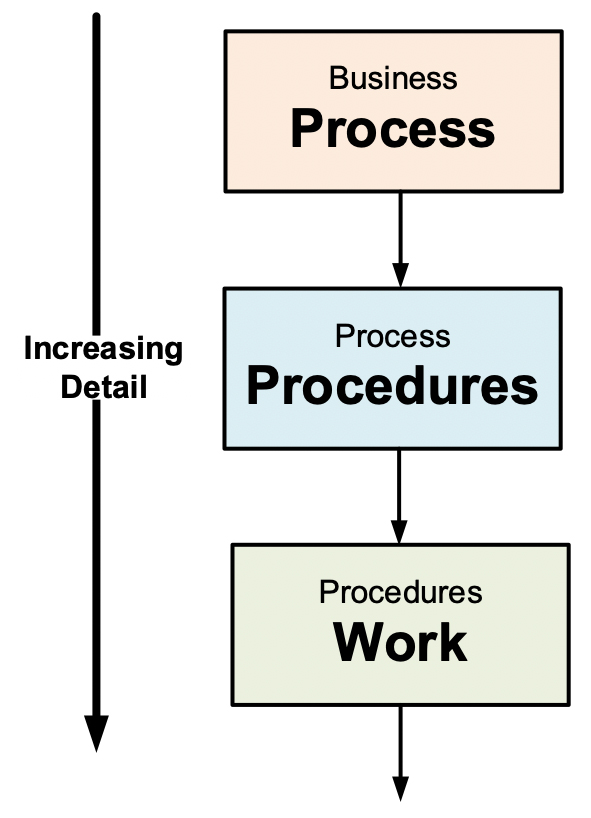
It is designed for repeatability and scalability, allowing consistent application and adaptation across operational areas.
The shift handover process exemplifies the difference between procedure and process: a procedure details steps, while a process defines desired outcomes, like effective communication and achievement of operational objectives. Establishing clear process outcomes and relevant KPIs is essential for measuring and monitoring performance.
Performance Measures
In the control room, specific performance measures are essential for safety and efficiency. These measures include pipeline safety, adherence to maximum allowable operating pressures (MAOPs), meeting minimum operational requirements, delivering scheduled rates and volumes, efficiently operating the system by monitoring and responding to abnormal operating conditions (AOC’s) and emergency operating conditions (EOCs), effectively conducting remote operations of valves and compressor stations and maintaining current and relevant training programs.
Adopting a “system first” philosophy prioritizes control system integrity and minimizes distractions. Timely and accurate recognition and response to AOC’s and EOCs are crucial, supported by clear protocols. Implementing a performance dashboard provides real-time visibility into key operational metrics, enabling informed decision-making.
Achieving operational excellence is an ongoing journey that requires commitment to data-driven decision-making and continuous process improvement.
Data is fundamental for effective operational decisions, providing the basis for measuring outcomes and making informed choices. Data analysis enables the identification of trends and patterns, revealing areas for improvement and informing proactive measures. Operational excellence is achieved through a continuous improvement cycle, involving ongoing process optimization. The Plan-Do-Check-Act (PDCA) cycle provides a structured framework for this continuous improvement, especially in pipeline safety management, by planning, implementing, checking and acting on improvements. As W. Edwards Deming stated, “If you can't describe what you're doing as a process, you don't know what you're doing.”
In the demanding environment of the oil and gas industry, operational success is not merely a matter of seizing opportunities but of systematically building and refining the processes that underpin those opportunities. Organizations “sink to the level of their processes,” meaning that during high-stress or time-critical situations, established processes will dictate the outcome. Therefore, robust processes are essential for consistent success.
Therefore, oil and gas operators must move beyond a narrow focus on regulatory compliance and cultivate a culture of continuous improvement. This involves embracing a process-driven approach, leveraging data for informed decision-making, and relentlessly pursuing operational excellence. By prioritizing process optimization, organizations can enhance safety, efficiency and overall performance.
Comments